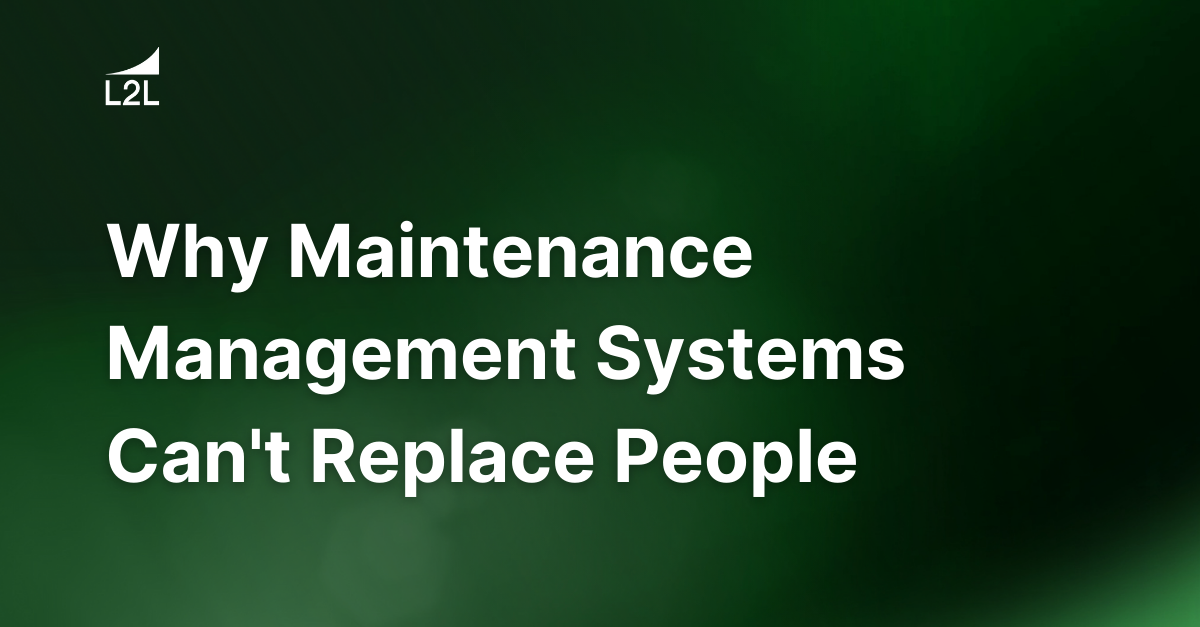
In every factory across the world, there are a number of maintenance management systems designed to support the manufacturing environment (MES, CMMS, ERP, etc.).
Unfortunately, most of these maintenance management systems assume that conditions are ideal. They assume that the machines are ready to run, the right material is there, the people are properly trained.
It doesn’t take into account any other factors that can impact a plant’s processes. As a result, these systems also operate on the assumption that any mishaps are the fault of the machine.
When something goes wrong, fingers point to maintenance. After all, the fault can only lie with worn or malfunctioning components, right?
The truth is, this only accounts for a small percentage of challenges in manufacturing.
A lot of times, even the machine issues aren't necessarily the machine’s fault. What I mean by that is the machine didn't actually do anything wrong. No component failed. What has happened is something outside of the machine’s ability to control.
For example, incoming raw materials could cause an issue of parts jamming up because these parts are on different parts of the spec. Maintenance is brought out to adjust the machine, so most facilities see an event like this as being a maintenance issue.
It’s not a maintenance issue.
It’s more of a product issue.
And really, the systemic problem goes all the way back to the product and machine design. So, if you want to correct these types of issues, you've got to dig way back to the systemic causes and correct it there. Otherwise, it's going to continue to happen. It's going to continue to plague your manufacturing environment.
Other factors (outside of machine issues) that may influence a plant’s productivity
- The operator isn’t trained properly
- The maintenance technician isn't trained properly
- No standards for training
- No standards for doing repairs (so every maintenance technician is repairing the machine differently, causing all kinds of problems)
In lean manufacturing, there's an understanding that without standards, we can never improve. If we don't have a baseline to work from, how can we ever improve from the position that we're already at? It's virtually impossible—like shooting at a moving target.
Your Maintenance Management System Needs Human Creativity
So, per my previous point, a lot of vendors and companies are heavily focused on machine issues. They ask questions like:
- Can the machine tell me what's going on?
- Can sensors tell me what the problem is?
- Can I put artificial intelligence in place to identify patterns so I can go out there and predict problems before they ever occur?
