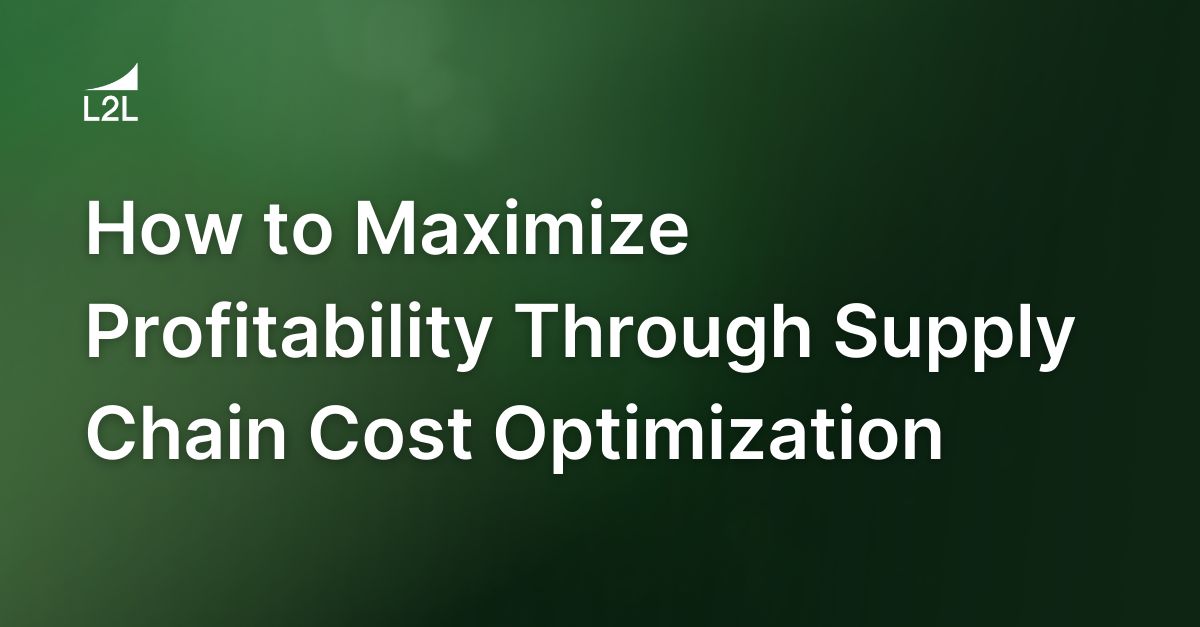
Supply chain costs account for a massive proportion of manufacturing expenses. In fact, supply chain logistics alone can account for up to 50% of the final product cost. To keep this number as low as possible, manufacturers are always looking for ways to cut expenses without sacrificing product quality or supply chain resilience.
In this article, we’ll cover the key components of supply chain cost optimization along with strategies for saving money across the supply chain.
What is cost optimization in the supply chain?
In simple terms, supply chain cost optimization is all about effectively managing supply chain costs. This requires balancing cost-cutting with quality and resilience (i.e., maintaining a reliable flow of goods) for the best possible return on investment (ROI).
Supply chain costs are typically divided into three major categories:
Direct costs are those directly tied to the production of a specific good. They include:
-
Raw materials: Often known as primary commodities; the basic materials used to produce specific goods.
-
Labor: The human activity involved in producing goods.
-
Transportation: The movement of goods from one place (or stage of the supply chain) to another.
Indirect costs refer to operational expenses or any costs not directly tied to revenue generation. The biggest ones are:
-
Storage and warehousing: The storing, safekeeping, and handling of goods before they’re shipped to customers.
-
Administrative expenses: Any expenses associated with supply chain management, administrative office maintenance, and systems supporting administrative functions.
-
Facility costs: Costs associated with maintaining physical facilities used throughout the supply chain, such as factories and warehouses.
Hidden costs are those that aren’t reflected on a balance sheet. Simply put, they’re expenses that arise when companies use internal resources without reimbursement. These include:
-
Inventory carrying costs: The costs incurred from handling, storing, and moving inventory.
