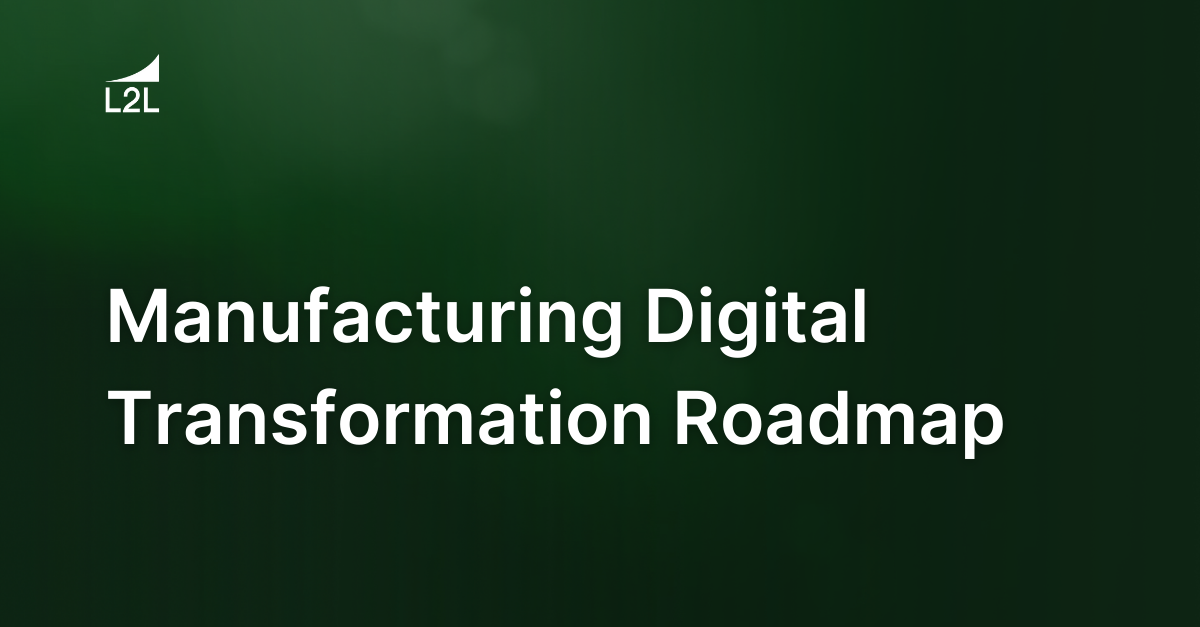
By now, most manufacturers understand that digital transformation is non-negotiable for ensuring economic viability. The question is no longer, “Should we invest in digital transformation?” — but “How fast should we be moving?”
In a 2023 report by Deloitte, 86% of manufacturing executives surveyed stated that they believe smart factory technology will be the number one driver of competitiveness over the next several years. Digital technologies, such as data analytics, the Internet of Things (IoT), augmented and virtual reality (AR/VR), and artificial intelligence (AI) are becoming more common in factory contexts and are only expected to gain popularity among manufacturers.
No matter where your manufacturing business falls on the digital transformation maturity curve, establishing a roadmap for digital transformation is crucial for the smooth integration and adoption of new technologies.
In this article, we lay out the five levels of digital maturity for manufacturers, the essential components of a digital transformation roadmap, and how you can get started on paving the best path forward.
What is the roadmap of digital transformation in manufacturing?
A digital transformation roadmap is a strategic guide that outlines the steps and milestones involved in integrating digital technologies into various aspects of the manufacturing process. It's like a well-thought-out blueprint that helps manufacturers navigate the complex journey toward a more technologically advanced and efficient operation.
Here are several major benefits of having a digital transformation roadmap for your manufacturing business:
-
Strategic alignment: A roadmap ensures that digital initiatives align with your overall business strategy. It keeps everyone on the same page, working toward common goals and objectives.
-
Incremental progress: Breaking down the transformation into manageable phases allows for incremental progress. This helps mitigate risks, reduces disruption, and allows the organization to learn and adapt along the way.
-
Workforce-centric change management: Change is challenging for employees. A roadmap helps manage this transition by providing clarity and fostering a culture of learning and continuous improvement. It includes plans for training and upskilling the workforce to ensure they are equipped to handle new technologies.
-
Resource optimization: By clearly defining the steps involved, a roadmap enables manufacturers to allocate resources more efficiently. This includes both financial resources and human capital, ensuring that investments are strategically distributed.
