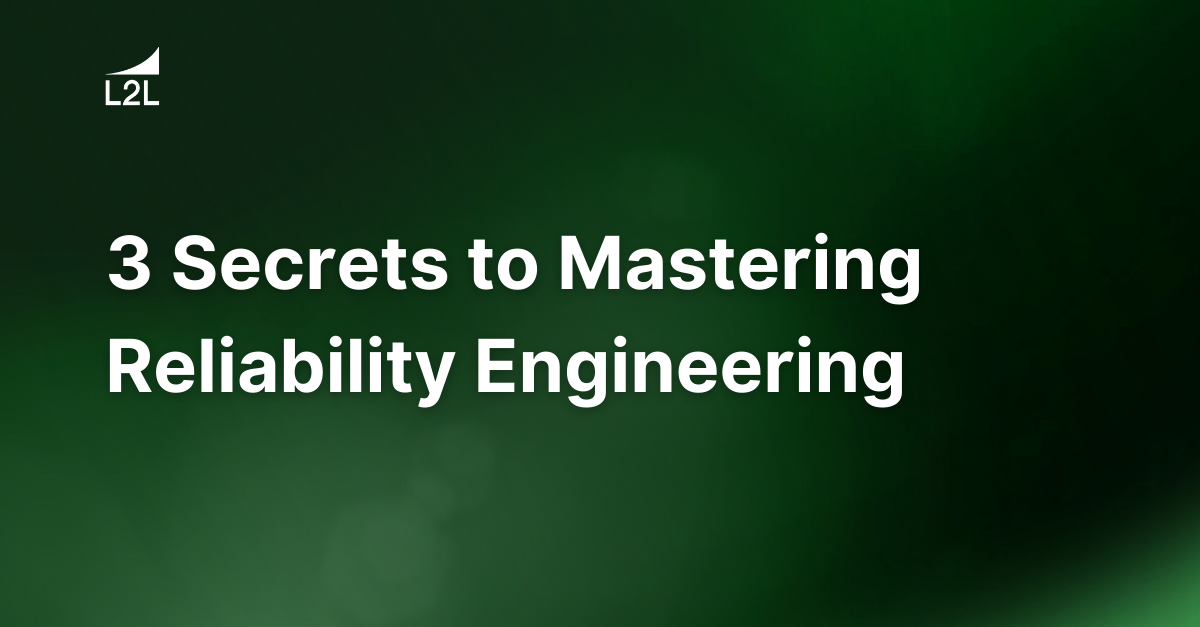
In every manufacturing plant, equipment is needed to produce product. And sooner or later, equipment fails. How we respond to these occurrences will largely dictate the effectiveness of any countermeasures and the potential re-occurrence of failures. This is where reliability engineering plays a vital role.
Our ultimate goal is to proactively identify all possible failure modes in products and processes. Predicting potential failure modes can drive product design decisions that ultimately can lead to design poka-yokes (ways to mistake-proof).
Designing, building and maintaining our manufacturing equipment is no different. Take a proactive approach to the manufacturing and process related failure modes. Designing equipment and processes with robust controls that can prevent, predict, and detect abnormal conditions.
What Is Reliability Engineering?
At the most basic level, reliability engineering refers to the engineering knowledge necessary to accomplish three objectives:
-
- Reduce the likelihood and frequency of failures
- Identify and correct the causes of failures that do occur despite the efforts taken to prevent them
- Identify and design ways of coping with failures that still may occur if their causes have not been corrected
Having the ability to analyze reliability data is vital to a company’s success. I’ve seen firsthand how powerful a few basic practices can be in improving equipment reliability when implemented regularly:
-
- Go to the Gemba (Spend time on the manufacturing floor)
- Listen to your Historical Machine Data (Review your data and look for the story)
- Yokoten (Share your successes and opportunities with other sites)
Gemba and Reliability Engineering
I have found that spending time at the Gemba (on the plant floor) holds huge value and drives change in key metrics that improves the overall Reliability in our factories. We all understand the value of using data to drive change and make decisions. However, data combined with production associate skills and experience can outperform decisions that are based solely on data.
