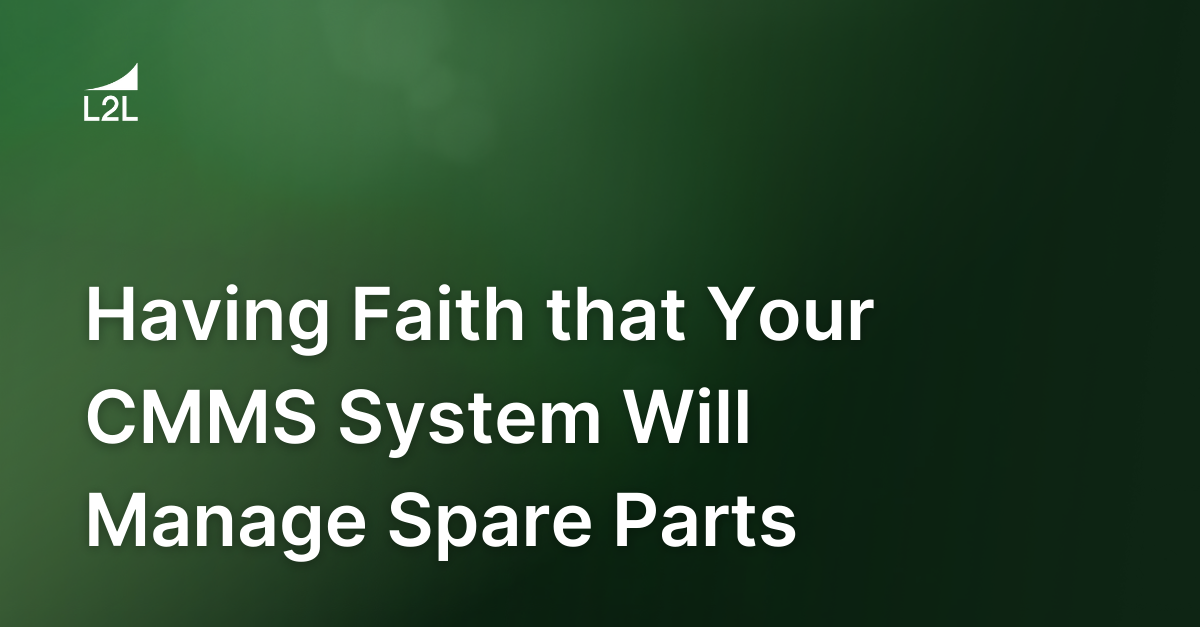
Spare parts are like an insurance policy. When you need them, it's nice to have them on the shelf, as it can save you thousands in downtime costs.
I have seen some places that let a $150 sensor hold them up for two days of downtime with the line producing at $250 an hour. It doesn’t take long to do the math: that sensor on the shelf could have paid for itself in 45 minutes, but instead it cost 45 hours and $11,250 in lost production.
Then, there is the cost of expedited shipping. You have to fly the part in first class to get it to your plant and then the labor has to go back and install the part again to get the machine back up and running. All this instead of doing preventive machine checks.
Be smart about what you keep on the shelf, and remember to look at ALL costs--not just the cost of the part. For example:
- What does it cost to expedite the part?
- How much labor is spent getting this done?
- How much production is lost and how much potential revenue loss occurred?
Some plants stock low inventories to keep costs down, but they run into the situation above. They're saving pennies and losing dollars. Successful plants have a way to know that their inventory levels are correct. In order to do that, you need to have a way to easily document what parts are used. This is one function of effective CMMS system.
How a CMMS System Can Make Spares Management Easier
There are many ways that CMMS system can help make managing spare parts easier, but four of these stand out as most critical to engaging your maintenance team in achieving the real objective of minimizing downtime:
- You need real-time visibility of when parts are consumed on the equipment
- You need to quickly locate spare parts in the warehouse
- You need a system to help increase accuracy of spare parts inventory
- You need history reports to help you calculate future cost of spares, and better manage your maintenance budget as a result
Let's take a closer look at each of these points below.
