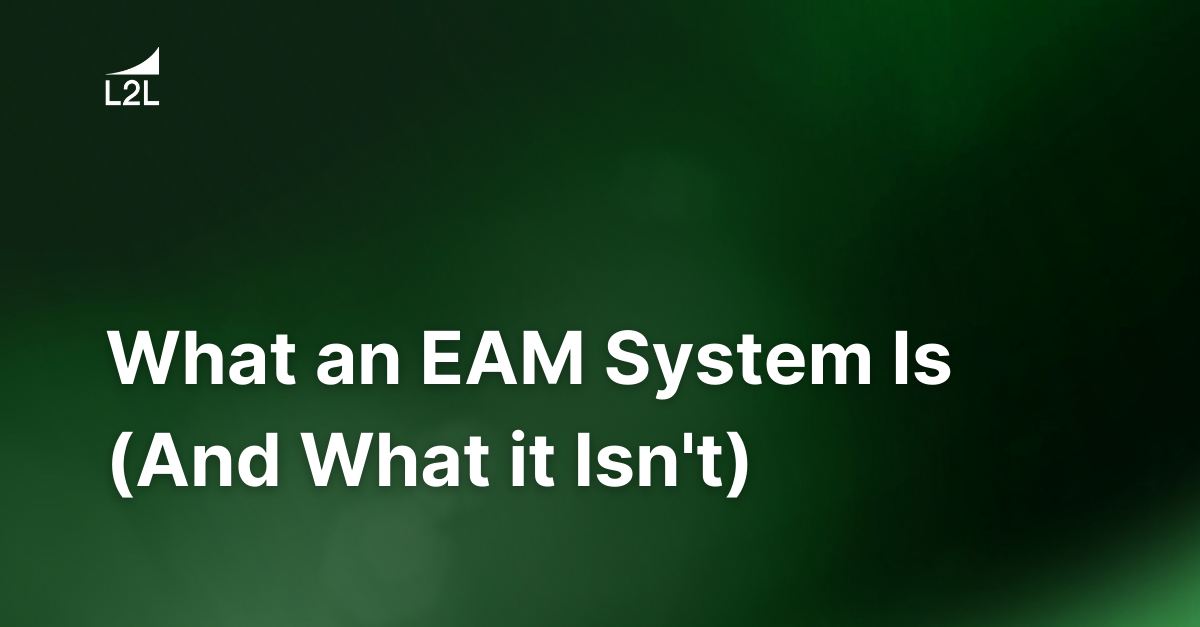
Estimated read time: Seven minutes
As any manufacturer knows, “close enough” just doesn’t cut it in this industry, especially when it comes to setting clear expectations. After all, it’s not like you’d want to go through the entire manufacturing process only to be surprised by the final result every single time, all because you were relying on “close enough” work to get the job done.
The same goes for manufacturing solutions like enterprise asset management (EAM). If you don’t know exactly what you’re getting into with an EAM system, you won’t be able to anticipate the results — and, in turn, you won’t reap the rewards like improved asset performance and valuable EAM data.
It’s time to kick guesswork to the curb. Today, we’re going to find out exactly what an EAM system is, what it isn’t and what you should expect from using an EAM system to manage your factory assets. Let’s get started!
Meet the modern enterprise asset management system
Imagine asset management is like ice cream, and it’s being served fresh just for your plant. If you don’t know what all the flavors are, you’re probably going to grab the one you’ve been choosing for years, missing out on a rich experience in the process.
Let’s take a closer look at those “flavors” to find out what your options are when it comes to asset management approaches:
-
Manual asset management: Likely the most familiar (and the most outdated), manual asset management means work orders are paper-based and every bit of asset data lives in a spreadsheet.
-
Traditional EAM software: This EAM system is a step up from manual asset management, but as far as flavors go, it’s falling out of favor. That’s because it simply doesn’t fit the modern factory anymore. Cumbersome, difficult to use and unable to provide the kind of robust asset data you need, end-users on the plant floor avoid using traditional EAM software like they avoid octopus-flavored ice cream (and yes, that exists).
-
Modern enterprise asset management software: When it comes to asset management, modern EAM software has all the best ingredients and flavor . It’s intuitive, easy to use and designed to provide value for end-users (not just management), making it easier to perform tasks like data capture and maintenance management. Simply put, it’s a better way to satisfy your craving for clarity, simplicity and improved efficiency on the plant floor.
Note that the main difference between these three approaches is their utilization of technology. Unlike manual asset management and traditional EAM software, modern EAM software unites both maintenance and production data, creating a comprehensive view of your physical assets and of how to harmonize production and maintenance scheduling needs. It also brings visibility by illuminating (or even anticipating) the need for preventive maintenance. And Modern EAM has more than a few solutions for spare parts management, including supply chain insights, projected arrival dates and centralized data storage that funnels all asset information into a single hub.
So that’s what modern EAM systems are. Now let’s find out what they aren't.
EAM software vs. ERP
Enterprise asset management is like the sibling of enterprise resource planning (ERP). They don’t necessarily offer the same benefits or cover the same manufacturing processes, but they do make a good team when implemented in the right way.
