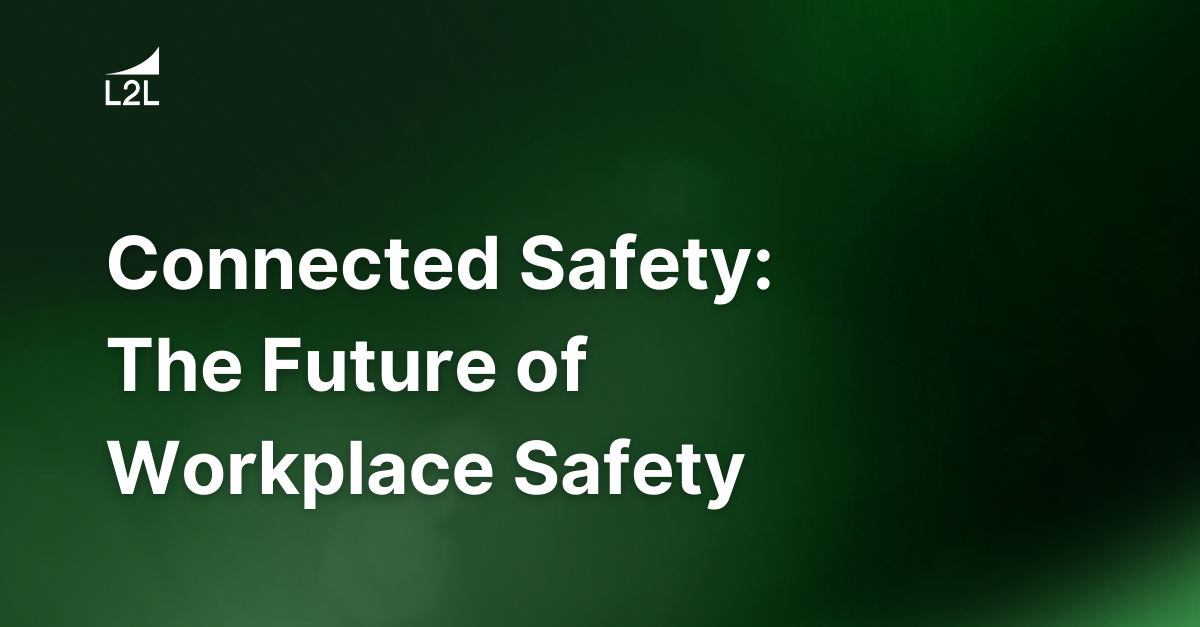
Despite the advancements we’ve seen in manufacturing technology over the past decade, industrial safety is still a major global concern. The manufacturing industry has an exceptionally high workplace safety risk, with thousands of injuries and deaths reported each year.
In 2019, the manufacturing sector accounted for approximately 15% of all private industry non-fatal injuries and 336 deaths in the U.S. for that year. In 2020, U.S. manufacturing deaths rose to 341, with the most common cause of death listed as contact with objects and equipment.
In addition to serious injury and loss of life, safety issues lower workplace morale and create financial burdens for manufacturers over time, making safety initiatives not just crucial for the livelihood of workers, but for business survival as well. To improve workplace safety and morale, industry leaders are making bigger investments in connected safety technology.
In this article, we dive into the concept of connected safety: its meaning, examples of connected workplace safety, key technologies, and how to overcome challenges associated with implementing connected safety solutions.
What is connected safety?
Connected safety in manufacturing refers to integrating digital technologies like the Internet of Things (IoT), wearable devices, and software to monitor and enhance worker safety. This approach proactively prevents accidents, ensures compliance, and improves overall workplace safety through real-time data and connectivity.
Modern safety technologies support a holistic approach to factory safety. Source
Solutions like connected worker platforms play a pivotal role in enhancing manufacturing workplace safety by providing workers with real-time data, alerts, and instant communication tools. This branch of connected manufacturing technology enables immediate response to hazards and fosters safer practices. It bridges the gap between workers and safety systems, leading to a more informed and protected work environment.
Examples of connected workplace safety
So, what does connected workplace safety look like in practice?
The following examples illustrate how connected technology can be used, in varying degrees of complexity, to create safe work environments for manufacturing workers.
Frontline Communications
In a connected manufacturing setting, field workers equipped with mobile devices have instant access to a wealth of information. For instance, a worker on the factory floor can quickly consult digital manuals, safety protocols, or machinery specs on their device. This immediate access to information reduces the risk of errors and enhances decision-making, especially in complex or hazardous tasks.
Moreover, these mobile devices enable seamless communication with team members and supervisors. If a worker encounters an unexpected situation or equipment malfunction, they can instantly share the issue with their team or seek expert guidance. This connectivity not only accelerates problem resolution but also fosters a collaborative safety culture, where workers are continuously supported and informed.
Real-Time Machine Monitoring
Another example of connected safety in a manufacturing facility is the use of IoT and sensors to monitor machine temperatures. If a machine or device becomes overheated, sensors immediately pick up the temperature abnormality and send a safety alert to nearby workers’ connected devices. From here, maintenance teams can quickly shut the machine down before beginning diagnostics and repairs.
