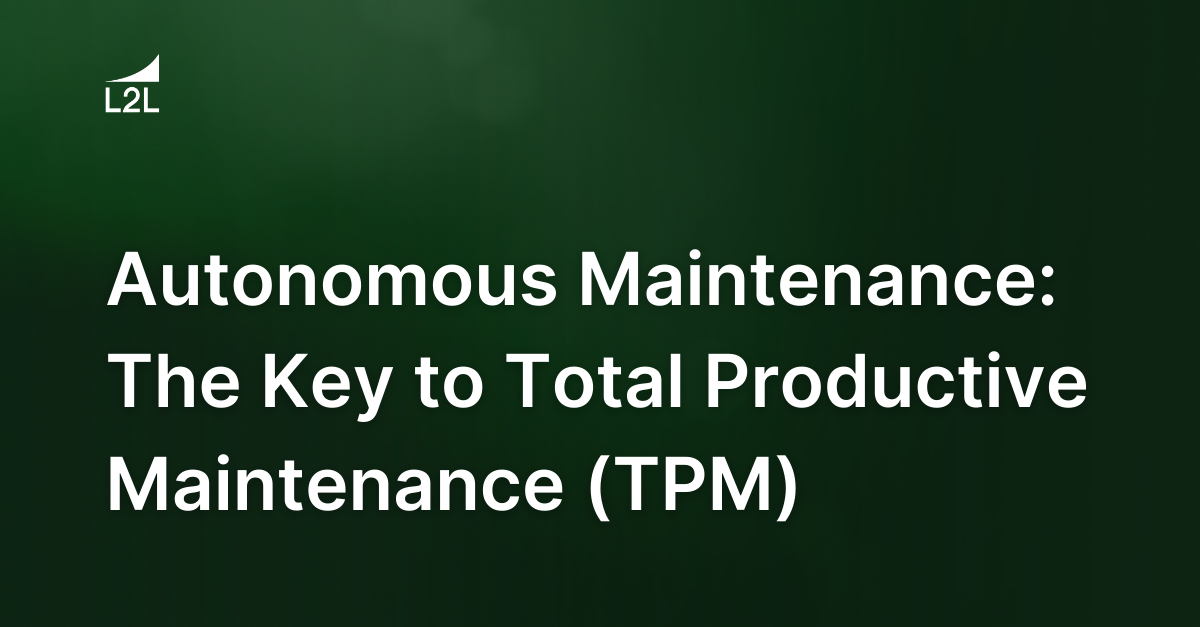
Arriving at my parents' house one afternoon, I found my 16-year-old sister lying on the couch, distraught, and sobbing uncontrollably. When I asked what was wrong, all I could get out of here was that she "broke the car." After trying to calm her down, I asked what she meant. She then began to describe a loud pop followed by the engine making a loud hissing sound like a train.
See, my sister had only recently turned 16, and my parents had purchased her a used car. My father had taken great care to teach her that at every 3,000 miles, she was to take the car to the garage and get the oil changed. Her anguish was around the fact that she did not have the time to take the car in, and she was 78 miles over her 3,000-mile interval, thus convincing her that was the root cause of the issue.
It turned out that the car had blown a spark plug clean out of its hole. If you are mechanically inclined, you know that has nothing to do with the oil change being 78 miles past due. But what the story relates is that even at a basic skill level, an operator of a car has certain obligations to the maintenance process of an automobile. If given the proper training and tools, they will take this obligation seriously.
We see this type of dedication and obligation every day in manufacturing plants. Like the operators of cars, operators of production equipment need the same training and tools to take care of their machines. For the last 30 years, the tool that has been deployed for this in manufacturing has been Total Productive Maintenance (TPM) — and within that, the pillar of autonomous maintenance.
Overview of Total Productive Maintenance
Originating as a concept in the 1950s by Seiichi Nakajima, total productive maintenance began as an overall strategy to properly manage production equipment and strengthen the relationship between production and maintenance by giving operators greater ownership over equipment.
Later in the early 1970s, these concepts were published in English and began to emerge in Western production facilities by the early to late 1980s. The concept of allowing the operator to play a role in the daily maintenance of the production equipment slowly but surely found its way into almost every corner of Western manufacturing.
Although Nakajima introduced total productive maintenance with six original pillars, most companies who practice total productive maintenance use the evolved eight-pillar approach for defining TPM in their factory. These pillars are:
-
Autonomous maintenance. The incorporation of daily maintenance tasks with the operator of the equipment. Creating ownership and involvement as the operator becomes part of the overall maintenance process.
