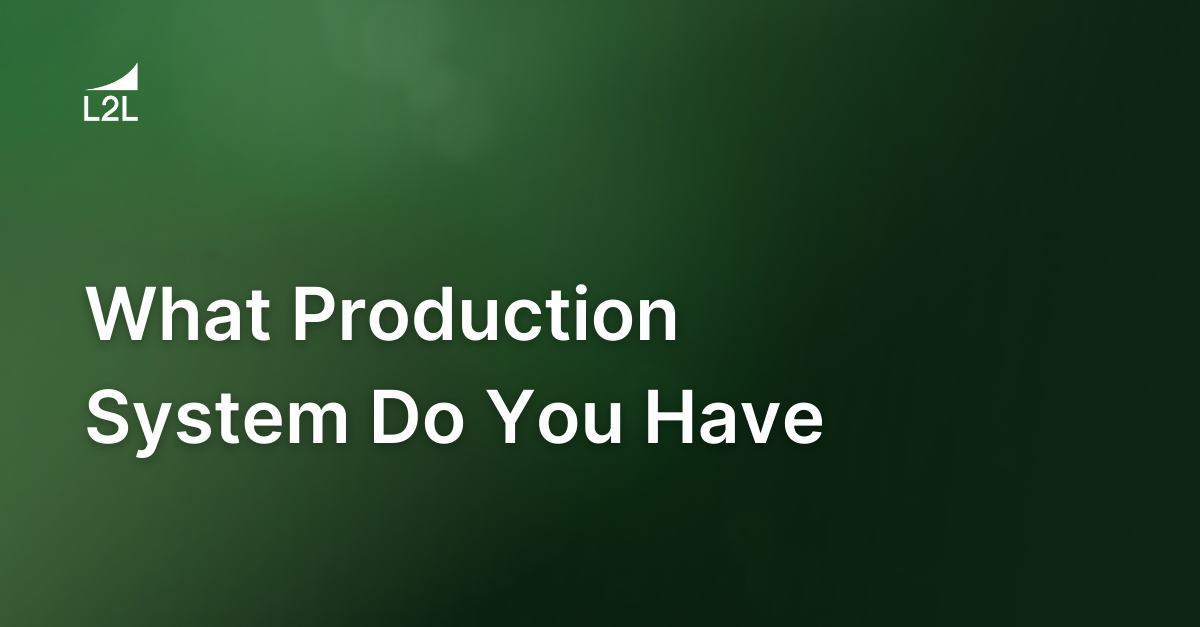
What is a Production System
Production is one of those ubiquitous, generic terms that so often seems to creep into conversations about business and economics as a more formal way to say “making things”. Yet as anyone experienced in one or more manufacturing industries can attest to, production is heavily nuanced: by industry, by company, by plant, and even by product line. Managing these manufacturing processes, from raw materials through finished product, is therefore an incredibly intricate, time-consuming, and more-oft-than not frustrating task, just like in an experiment to create predictable results in a complex system.
Modern manufacturers are fortunate to live in the age of digital transformation, where options for Production System tools are multiplying at an impressive rate. These solutions, such as Leading2Lean (L2L), offer a means to model and manage the manufacturing process from tip to tail in a single platform through inter-connectivity with other business management tools and live data feeds from the shop floor. With such an evident business case, the biggest challenge manufacturers face is deciding which manufacturing execution system best suits their production.
The Breakdown: What Underlies a Production System
A Production System is simply any of the industry methods of creating goods and services from base resources such as:
- Manpower
- Methods
- Machines
- Money
- Materials
While Production Systems are frequently considered from the perspective of physical inputs and outputs, each is comprised of two flows: materials and information.
Materials Flow
Materials flow is the physical act of converting raw components into intermediate product, or work in process, and then into finished goods. The system’s ability to meet demand is governed by its capacity, or rate at which inputs are transformed into outputs, as well as its quality, which is how well and how often outputs meet objective standards for particular properties.
Information Flow
The information process flow encompasses the “invisible” aspects of the Production System: the capture, transmittal, and leveraging of data to plan and manage materials processing. While historically the information flow may have been more tactile and interactive through the use of paper forms, the accelerating application of digital systems, like L2L, has allowed drastic increases in both data accessibility as well as information capture.
Variations on a Theme
Aside from breaking Production Systems down into elements of flow, these methods of manufacturing can also be classified based on the approach taken to converting resources to finished goods and services. There are typically three cited types of systems, broken down along perpendicular axes of product variety (x axis) and production volume (y axis):
- Continuous production
- Job-shop or project production
- Batch production
Continuous Production
Continuous production environments are designed to reflect the sequence of operations needed to convert raw materials to finished goods. Product flows through these operations are as single pieces, worked on in an assembly line system: at any particular time, only one unit per station is having value added to it. This production system is used in manufacturing conditions of low product variation and high volume of product demand. On the shop floor, continuous production employs specialized equipment and manufacturing methods targeted to the exact product detail needed to leverage economies of scale. Tasks performed by workers are often broken into small segments that are easily mastered.
