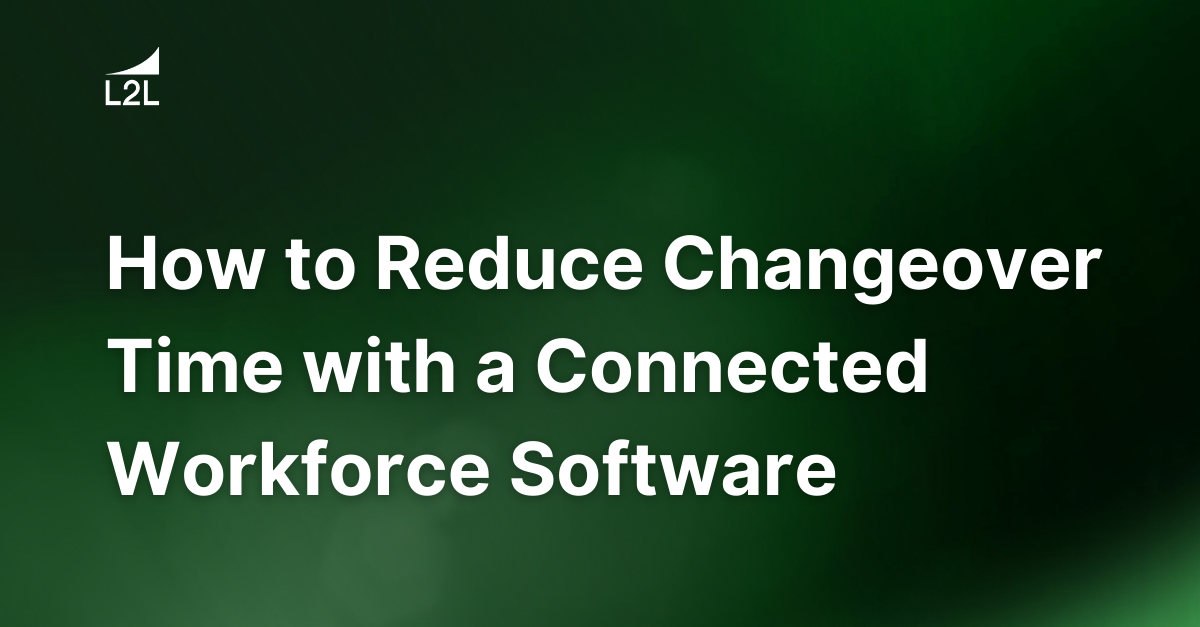
If you’re struggling with inefficiency in your plant, one of the first production activities you should analyze is your changeover process. A changeover — the time it takes to switch from producing one product to another — can take hours, days, or even longer, depending on the items in production. However, most manufacturers don’t realize how much time and effort they could save by optimizing their changeover processes.
In this article, you’ll learn how connected workforce platforms like L2L help manufacturers minimize changeover time and create more value for their customers.
The steps involved in a changeover process
Changeovers are essential processes in every manufacturing facility. However, they require production to stop for a brief period, and they also open the opportunity for error if performed incorrectly.
The typical elements of a manufacturing changeover process. Source.
In most discrete manufacturing facilities, the process of converting a machine or line from producing one product to a new one looks something like this:
-
Step 1 - Clean-up: Before you can prepare a line or machine to produce a new product, you need to clear leftover components, materials, and debris in the way. Thorough clean-up is crucial for preventing scrap and even mechanical problems.
-
Step 2 - Set-up: The set-up period is the time it takes to get lines or machines ready for the new production process. This step is typically the longest, especially if you haven’t optimized your changeover process.
-
Step 3 - Start-up: After you re-start your equipment, you’ll most likely enter the start-up phase — a brief period of minor adjustments and fine-tuning to ensure production runs smoothly.
These steps are commonly known as the “3 Ups.” Depending on the product made in the facility, changeover times can vary significantly. For example, whereas switching out one type of plastic film for another could take 10 to 20 minutes, a changeover in an automotive assembly plant could take multiple days.
Steps to minimize changeover time
Keeping changeovers quick and efficient is crucial for profitably meeting customer demand. To minimize the time it takes to shift from one production run to another, you need to identify inefficiencies in your current changeover processes, develop plans for optimization, and establish standard operating procedures (SOPs) to sustain best practices.