Time spent on the floor with production associates and maintenance technicians not only builds relationships and trust, it lays the foundation for culture that can become invaluable and be the biggest contributor to waste elimination and process/product improvements. These improvements and culture can be the largest contributor to one's overall reliability engineering.
Historical Machine Data & Reliability
Do you control the process? Or does the process control you?
An out-of-control process is easy to identify statistically. It’s easy to review variable data and determine if a process is normal vs. abnormal.
However, how do you address and improve a process when variable data is not available? Or even relevant to the current situation? In many cases variable data is not the answer or the tool to measure one's success.
The power of historical machine data (such as downtime and occurrences) is often overlooked and surprisingly, in many instances, not available in many of today’s factories. This is unfortunate because it's an important part of effective reliability engineering. Consistently reviewing your overall machine history:
- Allows teams to identify systemic causes of downtime
- Helps you quickly grasp a factory's success
- Builds a structure and culture that drives significant Operational Availability (OA) and Overall Equipment Effectiveness (OEE) improvements
A stable process significantly impacts all measurables. Access to historical machine data gives you the information you need to create that stability. At a glance, you can understand the true OA of a plant's manufacturing equipment, lines, and cells.
The Impact of Yokoten on Reliability Engineering
When it comes to failure modes and repeat issues, not all are created equal. We analyze failure modes and associate risk with them in an attempt to ensure we have adequate controls in places such as prevention and detection tools.
The reality is that in today's world and environment, it is imperative to use Yokoten in our approach to reliability engineering.
Yokoten is a lean principle that refers to the process of sharing learnings horizontally across an organization. Some of the greatest lessons and methods I have learned over the years have been a result of this lateral sharing.
To implement Yokoten on your floor, challenge your current methods by:
-
- Identifying lesson learned or best practice
- Documenting lessons learned
- Sharing lessons learned via a database (could be global, local, or site-to-site)
- Reviewing new potential shared lessons with a standardized method of review
- Hosting a team review and accepting/rejecting lessons according to feasibility
- Documenting all applicable areas and machines
- Tracking implementation of lessons learned through a database that documents, schedules, and tracks the pace of implementation of lessons learned
- Monitoring results
- Identifying and tracking current and future tangible savings
As we identify new failure modes and lessons learned, it is imperative that we grasp and utilize the Yokoten concept and principles to its fullest.
Transform Reliability Engineering in Your Factory
At the heart of reliability engineering is the desire to improve OEE and OA.
How does one know where to start the process of making improvements?
At many manufacturing sites, decisions regarding how to prioritize improvement projects are too often based on emotions; whoever yells the loudest drives resources and project planning.
Decisions made on this basis result in very little (if any) ROI. If real Reliability Improvements are to be made, you'll need to have answers to these questions:
-
- Can I identify number 1 source of downtime? Area, line, machine?
- Can I identify the number 1 source and component of downtime?
- Can I review Historical Data for these areas, lines, machines?
- Do I have a method to document best practices or lessons learned?
- Do I have a method to share best practices or lessons learned?
- Do I have a method to receive/review lessons learned?
- Can I track Yokoten Implementation and status for multiple machines/processes?
- Can I report Yokoten Implementation with Tangible Savings?
In order to measure the rate of improvement, we must be able to objectively view and understand our current situation. Use the concepts and tools that can measure your current situation and track your rate of improvement. Eliminate those emotion-based decisions and use data to drive all your factory’s decisions.
Ready to gain the data visibility needed to improve equipment reliability? Discover the system that captures more robust data, always in real-time, giving you digital visibility into what is happening on the front lines so your team can quickly identify and solve abnormalities.
Revisions
Original version: 18 July 2024
Written by: Evelyn DuJack
Reviewed by: Daan Assen
Please read our editorial process for more information
Related Posts
Subscribe to Our Blog
We won't spam you, we promise. Only informative stuff about manufacturing, that's all.