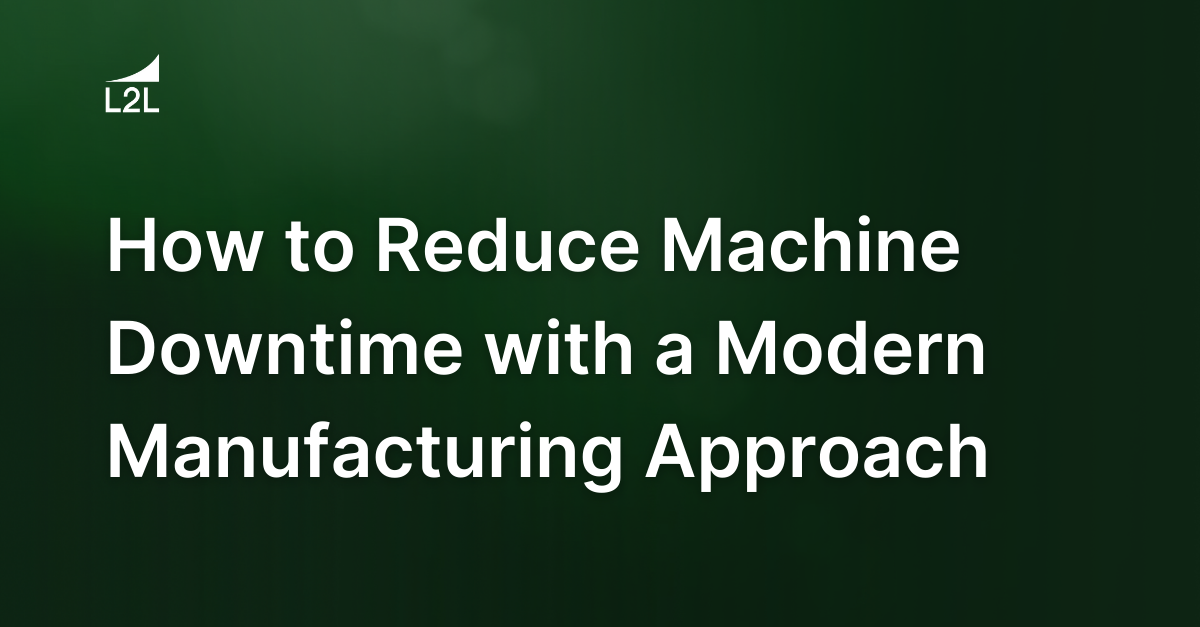
Machine downtime has long been known as the biggest enemy of productivity in manufacturing. When your machines aren’t running, you’re not creating value for your customers. Every minute of idle time can cost you thousands in lost profits.
While some downtime is needed for activities like planned maintenance or changeover processes, most industrial companies experience preventable periods of unplanned downtime.
If your plant is struggling to hit production goals, there’s a high chance your overall equipment effectiveness (OEE) is struggling, too. Let’s take a look at the top reasons manufacturers experience excessive downtime, what to do about it, and how connected workforce platforms like L2L help factories maximize uptime.
What is downtime in manufacturing?
First, let’s define downtime. Machine downtime is a broad term referring to any time that a machine isn’t running. Every time a production process stops, you accumulate machine downtime.
Downtime typically falls into two categories:
-
Planned downtime: This type of downtime occurs during scheduled machine shutdowns. Planned downtime is often assigned when there’s a material shortage, scheduled maintenance, or even teamwide meetings.
-
Unplanned downtime: This type of downtime includes any machine or line stoppages that happen outside of scheduled downtime periods. Unplanned downtime tends to be reactionary, usually resulting from mechanical problems or operator error.
Some downtime is inevitable in manufacturing — including unplanned downtime. However, frequent and prolonged unplanned downtime events are symptoms of systemic problems in a plant. Let’s take a look at some of these in the next section.
Top causes of unplanned downtime
Machines go down unexpectedly for many reasons. Each time this happens, manufacturers lose precious production time and even materials, which negatively affects profits.
Major breakdowns can occur from a number of circumstances. Source.
Here are some of the most common causes of unplanned machine downtime:
-
Break/fix maintenance culture: In environments where the approach is reactive (fixing things only when they break) rather than proactive (regular maintenance to prevent failures), downtime is more frequent and often longer, as issues are only addressed after they've caused a stoppage.
-
Equipment failure: Machinery and equipment can fail due to wear and tear, lack of maintenance, poor operation, or insufficient repairs, leading to sudden stops in production.
-
Supply chain disruptions: Shortages of materials, delays in supply delivery, or issues with the quality of supplies can halt production unexpectedly.
-
Power outages: Unexpected loss of power can stop production instantly and might take a significant amount of time to resume.
-
Software and system malfunctions: Glitches, bugs, or failures in software that controls machinery and production processes can cause unplanned downtime.
-
Human error: Mistakes made by employees, whether due to lack of attention, misunderstanding of instructions, or errors in judgment, can lead to production stoppages.
-
Safety incidents: Accidents or safety incidents can cause immediate shutdowns, either due to the incident itself or during the investigation and response period.
