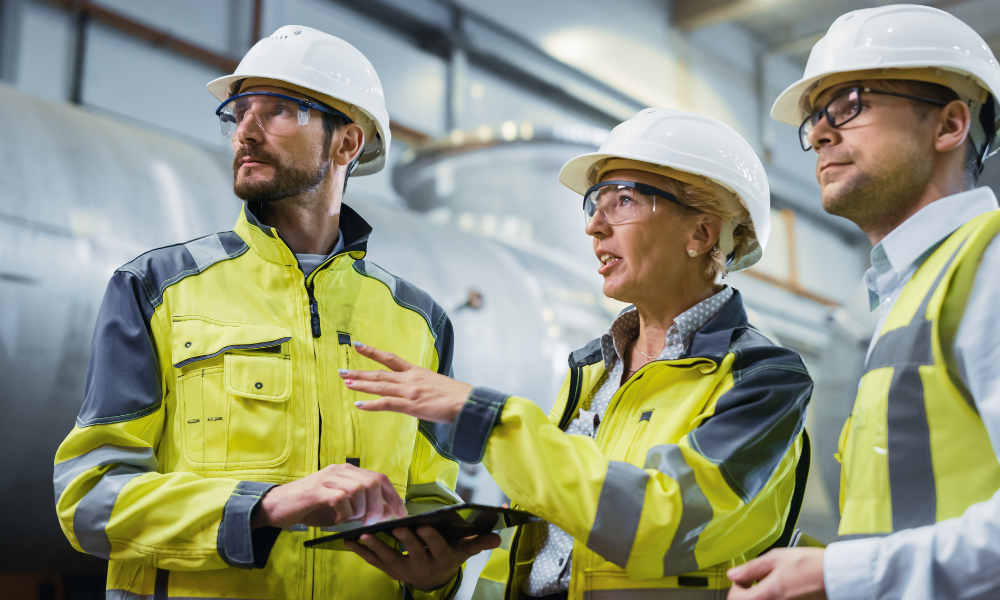
EAM Challenges: Where Traditional Enterprise Asset Management is Failing
If the words “enterprise asset management” inspire nothing but bitterness in your organization, traditional EAM is probably to blame. Although the foundational ideas may be solid, the implementation and functionality often disappoint — which is why EAM may have a bad reputation.
The good news is that the team at L2L have lived through the failings of traditional enterprise asset management. The better news is that we developed software that addresses those problems without breaking a sweat.
Here’s what you need to know about traditional EAM, its failures and the modern solution that has come along to save the day.
The downfall of traditional EAM
You’re probably all too familiar with it: Traditional EAM is the somewhat-outdated system used by manufacturers to manage machine breakdowns and improve efficiency. The thing is, if you knew it 20 years ago, you still know it now. Traditional EAM hasn’t changed much — and that’s just one of the reasons it’s failing to meet the needs of the modern manufacturer.
The truth is that, when it comes to maintenance, data analytics, asset management and more, the most important tool in your arsenal is being able to tell what’s out of your control vs. what you do have control over. And, unfortunately, your traditional EAM system probably puts a whole lot in the “don’t have control over” category.
Sure, it’s good for helping leaders and employees stay on the same page about machine downtime — but you need a whole lot more from your EAM system.
Going beyond machine downtime
While machine reliability is a key challenge in the manufacturing landscape, it’s not the single defining factor behind your success. In fact, you need support from a much wider variety of elements — many of which find themselves firmly in the “don’t have control over” category thanks to traditional EAM.
Here are just a few critical things that fall outside your reach when you use a traditional EAM system:
Data and analytics
Like most manufacturing solutions, enterprise asset management is built on data. However, with the limitations inherent to traditional EAM, that data quickly becomes trapped.
This is because traditional EAM is far from user-friendly. Even if your team members can determine how to properly input data while they’re focused on another task, others likely won’t be able to get that data back out — which means the rest of the shop floor receives an outdated, incorrect or significantly delayed view of what’s going on. If you don’t have control over the data critical to asset management, your team can’t perform the analytics necessary to guide your decision-making process.
Implementation
Another element put out of reach with traditional EAM is fast, efficient implementation. These systems are often difficult to deploy, limiting your chances of seeing results and turning EAM into its own kind of challenge. The worst part is that there’s nothing you can do about it. Slow, complex implementation is just part of the deal with traditional EAM.
Communication
Traditional EAM treats manufacturing and production data as two separate things. This means neither team has an accurate view of what’s really happening on the shop floor. As a result, communication breaks down, efficiency takes a blow and leaders have to step in just to get everybody back on the same page.
Material shortages
Short of some manufacturing miracle, you probably won’t have control over material shortages no matter what you do. However, because of its narrow focus on machine breakdowns, traditional EAM all but eliminates your chances of managing the impacts of those material shortages. That’s right: These outdated systems don’t just shrug in the face of big problems — they actually limit your ability to respond to external issues with speed and flexibility.
Team management issues
From poor communication to unhappy employees, team management issues can have a significant impact on manufacturing efficiency. Traditional EAM gives you no insight into the problems that may be causing team members to get frustrated — which, in turn, leaves you all the more likely to be blindsided by those problems when they start interfering with the organization overall.
The takeaway: Traditional EAM simply isn’t smart, flexible or evolved enough to adapt to our unpredictable world. It needs an upgrade — and fast.
A modern enterprise management solution
The good news is that Modern EAM software is much smarter, simpler and better equipped than its predecessor. It combines the best of both worlds, allowing you to manage machine downtime and move toward more advanced methods of achieving reliability such as condition based and predictive maintenance.
Modern EAM software also solves that classic communication problem by taking data from across your organization — manufacturing and production included — and uniting it under one digital roof. You’ll have a streamlined view of what’s happening, where and why, as well as the asset or team involved. Plus, with real-time mobile access, that information is constantly and consistently updated.
Perhaps most importantly, Modern EAM software clarifies what you do and don’t have control over, all while putting more elements within your reach. Where traditional EAM says “no,” its younger sibling says “yes — and here’s how.” That represents a significant competitive advantage. Sure, you may not have control over everything, even with modern EAM software — but you’ll have the tools and insights necessary to navigate any production challenge, asset question, data and analytics process, team management problem or other issue that comes your way.
See the power of Modern EAM software
If your traditional EAM system looks just like it did 20 years ago, it’s time for an evolution. Modern EAM software puts you in control of more elements critical to your success, and it does that without the long lead times associated with traditional EAM implementation.
To see the power of Modern EAM software, download our eBook today!
Revisions
Original version: 18 July 2024
Written by: Evelyn DuJack
Reviewed by: Daan Assen
Please read our editorial process for more information
Subscribe to Our Blog
We won't spam you, we promise. Only informative stuff about manufacturing, that's all.