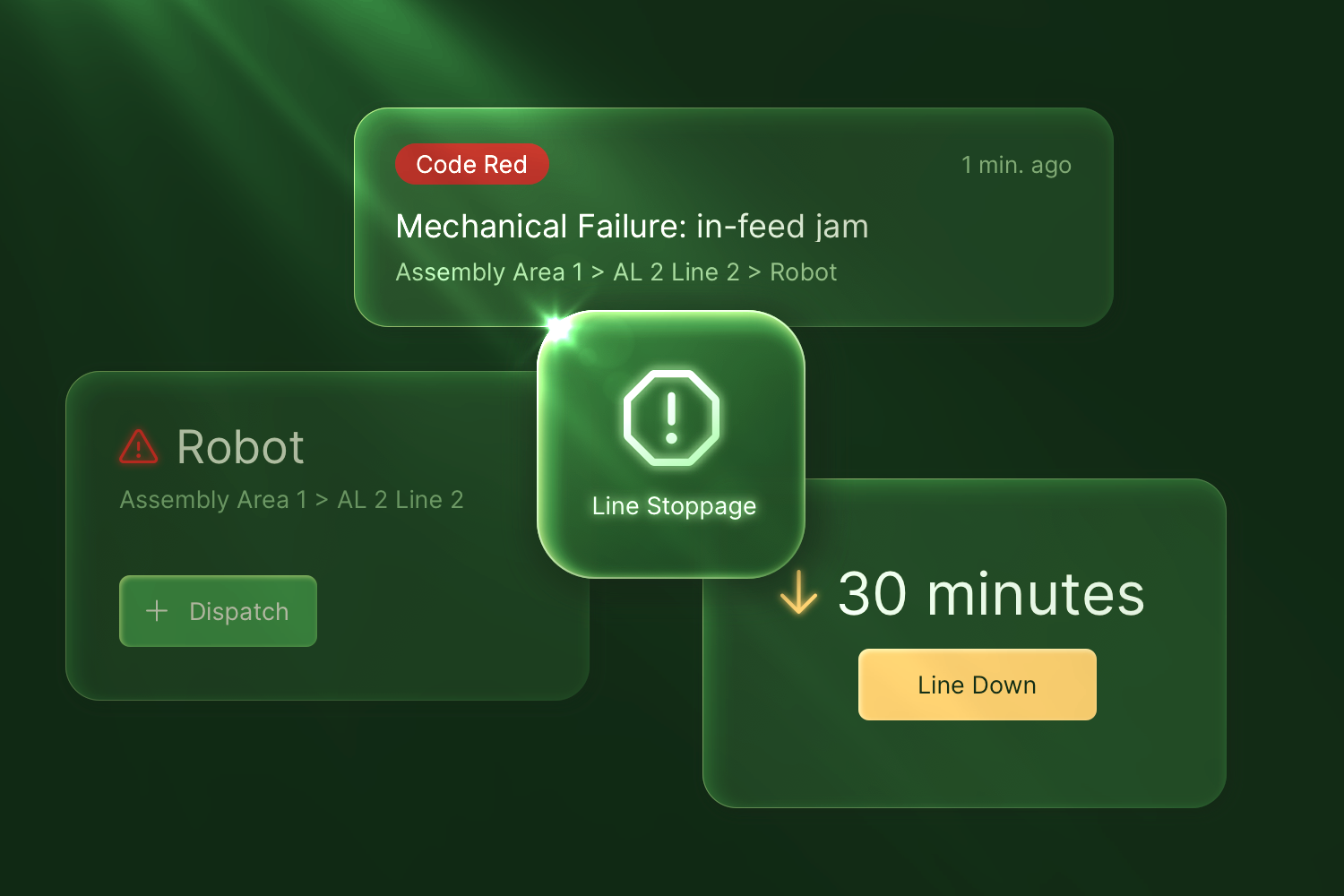
When we ask frontline leaders what keeps them up at night, the answer is usually the same.
Line stoppages.
They’re a universal problem and a significant drain on our resources. But what exactly are lines stoppages, and why do they matter so much in modern manufacturing?
What is a line stoppage in manufacturing?
A line stoppage means that somewhere in your facility, production has stopped.
While the most commonly cited cause is a machine breakdown, the reality is far more complex. The modern shop floor is made up of thousands of moving parts, complex machines, and hundreds of human workers all moving together towards a production target.
When any one of these elements doesn’t function as it should, production stops. The reasons range from:
So why do we care about line stoppages?
The simple answer?
They’re incredibly expensive.
We talked to manufacturing expert Mohsin Saeed about his experience with line stoppages.
Every minute of this unplanned downtime translates to lost revenue, wasted resources, and missed deadlines.
"I have a building that's running," Mohsin said. "There's lights, there's power, there's internet, there's land costs, there's the cost of not getting stuff out the door. All of these different costs add up when a line is stopped."
The severity of a stoppage varies, but they all create a negative impact—from down on the factory floor to up in the corner office. A simple production bottleneck can create a ripple effect that impacts uptime and quality, while a complete shutdown can bring an entire facility to a standstill.
The reasons behind line stoppages.
While machine breakdowns are the most common culprit, the root cause is often more of a mixed bag.
