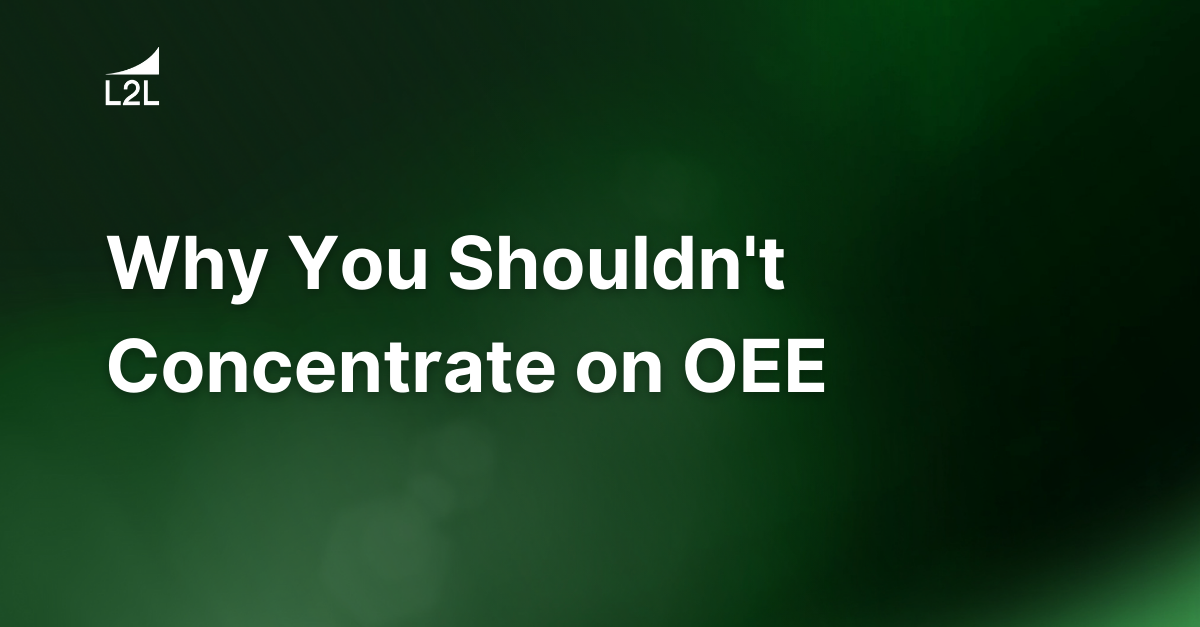
In the bustling landscape of manufacturing, efficiency reigns supreme. For decades, the gold standard metric has been Overall Equipment Effectiveness (OEE), a yardstick to measure the productivity of machinery and processes. However, manufacturers need to look beyond OEE if they want to fix the ongoing labor shortage. Instead of fixating solely on machine performance, they need to shift their attention toward labor metrics to address the root cause of the crisis.
The OEE conundrum: Underestimating the human element
OEE, a composite metric combining availability, performance, and quality, has long been the cornerstone of manufacturing optimization strategies. It provides a comprehensive view of equipment effectiveness and identifies areas for improvement. However, its sole focus on machines overlooks a crucial component: the human factor.
To maximize OEE, manufacturers often prioritize automation and capital-intensive investments. While these initiatives can enhance machine productivity, they inadvertently exacerbate the labor shortage by reducing the reliance on human workers. Moreover, chasing elusive OEE targets can lead to a neglect of workforce development and engagement, exacerbating the shortage further.
Unpacking the manufacturing labor shortage
The labor shortage in manufacturing is not a recent phenomenon but a persistent challenge with multifaceted causes. Factors such as retiring Baby Boomers, a skills gap among incoming workers, and shifting demographics have all contributed to the decline of skilled labor. Moreover, the pandemic amplified these issues, accelerating retirements, disrupting supply chains, and reshaping workforce dynamics.
Traditional approaches to address the labor shortage often revolve around recruitment and retention strategies. While important, these tactics only scratch the surface of the problem. To truly tackle the root cause, manufacturers must delve deeper into the dynamics of their workforce and implement strategies that empower and optimize human capital.
Shifting from overall equipment effectiveness to labor metrics
Labor metrics encompass a range of key performance indicators (KPIs) related to workforce efficiency, engagement, and effectiveness. Unlike OEE, which primarily measures machine performance, labor metrics shine a spotlight on the human element of manufacturing operations. By prioritizing labor metrics, manufacturers can unlock untapped potential within their workforce and mitigate the impacts of the labor shortage.
Here’s what you should be measuring if you want to tackle labor and retention issues.
1. Labor productivity
Labor productivity metrics gauge the efficiency of human resources in the production process. Metrics such as labor utilization rate, labor cost per unit, and labor efficiency variance provide insights into how effectively labor resources are deployed. By optimizing workflows, providing targeted training, and leveraging technology to augment human capabilities, manufacturers can maximize labor productivity without overburdening their workforce.
2. Employee engagement
Employee engagement is a critical yet often overlooked aspect of workforce optimization. Engaged employees are more motivated, productive, and likely to stay with their employers. Metrics such as employee turnover rate, absenteeism, and satisfaction surveys offer valuable insights into the health of the workforce. By fostering a culture of transparency, communication, and continuous improvement, manufacturers can boost employee morale and retention rates.
3. Skills development
The skills gap is a significant contributor to the labor shortage, as many manufacturing jobs require specialized knowledge and expertise. Investing in skills development initiatives, such as apprenticeship programs, on-the-job training, and lifelong learning opportunities, is essential for bridging this gap. Metrics tracking skill proficiency, training hours per employee, and certification attainment can help measure the effectiveness of these initiatives and ensure a skilled workforce for the future.
The path to labor efficiency
In navigating the labor shortage, manufacturers must adopt a holistic approach that prioritizes both machine and human performance. While OEE remains a valuable metric for evaluating equipment effectiveness, it should not overshadow the importance of labor metrics in addressing the underlying skilled worker shortage.
A connected worker platform like L2L is ideal for collecting labor data. This is because it integrates seamlessly with various devices and systems used in the workplace, providing real-time data collection and analysis. The platform's ability to aggregate and analyze data helps you identify trends, optimize workflows, and improve overall operational efficiency.
Improve productivity with the L2L Platform
The manufacturing labor shortage is a complex challenge that demands a multifaceted solution. While OEE has long been the reigning metric for measuring productivity, its exclusive focus on machines overlooks the critical role of human capital. By shifting your focus toward labor metrics, you can unlock the full potential of your workforce and mitigate the impacts of the labor shortage.
By investing in labor productivity, employee engagement, skills development, and connected workforce technologies like L2L, manufacturers can not only address the immediate challenges posed by the labor shortage but also build a resilient and sustainable workforce for the future.
It’s time for manufacturers to embrace a new era of manufacturing metrics—ones that place human beings at the center of productivity and innovation.
See how connected workforce platforms enhance workforce productivity when you take L2L’s Interactive Product Tour!
Revisions
Original version: 9 June 2024
Written by: Eric Whitley
Reviewed by: Daan Assen
Please read our editorial process for more information
Related Posts
Subscribe to Our Blog
We won't spam you, we promise. Only informative stuff about manufacturing, that's all.