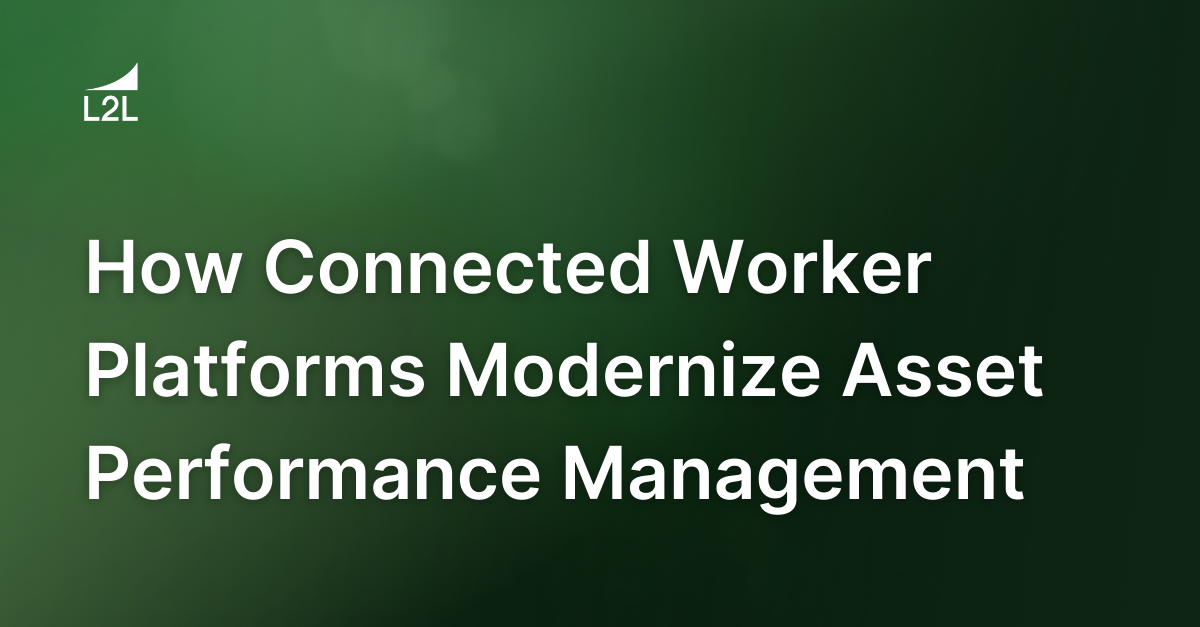
Manufacturing can be pretty difficult, and the same challenges have persisted for businesses everywhere. Equipment breaks down, physical asset reliability is largely unknown and asset performance is something you have to constantly keep track of. Unplanned downtime as a result of equipment failure causes you to miss your quotas — and the end result is a tired and stressed-out team of workers.
Thankfully, it doesn’t have to be this way. Manufacturing technologies have evolved, and we’ve discovered new solutions to address these problems. For example, what if your workers could stay connected in ways that make the communication system in Star Trek look like an ancient relic? What if your employees could share data, images, video and audio in real time? What if they could perform complex repairs without necessarily needing to be taught how through augmented reality?
Arthur C. Clarke is quoted as saying, “Any sufficiently advanced technology is indistinguishable from magic.” It’s time for your business to prove him right. A combination of asset performance management (APM) software and connected worker solutions can make common issues of expensive repairs, unplanned downtime and missed quotas problems of the past. It all starts right here.
A brief history of asset performance management (and why it matters)
It all started in 1965 with the invention of computerized maintenance management systems (CMMS). This was an innovative software solution streamlining maintenance information into a centralized computer system. It was the first time computing had been combined with asset management.
It was like the flip phone before the iPhone: Cool, stylish and exceptionally useful — but doomed to be obsolete within a few years. As technology advanced, allowing networks to span across multiple computer systems over several sites, enterprise asset management (EAM) started taking over to bring these locations together. By the time the 1990s came around, asset performance management had arrived — a new, smarter and data-driven approach utilizing machine learning and predictive analytics.