-
Increased efficiency: The digital transformation roadmap helps you identify and implement digital technologies that enhance operational efficiency, helping you streamline processes and reduce waste.
-
Compliance and risk management: A digital transformation roadmap helps companies account for regulatory requirements and risk factors associated with adopting new technologies. This proactive approach helps manufacturers navigate potential challenges and ensure compliance with industry standards.
A digital transformation roadmap is like a compass that guides you through the evolving landscape of technology integration. It's a proactive and strategic tool that not only ensures the successful adoption of digital technologies but also positions your business for sustained growth, efficiency, and competitiveness.
How “smart” are your factories? Find out with our Smart Manufacturing Scorecard.
The 5 levels of digital maturity for manufacturing organizations
You can assess and segment the digital maturity of your manufacturing operations into multiple stages. Using this framework, you can better understand your current position in the digital transformation journey and what steps to take next.
Here's a general breakdown of these stages:
1. Traditional Stage
Manufacturers that haven’t yet started their digital transformation journey can be recognized by these operational characteristics:
-
Reliance on manual processes and traditional manufacturing methods
-
Minimal use of digital tools, often limited to basic functions like email or basic office software
-
Low levels of data collection and analysis
To advance their operations to the next level of digital maturity, manufacturers in this stage must first lay a foundation for digital transformation to take place. This includes identifying opportunities to boost operational efficiency, reduce costs, and improve product quality with digital technology. By pinpointing processes that can be digitally upgraded, you can pave the way for targeted improvements.
Additionally, building workforce awareness about digital transformation cultivates a culture receptive to change. Make sure your workforce understands how technologies like automation and data analytics can boost productivity and make their tasks easier.
2. Emergent Stage
Manufacturing organizations in the emergent stage are beginning to adopt digital technologies for specific tasks, such as digital inventory management and basic automation functions. They typically employ some level of data collection but with limited integration and analysis capabilities. They may even incorporate cloud technologies and the Internet of Things (IoT) into some processes.
If you’re in the emergent stage, you should focus on developing a more structured approach to digital technology adoption while aligning digital strategies with overall business goals. This mitigates disruption during the transformation period and ensures that technological advancements directly contribute to overarching objectives.
3. Connected Stage
Once manufacturers reach the connected stage of digital maturity, they exhibit the following technological attributes within their facilities:
-
Greater integration of digital technologies across operations
-
More sophisticated and widespread use of data analytics for decision-making
-
More notable improvements in efficiency and productivity due to digital adoption
As they continue to mature, organizations in this stage should focus on enhancing connectivity between their digital systems. IoT systems, for example, can be optimized to ensure a seamless flow of data among different devices within their networks. At the same time, it’s important to use factory data insights to inform decisions and strategies as you progress through your digital transformation journey.
4. Integrated Stage
The integrated stage of digital maturation marks the point where organizations have digitized most of their operations. Manufacturers at this stage have become advanced in their use of technologies like AI, smart robotics, and IoT networks, which enable high levels of automation and connectivity across their organizations. Moreover, they use robust data analytics capabilities to drive operational decisions.
However, manufacturers in this stage can still improve their operations by working toward seamless integration of digital systems. Additionally, leveraging advanced AI capabilities like machine learning (ML) enhances data analytics processes, enabling predictive insights that fuel continuous improvement.
5. Digital-First Stage
If you’re a digital-first company, technology is at the heart of your business. You implement new digital solutions in anticipation of change — not a reaction to it.
At the final stage of digital maturity, manufacturers are invested in continuous innovation and improvement. This is driven by advanced analytics, along with AI and ML capabilities baked into every applicable process. Companies at this stage also exhibit a strong digital culture, investing in new technologies and equipping their workforce with new skills.
Digital-first manufacturers need to continue expanding their digital capabilities (e.g., predictive modeling, digital twin technology) and sustain a culture of continuous improvement and technological adaptation. This way, digitally mature companies can lead their industries in innovation that maximizes productivity, efficiency, and customer satisfaction.
Each stage of this maturity scale reflects a progressively more sophisticated and integrated use of digital technologies. Businesses need to recognize that digital maturity progression isn’t a linear process. Different parts of a business may be at different stages of digital maturity.
Additionally, transitioning from one stage to another will require strategic planning, investment, and often a cultural shift within the organization.