In this scenario, the connected infrastructure of the IoT network provides a communication framework for instant safety alerts and swift action.
Fatigue Monitoring Technologies
Connected safety technology includes devices and systems that monitor human workers’ physical states as they perform risky tasks.
For example, a natural gas company may use connected technology to enhance road safety by monitoring truck driver fatigue during long drives. In-cab cameras equipped with facial recognition software can analyze a driver's eye movements and facial expressions, detecting early signs of fatigue. This system works in tandem with telemetry data, which tracks driving patterns like steering stability and braking response, flagging irregularities indicative of tiredness.
Additionally, wearable devices can monitor a driver's vital signs and provide real-time health data. When signs of fatigue are detected, the system alerts both the driver and the fleet management team, prompting necessary interventions like rest breaks. This integrated approach significantly reduces the risk of accidents related to fatigue.
The technology behind connected safety
Connected safety technology falls under three main categories: connected infrastructure, software, and wearables. Let’s break down the most common types of connected technologies modern factories use across each type.
Connected Infrastructure
Connected infrastructure refers to the integration of advanced technologies like IoT sensors, automation systems, and networked equipment and machinery. This setup allows for real-time monitoring and control of manufacturing processes, enhancing efficiency, safety, and predictive maintenance. It forms a smart, interconnected environment where data is continuously exchanged, leading to improved decision-making and operational optimization.
A prime example of connected infrastructure in a plant is predictive maintenance. This approach to maintenance uses sensors to collect real-time machine data to predict failures — and prevent safety hazards — before they happen. This helps manufacturers minimize downtime, reduce costs, and improve plant safety.
Software Solutions
Manufacturing software solutions play a critical role in enhancing plant safety. They foster a more collaborative, informed, and responsive work environment, particularly on the shop floor. Key software solutions include connected workforce platforms, safety apps, predictive analytics, and environmental, health, and safety (EHS) management software.
For example, connected workforce technology and safety apps enable real-time communication and instant access to safety guidelines and operating procedures. This keeps everyone in the plant aware of present and future hazards. Predictive analytics use current and historical data gathered from multiple sources to circumvent potential safety threats. EHS management software helps manufacturers update protocols, track incidents, and ensure regulatory compliance.
Wearables
Wearable technology connects workers to monitoring systems through IoT networks. Using sensors and telemetrics, wearables detect changes in movement, pressure, temperature, and biometric factors. Common wearable technologies include heart rate monitors, smart watches, smart helmets, exoskeletons, and fall detection devices.
Wearables not only alert wearers to potential accidents, but they also share that data with supervisors and nearby personnel in many cases. This helps workers develop safer habits on the job and gives managers a clearer picture of shop floor safety.
New safety technology requires balancing risk and reward
Integrating new connected safety technologies in a manufacturing environment presents unique challenges, notably the risk of what can be termed a “digital safety paradox.” This paradox arises when manufacturers introduce advanced technologies and processes without a plan for helping the workforce adapt to the resulting changes. This scenario can inadvertently introduce new risks, overshadowing the intended safety benefits.
For instance, while new technologies may streamline certain processes, they can also expose workers to unforeseen hazards, especially if the workforce isn’t adequately trained or the technology isn’t properly integrated. Advanced systems often require specialized skills for operation and maintenance, which might not be readily available within the existing workforce.
Moreover, the influx of data from these systems can overwhelm traditional data management protocols, causing lapses in monitoring or delayed responses to safety issues.
Organizations must consider whether the implementation of a particular technology, such as robots for specific tasks, justifies the potential risks involved. For example, using robots might reduce ergonomic stress for multiple employees, but it also introduces the risk of human-machine interaction mishaps.
To adapt to technological changes, manufacturing leaders need to cultivate a culture that emphasizes continuous learning and flexibility. They must also implement a robust framework for risk assessment and mitigation, ensuring that every new technological integration is accompanied by thorough safety evaluations and contingency planning. This proactive approach will help maximize the benefits of connected safety technologies while safeguarding against potential pitfalls.
Transform connected worker safety with L2L
Keeping workers safe on the job should be every manufacturer’s number-one priority. This goes beyond simply meeting OSHA guidelines; you need to actively work toward reducing the number of safety incidents that occur in your facilities each year.
Connected workforce platforms like L2L support shop floor safety by establishing a network of communication and real-time access to data that impact personal safety. A connected plant is a safer plant — and a happier one, too.
Learn how L2L’s connected workforce technology helps manufacturers elevate their safety standards, improves productivity, and enables fast problem-solving in our eBook: Everything You Need to Know About Connected Workers.
Revisions
Original version: 23 January 2024
Written by: Evelyn DuJack
Reviewed by: Daan Assen
Please read our editorial process for more information
Related Posts
Subscribe to Our Blog
We won't spam you, we promise. Only informative stuff about manufacturing, that's all.