-
Planned maintenance. The process of routine maintenance being planned and scheduled in order to efficiently use resources and maximize wrench time.
-
Quality maintenance. The focus of using maintenance as a driver to improve and influence the quality of product being produced on the line.
-
Focused improvement. The concept of using good data to point maintenance and machine improvement technicians in the proper area in order to maximize impact on the process.
-
Early equipment management. The identification and improvement of machine design weaknesses, then incorporating those designs into new machinery and enhancing the reliability (also known as Reliability Engineering).
-
Education and training. Understanding the skills required and ensuring the maintenance techs and operators have the necessary skill to perform routine maintenance functions properly.
-
Safety, health, environment. The use of machine reliability improvements to reduce safety incidents, improper use, and disposal of materials such as oils and solvents, to name a few.
-
Administration. Sustaining a reliability culture throughout the organization by focusing on the safety, quality, and throughput of the equipment at all levels.
The reason it is important to understand the eight pillars is that all too often, total productive maintenance within factories has been boiled down to only one of these pillars: Autonomous Maintenance or Operator Performed Maintenance.
The key is to understand the power of operator maintenance and its role in the overall maintenance strategy.
An Autonomous Maintenance Foundation
Understanding why and where autonomous maintenance fits into an overall maintenance strategy is vital for any organization trying to move towards a proactive maintenance culture.
Autonomous maintenance tasks, such as daily cleaning and inspection, allow operators to identify and monitor small abnormalities on machines and in the process. Finding and fixing these small problems in their infant stages reduces the need for greater reactive maintenance measures that cost vital time and money.
During one autonomous maintenance Kaizen event, we had teams on the shop floor performing routine cleaning and inspection on hydraulic inertia welders. Because a great amount of power was needed to generate the energy for the inertia, each welder was powered by a high-horsepower electric motor housed in a soundproof enclosure. As the teams cleaned the motors, they discovered that a motor's cooling fan under the shroud had become brittle and begun to break apart.
Further investigation found that the fans mounted on the soundproof house were installed incorrectly. The air from the fan on the motor was running opposite the cooling fans mounted on the enclosure. The fan was getting no cool air, and the hot air in the house swirled around, causing the temperature to rise to the point of failure.
Looking back, the team found that over the past few years, these motors had failed to the cost of tens of thousands of dollars. One can only guess at the thousands of dollars and countless labor hours avoided by finding this abnormality during the cleaning and inspection phase of TPM.
So why, with incredible results, do TPM efforts flounder to move forward and deliver on the results?
The answer is simple: complexity!
The Challenge of Autonomous Maintenance
Performing these simple tasks on a daily basis is usually a relatively easy ask of the production operators. The complexity comes into play with the daily management of the entire system.
The daily management of paperwork, checklists, abnormality repairs, etc. can be daunting. In most cases, companies hire a Total Production Maintenance Coordinator devoted to the single task of ensuring paper inspection sheets are distributed, filled out, and picked up on a daily basis.
In a large factory, that is all but impossible, so people stop doing it. It only takes about two days for operators to realize, "If it's not important for them to get me a new checklist, then it must not be important for me to do it." But this is all changing.
Autonomous Maintenance Made Easy with the Cloud
With new cloud-based technology, daily cleaning and inspection checklists can now be delivered directly to the operator via a mobile device. Specifically written for their machine, these task lists can be updated remotely in virtual document control and changed the very next day without any legwork to apply the new change.
Abnormalities found during the inspection can quickly be entered into the system with no tags or paperwork and prioritized along with other maintenance work scheduled for the machine. Finally, cloud-based TPM programs have all of the data stored in real-time and archived in history. It is all immediately accessible to maintenance for troubleshooting and teams for root cause analysis efforts.
We must understand that when speaking about maintenance in a factory, we are not talking about a group of people, nor are we talking about real estate in the factory where toolboxes are stored. We are talking about the system or the process chosen by the company to care for, repair, and improve the production machinery.
Unfortunately, that system is often reactive maintenance. But the companies that are winning choose proactive maintenance, and that choice will always involvement of the production operator.
With new cloud-based systems like L2L's CloudDISPATCH, it is becoming much easier to manage maintenance operations. See how L2L can put new life into your TPM process. Let us schedule a demo for you today!
Revisions
Original version: 3 September 2019
Written by: Eric Whitley
Please read our editorial process for more information
Related Posts
Subscribe to Our Blog
We won't spam you, we promise. Only informative stuff about manufacturing, that's all.