Line stoppages can be caused by countless factors within your production environment. After all, production lines are incredibly complex systems with human operators, thousands of moving parts, and other risk factors.
These include (but are certainly not limited to):
Quality issues: Product defects can cause a line to shut down until teams can address the root cause or remake the unit.
Skills gaps: When an operator isn’t properly trained or certified to perform a role, they’re liable to make mistakes that need to be corrected.
Safety concerns: Manufacturers must stop production until safety concerns, like unsafe conditions and faulty equipment, are eliminated.
Material shortages: Resource planning and allocation must be performed correctly, efficiently, and at scale to ensure seamless production timelines.
And yes, machine malfunctions: Machines break down. It’s a simple fact in manufacturing. When they do, they need to be fixed before production can continue.
The human factor.
Stoppages often involve human errors. These range from simple operational errors (like incorrect measurements or usage of a machine) to more complex issues like operator absenteeism or persistent skills gaps.
This is (and will continue to be) a human-centered industry. We need to give manufacturing teams the tools they need to succeed. Reducing downtime at scale requires a holistic approach that seamlessly integrates data, proactivity, and visibility with our teams on the shop floor.
The fix: better data, visibility, and proactivity.
So, how do manufacturers combat line stoppages? The response needs to be focused on:
- Understanding the root cause of the problem
- Quickly notifying the people who need to fix it
- Ensuring that it won’t happen again
A data-driven response.
"Until you have data, you're not going to be able to identify or solve your problems," said Mohsin.
Manufacturers need systems that provide real-time data on what’s happening during a line stoppage—the who, what, when, where, and why. This information allows teams to quickly identify what went wrong and understand how to apply the correct fix.
There’s a broad range of data sources that are useful to identify the root cause of a line stoppage:
Centerlining: Manufacturers standardize machine performance into a desired range and regularly compare their function against these parameters. Any variances can be flagged, investigated, and corrected.
Quality checklists: Data from quality control inspections is analyzed to identify trends and root causes of defects. Statistical process control (SPC) techniques are used to monitor process variability.
Sensor-driven machine data: Manufacturers use sensors to monitor critical equipment parameters like vibration, temperature, pressure, and electrical current. This real-time data is then fed into CMMS platforms.
Skills and shift data: Understanding who is working on which line and having an overview of their skills and capabilities with tools like digital skills matrices allows teams to pinpoint the source of human errors.
But it's not only about collecting data, it's about making it actionable.
Manufacturers need the right tools to understand and respond effectively to concerns before they grow. The best systems will be able to take the information collected from the systems mentioned above and coordinate a response with the correct people.
Work orders and dispatches.
The most effective way to quickly correct a line stoppage is to automatically coordinate work orders, spare parts, and maintenance through a centralized digital system. This is especially true for large organizations that need to respond quickly and at scale
Solutions like Dispatch are able to coordinate and combine…
- What needs to be done
- Where is the problem located
- Who needs to be involved
- What parts and skills are needed to fix it
…into a single unit of collaborative work. These Dispatches are delivered in real time to the correct people to be tracked until the issue is resolved. They can also be linked directly to quality checklists and used as a platform to deliver visual work instructions to the front line.
Proactive maintenance.
Modern manufacturers have the opportunity to leverage better digital tools to schedule maintenance at scale. Optimizing scheduled maintenance for recurring and one-off tasks is often the best defense against unplanned downtime like line-stoppages.
Teams use a combination of sensor data from machinery and detailed records of prior maintenance, run times, and even previous fixes to determine the optimal timing and procedures to keep a line running at peak efficiency.
Leveraging a CMMS system helps to manage the large volume of data involved in successful predictive maintenance and optimize resource use, lower costs, and even increase the lifespan of machinery. Integrated AI and tools take this one step further by using predictive analytics to find trends in maintenance data and predict when machinery is likely to fail, among other maintenance needs.
Upskilling and training.
Manufacturing is still a human industry. Leaders need to effectively address frequent line stoppages that stem from skills gaps, human errors, and other issues associated with competency and training.
The faster that a supervisor can find a qualified operator to fill a skills gap, the faster they can get the line up, running, and productive again.
Digital skills matrices give teams a snapshot of the skills and competencies of their entire production floor while assigning training and upskilling resources as needed. You can regularly administer skills assessments to assure compliance and confirm that training sticks.
The takeaway.
Line stoppages are inevitable. However, we can do a great deal to reduce their frequency and mitigate their impact on our bottom line and on our frontline teams. The key lies in our ability to understand their root causes and how effectively we can respond to them at scale.
Moreover, this means using powerful digital tools that can help us process the incredible amount of data and resources that our operations utilize every minute of every day. By embracing data-driven solutions, prioritizing proactive responses, and empowering the human players involved, manufacturers can minimize the negative impact of line stoppages.
More manufacturers than ever are relying on the capabilities of connected worker platforms to harness actionable insights from the shop floor and use them to improve efficiency while reducing downtime.
Want to learn more about improving uptime? Schedule your demo of the L2L platform.
Revisions
Original version: 12 March 2025
Written by: Chris Rost
Reviewed by: Mohsin Saeed
Please read our editorial process for more information
Related Posts
Subscribe to Our Blog
We won't spam you, we promise. Only informative stuff about manufacturing, that's all.