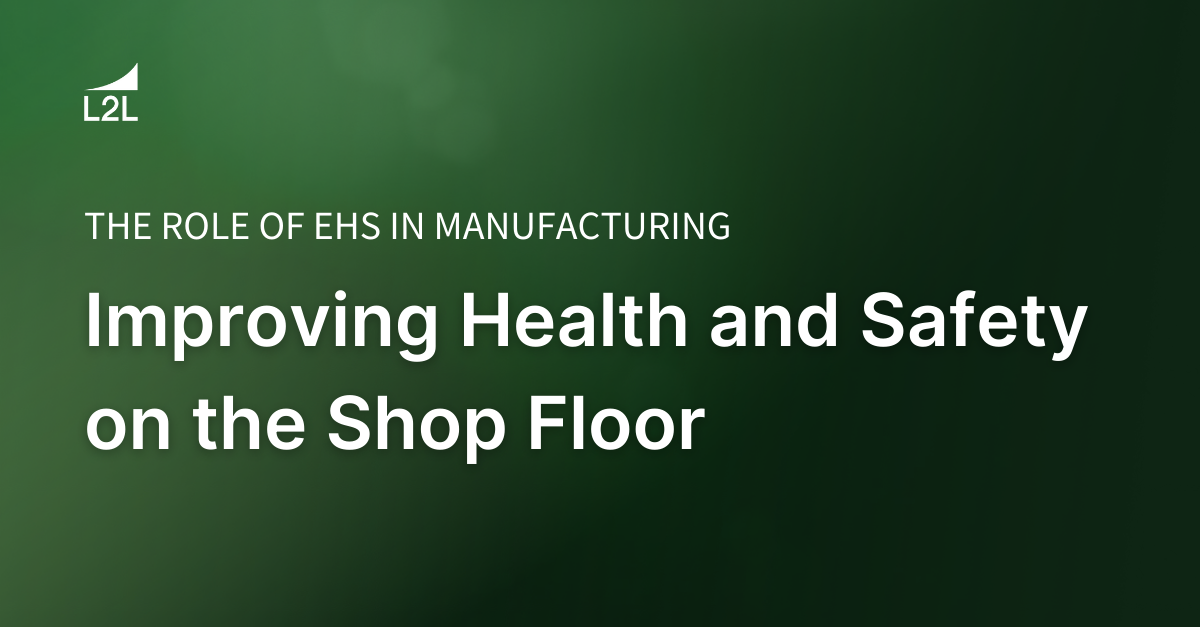
In today's manufacturing landscape, Environment, Health, and Safety (EHS) management is more than a regulatory requirement. It's a foundational component that ensures operational continuity and protects our most valuable asset — our workforce.
At L2L, we believe that EHS is critical not only for compliance but for enhancing overall business performance. Integrating EHS into every facet of operations with modern tools like L2L's Connected Workforce Platform can transform it from a background activity to a dynamic force driving manufacturing excellence.
With that in mind, let’s explore the role of EHS in manufacturing: why it’s so important, why it needs to be proactive, and how modern technology is changing EHS management.
What is EHS in the manufacturing industry?
EHS management has evolved significantly from its early days of basic safety compliance and environmental conservation. It has grown into a sophisticated discipline that blends technology, corporate culture, and proactive risk management to protect workers and the environment while bolstering operational efficiency.
A typical EHS department in a manufacturing plant will be responsible for:
-
Workplace safety: Implementing safety protocols, training programs, and emergency response strategies to safeguard employees from occupational hazards.
-
Compliance with environmental regulations: Adhering to local, national, and international environmental laws and guidelines to minimize the ecological footprint of manufacturing processes.
-
Managing hazardous materials: Ensuring safe handling, storage, and disposal of hazardous substances to prevent accidents and environmental contamination.
-
Health monitoring and promotion: Conducting regular health assessments and promoting wellness initiatives to maintain and improve worker health and well-being.
-
Risk management: Identifying, assessing, and mitigating risks associated with manufacturing activities to prevent accidents and ensure operational continuity.
Today's EHS programs are vital for maintaining productivity and act as an insurance policy against the costs and disruptions of workplace accidents and environmental mishaps.
The origins of EHS
The journey of EHS management began as a response to severe workplace incidents and environmental crises. Events such as the publication of Rachel Carson's Silent Spring and the Bhopal disaster were catalysts in the creation of regulatory bodies like the Environmental Protection Agency (EPA) and the Occupational Safety and Health Administration (OSHA). These historical milestones revealed the need for stringent safety protocols and environmental stewardship, setting the stage for the comprehensive EHS strategies we implement today.