-
Opportunity costs: The costs associated with lost revenue generation opportunities when one alternative is chosen over others.
-
“Hidden factories”: Unaccounted-for activities that lead to inefficiencies and waste during the manufacturing production process.
From material price fluctuations to supply chain disruptions, countless situations factor into the total cost of manufacturing goods. However, there are many tools and strategies organizations can use to maximize profitability through effective supply chain cost management.
Strategies for reducing direct supply chain costs
Optimizing direct supply chain costs like labor, materials, and transportation is essential to protect margins and improve overall operational efficiency. Through strategic supply chain cost management, you can reduce waste, improve resource allocation, and respond more effectively to market fluctuations.
Here are a few ways to reduce direct supply chain expenses.
Negotiating with suppliers
Negotiating with suppliers allows you to secure better pricing, terms, and conditions. For instance, leveraging volume discounts and committing to long-term contracts often leads to lower rates on bulk purchases and better payment terms. These agreements help reduce material costs, lower transportation expenses, and improve cash flow.
In addition to direct cost savings, supplier negotiations can also foster collaboration on process improvements. By working closely with suppliers, you can identify opportunities to optimize production schedules, improve product quality, streamline logistics, and much more.
Improving the efficiency of transportation
Typically, transportation and logistics are areas ripe with cost-cutting opportunities. For example, adopting multi-modal transportation — using a combination of air, sea, rail, and road — can lower costs by selecting the most economical or efficient mode for each leg of the journey. This flexibility helps reduce transit times, optimize fuel usage, and better manage unexpected disruptions.
Moreover, analyzing transportation routes and delivery schedules for the most efficient paths can minimize fuel consumption, lower labor costs, and speed up delivery times. This not only reduces operational expenses but also improves supply chain reliability, helping your business meet customer demands more effectively.
Leveraging automation and technology
Incorporating advanced technologies and automation solutions into your supply chain management strategy can reduce costs by streamlining operations and minimizing human error. For example, artificial intelligence (AI) and robotics in production can improve efficiency, reduce labor costs, and increase output by automating repetitive tasks and improving precision.
Also, these common manufacturing software solutions streamline production processes and help you reduce waste and improve efficiency:
-
ERP software helps you optimize the use of materials, labor, and inventory, ensuring that resources are allocated effectively.
-
Tools like CMMS improve equipment maintenance and communication.
-
Connected worker platforms maximize workforce productivity and effectiveness.
These technologies create a more agile and cost-effective supply chain and position your business for long-term success.
Strategies for minimizing indirect supply chain costs
Minimizing indirect supply chain costs like storage, administrative expenses, and facility upkeep without sacrificing operational efficiency is critical for profitability. By strategically managing these costs, you can free up capital for more critical investments and prevent unnecessary overhead from eroding your margins.
Here are a couple of strategies for managing these costs and improving your business’s agility.
Optimizing warehousing management
Your warehouse management strategy can have a significant impact on overall supply chain costs. Lean warehousing practices, such as eliminating non-value-added activities and automating processes when possible, minimize excess handling and inventory storage costs. Just-in-time (JIT) inventory management systems further reduce costs by ensuring you only store what is needed. This prevents overstocking and frees up valuable warehouse space.
Maximizing the use of warehouse space is also critical for cutting inventory costs. For instance, Designing warehouse layouts to increase storage density and using automated storage systems helps companies maximize space utilization, reduce unnecessary expenses, and improve overall warehouse efficiency. These tactics not only lower indirect costs but also increase the responsiveness and flexibility of your supply chain.
Improving energy and resource management
Effective energy management not only cuts operational costs but also aligns with sustainability goals, positioning your business as a forward-thinking leader in the industry.
Here are some practical examples of energy and resource management strategies:
-
LED lighting: LED lighting uses less electricity and lasts longer, which reduces both energy consumption and maintenance costs.
-
Energy-efficient machinery and HVAC: Upgrading to energy-efficient equipment lowers energy usage and operating costs while improving system reliability.
