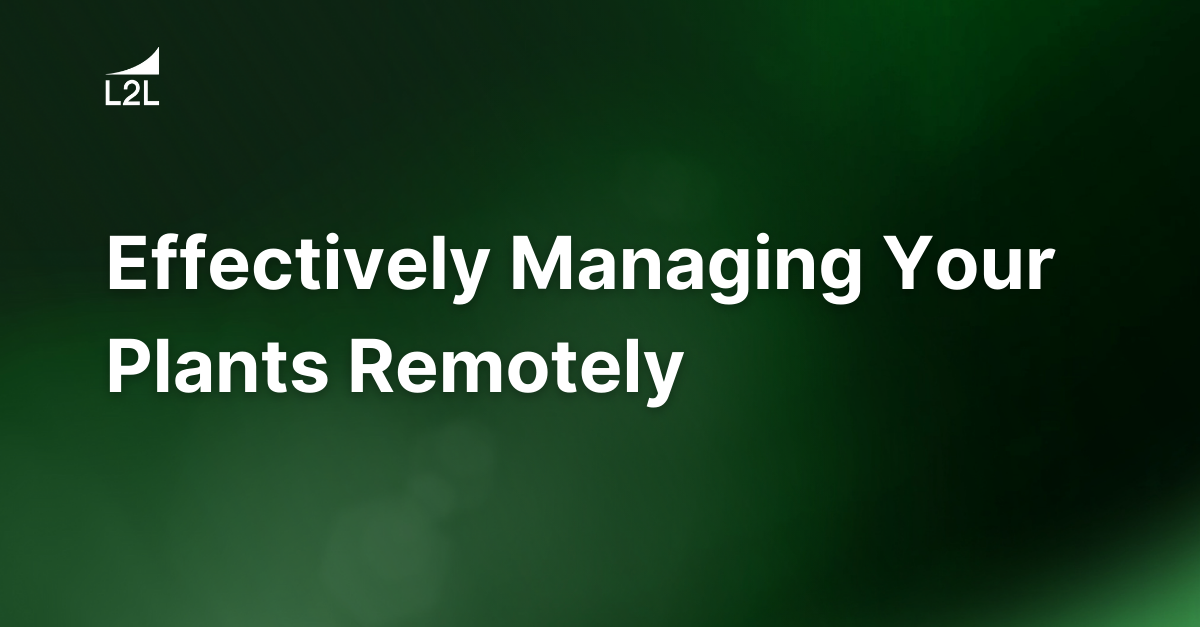
In 2020, "working from home" transformed from a millennial buzz word to a survival need in the workforce across every industry. For manufacturers this meant mitigating the number of employees working in the plant while still maintaining full productivity. There are numerous challenges in doing this, and with COVID-19, current situations range from drastically reduced demand for product in verticals such as automotive or energy to significantly increased demand for food and medical products.
In order to understand how manufacturers are responding in a variety of situations, we reached out to some of our customers to see what challenges they're experiencing and how they're dealing with them.
Current State of Manufacturing
Among current customers we're seeing everything from essential products where demand has increased to non-essential products where demand has decreased, and in some cases facing temporary plant shutdowns. In all cases, only essential employees remain on-site while anyone else that can work from home is doing so.
CI Manager - process manufacturing co: "Our products are clearing off the shelves. Everything we can make, we've already sold." "We gave people that are immunocompromised the option to be off work for awhile, but business is booming and we need to keep up with the increased demand."
Corporate Maintenance Manager - food processor: "We're classified as an essential product during this COVID-19 pandemic, and some lines of our business are seeing increased demand. For 'non-essential roles,' we're working remotely and have restricted all our travel."
IT Global MES Director - Tier 1 automotive supplier: "Some regions of the world are starting to ramp back up while others are shutting down. We are seeing forecasts come from customers now saying that they're planning to ramp back up by the first of May in most cases. So we'll see a solid month of 80% or less volumes."
General Manager - Tier 1 automotive supplier: "I would say in some areas it's a bit complicated because we're not able to do necessary things in person like our morning meetings. But to have all this technology available, it helps. It's good to have Skype, it's good to have zoom, it's good to have WeChat, and L2L."
VP Operations & Manufacturing - Food Packaging Supplier: Our operations have ramped up approximately 50% in recent weeks due to demand for canned food goods."
Challenges Created by COVID-19
The challenge is finding how to successfully continue producing product, or in some cases take advantage of the downtime to drive improvement or manage projects remotely. Here's what these manufacturing leaders are saying:
Corporate Maintenance Manager - Food Processor: With L2L, and a few other applications we have, I can pretty much do 90-95% of my job remotely. As long as I have internet or mobile phone access, I can get all my updates." "We're quarantined, but I can still data share with people at our plants through L2L."
IT Global MES Director - Tier 1 automotive supplier: "With the slow downs due to COVID-19, it's both a challenge and an opportunity. While our machines are down, we're taking advantage of the time to make improvements, and we're using L2L data to help us understand what the most critical improvements are we can make during this timeframe."
General Manager - Tier 1 automotive supplier: "We have to check much more what's going on in the company via computer, I have to know what my lines are producing. I cannot go there and check, and I cannot use my hourly boards anymore. I have to use the hourly board from my computer. All my operations guys, and production guys, they have to be much more in touch with their computers than before. This is a big change."
"This is the first time in my life that I've seen that visual management like traditional whiteboards or Kanban cards is not possible. Now we really have to rely on our screens, we really have to rely on software instead.