A technology-driven evolution
The advent of the Internet and digital technologies has transformed EHS management from a largely reactive, compliance-driven function into a strategic component integrated across business operations. Modern EHS management tools, powered by web-based systems and real-time data, help manufacturing companies shift from reacting to health and safety incidents to preventing them. This proactive approach is supported by predictive analytics, the Internet of Things (IoT), and mobile technologies, enhancing the ability to monitor and respond to EHS risks in real time.
The benefits of proactively managing health and safety in manufacturing
Many manufacturers don’t realize how wide-spanning these benefits can be. Proactive EHS management leads to:
-
Reduced workplace incidents and downtime: By anticipating potential safety hazards and implementing preventive measures, manufacturers can drastically reduce the incidence of workplace accidents. This protects employees, minimizes operational disruptions, and reduces costly downtimes.
-
Higher morale and productivity: When workers feel safe, they can focus on their tasks without concerns over personal safety, improving their morale and productivity.
-
Compliance and legal protection: Proactive EHS management ensures that manufacturing processes are meeting the evolving standards, thereby safeguarding against legal complications and hefty fines associated with non-compliance.
-
Cost savings: The savings come from reducing the number of accidents, which in turn lowers medical costs, legal fees, and compensation payouts. Additionally, maintaining a strong safety record can reduce insurance premiums over time.
-
Improved reputation and competitive advantage: Companies known for their commitment to health and safety are viewed more favorably by consumers, partners, and potential employees.
-
Sustainability and environmental stewardship: Proactive health and safety practices often align with environmental sustainability efforts. By reducing waste, managing hazardous materials effectively, minimizing emissions, and performing regular environmental audits, manufacturers can further improve their public image and compliance with global sustainability standards.
The L2L Platform: A game-changer for EHS management
L2L’s Connected Workforce Platform represents the next-generation approach to integrating EHS into daily factory floor workflows.
Our solution empowers frontline workers to support EHS initiatives through an integrated and standardized approach that embeds EHS principles and actions into their daily standard work and regular training. This helps manufacturers gain critical mindshare of their workforce to drive program compliance to elevate EHS to a strategic and sustainable program.
Here's how L2L helps manufacturers improve EHS management:
-
Proactive risk management: L2L Dispatch helps identify potential safety and environmental risks before they become incidents. By leveraging real-time data, human interaction, and predictive analytics, manufacturers can anticipate and mitigate risks, significantly reducing the likelihood of accidents and environmental impact.
-
Cross-functional integration: One of the unique aspects of L2L is the seamless integration of EHS with other operational domains such as quality, maintenance, and production. This integration ensures that EHS considerations are not isolated but are a central part of operational planning and decision-making, promoting a culture of safety and responsibility across all levels of the organization.
-
Empowering frontline workers: At the heart of our EHS strategy is the empowerment of frontline workers. L2L provides workers with the tools and information they need to take proactive steps toward their own safety and environmental responsibility. This includes access to training modules, safety protocols, and real-time alerts that help maintain high standards of workplace safety and environmental care.
-
Compliance tracking and reporting: L2L helps automate the collection and analysis of compliance data, making it easier for manufacturers to prepare reports and ensure that they meet all regulatory requirements. This includes automated record-keeping, real-time compliance monitoring, trend analysis, audit support, and customizable reporting tools.
The future of EHS in manufacturing: Strategic, integrated, and technology-driven
As we look to the future, the role of EHS in manufacturing is shifting from a shop floor initiative to a foundational strategic differentiator. With increasing global attention on corporate sustainability and social responsibility, EHS performance is directly tied to a company's reputation and bottom line. The next generation of EHS management will likely push for greater integration with enterprise systems, enhancing EHS’s role in strategic decision-making and business intelligence.
Our vision at L2L is to foster an operational culture where environment, health, and safety management is a cornerstone of excellence. By integrating EHS deeply into shop floor operational processes and leveraging advanced IoT and AI technologies, manufacturers can protect their workforce, minimize environmental impact, and enhance operational efficiency and resilience.
EHS as a pillar of modern manufacturing
Redefining EHS as a core component of modern manufacturing is about more than enhancing safety and environmental performance. It's about ensuring the longevity and success of the manufacturing sector. Using connected workforce solutions like L2L, manufacturers can transform EHS from a cost center into a strategic asset that drives business continuity, operational excellence, and sustainable growth.
Embracing advanced management tools with embedded EHS functionality is imperative not only for protecting workers and the environment but also for future-proofing your business. As we continue to push the boundaries of what is possible in manufacturing, we must also commit to the health, safety, and environmental stewardship that will define the legacy of our industry.
Learn more about how L2L helps manufacturers meet their EHS requirements when you explore our connected safety capabilities.
Revisions
Original version: 7 May 2024
Written by: Tyler Whitaker
Reviewed by: Daan Assen
Please read our editorial process for more information
Related Posts
Subscribe to Our Blog
We won't spam you, we promise. Only informative stuff about manufacturing, that's all.