1. Real-Time Spares Consumption with CMMS System
The technician needs to be able to look at history and quickly see what parts have been consumed on the equipment they are working on, so that they can make a better call on how to proceed when troubleshooting. Visibility of the equipment history and parts used will show the health of the equipment, and if there are any abnormal issues that could consume spare parts at a faster rate.
A CMMS system also helps those companies that are lucky enough to have an MRO (Maintenance, Repair, Operating Supplies) staff to manage the inventory and to see the parts usage as it happens. That way, they can quickly react to an abnormal pull rate (part usage) instead of waiting until after the nightly back-flush (inventory update) takes place and you find you're out of a critical part that you need.
2. Locate Spare Parts with CMMS System
Nothing is more frustrating for a technician than to have to go shopping in a spares storage room and pulling drawers in order to find what they need to get the line back up and running.
Some may have an electronic system to help locate parts, but you feel like you have to have a secret decoder ring in order to search the right way to find the part you need.
A good CMMS system has a dynamic search function that will easily find the part location in the inventory. This is critical, especially for cases where you only have a partial part number to work with. I have spent time pulling drawers, and I can tell you the faster I can find the part and get out to the line, the happier the line leaders (who are circling around asking when the machine will be back up and running).
3. Use CMMS System to Keep Inventory Accurate
Technicians are often in a hurry (remember the line leader). Sometimes they forget to write down on the storeroom clipboard what they took out of inventory. Or, maybe the engineer just wanted to see if the part would work for a project and forgot to bring it back. There are many scenarios that cause inaccuracies.
One way to ensure your spares inventory records match your actual inventory is to place an armed guard with two junkyard dogs in the spares room.
The preferred method, however, is to have a digital spares system that everyone can rely on.
You can only count on the data if people are consistently inputting it at the right times. In order for that to happen, the juice has to be worth the squeeze. Inputting the data has to be easy enough that it's worth the time to input it.
I may have done this a time or two as a technician: When a new shipment of parts was received that would often break, I may have been tempted to grab 4 or 5 of them and stow them away for when I needed them to keep the line running.
People just want to do their job, and if they have faith that parts will be on the shelf when they need them, they won't be tempted to hoard them (which causes several problems). The goal of every parts crib should be to help keep the production lines running. Therefore, having the right parts on the shelf when needed is critical.
CMMS systems can help you do exactly this. One element in keeping accurate inventories available and costs down is to have accurate parts usage history and use that history to set your min/max levels. As you do this and parts are available when needed, technicians will come to have faith that the parts will be there when they need them.
4. Use CMMS System Reports to Reduce Inventory Costs
Who owns the downtime of the equipment? Both production and maintenance does, but maintenance has the responsibility to maintain the equipment and therefore needs to own the KPI to reduce the spares costs each year. So why not give them a tool that has great cost reporting capabilities to keep their destiny in their own hands? With CMMS system you can hold them accountable for cost reduction, in addition to having:
-
- History reports that can help you calculate future cost of spares, and better manage your maintenance budget as a result.
- Data to analyze cost trends and set an optimal reorder point so you're never left waiting for parts.
- The ability to chart parts usage to see trends in equipment behaviors or even training needs.
I have seen successful spares groups that actually do a RCA (Root Cause Analysis) when a machine breaks down and they don’t have the part. They own their destiny and they do whatever they can to ensure continuous availability of the equipment.
Cloud-Based CMMS System for the Ultimate Spares Management Process
The four points above are a few of the benefits you can enjoy by implementing a CMMS system. However, most systems simply aren't easy enough to use. Your workforce may struggle to identify and prioritize your top problems that need to be solved throughout the plant.
When only a few system admins can access data, it impedes the rest of the people in the plant from helping to solve problems and drive improvement. The real benefits come from engaging your technicians in real-time by making the right data available at the right times.
That's where cloud-based a CMMS system comes into play. Check out CloudDISPATCH--a next-gen CMMS software trusted by companies like Autoliv and Goodyear--to see how cloud-based CMMS software can help you achieve your spare parts management.
Revisions
Original version: 18 July 2024
Written by: Evelyn DuJack
Reviewed by: Daan Assen
Please read our editorial process for more information
Related Posts
Subscribe to Our Blog
We won't spam you, we promise. Only informative stuff about manufacturing, that's all.