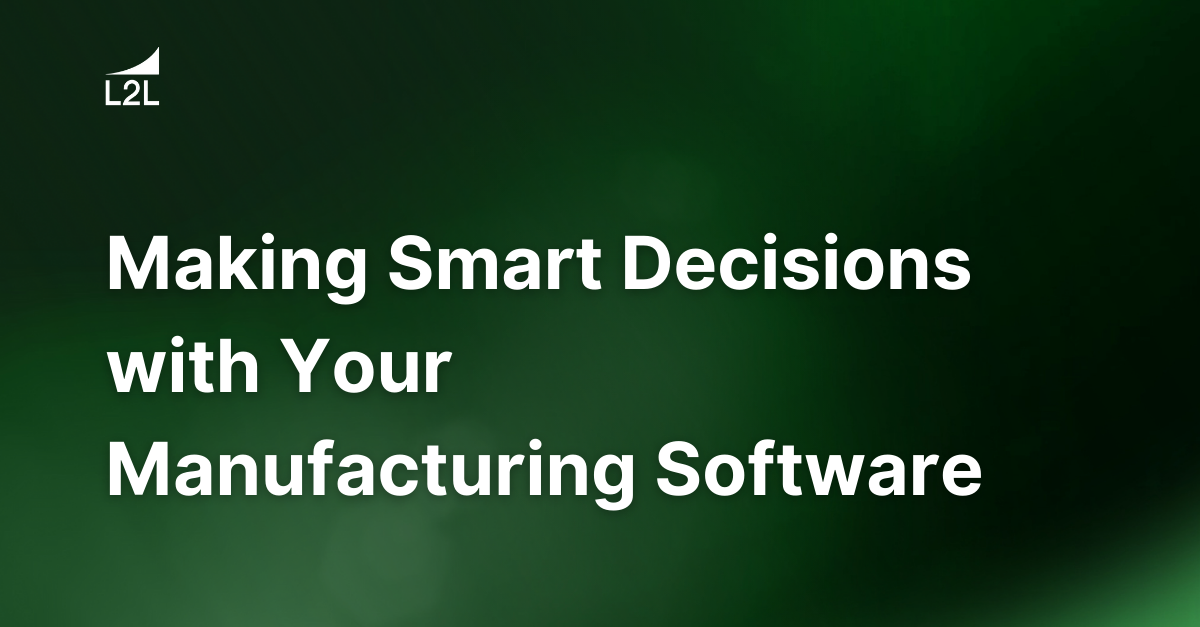
With the advent of the digital age, many industries have been deploying systems and technology solutions to transform their business processes and cultures. Manufacturing Software is one of the tools often pursued during these initiatives in the hopes of capturing the competitive advantages they proffer, such as improved efficiency through process performance feedback, coordinated execution of activities on the shop floor, and traceability of consumables and material.
The hope is to capture benefits from the outset of the product lifecycle management process to the end of production. This is achieved through both independent and automated aggregation, via IoT-enabled devices of data from within processes, as well as through integration with other platforms. Thus providing a holistic perspective on a company’s process of generating product and customer value.
Who Uses Manufacturing Software
Although implementation of Manufacturing Software continues to propagate across various global industries, it has become firmly rooted in some segments based on its ability to address explicit needs for those manufacturers.
Food and beverage producers operate under strict regulatory guidelines to ensure safe, quality product, and are able to leverage such systems to ensure compliance. Similarly, electronics manufacturers and industrial machining operations have found that manufacturing software suites address unique challenges they face around third-party partnerships and managing a high product-mix operation.
The success achieved by firms in these cornerstone industries through manufacturing software deployment continues to spur adoption in new business segments. These newer entrants, while playing catch up to the early adopters, have the advantage now of an explosion of suites to choose from.
Whereas these first industries had relatively limited options in manufacturing software, sometimes forcing them to develop it internally, their success paved the way for an abundance of new entrants extending far beyond those captured on Gartner’s Magic Quadrant, such as Leading2Lean. The variety of solutions, from global to tailor-made, allows companies the opportunity to select a product that uniquely suits their production environment and its inherent challenges.
The Value Proposition
The gains from implementing manufacturing software are as broad as the choices of provider. However, the core value is efficiency, which is ingrained in the process visibility enabled by these systems. Capturing the time and resources required across the stages of production offers manufacturers the insight necessary to optimize order planning and flow through the factory.
Stepping one tier higher in the processes, manufacturing software integrated with other business systems provides a comprehensive picture of the product supply chain. This end-to-end view enables issues to be identified and redressed more quickly with fewer and smaller impacts to customer needs.