-
Variable frequency drivers (VFDs): VFDs adjust motor speeds based on demand, reducing energy waste and extending equipment life.
-
Automated energy management systems: These systems monitor and optimize energy use in real-time, preventing waste and ensuring efficient operations.
By optimizing how resources are consumed, you free up capital that can be reinvested in other areas of the business — while reducing your environmental footprint.
Strategies for identifying and reducing hidden costs
Hidden costs, from carrying excess inventory to inefficient production processes, can plague any part of your supply chain. However, reducing these costs can be tricky because they are often hard to identify.
If you’re looking to eliminate these “invisible” expenses in your supply chain, here are the best places to start.
Solving inventory management issues
Inventory mismanagement accounts for a substantial proportion of hidden costs in supply chain management. Oftentimes, stockouts or excess inventory results from mismanaged or outdated inventory management systems paired with poor forecasting. To prevent this, it’s important to maintain up-to-date inventory systems and databases while leveraging AI-powered forecasting tools.
Additionally, improving your inventory turnover rates will minimize excess inventory expenses. With less capital tied up in unsold goods, you can improve cash flow and reduce the risk of products becoming outdated or damaged.
This lean approach to inventory management also frees up warehouse space and allows for more accurate forecasting, leading to more efficient operations and lower indirect costs.
Reducing opportunity costs
In supply chain management, opportunity costs are the profits or benefits lost when resources are allocated inefficiently. Although trade-offs are a normal part of business, it’s crucial for manufacturers to accurately calculate opportunity costs.
Manufacturers can mitigate opportunity costs by implementing agile supply chain strategies. This flexibility allows for more efficient resource allocation, preventing overproduction or stockouts that can drain financial resources or sabotage sales opportunities. Additionally, improving demand forecasting accuracy using predictive analytics helps align production with real-time market needs, ultimately freeing up resources for more profitable activities.
Leverage technology for easier supply chain cost management
Using digital technology like supply chain analytics is key to optimizing costs by providing valuable insights into operational efficiency. With intelligent tools available for nearly every area of supply chain management, manufacturers can dramatically improve the cost-effectiveness of their supply chain strategies.
With predictive analytics, manufacturers can enhance demand forecasting, ensuring better inventory management and minimizing excess stock or shortages. Real-time supply chain monitoring allows businesses to quickly identify inefficiencies, track performance, and make data-driven decisions that reduce operational costs.
The Internet of Things (IoT) plays a critical role in asset tracking and monitoring, offering visibility into the location, condition, and movement of goods throughout the supply chain. This helps improve logistics efficiency, reduce delays, and lower transportation costs.
Smart sensors further enhance real-time data collection, providing insights into equipment performance, warehouse conditions, and product status. This data enables proactive maintenance and quicker response to issues, preventing costly downtime and reducing waste.
By integrating these digital technologies, manufacturers can gain better control over supply chain operations, reduce inefficiencies, and drive long-term cost optimization.
Reduce supply chain costs with efficient manufacturing solutions
Optimizing manufacturing production efficiency can lead to major reductions in overall supply chain costs. The more streamlined your production processes, the better you can respond to disruptions such as material shortages and changing customer demands.
L2L’s connected workforce platform not only empowers workers with the tools they need to be more efficient — it also allows you to combine your manufacturing data with data from other systems. L2L Business Intelligence (BI) helps you merge data from manufacturing processes, machines, and your workforce with supply chain data, ERP systems, and inventory management systems.
This enhances your ability to identify the underlying causes of waste in the production process, visualize hypothetical manufacturing scenarios, and drive continuous improvement.
See for yourself how L2L can help you optimize your manufacturing facilities and cut down unnecessary supply chain costs when you book a demo or reach out to sales@l2l.com!
Revisions
Original version: 20 September 2024
Written by: Evelyn DuJack
Reviewed by: Daan Assen
Please read our editorial process for more information
Related Posts
Subscribe to Our Blog
We won't spam you, we promise. Only informative stuff about manufacturing, that's all.