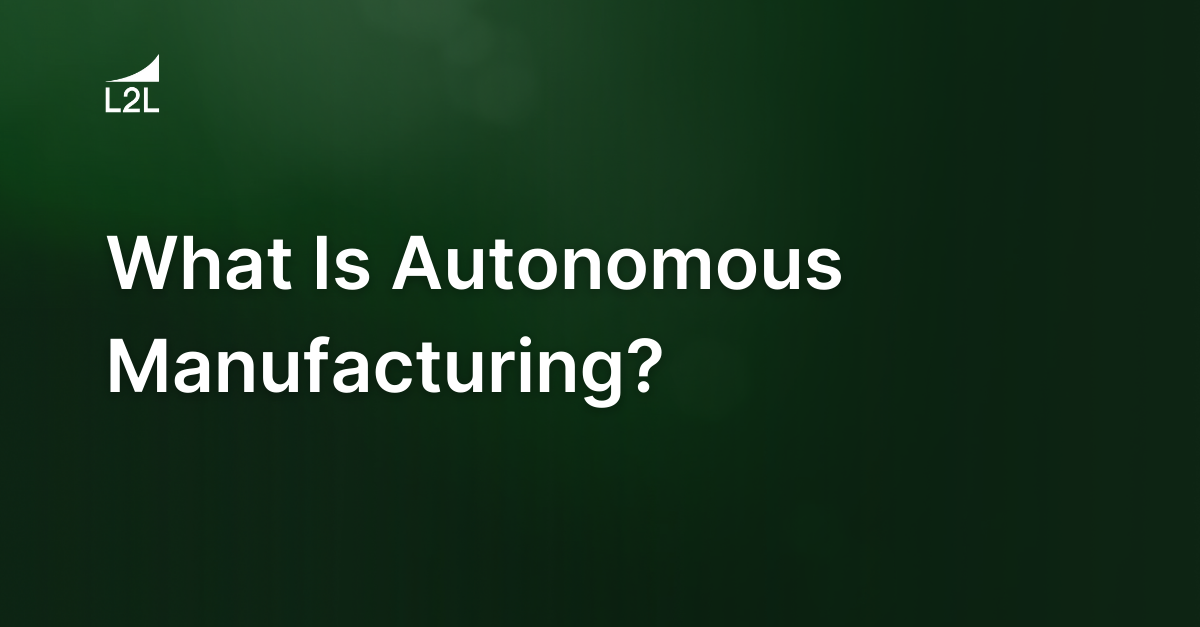
The convergence of key manufacturing trends, such as onshoring, digital transformation, and artificial intelligence (AI), is paving the way toward a new era of autonomous manufacturing. This transformative phase is not merely a futuristic concept but a logical outcome of ongoing shifts in the manufacturing landscape.
At L2L, we’re at the forefront of enabling this transition, providing the tools and insights necessary for manufacturers to thrive in this new environment. In this article, we’ll explore what autonomous manufacturing is, its benefits and challenges, and key technologies involved in running an autonomous facility.
What is autonomous manufacturing?
Autonomous manufacturing, also associated with the terms autonomous factory and autonomous production, refers to an advanced stage of manufacturing where systems and processes are highly integrated and automated, enabling the manufacturing environment to operate with minimal human intervention.
In this software-defined and data-intensive setting, AI-driven machines and robots perform repetitive and labor-intensive tasks, while humans focus on strategy, oversight, and decision-making.
This shift enhances the efficiency, productivity, agility, and adaptability of manufacturing operations, which allows for quicker responses to issues and market changes. However, those benefits come at a cost.
Benefits of autonomous manufacturing
Here are some of the major ways industrial companies can use autonomous manufacturing to their advantage:
-
Increased efficiency and productivity: Machines can operate 24/7 without breaks, significantly increasing production rates. Automation also reduces the time required for tasks like setup and transition between product lines.