The software suites furthermore act as systems of record for support functions including safety, maintenance, and materials coordination activities, from which many groups pull documentation to demonstrate historic compliance to relevant regulatory agencies.
A Caution
There are measurable advantages driving adoption of manufacturing software, as evidenced above, each being enabled through the availability of comprehensive data captured within the system and via links to other business applications.
Yet for all the process information available to a company through its manufacturing suite and partner information sources, the software alone lacks the business acumen needed to dissect the data and focus improvement efforts. The human element is required to interpret and make use of the data to drive action. The true power of any manufacturing software is in providing access to the right information to drive necessary change.
The common thought process is to ensure the right data that people need to drive improvements to their business is captured. Why not simply capture all data?
This ‘big data’ approach is understandable, especially with the increasing ease of gathering data through systems like manufacturing suites, IoT components, and integration methodology. By capturing all information, it is assured that any question that might be asked will have a documented answer. The challenge though, as always in the face of big data, becomes seeing the forest for the trees. In the shadow of seemingly boundless information, this becomes a daunting task.
The Highs and Lows of Big Data
Understanding the difference in actionable data versus ‘big data’ requires first defining big data. Big data is commonly identified through the presence of four qualities, or the Four Vs:
- Volume: the amount of data being generated, which can create challenges in both data storage and analysis.
- Velocity: the speed of the data being generated and the rate at which it is processed, during both collection and analysis.
- Variety: the range of different types of data being generated across numerous sources.
- Veracity: the quality and reliability of the data; only data that is current, of high quality, and which is reliable may be properly analyzed.
With the advent of cloud technology and data storage infrastructure, as well as the ubiquity of technology into daily life, every company and individual now produces data through the course of normal use and interaction with systems. This information is similarly being consumed by every person and business, informing decisions and optimizing performance against systemic flaws.
Yet, for a single firm, there is often a massive disparity between the data it generates versus consumes. Within manufacturing software and its integrated systems and sensors, millions of data points can be rapidly generated. Yet most often, this information is relegated to a data graveyard and remains untouched.
This is because consideration is not duly given at the outset of improvement initiatives as to how the captured data will be used. Lack of definition results in a wide net being cast at the expense of many capital dollars, though many captured points may be considered non-value added.
Starting with Actionable Data
While big data is the inevitability of technological advancement and the means to resolve buried systemic issues, it is an overwhelming place to start from when identifying improvement opportunities. Instead, companies should begin by leveraging their actionable data: the information needed to support frontline personnel in fixing problems on the shop floor in real time.
Starting with actionable data creates a two-fold benefit. First, this information exposes 70-80% of the shop floor problems being faced: the low-hanging fruit. It is simply a matter of putting the information in front of those who can resolve problems in real time. Furthermore, this data can be captured through the base functions of manufacturing software without additional infrastructure and thus, greater cost.
An added benefit of beginning with actionable data is that collecting this information builds a foundation for future big data deployment. Issues exposed through actionable data may require further dissection to pinpoint root cause and drive informed change. In these cases, the actionable data informs a company of precise instances where enabling big data collection would provide a specific ROI through problem resolution. In this way, actionable data becomes the context in which big data is applied.
A Consideration
Although many manufacturing software options offer data capture around machine issues, which anecdotally tend to be the major component of poor performance, it is critical to consider what other root causes exist and ensure that the chosen system can also accommodate data in these areas and processes.
For example, Leading2Lean (L2L), documents actionable data such as machine downtime, on time scheduled maintenance completion, and tool calibration. However, L2L additionally captures data on the other root causes like materials, process performance, quality, and manpower. This ensures that both a more comprehensive set of issues are being unearthed and addressed while engaging a greater swath of the workforce in resolving issues, based on the variety of associated root causes. Improvement is accelerated and the point of strategic integration reached more swiftly.
At the End of the Day, Evolution vs. Revolution
Manufacturing software is a powerful tool in modern industries’ digital transformation tool-belt. Its ability to integrate with other business systems has provided many users with demonstrated efficiency gains by exposing failure modes across business and production processes.
However, with the high cost and unknown return on these ‘big data’ approaches to improvement, companies should approach implementing manufacturing software as an evolution versus a revolution. Businesses should start from where they are, using their suites to capture known data points across all processes to form an initial idea of where problems lie. These lessons can then inform where more information is valuable and investment in big data offers a sure reward.
Learn how manufacturing software can drive operational efficiency for your plant.
Revisions
Original version: 18 July 2024
Written by: Evelyn DuJack
Reviewed by: Daan Assen
Please read our editorial process for more information
Related Posts
Subscribe to Our Blog
We won't spam you, we promise. Only informative stuff about manufacturing, that's all.