Job Shop Production
Job shop production occurs in the inverse conditions of continuous production: product differentiation is extreme and volume is minimal. These conditions are most often met in the case of customized production, where the particular operations and departments each until must pass through is distinct to the precise characteristics required of that unit of product. Departments are comprised of generic equipment that can be modified for each job and used by highly trained and skilled workers to create the exact qualities required in each unit.
Batch Production
Batch production is the third class of Production System. Unlike the other systems, batch production is applied to situations where product variation and product volume are roughly balanced. Batches, or groups of product units of the same type clustered as a single routing, move through the various functions or process steps such that the total volume is output simultaneously at the end of production. This manufacturing approach utilizes generic equipment and processes that are adapted or applied at each phase of production to produce the specific characteristics sought in each batch. Based on product diversity, training for front-line personnel may be broken down both by work cell and different traits that may be applied to the product within the cell.
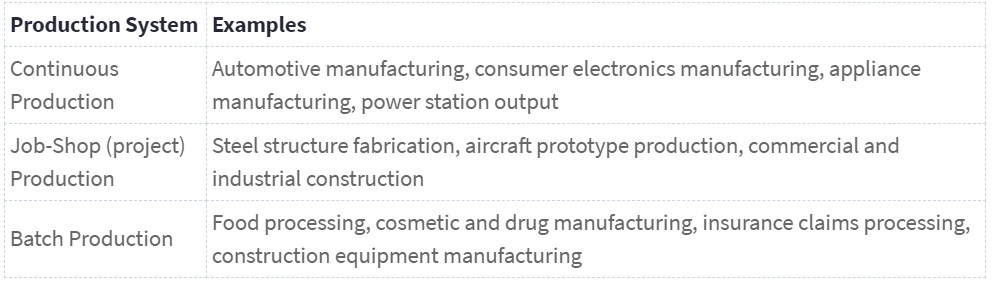
Mass or Flow Production
A fourth type of Production System may occasionally be defined, called mass or flow production. From the definitions above, flow production falls within the continuous Production System type; however, the two may called out distinctly to segregate systems with an added degree of specificity. When used, mass production traditionally refers to an assembly line situation in which both machines and a workforce are applied in tandem to create a product. Continuous production, alternately, relies primarily on machine resources with minimal human resources, and production occurs all hours of all days of the year. An example of this purified definition of continuous production is fermentation.
The Book vs. The Plant
While the strict operations management definitions of Production System may imply that each plant can be neatly slotted into one of the three types of systems, this is often far from reality. Many plants may contain a mixture of these production systems, particularly for comprehensive operations that include sub-assembly and final assembly manufacturing as well as internalized development groups.
For example, a single plant could produce fittings used for several of its canister types. These fittings may be produced on one line which continually runs that same fitting every day, making it continuous production. The canisters to which the fittings are applied have several configurations and are produced in groups of 200 units, in batch production. Additionally, there is a “large” canister production line that does custom construction for industrial applications as single, built-to-spec units; this would be project or job-shop production.
Can the Software match Real Life?
A manufacturing execution system (MES) is a powerful tool for businesses; capturing real time production data including throughput, stoppages, staffing, and rejects to calculate a host of descriptive metrics to identify performance gaps and promote process improvements. However, as plants add complexity with each production system present and their requisite data needs, finding an MES that can represent them all may seem a like a tall order.
Continuous production may only need a simple indication of units processed per time and defect numbers, given the constancy of its production. Batch production requires another level of detail, capturing both the output produced and resources input plus associating them to a specific lot of a particular product. Job-shop production can go even further, adding to all preceding needs the ability to track production and be connected across multiple processes and phases of manufacturing.
Fortunately, among the profusion of manufacturing execution systems available, Leading2Lean's LES (Lean Execution System) offers all the capability a plant needs to capture and manage its data across all types of Production Systems in a single, intuitive software. Line and cell level dashboards allow quick capture and visualization of the resources input to produce output and scrap quantities, along with demand values as a baseline and flow interrupters. Easy integration with current PLC and wireless device technology also enables this data to be directly input into the MES platform, which will then calculate and display the production metrics to show success and opportunities.
Every manufacturing plant’s production is unique to that facility and its parent industry, and becomes considerably more nuanced when accounting for the present Production System. Despite these potentially compounding complexities, modern manufacturing platforms are rising to the challenge to simplify data for all forms of Production Systems to focus on managing and improving their processes.
If you like this blog, check out another one on Production planning during erratic customer demand.
Revisions
Original version: 18 July 2024
Written by: Evelyn DuJack
Reviewed by: Daan Assen
Please read our editorial process for more information
Related Posts
Subscribe to Our Blog
We won't spam you, we promise. Only informative stuff about manufacturing, that's all.