While those technologies exist and can be helpful, the machine cannot see everything that’s impacting the facility. The machine doesn't know that:
- The forklift dropped a pallet of parts, and now we're out of parts
- The new operator is being trained but doing some things incorrectly
- There’s a storm outside and all trucks are delayed
- Our lab test came back and we have to quarantine product
- We switched to a new supplier and now the components won't run through the machine
- We ran out of spare parts
The machine definitely doesn't know that the reason we ran out of spare parts is because a purchasing agent went and found a cheaper vendor to buy the parts from, but those parts are lower quality and don’t last as long.
There is a lot the machine doesn’t know.
But still, plants put the focus and money on maintenance management system issues rather than looking at the entire picture.
In order to capture the entire picture, you have to engage the people on the floor to tell you what's going on. There's no technology out there that will be able to identify these issues like the human mind can.
Humans are very good at handling abnormalities at handling things that don't fit in the pattern.
Computers and technology have to have all those different scenarios addressed in their code before they can ever understand them.
In other words, there is no substitute for human creativity and problem-solving.
And before you go there, AI isn’t even close.
The Limitations of AI
Artificial Intelligence works to analyze data to understand patterns.
It can be a valuable part of your maintenance management system, but only if you have the data you need. And I would even say that the machine data and the data that most companies are focused on isn't even close to half the data needed.
If you're only looking at a small percentage of the data needed, you're going to make some very poor and costly decisions.
You're going to make a lot of mistakes. And in the end, there will never be a payback.
There will never be an ROI.
Because you don't have the full picture. You're making decisions and you're focusing on problems based on a very small percentage of the actual data needed to truly understand what the problem actually is.
That's what Toyota understands. That's what companies that are leading the industry understand and they understand it very well: Things will go wrong.
We have to learn from those things. We have to make those problems/abnormalities as visible as possible. We have to engage with them. We have to solve them. We have to follow up on them. And we have to hit the systemic cause of those problems or they will continue to reoccur.
A Case Study
Let’s go back to the example of parts jamming. If new material comes in, it won't run through the feeder tracks. Maintenance goes out and adjusts the feeder tracks to accept the new material. As soon as we run out of material and change over to new material, maintenance is going to get called out there again to adjust the feeder tracks.
When we're doing these types of adjustments and this type of compensation, it opens this way up for quality issues.
This is actually an example that one of our customers shared with us. And it's a perfect example of why maintenance management systems need people.
Before implementing L2L as their maintenance management system, their daily meetings revolved around yesterday’s big issues. Oh, the shaft on the cylinder broke and it took us six hours—we had to re-machine it. We had to re-engineer some things and we were down for six hours.
What they don't talk about is the fact that maintenance went out and adjusted the feeder track 20 times this week. Each adjustment took 20 minutes. This happens every week. If you crunch the numbers, that’s a lot of time wasted.
A lot of lost production.
Adjusting the track 20 times a week is not fixing the problem. The fix is to understand why we're having to adjust the track and what we can do to eliminate that adjustment completely. And in their case, they found that the machine was never designed to accept raw materials at both ends of the spec.
Their first solution was to go understand the supplier’s process and see if they could control the parameters a little tighter than the spec. What they found was the supplier had three machines running these parts. And two of the machines were on the low end of the spectrum, one was on the high end of the spec.
They agreed to changing all machines to run on the middle of the spec and put some gauges in place to ensure that they're staying fairly close to the middle of the spec.
That actually solved the problem. Track adjustments went down to zero. Their supplier had a control in place to make sure that everything stayed that way from here on out. They really solved that problem.
But systemically, they didn't solve the bigger problem: Why did it happen in the first place?
And to solve that problem, they had to go look at their engineering and development process to understand what checks are put in place when a new product is developed. They needed to understand the process parameters, the machine parameters, and the machine specifications needed to run all the products within that specification.
They've now addressed that issue and they've addressed it across the board.
They have a process in place now to ensure that when new products are designed, they're also addressing all the process issues and machine design issues to ensure that the product can run through the process. That's called design for manufacturing. That's called the design for manufacturing, and that's very important.
That solves thousands and thousands of problems that are going to have more impact on that company than any machine-downtime-related issue. Any predictive maintenance related issues, any adding AI to the analyze the data and see what the heck's going on? I mean that one issue right there and get into the systemic cause? That is what makes companies like Toyota so powerful. That's what separates the best from the rest.
Discover the maintenance management system that's designed to work with human creativity--schedule your CloudDISPATCH demo today!
Revisions
Original version: 18 July 2024
Written by: Evelyn DuJack
Reviewed by: Daan Assen
Please read our editorial process for more information
Subscribe to Our Blog
We won't spam you, we promise. Only informative stuff about manufacturing, that's all.