Steps for creating a manufacturing digital transformation roadmap
Digital transformation looks different for every organization. However, all successful digitalization journeys are due in large part to carefully designed roadmaps.
Here’s what a typical digital transformation roadmap could look like for a mid-sized manufacturing business:
1. Perform an assessment of the current state
Begin your digital transformation strategy by auditing your existing manufacturing processes, systems, and technologies. Evaluate the current level of digital maturity and technological capabilities across your business and determine which processes are ready for digitalization. Then, Identify pain points, inefficiencies, and areas for improvement and gather input from stakeholders across various departments.
2. Define your vision and objectives for digital transformation
Articulate a clear vision for what your business’s digital transformation should achieve and set SMART objectives: specific, measurable, achievable, relevant, and time-bound. Share your vision and goals with the rest of your organization and ask stakeholders for input. This will help you ensure that your digital transformation goals align with your overall business strategy and objectives.
3. Identify key digital technologies and solutions
Evaluate relevant digital technologies, such as IoT, AI, cloud computing, big data analytics, and robotics, that you can implement to improve productivity, efficiency, and cost savings in your organization. Assess the feasibility and potential impact of each technology on your manufacturing operations. It’s important to prioritize technologies based on their alignment with defined objectives and overall business strategy.
4. Develop a strategic implementation plan
Develop an implementation plan by first creating a phased approach for technology implementation that considers resource availability and risk management. Determine key milestones, deliverables, and timelines for each phase with guidance from stakeholders, IT teams, and even external experts. Then, assign responsibilities and establish cross-functional implementation teams.
5. Plan skill development and workforce training
Creating a plan for training and upskilling your workforce is crucial for ensuring smooth technology adoption. First, identify skill gaps in the current workforce related to new technologies. Then, address these gaps by developing training programs for upskilling employees. Plan for hiring or partnering with external resources if necessary.
6. Determine data management and infrastructure readiness
It’s imperative to evaluate existing data management capabilities and identify infrastructure requirements. This involves planning for scalable IT solutions and implementing robust data security measures to safeguard critical information. Additionally, ensure your new technology’s compliance with relevant data privacy and protection regulations to establish a foundation of trust and accountability.
7. Start pilot projects
After you map out your digital transformation strategy in detail, it’s time to implement pilot projects for selected technologies in controlled environments. During this phase, you can monitor performance and gather feedback to refine solutions. Use learnings from pilot projects to inform broader roll-out strategies. If the appropriate technology is accessible, using a digital twin for prototyping and testing can save you time and money during this phase.
8. Continue with full-scale implementation and integration
Once testing is finished, you can begin to roll out successful pilot projects across the manufacturing operation. It’s best to introduce these pilot projects incrementally so that your workforce can adapt without disruption. Ensure your new digital solutions integrate with existing systems and processes for seamless operation. Remember to foster continuous communication and collaboration among stakeholders.
9. Monitor and evaluate your progress
Digital transformation is an ongoing process that extends far beyond your initial roadmap. When your integration and implementation phase is complete, establish key performance indicators (KPIs) to measure success and impact.
Regularly review your organization’s progress against objectives and KPIs, and refine your roadmap based on feedback, new technologies, and evolving business needs. Periodically review and update the roadmap to reflect changes in technology trends, market demands, and business priorities.
Digital transformation is an imperative for today’s manufacturers, regardless of industry. By developing a comprehensive digitalization roadmap, you’ll significantly increase your chances of success at every stage of the organizational journey.
Start your transformation journey with L2L
Digital transformation begins and ends with your workforce. Connected workforce platforms like L2L help manufacturers unite people and technology on the shop floor for more productive, efficient, and harmonious operations.
With L2L’s connected workforce technology, you can:
-
Empower your workers with the right data at the right time
-
Solve problems proactively with real-time insights and AI guidance
-
Visualize data across your entire plant
-
See who’s winning or losing on the shop floor
-
Track your workforce’s training progress and skill levels
-
Prevent unplanned downtime
…And much more. Discover how our platform can help you fast-track your digital transformation when you take our Virtual Product Tour.
Want to know how fast you can see ROI from L2L? Find out now with our ROI Calculator!
Revisions
Original version: 28 December 2023
Written by: Evelyn DuJack
Reviewed by: Daan Assen
Please read our editorial process for more information
Related Posts
Subscribe to Our Blog
We won't spam you, we promise. Only informative stuff about manufacturing, that's all.