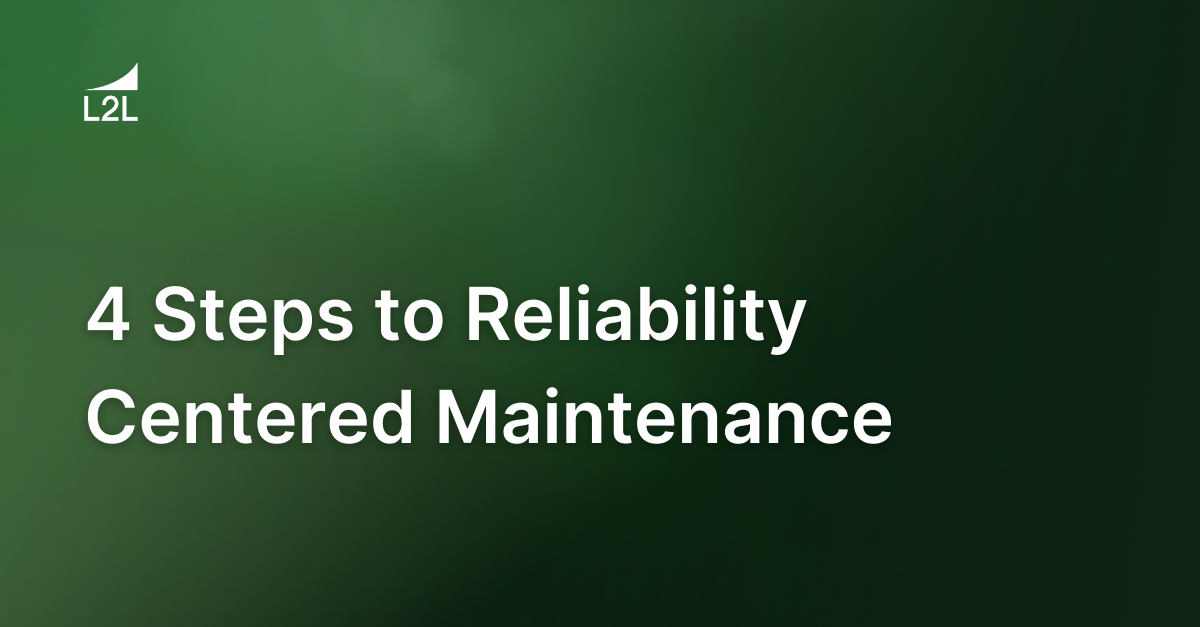
In today’s fast-changing global environment, companies are less likely to invest in high-cost reliability programs that take years to implement and struggle to provide an ROI. In some cases, equipment and products are changing faster than your reliability program has time to analyze.
If it's reliability centered maintenance you're after, it's essential to get the best information in front of the maintenance team to help aid in troubleshooting and problem-solving. Your reliability centered maintenance program should be viewed as a valuable tool and not as the overall strategy.
Basically, the maintenance department needs to be run like a business; a profit center that must provide value. Otherwise, you’ll never get any support from management and feel like you’re constantly losing ground.
A New Look At Reliability Centered Maintenance
It’s time to stop looking at the maintenance department the way we did 30, 20, or even 1 year ago.
We need to look at the maintenance department as a value add to the business that’s helping drive the overall company metrics (safety, quality, cost, and delivery).
Instead of changing a bearing out every 12 months because that’s how it’s always been done, you need to look at ways to make the bearing last longer and/or even signal the team before there is an actual problem. It’s time to start looking at utilizing all the options available to aid your maintenance team in becoming more effective. It’s time to look at every maintenance activity as an opportunity for improvement.
I was in a facility recently that has extremely high operational availability. Now their main focus is on reducing preventive maintenance time. Instead of just being satisfied with their success, they’re looking for ways to reduce costs in all areas while still maintaining a high level of availability.
I would also caution against looking at reliability centered maintenance as something that can be perfected. There will always be opportunities to improve. For example, lots of facilities fall into the “we’re world-class” syndrome. They’ve basically decided that once they meet a defined level of performance there is no need to go any further. I’d challenge these companies to set their sights much higher, something like zero downtime, zero cost, etc. Understanding that this goal is unattainable is okay: The idea is that you should always be inching your way closer and closer to this vision.
1. Beyond Reliability Centered Maintenance to Transform Your Team
Shifting your maintenance department from a mentality of maintaining toward a continuous improvement mindset with a goal of perfection should be your vision. Every maintenance organization should have a relentless focus on the elimination of maintenance (no more maintenance).
I know companies that have changed the name of their maintenance department to Technical Support. They understand the importance of changing the traditional focus of maintenance in order to create a cultural shift. This approach in thinking will help align the maintenance group with operations. Operations should be the focus of any manufacturing company. Production is what pays the bills in the end.
2. Make Connectivity a Priority with Reliability Centered Maintenance
As technology evolves, factories must evolve with it. That means understanding how the changing digital manufacturing landscape will impact reliability centered maintenance.
Next-generation of workers: One of the challenges facing manufacturers today is the fact that younger generations see manufacturing as labor-intensive, dirty work that has no future.
This generation of workers will require an environment that is stimulating; where information and communication are instant. They will not be satisfied with the way manufacturing has been in the past. The scary thing is that without these workers, manufacturing will have no future. Therefore it is imperative to address this issue before it's too late.
Mobility: Mobility will also play an important role in the future of reliability centered maintenance. Industry 4.0 is coming whether we like it or not, and one of the keys to its success will be getting valuable data in front of the right people at the right time. Mobility will be key to making this a reality.
IoT: As Industry 4.0 continues to gather more momentum, things like IoT and AI will also become more and more important. I would look at these advances in technology as tools that can help your reliability centered maintenance organization become more effective.
IoT devices are becoming cheaper and easier to implement. Imagine adding a vibration sensor to a bearing that can instantly provide data and signal maintenance when there is a potential problem.
Now imagine implementing this at a very low cost in hours with no development or consulting resources needed. The truth is this technology is already here and companies are already starting to reap the benefits.
3.Make Production Your Objective
Like I mentioned earlier, the purpose of any reliability centered maintenance organization should be to support production. Remember, without production there is no maintenance.
No manufacturing company views themselves as a maintenance company, and for good reason. With this understanding, doesn’t it make sense that maintenance measures its success on things like production efficiency, delivery, quality, etc.?
4. Implement a Real-Time Scoreboard to Optimize Reliability Centered Maintenance
Everyone in a manufacturing plant should have visibility to the current (real-time) status of operations. When you walk into any Toyota facility you’ll see the current condition of production everywhere. That’s because they understand that everyone is there to manufacture their products.
Do you have a real-time scoreboard in your facility? Is maintenance, engineering, etc. focused on those scoreboards?
One way to look at this is if manufacturing was an NFL football team and production was the offense and reliability centered maintenance was the defense. No matter what the defense does, good or bad, the only thing that matters in the end, is the score on the scoreboard.
It won’t matter much if maintenance has 100% PM on-time completion, or a world-class rating if production cannot produce products at a lower cost and higher quality than their competition.
Ready to make reliability centered maintenance easy? Discover how it's possible with L2L's groundbreaking software, CloudDISPATCH. Schedule a demo today!
Revisions
Original version: 18 July 2024
Written by: Evelyn DuJack
Reviewed by: Daan Assen
Please read our editorial process for more information
Subscribe to Our Blog
We won't spam you, we promise. Only informative stuff about manufacturing, that's all.