Here’s a quick overview of changeover optimization basics:
1. Analyze your changeover process
Before making any changes, analyze your current changeover processes, focusing on idle time and inefficient tasks. Additionally, take inventory of the materials, mechanical parts, and tools required for each changeover and observe how well workers performing the changeover execute their tasks. Pay particular attention to the time it takes to complete each task during the changeover.
Once your analysis is complete, document your findings in a digital format that’s easily shareable with any team members involved in the changeover optimization process.
2. Cut changeover time where you can
Once you’ve mapped out your current changeover process, it’s time to identify tasks for optimization. If you think a task takes an operator too long, get to the root of the problem.
For instance, manually cleaning a fixed industrial mixer in a beverage facility may take workers twice as long as it should. You may find that sanitizing hard-to-reach areas within the mixer takes extra time, and it may be time to invest in a cleaning-in-place (CIP) system to avoid unnecessary downtime.
One of the most common and effective methods for accelerating changeovers is the Single-Minute-Exchange-of-Dies (SMED) approach. Originating from the Toyota Production System, SMED separates changeover tasks into internal (when the lines are stopped) and external (when the lines are running) activities. The goal of SMED is to maximize the number of changeover activities performed externally — without stopping lines.
Implementing SMED requires a thorough analysis of internal activities that could be performed while machines run. You can then streamline the remaining internal tasks with the help of digital tools. Ideally, the changeover time for most lines should be reduced to 10 minutes.
3. Standardize best practices
After you develop faster, more efficient changeover processes, it’s crucial that you standardize them as soon as possible. Make sure your new changeover SOPs contain clear, detailed steps that include important information like:
-
Required parts and tools
-
Safety procedures
-
Machine settings
-
Cleaning instructions
The best way to ensure that your workforce quickly learns these new protocols is by digitizing them in a centralized platform that everyone can access. Connected workforce platforms are excellent solutions for standardizing work and updating procedures as needed. Not only do they capture real-time data from mechanical processes, but they also make it easy to digitally store process- and machine-specific documents and enable seamless collaboration among frontline workers.
By shortening changeover time as much as possible, you can dramatically improve operational availability, reduce waste, and improve productivity. In the long run, these benefits will also improve your plant’s profitability.
How connected worker platforms minimize changeover time
Using connected workforce technology, manufacturers can keep downtime at a minimum by ensuring that operators can instantly access all information required for a fast changeover.
Think of a connected workforce platform as a single source of truth for changeover operations — a place where relevant SOPs, operator notes, and even video tutorials live. Instead of flipping through binders or chasing down colleagues to clarify or re-explain a changeover step, operators can simply log into the platform and find up-to-date protocols in a few clicks.
Connected workforce platforms can ease the changeover optimization process as well. With current changeover procedures already documented in the system, supervisors can save hours analyzing existing processes and address issues faster. The ability to visualize line data on a single dashboard helps supervisors instantly identify changeover inefficiencies and prioritize lines for optimization.
Think about it this way: Connected worker solutions help shop floor teams function like a seasoned pit crew. When it’s time for a changeover, everyone knows what to do, when to do it, and how long each task should take.
Immediate access to digital work instructions and multimedia training resources ensures that operators have the information they need for a seamless transition from one production run to another.
Minimize changeover time with L2L
When it comes to keeping your changeovers as short as possible, you need to equip your workforce with the tools and information they need to do their best work.
The L2L Connected Workforce Platform is designed to help your operators perform like a well-trained pit crew, putting real-time data and insights at their fingertips. Instant access to digital changeover instructions keeps every operator up-to-date with current processes while minimizing errors and safety hazards.
Detailed production dashboards and SQDC boards ensure that supervisors and plant leaders can analyze production processes at a granular level and quickly identify opportunities for improvement. Additionally, L2L makes it easy to update new changeover procedures, standardize them, and quickly get operators up to speed.
Stop wasting time between production runs. Check out L2L’s Interactive Product Tour to see how our platform can help you transform changeovers — or request a demo for a personalized look at how much time (and money) you could save with L2L.
Revisions
Original version: 18 March 2024
Written by: Evelyn DuJack
Reviewed by: Daan Assen
Please read our editorial process for more information
Subscribe to Our Blog
We won't spam you, we promise. Only informative stuff about manufacturing, that's all.