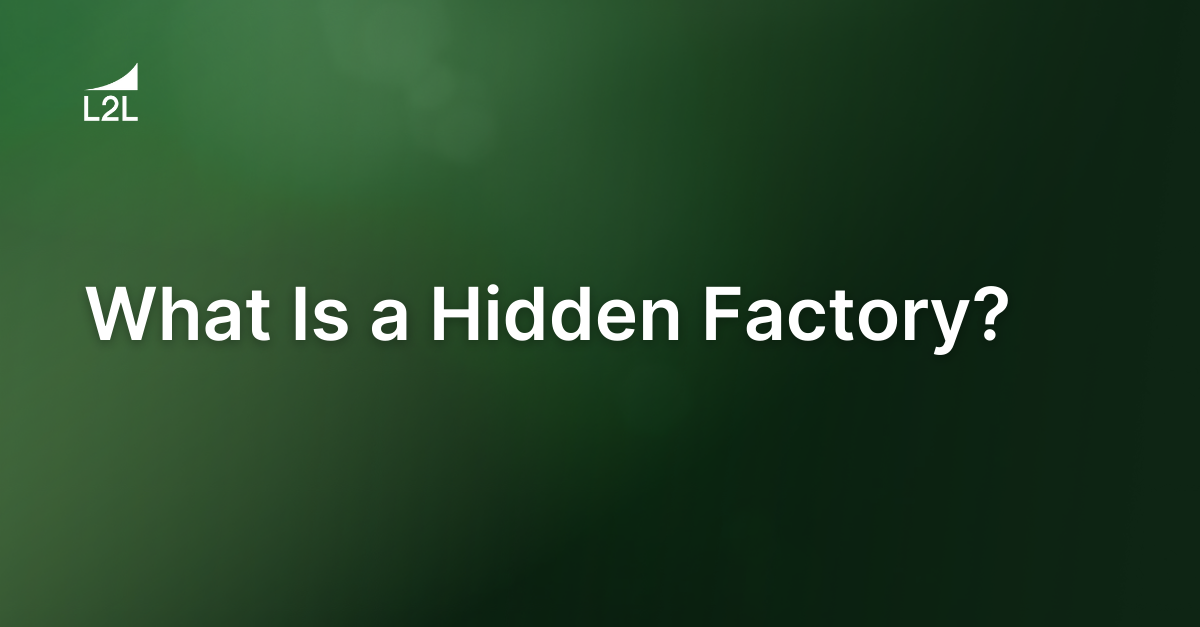
In every manufacturing organization, there exists a parallel operation, often unnoticed and unaccounted for, that significantly impacts productivity and profitability. This unseen operation is commonly referred to as "The Hidden Factory."
The concept of the hidden factory embodies all the unmeasured, unseen, or unintended activities and flaws within a production process that consume resources but add no value to the product or service. In this article, we explain what constitutes a hidden factory, real-world examples of hidden factories, and how manufacturers can address this problem.
Why is the hidden factory important?
The hidden factory represents the sum of all non-value-adding activities in a production process. These activities, while not contributing to the final product, consume resources like time, labor, and materials. Examples include excessive paperwork, rework, handling of defects, and unproductive wait times. Understanding and addressing the hidden factory is essential for any business seeking to enhance efficiency and profitability.
The impact of the hidden factory is profound. It can account for a significant portion of a company's operational costs. In some cases, studies have shown that the hidden factory can represent as much as 20-30% of total capacity. This hidden inefficiency leads to increased production costs, longer lead times, lower quality, and ultimately, reduced customer satisfaction.
Common hidden factory elements
A Hidden Factory can be identified by the following characteristics:
- Rework: Correcting defective products or services.
- Overproduction: Producing more than what's needed or before it's required.
- Excess Inventory: Maintaining more raw materials, work-in-progress, or finished goods than necessary.
- Unnecessary Movement: Inefficient layout leading to excessive movement of materials or employees.
- Waiting: Delays in processes due to various inefficiencies.
- Over-processing: Performing more work or using higher precision than required.
Is there a hidden factory lurking beneath your plant? Here are the most efficient approaches to answering this question:
-
Process Mapping: Analyzing workflows to identify bottlenecks and wasteful steps.
-
Lean Manufacturing Techniques: Applying principles such as 5S, Kaizen, and Six Sigma to identify and eliminate waste.
-
Employee Feedback: Encouraging employees to report inefficiencies they encounter in their daily tasks.
Addressing the hidden factory
Once you've discovered your hidden factory, you need a comprehensive plan to address it. You can follow the outline below to get started.
- Lean Manufacturing Implementation: Adopting lean principles to minimize waste. A tool like L2L can accelerate this process.
- Continuous Improvement Culture: Encouraging a company culture that seeks regular improvement in all processes.
- Automation: Implementing technology to automate repetitive and non-value-adding tasks.
- Training and Development: Educating employees about efficiency and best practices.
- Quality Management Systems: Establishing systems to prevent defects and ensure quality.
Additionally, you need the right tools and strategies to uncover your hidden factory and eliminate the waste of time, money, and resources.
Here are some tools commonly used to help with this process:
-
Six Sigma: A data-driven approach to eliminate defects.
-
Total Quality Management (TQM): A holistic approach to long-term success through customer satisfaction.
-
Just-in-Time (JIT) Production: Reducing inventory costs by producing only what is needed when it is needed.
Hidden factory case studies
Many companies have successfully addressed the hidden factory, leading to substantial improvements in efficiency and profitability. Toyota's implementation of the Toyota Production System (TPS) is one of the most famous examples of effectively eliminating waste and optimizing production. Check out some of L2L's case studies to see more.
Key lessons from these success stories include the importance of top-down commitment, employee involvement, and the need for continuous assessment and adaptation of processes.
Technology's role in eliminating hidden factories
In the modern manufacturing landscape, technology plays a crucial role in uncovering and addressing the hidden factory. Advanced analytics, the Internet of Things (IoT), and Artificial Intelligence (AI) provide valuable insights into production processes, enabling organizations to identify inefficiencies in real time and make data-driven decisions.
L2L, for example, is a platform that combines these technologies and enables manufacturers to reveal their hidden factory quickly, drive operational efficiency across their plant, and increase productivity with measurable ROI.
The future of manufacturing
As we move toward an increasingly digital and automated world, the importance of identifying and reducing the hidden factory becomes ever more critical. Companies that successfully navigate these challenges will find themselves at a competitive advantage, with leaner operations, higher quality products, and greater customer satisfaction.
As we embrace new technologies and methodologies, the future of manufacturing looks bright, with the hidden factory becoming less hidden and more manageable.
Revisions
Original version: 23 January 2024
Written by: Malcolm Faulds
Reviewed by: Daan Assen
Please read our editorial process for more information
Related Posts
Subscribe to Our Blog
We won't spam you, we promise. Only informative stuff about manufacturing, that's all.