If CMMS was the flip phone of the manufacturing industry, then the asset performance management market was the iPhone with its vastly new capabilities. The implications for monitoring asset health and smartly determining when predictive maintenance was warranted became the new standard for manufacturers worldwide. Asset performance management is a sophisticated solution to a problem that can be described in two words: “unplanned downtime.”
They don’t make EAMs like they used to, and that’s a good thing
That’s not to suggest that EAMs are obsolete, however. A modern EAM has little in common with traditional EAM solutions. It’s important to understand what an EAM is and what it isn’t. Traditional EAM systems used to be difficult to use and couldn’t provide a modern data analytics platform able to keep up with the ground floor. Sure, they might have had their uses for management, but the workers in the plant didn’t have much to gain from them.
Modern EAM systems aren’t like that. In addition to being far easier to use, beneficial for plant workers and easily combined with asset performance management software, modern EAMs provide solutions for elements like:
- Asset health.
- Spare parts management.
- Supply chain insights.Projected arrival dates.
- Centralized data storage.
The ultimate goal is to bring predictive maintenance and production data into one singular hub — and modern EAM systems deliver
Why it’s important for manufacturers to stay up-to-date on the latest APM solutions
Asset performance management solutions are just like any other smart technology: Keep up with the times or be left behind.
For example, think about how the iPhone was revolutionary in 2007 and then times changed. No one’s using the first iPhone model anymore because it’s impractical and unsafe from a data security standpoint. The original iPhone just can’t keep up with new technology, like the ever-increasing processing demands from apps and wildly more advanced, smarter hardware and software components.
Asset performance management is no different. As industry standards change and new technologies are introduced into the manufacturing process, the software monitoring asset health must also stay informed. Simply put, the manufacturing process and its assets are constantly updating their standards to prevent equipment failure, so asset performance management has to be revised to stay up to date to keep up with those new requirements.
Improving asset performance management with connectivity
The asset performance management market was born after networking technologies advanced enough to connect sites together into one centralized computing platform. The sites are connected — why not connect the workers, too?
A connected worker solution uses smart technologies to keep workers in constant contact both visually and audibly while sharing constant streams of real-time data. It’s more than just having a headset and talking to one another — it’s sharing information on the fly using advanced technologies such as augmented reality and on-the-go data access. Workers can share not just their speech, but images, videos and all that they see in front of them. It’s a collection of technologies coming together to create an effective team of employees with more information being shared than ever before. Star Trek, eat your heart out.
Benefits of better asset performance management
Connected worker solutions have tons of benefits when implemented with an APM data analytics platform, and the most notable is that your workers will be able to act on the information provided by your APM efficiently and swiftly. They’ll be able to handle complex maintenance tasks even if they don’t necessarily know how. A connected worker could, for example, see how to repair an asset right in front of them using augmented reality, which means they could be guided through how to fix a problem without needing to immediately memorize the process.
APM is all about minimizing unplanned downtime through data analytics and condition monitoring. It’s how a business can tell when equipment needs repairs. Combined with a connected worker solution, those repairs can be done swiftly by almost anyone, without the need to call for a team of specialists. That’s smart technology taken to a new level.
APM and connected workers: Manufacturing has never been so sci-fi
With a combined APM and connected worker solution, unplanned downtime can be reduced or eliminated, long-term repair costs could go down dramatically, unexpected asset failure might be a thing of the past and your business’ overall productivity can reach unprecedented heights. This is truly the future of manufacturing (and the end of missed quotas).
Contact us today and book a demo to get started revolutionizing your manufacturing technology.
Revisions
Original version: 7 November 2022
Written by: Eric Whitley
Reviewed by: Daan Assen
Please read our editorial process for more information
Related Posts
Subscribe to Our Blog
We won't spam you, we promise. Only informative stuff about manufacturing, that's all.