-
Improved quality and consistency: Autonomous systems provide consistent products with fewer errors, improving overall quality. Advanced sensors and AI algorithms detect and correct deviations in real time.
-
Cost reduction: Over time, the reduction in labor costs and increased efficiency can lead to significant savings. Decreased waste and optimized resource usage also contribute to lowering operational costs.
-
Enhanced safety: Machines can perform dangerous tasks, reducing workplace accidents and improving safety for human workers. On top of that, automated systems facilitate better handling of hazardous materials.
-
Scalability and flexibility: Autonomous manufacturing makes it easier to scale operations up or down without the constraints of human workforce availability. Quick adaptation to new product lines or changes in production without major disruptions.
-
Better decision making: Integration of IoT devices allows manufacturers to collect vast amounts of data. AI can then analyze that data to make predictions and recommendations for decision-makers.
Challenges with creating an autonomous factory
As with any digital transformation initiative, creating an autonomous factory is a years-long journey that takes careful planning. Challenges are bound to arise, but they can be overcome with the right tools, strategies, and people.
Here are some of the most common challenges associated with autonomous manufacturing:
-
High initial investment: Significant initial costs are involved in purchasing, setting up, and integrating new technologies, with ongoing expenses for technology updates and maintenance.
-
Technical challenges: The complexity of integrating sophisticated software and hardware systems requires continuous updates and maintenance to ensure cohesive, functioning operations.
-
Workforce displacement and skills gap: Automation risks job displacement and a significant skills gap in the existing workforce, necessitating investment in training and education to manage new technologies.
-
Cybersecurity risks: Increased connectivity and data reliance heighten vulnerability to cyber attacks, making the protection of sensitive information and system integrity a major concern.
-
Dependence on technology: While the upside is huge, high reliance on technology for manufacturing operations increases vulnerability to system breakdowns and disruptions, complicating troubleshooting and repairs.
Key technologies in autonomous manufacturing
Autonomous production requires advanced digital technologies to run efficiently and with minimal human intervention. Here are the primary technologies involved in enabling autonomous operations in manufacturing.
Artificial intelligence and machine learning
AI and machine learning play pivotal roles in transforming manufacturing environments into highly efficient and autonomous operations. Here are a few key ways these technologies support automation:
-
By collecting and analyzing vast amounts of data from machines and systems, AI can identify patterns and predict maintenance needs to help facilities reduce downtime and improve productivity.
-
Machine learning algorithms enable the system to adapt and optimize processes in real time so production lines run with minimal worker intervention.
-
AI and machine learning systems detect defects and anomalies that might be missed by human inspectors, improving product quality and reducing waste.
As these technologies continue to advance, they’ll not only get better at boosting operational efficiency but also provide valuable insights that help manufacturers make better decisions, ultimately driving innovation and competitiveness.
Robotics
Modern robots can handle many essential manufacturing tasks, from assembly and welding to packaging and inspection, with unmatched accuracy and speed. Their ability to operate around the clock significantly boosts productivity and enables consistent, high-quality output.
By integrating robotics into production processes, companies can streamline operations, address labor shortages, and profitably meet demand. Robots often come equipped with advanced sensors and AI, enabling them to make real-time decisions and adapt to changing conditions on the plant floor.
Sensors and IoT
The Internet of Things (IoT) is a pillar of autonomous manufacturing, enabling manufacturers to connect machines, systems, and devices using sensors and intelligent technologies. IoT enables real-time monitoring and data collection, facilitating the continuous flow of information across the production floor.
This stream of data provides valuable insights into performance, production efficiency, and potential issues that enable proactive maintenance and continuous improvement.
Moreover, IoT facilitates better decision-making by integrating data from various sources and providing a holistic view of the manufacturing environment. This interconnected network allows for rapid adjustments and improvements, whether it's tweaking machine settings for better performance or reallocating resources to meet changing customer demands.
As a result, manufacturers become more efficient and agile.