Although some of these causes, such as power outages and material shortages, are often unavoidable, most instances of unplanned downtime are avoidable or quickly amenable. The key to minimizing downtime is uniting your workforce around the right tools and strategies to maximize OEE.
How to calculate machine downtime
To reduce downtime, you need to understand how to calculate it. This requires gathering enough data from equipment, people, systems, and processes to uncover areas requiring improvement.
Most manufacturers use the following steps to calculate machine downtime:
-
Establish planned operating time. This is a set operating period from which you’ll gather data. For example, if production runs for 12 hours a day over 20 days per month, your planned operating period would be 240 hours.
-
Record downtime periods. Document the amount of downtime, planned and unplanned, that occurs over the month. Comparing this report to previous months’ data, if available, may be helpful for tracking trends as well. Modern EAM solutions store production data digitally, making this a simple process.
-
Subtract downtime from planned operating time. The difference tells you your actual operating time. If you log 40 hours of downtime during your 240-hour planned operating period, your actual operating time is 200 hours.
-
Convert the result into a percentage. Using the following formula, your downtime percentage will be roughly 16.7%.
Once you determine your downtime percentage, you can take your downtime calculations further by measuring individual asset downtime. This helps you determine asset criticality and how much revenue you lose when certain assets are down.
Here’s one way to calculate asset criticality and revenue loss:
-
Divide total revenue by planned operating time to get your plant’s daily revenue.
-
Observe how much daily revenue drops when a chosen machine goes down.
-
Compare how different assets affect daily revenue.
Pinpointing your costliest equipment failures helps you prioritize which assets to address first so your factory can stop hemorrhaging precious dollars. However, knowing isn’t enough. You need the right tools and systems to attack the root of the problem.
How connected workforce platforms reduce machine downtime
Connected workforce platforms play a critical role in solving and preventing unnecessary downtime. With advanced capabilities like predictive analytics, real-time machine monitoring, data visualization, and more, this software empowers workers at every level to identify and quickly solve production problems.
Here’s how connected workforce technology helps manufacturers address downtime:
Visibility into machine performance
One of the key benefits of connected workforce platforms is their ability to gather and visualize real-time data. Using equipment sensors and data analytics, you can view current machine and line data and know immediately when a machine is underperforming. Operators can access this critical data, too, from easy-to-use portals that tell them everything they need to know about a machine’s current status and history.
Additionally, this level of visibility makes maintenance scheduling much easier. Rather than waiting for a machine to break down or become a safety hazard, you can dispatch maintenance technicians to fix mechanical issues proactively.
Operator error prevention
Another game-changing benefit of connected worker technology is the ability to digitize and democratize instructional materials. You can store standard operating procedures (SOPs), digital work instructions, safety guidelines, and troubleshooting guides in digital formats and make them accessible to those who need them through a single platform.
When workers have all of the information they need for successful machine operation at their fingertips, they make fewer mistakes and solve problems quickly and independently.
If a mechanical issue is beyond an operator’s scope of knowledge, the operator can easily communicate with experts inside and outside the plant using built-in communication tools.
Equipping maintenance teams
Another benefit of connected workforce platforms is that they keep maintenance teams equipped with the tools and knowledge they need to fix issues quickly and proactively. Not only does this technology give maintenance teams a full view of machine health, but it also helps you ensure your maintenance teams have the right training to perform certain repairs. Moreover, you can easily assign technicians training modules to help them expand their skill sets and achieve new certifications.
Connected workforce platforms can also support inventory management. For instance, many platforms let you track spare parts availability and inventory levels so you can ensure your maintenance technicians always have what they need to make fast repairs.
Using the L2L Platform to avoid manufacturing downtime
If your plant is struggling with excessive machine downtime, the L2L’s Connected Workforce Platform can drive significant improvement in months or even weeks. Our advanced technology was made by manufacturers for manufacturers and has helped hundreds of facilities reduce downtime by double digits.
The L2L Platform empowers your workforce to boost asset reliability and address production disruptions fast with:
-
Real-time alerts and escalation processes: When problems arise, the right people are notified immediately on their desktops, phones, or tablets so you can prevent shutdowns before they happen.
-
Instant access to critical knowledge: When a machine breaks down, operators and technicians can quickly pull up issue-specific information, including required spares, manuals, and machine history.
-
Capture downtime information: L2L lets you quickly document information about each downtime event in detail using video, images, and text.
Simplified maintenance scheduling: Using L2L, you can coordinate maintenance and production schedules using intuitive eKanban tools, helping you maximize throughput and reduce disruptions.
Every minute of downtime costs you big. Get a more in-depth look at how L2L helps manufacturers across industries slash machine downtime and other disruptions by double digits in our FREE eBook: Why Connecting Your Workforce Is Key to Minimizing Downtime.
But if you’re ready to see first-hand how L2L can increase productivity in your plant, simply request a demo today, and one of our sales reps will be in touch!
Revisions
Original version: 23 March 2024
Written by: Evelyn DuJack
Reviewed by: Daan Assen
Please read our editorial process for more information
Subscribe to Our Blog
We won't spam you, we promise. Only informative stuff about manufacturing, that's all.