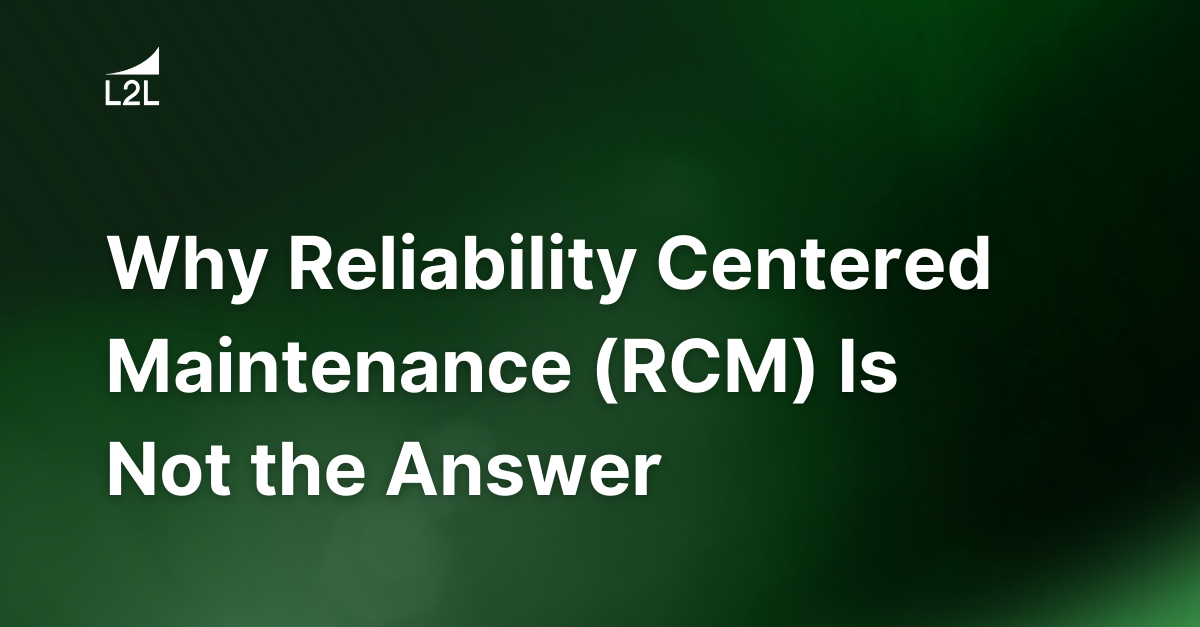
-
- Reliability Centered Maintenance is effective in the aircraft industry, where it was created.
- Other industries don't benefit from RCM in the same ways, especially if they're in 'firefighting' mode.
- If you do struggle with your current processes, RCM can't help you—but CloudDispatch can.
25 years of teaching and consulting maintenance process improvement has taught me one thing: Maintenance managers and maintenance organizations are always looking for the magic pill to cure the ill of reactive maintenance. This is where maintenance consulting companies have made a truckload of money with myriad of programs. These programs may include Physical Maintenance Analysis (PMA), Total Productive Maintenance (TPM), Conditioned Based Maintenance (CBM), and Reliability Centered Maintenance (RCM), as well as others. It is Reliability Centered Maintenance that I would like to address in this article.
Reliability Centered Maintenance Works for the Aircraft Industry
Now, let’s set things straight. As a Consultant and Account Manager for my clients, I spend my fair share of time at 35,000 feet, seeing the world through the windows of every type of commercial aircraft in the sky.
I fully acknowledge that Reliability Centered Maintenance was born in the aircraft industry and has led to the avoidance of hundreds if not thousands of potential disasters. For this I am grateful; and in this article, I am not talking about RCM used in its original and purest form.
But, what I will say is that there are circumstances and industries where the discussion and attempt to implement RCM is just flat-out wrong.
Reliability Centered Maintenance was developed as an engineering process to optimize reliability and reduce maintenance costs of commercial airliners. The sheer amount of data that is generated through millions of hours in flight-time has allowed these aviation engineers to pinpoint the hot spots over the years, allowing them to design and improve the maintenance process.
The RCM approach is best known for its continued monitoring of the equipment and analysis of the data to make adjustments and improvements to the equipment and its maintenance program.
The rub with RCM is that it's methodical in its approach to implementation and execution.
Why Reliability Centered Maintenance May Not Work Elsewhere
Because Reliability Centered Maintenance requires meticulous implementation and execution, it is often not the best approach for those organizations that find themselves in a constant battle of firefighting.
In other words, when the house is burning, it is impossible to have a discussion about how the house should be built for the best fire prevention.
But, I often hear in maintenance circles—and in the mouths of consultants—that RCM is the answer.
Here are a few reasons it is not:
- The resources and manpower needed to perform RCM functions are not usually available in high volume, low margin businesses such as packaging, food, automotive, and consumer goods sectors, to name a few.
- The burning platform, such as; “do it right, or people die”, is not as intense in most maintenance organizations.
- Millions of hours of run data on machines using the exact same components and processes is difficult to come by when paper downtime logs are being used on the shop floor.
- Feedback from production workers/operators is lost in the RCM process when machines are already running in 'firefighting mode.'
If Not Reliability Centered Maintenance, Then What?
So, don’t get me wrong, there are industries and scenarios when Reliability Centered Maintenance is the answer. And in those cases, you should pursue that course. But, if you are in a firefighting maintenance mode, here are a few suggestions:
- Start by understanding exactly what the fires are and how long it is taking to get them out. Your CMMS system must have the ability to capture this data in real-time with minimal impact to the wrench-time of the mechanic.
- Have a process that captures all downtime in the production process. This will include a way to know if production is down for material, maintenance, defects, and even manpower. We consistently find that maintenance downtime is not the tall pole on Production's downtime Pareto.
- Solve the problem that is in front of you. Don’t go searching for theoretical issues when your data is telling you exactly what the issue is. Solve those simple to see issues and make sure your system allows you to see those issues clearly and in real-time.
- Employees (human capital) are the most important asset you have to help you solve problems. Your shop floor operators, mechanics and electricians have the answers to solve the easy problems if you will give them the tools to do so.
If you have done all of the above, then Reliability Centered Maintenance may be the program for your company. But if you struggle to gain control of the current process, then RCM will only add complexity and misuse of resources needed to solve the problems at hand. L2L’s CloudDispatch is the perfect tool to help your organization out of firefighting maintenance mode, by helping identify immediately those issues affecting your shop floor right now.
Revisions
Original version: 18 July 2024
Written by: Evelyn DuJack
Reviewed by: Daan Assen
Please read our editorial process for more information
Related Posts
Subscribe to Our Blog
We won't spam you, we promise. Only informative stuff about manufacturing, that's all.