Software and control systems
Another technological cornerstone of autonomous manufacturing is advanced shop floor software. Connected workforce platforms like L2L empower frontline workers with immediate access to critical data, in-the-moment guidance, and streamlined communication tools, helping them spot and solve problems quickly.
Control systems like supervisory control and data acquisition (SCADA) systems, distributed control systems (DCS), and programmable logic controllers (PLC) are also critical components of an autonomous factory.
These systems act as the “hands” and “brains” that allow a factory to operate autonomously with minimal human intervention. Together, these control systems create a cohesive, intelligent environment that maximizes productivity and efficiency.
Examples of autonomous operations in manufacturing
Automation is transforming many critical processes within manufacturing — from machine maintenance to defect detection. Let’s take a look at how some of these processes work in an autonomous factory.
Using AI to predict and streamline equipment maintenance needs
An autonomous factory may use AI to predict and streamline equipment maintenance needs, which significantly boosts efficiency and reduces downtime.
Consider a production line that relies on several high-precision CNC machines. Traditionally, maintenance schedules might be based on fixed intervals or when a problem becomes noticeable, leading to either unnecessary maintenance or unexpected breakdowns.
To prevent these issues, AI continuously analyzes data from sensors embedded in the CNC machines, monitoring parameters like vibration, temperature, and spindle speed. By applying machine learning algorithms, the AI system detects subtle patterns and anomalies that indicate potential wear or failure.
When the AI predicts that a particular machine part could fail within the next few weeks, it automatically schedules maintenance during planned downtime, ensuring minimal disruption to production and ultimately extending the equipment’s lifespan.
Automating quality control and assurance processes
Automating quality control and assurance processes can dramatically enhance product consistency and reduce waste.
Picture a factory producing transistors, where each piece must meet strict specifications to ensure reliability and performance. Traditionally, quality control might involve random sampling and manual inspection, which can be time-consuming and prone to human error.
In an autonomous factory, advanced machine vision systems and AI algorithms take over these tasks. High-resolution cameras and sensors are strategically placed along the production line to capture detailed images and measurements of every component as it is being manufactured. AI algorithms analyze this data in real time, comparing each item against predefined quality standards.
If the system detects a defect or deviation, it can instantly flag the item for further inspection or remove it from the production line. Additionally, the AI can provide insights into patterns or recurring issues, helping engineers to quickly identify and address root causes.
The path to an autonomous factory
For most manufacturers, fully automated factories are still a long way from becoming a reality. However, creating an autonomous manufacturing facility is a process that takes considerable time and resources — and it starts with pursuing digital transformation initiatives and embracing artificial intelligence.
Updating every manufacturing asset, from machines to software systems, is crucial for building a foundation for autonomous operations. Of course, this won’t happen overnight. By prioritizing digitalization and understanding what can (and can’t) be automated, you’ll position yourself for a successful automation journey.
Remember to leverage the expertise of trusted technology vendors and leaders in industrial automation during this process. This will not only help you fine-tune your transformation strategy, but it will also better equip you to train your workforce on new technologies when the time comes.
How L2L facilitates autonomous production
L2L’s connected workforce platform helps manufacturers start their journey toward autonomous production by empowering frontline workers with the right data at the right moment.
With capabilities like intelligent shop floor guidance and automated workflows, teams have the tools and information they need to ensure production flows smoothly and with minimal human intervention.
Additionally, can help you automate maintenance activities with predictive maintenance while empowering operators to perform basic asset care. As a result, you can maximize equipment uptime, reduce maintenance-related costs, and free your maintenance teams to focus on priority issues.
Learn more about how L2L helps manufacturers like you set the foundation for autonomous operations when you schedule a demo with our experts. Have specific questions? Reach out to sales@l2l.com today!
Revisions
Original version: 17 June 2024
Written by: Tyler Whitaker
Reviewed by: Daan Assen
Please read our editorial process for more information
Related Posts
Subscribe to Our Blog
We won't spam you, we promise. Only informative stuff about manufacturing, that's all.