Here’s a closer look:
ERP
With an ERP system, you essentially get a digitized brain to help run your manufacturing plant. This centralized database allows you to view mission-critical data in one place, including:
-
Financial data, like payments and receivables.
-
HR data covering your “human assets.”
-
Inventory control, including supply chain management and the purchase and delivery of raw materials.
-
Timing for product building, shipping and sales.
While this information is certainly useful, you may have noticed there’s something missing: asset management. When it comes to managing assets, scheduling preventive maintenance and monitoring each work order, you’ll need a complementary approach.
EAM
If ERP is the brain of your manufacturing plant, EAM is the heart and immune system. It helps optimize and protect the moving parts — that is, the physical assets — within your organization, empowering predictive maintenance, improved asset performance and more.
Naturally, an EAM solution may often rely on data from an ERP to get the job done — for example, supply chain, maintenance costs and inventory management information. That’s why you need a system that can combine these functionalities to maximize your benefits.
Getting the best of both worlds
The best way to combine the brain and heart of your factory is to choose a tool that combines maintenance management with your plant’s production data. Modern EAM software is capable of doing just that, providing a truly comprehensive view of everything that might be disrupting production — from machine breakdowns or abnormalities to material, quality, and other areas where disruptions typically occur.
EAM software vs. CMMS
Another thing modern EAM software isn’t is a computerized maintenance management system (CMMS). Let’s take a closer look at why these two similar systems are different:
CMMS
Return, for a moment, to the ice cream simile. Traditional CMMS is like one scoop, which is just enough to get a taste of this chilly snack. That “taste” includes plenty of benefits, like:
-
Providing a database of asset performance management and quality management data for asset managers.
-
Supporting asset tracking tasks.
-
Budgeting for overall maintenance cost and asset performance management.
-
Capturing financial asset data, including purchase prices and depreciation rates.
-
Maintaining a list of physical assets.
-
Controlling preventative maintenance tasks and maintenance process documentation.
-
Organizing maintenance personnel based on asset hierarchy.
The unfortunate truth is that one taste of your favorite ice cream often isn’t enough — especially when you’ve got a whole manufacturing plant or network of plants to feed. That’s why sizable manufacturers need something more robust than traditional CMMS.
EAM
Enterprise asset management generally covers all the functions of traditional CMMS. However, modern EAM software takes that one scoop and adds a whole lot more — so you get all the same benefits on a much larger scale. While a traditional CMMS focuses mostly on asset maintenance, modern EAM software helps manage the entire asset lifecycle, preventing downtime and dodging disruptions across the entire plant floor, including both machine and non-machine related issues.
What modern EAM software can do for you
Now that you have a clear idea of what EAM is and isn’t, let’s find out what modern EAM can really do:
-
It manages each stage of the asset lifecycle: The asset lifecycle has four key stages — planning, acquisition, utilization and disposal. Modern EAM software can help you navigate every stage with confidence by guiding you through key processes, including but not limited to preventive maintenance, maintenance management and the effective documentation of every work order.
-
It supports overall equipment effectiveness (OEE): When it comes to OEE, there’s no better choice than a modern EAM solution. By definition, modern EAM software is designed to help show your physical assets some TLC, and it does this by flagging abnormalities in asset performance, improving maintenance response time and efficiency, reducing downtime and boosting efficiency across the board. This in turn improves quality through better performing equipment and increased process consistency, which reduces costly scrap and rework.
-
It enables proactive responses: When coupled with machine integration or sensors, modern EAM software can help make sense of data and predict when your assets will need repairs and maintenance, what tasks will be required and how exactly you should respond. This information is always at your fingertips, which means a work order can be scheduled long before a potential issue becomes a really big problem.
-
It makes data more valuable: It’s one thing to capture data in droves; it’s another thing entirely to use that data to improve your manufacturing process. With modern EAM software, you’ll have all the tools you need to put plant data into context, narrowing or expanding your view as necessary to be sure you’re making informed decisions about a machine, line, plant, or at the enterprise level.
-
It removes barriers: When data capture is frustrating, maintenance documentation is inconsistent, asset utilization is a guessing game and your spares stock is a big question-mark, there are about a million barriers between you and operational efficiency. Modern EAM software is designed to overcome those barriers, helping data flow smoothly from one side of your factory to the other and creating a unified version of the truth along the way.
In the end, the difference between modern EAM software and other asset management approaches isn’t just about technology — it’s about how you put that technology to work for your enterprise.
Modernize your plant
Enterprise asset management has come a long way since spreadsheets and paper documents — but if you’re not on the modern EAM software bandwagon, you’re still missing out. Modern EAM is the bridge uniting maintenance and production data, and giving you the cutting-edge tools to manage production disruptors across the entire plat floor, empowering you to turn everyday struggles into everyday wins. In fact, with modern EAM software, asset maintenance is just the beginning.
If you’re ready to modernize your plant with the latest EAM software, book a demo today to see what our platform can do for you.
Revisions
Original version: 18 July 2024
Written by: Evelyn DuJack
Reviewed by: Daan Assen
Please read our editorial process for more information
Related Posts
Subscribe to Our Blog
We won't spam you, we promise. Only informative stuff about manufacturing, that's all.