How L2L Is Helping Manage Remotely
IT Global MES Director - Tier 1 automotive supplier: "In the cases where lines are running, L2L has played a critical role in allowing people to understand the performance of the production line while they've been away from the plant." "We use mobile devices to notify maintenance technicians, and we use operator workstations to interact with L2L's LES. And I think, because those capabilities have already been there, we haven't had to train the workforce to do things differently. The social distancing has just come kind of naturally through that tool."
CI Manager - process manufacturing co: "Maintenance and production are still on-site, but supervisors are able to react to escalation through L2L as opposed to being out on the floor all the time, which has sheltered them from interacting with people as much during this time." "Our maintenance team is still conducting their downtime meetings remotely, and the fact that you have readily available reports you can run to see the status of an area or what's going on, and the escalation chain is built in, I don't think they've missed a beat. I haven't seen any degradation of maintenance support in the last few weeks."
General Manager - Tier 1 automotive supplier: "Some companies, you know, they preach 'let's go simple. Let's go lean,' and they don't like to use any of these software systems like L2L. However it's really the right thing to do, especially if we have this kind of thing happening [COVID-19]. If I didn't have this system, we would not survive. It would be really difficult to manage all the facility without using technology or any software like L2L's LES." "Before you could have the option to not look at your screen and maybe go to the shop floor, but now you can't."
CI Manager - process manufacturing co:"For PM [preventive maintenance] work in the past we print off paperwork, put it in a slot, and multiple people will handle that paperwork, furthering the potential spread of a virus. For the most part that's gone now. Another advantage is that if they have an iPad, they're not needing to use the same computer terminal as operations and other maintenance techs."
"The fact that everything is set up and automated, even if we weren't able to interface one way or another, PM's are still going to launch, production schedules are still going to launch, data is still captured, reporting is still going to be automatically generated. It's nice to know that you don't have to be as hands on as you did in the past."
Corporate Maintenance Manager - Food Processor: "Before we used L2L, we handled paper everyday. Having everything digital has helped us a hundred fold in staying safe in this regard. If we were still passing paperwork today, that would be much worse." "Through any adjustments we've made in recent weeks, L2L's customer support has continued to be on the spot."
IT Global MES Director - Tier 1 automotive supplier: "Our management teams very regularly check in to L2L through their mobile devices or their computers at home during office hours, when they're not actually in the office. So, for us transitioning to working from home was kind of second nature and largely because we already had the solution in place. It was fully functional, it was part of our culture. And so being able to extend that from just using it from home, you know, on off hours, we're able to use it from home all the time when we needed to immediately go to a home office."
VP Operations & Manufacturing - Food Packaging Supplier: "Without L2L... managing through the crisis would have been exponentially more difficult, which then would have impacted business continuity somewhere."
"The visibility into what's going on for our work-from-home crew who have anxiety about the status of production, and the communication tools in it have been definitely used as we've eliminated tier meetings and other meetings that normally were in person."
"I think that's one key thing, we haven't stopped improving. We want to be the best packaging plant in the world and so it helps bring some normalcy to us in this crisis to give people a purpose and say, before you fret or worry, where are you at on your A3 and tall poll?"
One Operations Director at a large electronics company even said, "I wish we hadn't waited on implementing your production module because it would be a big help right now."
Unique Solutions To Combat COVID-19 In The Plant
Manufacturers are showing their ingenuity in how they're adapting to scarcity of certain supplies:
VP Operations & Manufacturing - Food Packaging Supplier: "We've gone all in on the CDC protective measures but with a focus on business continuity." "We marked off most rooms with 6 foot distances, and eliminated most meetings that were deemed too great a risk." "We increased cleaning everywhere." "We didn't phase in the changes, we did it overnight." "We delegated maximum authority to make these changes to the plant managers, we didn't manage it centrally." "We had salary personnel train for shop floor jobs as well to backfill replacements." "Everyone was asked to identify skills they could do."
"We have actually made our own hand sanitizers from aloe gel so that we have a never ending supply of hand gel. We have mixed our own cleaner as well in certain places. And in order to address the shortage of nitrile gloves, we actually went out and basically cornered the market on certain kitchen gloves that are durable and can be reused for cleaning processes."
Coming Out of This Stronger
VP Operations & Manufacturing - Food Packaging Supplier: "This situation has kind of been a rally point, I think in many of our plants. They got shirts made up at corporate HR here for America. Hashtag here for America on the back and company name on the front."
IT Global MES Director - Tier 1 automotive supplier: "My biggest message is it really has felt kind of easy for us to transition to a home office work environment. And I think that L2L is a huge factor in that. We deployed L2L a few years ago and now it's part of our culture. There wasn't really any effort needed, it was just like 'everybody, go home, work from home' and we said, 'okay,' and when we did it there wasn't really much business interruption at all."
Overall we felt a great deal of positivity as we talked with these manufacturers. They've felt the pain of the pandemic, but have been able to respond quickly and smoothly so they wouldn't have to "skip a beat," and use the situation as an opportunity to improve. In tough situations, two things that make all the difference are the right tools and the right perspective.
If you would like to learn more about how we're helping manufacturers successfully manage their plants remotely, or take advantage of our free remote work consultation offer, click the Contact Us button below.
Revisions
Original version: 18 July 2024
Written by: Evelyn DuJack
Reviewed by: Daan Assen
Please read our editorial process for more information
Related Posts
Subscribe to Our Blog
We won't spam you, we promise. Only informative stuff about manufacturing, that's all.