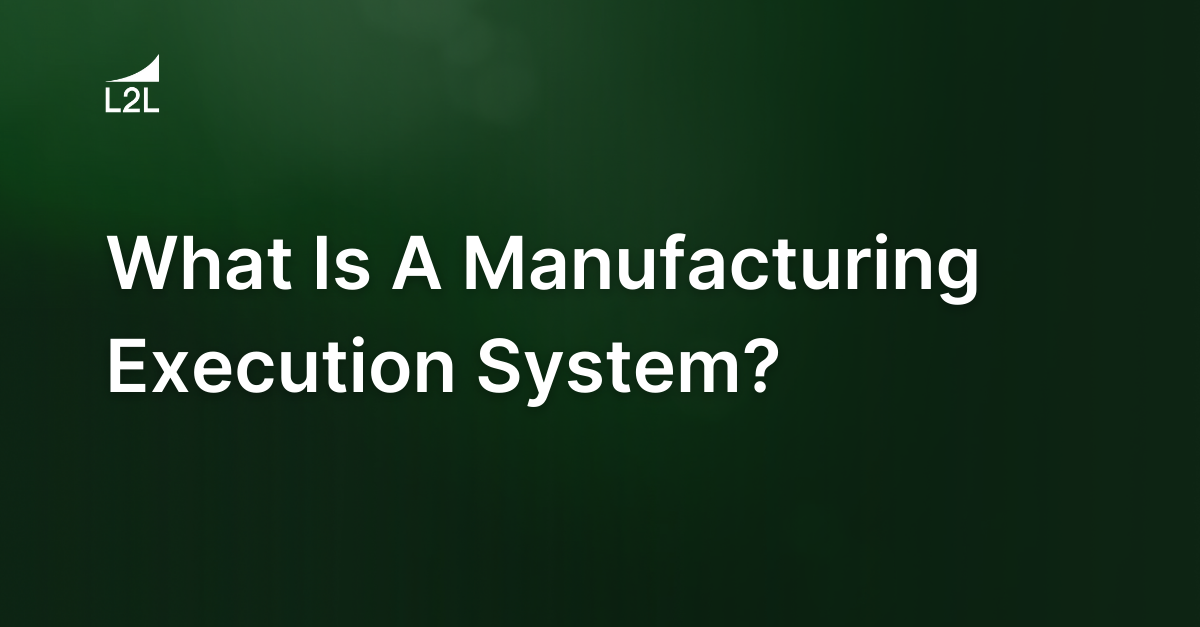
Would it surprise you to learn that when you perform an online search of MES, the second item returned is an advertisement for PPE (Personal Protection Equipment)? More specifically, firefighting equipment? You may chuckle or grimace, but if you live and breathe manufacturing, I'll bet you're not surprised, and I'll bet you can appreciate the irony.
Overview of a Manufacturing Execution System
The most widely accepted definition of the acronym MES is Manufacturing Execution System(s). In case you have not yet been issued your secret Decoder Ring for Manufacturing acronyms, I'll break it down for you.
Definition of Manufacturing Execution System
MES is a computerized system used in manufacturing to track, control, and document manufacturing processes from raw materials to finished goods.
Tracking and documenting these processes provides data intended to help improve operations on the plant floor by smoothing and defining the workflow.
In the quest for operational improvement, manufacturing execution system software collects data to be analyzed and shared across disciplines.
Evolution & History of MES
How did manufacturing begin to adopt MES? In the early '70s, manufacturing entities began to computerize their accounting functions. They soon realized that this technology translated easily to inventory control as well.
In the latter part of the 1970s and early 1980s, the applications which are referred to as Manufacturing Resource Planning/Material Resource Planning (MRP systems) came into existence. These systems were capable of providing three major features:
- Material Planning
- Material Control
- Production Definition
These applications were widely adopted and still continue to exist in many companies. The reason for their popularity can be attributed to the fact that these applications improved material/resource management and positively impacted the bottom line for those who employed them.
What Is a Manufacturing Execution System Integrated With?
There are many different kinds of software and systems that integrate with a manufacturing execution system. Some are comparable but not synonymous with MES. These include:
- Computerized Maintenance Management System (CMMS)
- Enterprise Resource Planning (ERP)
- Manufacturing Operations Management (MOM)
- Manufacturing Resource Planning/Material Resource Planning MRP
- Enterprise Asset Management (EAM)
- Statistical Process Control (SPC)
What Is A Manufacturing Execution System For?
What's in a name? In this case, a lot. A manufacturing execution system is intended to do just that: Help improve the ability of manufacturing to execute to their plan.
To better understand what an MES is for, let's look at the basic functionality of MES on the modern manufacturing plant floor.
Production Dispatching: MES can be used in conjunction with production planning, product scheduling, and delivery and logistics planning.
