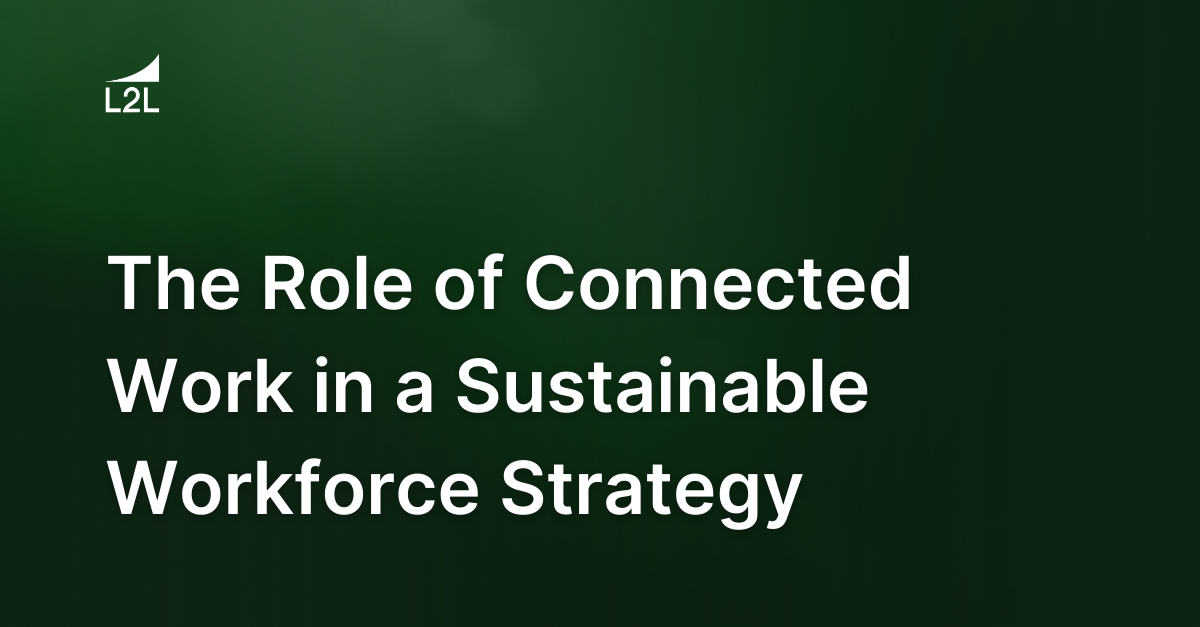
For manufacturers, sustainability is more than a measure of environmental stewardship. Eco-friendly practices, from recycling to CO2 emissions reduction, will remain top-of-mind for businesses, stakeholders, and customers. But another type of sustainability has captured the attention of manufacturing leaders in recent years — and it's changing the future of industrial work.
The Sustainable Workforce: What It Is & Why It's Important
The concept of the sustainable workforce is quickly gaining traction across the global manufacturing industry. Simply put, a sustainable workforce refers to a work environment designed to attract and retain long-term employees by emphasizing well-being, flexibility, and empathetic leadership.
Manufacturers in every industry are desperate to slow the churn of frontline workers, a need underscored by post-pandemic labor challenges and an aging workforce entering retirement. LNS Research reports that 72% of industrial leaders say frontline workforce hiring and retention issues have negatively impacted performance.
But here's the good news: Some manufacturers are turning their own labor crises around. According to LNS Research, top-performing industrial corporations are embracing a new, people-focused approach called The Future of Industrial Work (FOIW). These companies have seen dramatic improvements in not only labor retention but employee morale and overall productivity.
Designed as a sustainable workforce strategy, the FOIW approach can best be defined by three capabilities:
-
Total Employee Experience: A measure of how well an organization treats its workers across the employee lifecycle.
-
Servant Leadership: A leadership philosophy that elevates the needs of employees.
-
Connected Frontline Workforce Applications: The use of digital tools designed to enhance and complement workers' skills and enable them to do their best work.
By combining these capabilities, many manufacturers have been able to "future-proof" their frontline workforces. The diagram below illustrates this concept in greater detail:
In short, embracing a sustainable workforce strategy is critical for combatting the manufacturing labor shortage.
Technology's Role in Executing a Sustainable Workforce Strategy
Creating a work environment conducive to employee longevity begins with adopting a people-first mindset. However, putting this mindset into practice across every level of business requires the right technology, systems, and processes.
The FOIW approach is most effective when integrated with connected workforce technology and other Industry 4.0 initiatives. In fact, LNS Research reports that FOIW leaders deploy connected worker solutions 2.3 times more often than those who have yet to embrace this cultural and technological shift.
Connected worker platforms like L2L enable manufacturing leaders to execute sustainable workforce strategies in various ways. When integrated with existing systems like CMMS, MES, ERP, and QMS, the benefits of these solutions not only help organizations attract skilled labor but keep workers on board for years — not weeks or months.
Human-centric digital technology is crucial for building a sustainable workforce. In this next section, we'll reveal the biggest advantages of leveraging connected worker solutions in your industrial transformation (IX) strategy.
Connected Workforce Technology Applications
As we've discussed, one of the pillars of a sustainable workforce strategy is ensuring that frontline workers have the tools and resources they need to perform tasks safely and effectively. Here's why FOIW leaders are quick to implement connected worker technology across their businesses.
Real-time collaboration
Connected worker solutions enable instant communication and seamless collaboration, even on the factory floor. Workers can use mobile devices to report problems, ask questions, receive updates, and enlist the help of experts outside of the plant when needed. This facilitates better and faster decision-making as well as improved OEE.
Better training programs
Training and onboarding new workers is an expensive and time-consuming process. Connected worker technology enables manufacturers to train new hires using digital tools that make learning faster and more interactive. Managers and supervisors can also track each employee's training progress, skill level, and certifications to ensure the right people are assigned to the right jobs.
Digital knowledge management
Digitizing important knowledge sources such as SOPs, BOMs, safety manuals, and job-specific work instructions and democratizing access to them is a critical function of connected worker technology. Centralized and easily accessible content removes knowledge barriers and provides workers with the right information at the right time, leading to a less frustrating and more action-oriented work environment. Plus, content can be updated in real time.
Flexible scheduling
When workers request time off or need to miss a shift, plants often have a hard time rearranging schedules to fill in the gaps — especially if they're using inflexible scheduling systems. Connected worker technology enables seamless shift scheduling with features like real-time visibility into worker availability and integration with HR software. Plus, aligning maintenance and production schedules is significantly easier, minimizing disruptions to production.
Connected worker solutions are designed to optimize the employee experience — from the shop floor to the control room. They're also becoming a vital component of manufacturing leaders' sustainable workforce strategies.
A Sustainable Workforce Is a Connected Workforce
By demonstrating a commitment to growth, flexibility, collaboration, and innovation, manufacturers can attract and retain the skilled workforce they need to thrive in a competitive market. Although it's only one component of a sustainable workforce strategy, FOIW leaders are starting to recognize connected worker technology as a must-have for long-term manufacturing success.
Download the full report by LNS Research to get the latest data on frontline workforce initiatives, key differentiating factors that set FOIW leaders apart from followers, and practical guidance for creating a sustainable workforce.
Ready to take the first step to future-proofing your frontline? L2L can help. Book a demo with us today to see for yourself how our connected worker technology can transform your plant performance.
Revisions
Original version: 5 September 2023
Written by: Evelyn DuJack
Reviewed by: Daan Assen
Please read our editorial process for more information
Related Posts
Subscribe to Our Blog
We won't spam you, we promise. Only informative stuff about manufacturing, that's all.