Quality Management: MES can play a role in quality management processes and procedures, particularly through process documentation. This can be helpful in demonstrating required compliance.
Maintenance Management: MES can play a significant role in maintenance management. However, it is much better suited as an add-on because MES is not maintenance-specific. Integration with a more robust and comprehensive solution will check more boxes off your list.
Resource Allocation & Management: MES can touch on these needs. Depending on the resource you are trying to manage (human, machine, or material) you will find MES to be an excellent first step in the right direction.
Labor Management: MES can be a component of labor management to track who worked where and on what from when to when.
What A Manufacturing Execution System Should Provide, But Often Doesn't
There are some clear signs that indicate whether or not you are in need of more than a traditional MES. These include a lack of data (visibility), data that's too late, failure to meet production schedules, and an inability to trace materials. Let's take a deeper dive into each of these points below.
Lack of visibility
You know you have issues that need to be addressed in your plant. If you're trying to manage them using gut instinct, it's time to consider a manufacturing execution system. Hunches work great when you're the special agent in charge of a hit television show. But not so great when you're the one who is responsible for improvements. Anecdotal evidence and folklore won't get your accounting folks to loosen the purse strings.
You need data: good data. You need to clearly make problems visible. You need to show where you've been and where you're going. Your "spidey" senses won't get that done.
I cannot stress this strongly enough. Data is everything. Period. For manufacturing people, Data is the Bible.
Data too late to be useful
You've got tons of data. It might even be data that's really pretty darn good. Your shop floor folks have been scribbling their fingers to the bone making tick marks to put on a spreadsheet. Unfortunately, you spent all of the past weekend compiling and computing last week's data. If only you'd been able to finish it sooner and could have made adjustments for this week.
If you don't have accurate, real-time data, whatever "solution" you're using isn't doing you any favors. It might be time to consider that MES.
Not meeting production schedules or throughput
Your associates have worked overtime and every weekend for as long as anyone can remember. Your purchasing folks have met every one of their suppliers for lunch. You even saw one of them stay half an hour late one day. Your maintenance department is so swamped they can't even make it out to your line.
So how come you're not meeting the production numbers? Why are your shipments late? How many times is your customer going to tolerate being shut down because you've run them out of product? How many premium shipping invoices have you paid lately?
If only you had a way to provide good data, on time, every time.
Inability to trace materials
You've just been alerted to a quality concern. Where is that darn spreadsheet? Were your components bad? Did something go wrong in the manufacturing process?
How do you start to identify what went wrong and where? When did it happen? How long has this been going on?
If your crystal manufacturing ball of goodness is on the fritz, who are you going to call? That's right. MES, Buster.
When an abnormality occurs, you must be able to identify what went wrong with certainty. Where it happened. The extent of the potential damage and loss. While your MES will help, it will have a difficult time pulling this load on its own. "
Benefits and Limitations of a Manufacturing Execution System
Any manufacturing execution system can be a valuable tool. A system that lends structure to chaos can help drive improvement by giving a measure of before and after.
Here are some potential benefits of MES:
-
Reduced downtime by exposing inefficiencies
-
Cost reduction by identifying and eliminating waste
-
Operator empowerment when your associates can point out areas of improvement and you can take action
-
Drive efficiencies by demonstrating progress
-
Smooth integration of new personnel and processes
-
Standardize operations thanks to documenting and communicating procedures
It's important to note that any manufacturing execution system is certainly better than no MES. However understanding MES's limitations is also important.
Limitations of MES include:
-
MES software can be very difficult to use
-
If you're lucky, you have a couple of experts who can worry about it. Just worry, though. That's a full-time job. Think too many tasters and not enough cooks
-
Your shop floor folks don't have the time to spend hours (if not days) being trained by your IT folks who aren't likely to come to the plant floor
-
Most MES software doesn't provide REAL-TIME visibility
-
You're trying to connect your factory. Most traditional MES are not compatible with IoT (Internet of Things — think digital transformation)
-
You want to connect your people and processes. MES can lead to more silo-building between departments, isolating important data from those who could use it
So, where does that leave you? Obviously, MES plays a role in driving improvement on the plant floor, but it's not a complete solution.
If you've taken the steps to put MES in place, pat yourself on the back.
If you've taken the next step to update and integrate your MES, good for you!
If you know that you need more real-time visibility to production and a way to better engage your people in driving operational improvements, but it has to be easy to use, train, and implement, congratulations! You've come to the right place.
Request a demo today! We'd love to show you how to get more out of your MES.
Revisions
Original version: 9 August 2019
Written by: Cara Winther
Reviewed by: Daan Assen
Please read our editorial process for more information
Related Posts
Subscribe to Our Blog
We won't spam you, we promise. Only informative stuff about manufacturing, that's all.