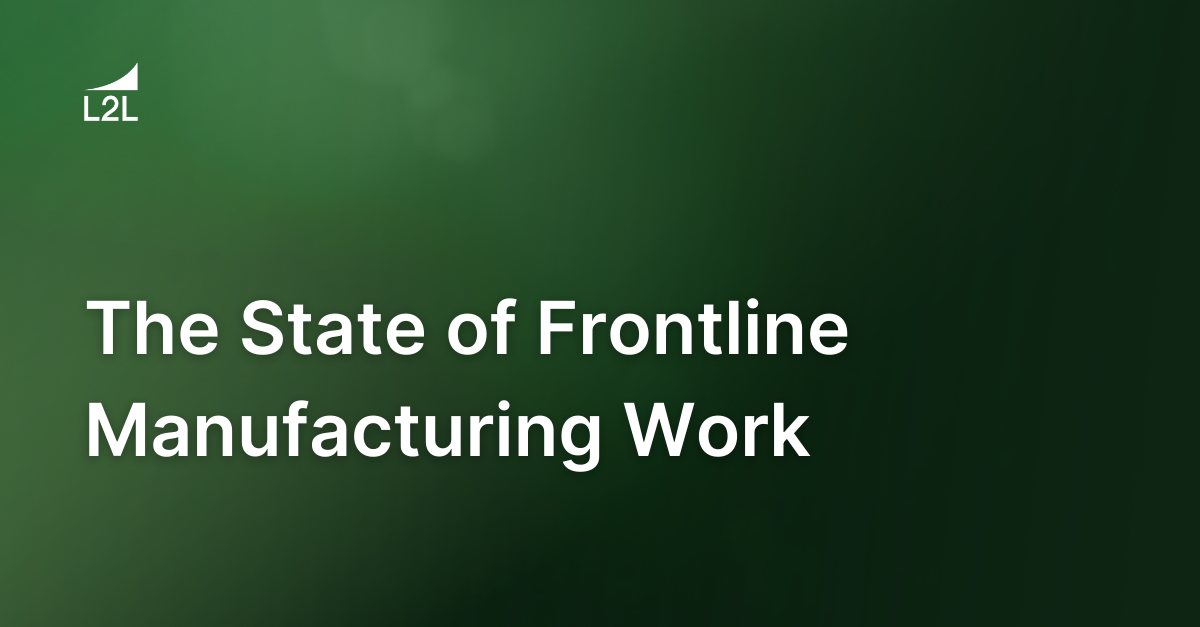
We asked 200+ manufacturing workers about their experience on the shop floor. Here’s what we learned.
Amid the current labor shortage, U.S. manufacturers are struggling to win the competition for shop floor talent. Attracting and retaining skilled workers is much more difficult than it was 20 years ago due to many factors, including a cultural de-emphasis on vocational work and sub-par experiences within manufacturing facilities.
However, manufacturers can address the latter by aligning processes and technologies with the way younger generations work offering paths for professional development.
In November 2023, L2L surveyed over 200 U.S. frontline manufacturing workers about their day-to-day workplace experiences and their sentiments about the future of manufacturing.
The workers surveyed spanned multiple generations, from ages 18 to 65+, with years of manufacturing experience ranging from 0 to 20+ years. The participants also came from various manufacturing roles, from shop floor production to plant management.
Below, we share the most important highlights from this report, including shop floor technology’s positive impact on workers’ experiences — plus some surprising insights we learned from the participants’ responses.
Part 1: The future of manufacturing labor
When asked how likely they were to consider a manufacturing job in the future, around 86% of respondents responded positively.
86% of workers surveyed said they would consider manufacturing work for their next job.
When asked if they agreed that the manufacturing field was attractive to young workers (under 30), 69.1% of respondents were in general agreement.
However, the respondents in the 18–29 age group weren’t as positive about manufacturing’s appeal to this demographic, with 64.3% in general agreement and 27.3% in strong agreement.
64.3% of respondents under 30 indicated that manufacturing is an appealing field for young workers.
On the other hand, respondents aged 30 and older were more optimistic, with 43.4% in strong agreement that manufacturing appeals to their younger counterparts.
43.3% of respondents 30 and older indicated that manufacturing jobs were attractive to younger workers.
While the survey didn’t uncover the causes of this generational disparity in opinion, the overwhelmingly positive response from older respondents could be attributed to the following factors:
-
Workers 30 and older tend to occupy higher-paying, more senior positions, while younger workers more commonly occupy lower-paying, entry-level positions.
-
Older workers may overestimate the impact of recent technological advancements on the overall shop floor experience.
-
Most young workers are looking for a career — not just a stable job — and feel that manufacturing work doesn’t offer the upward mobility they want.
Despite the difference in opinion over manufacturing’s appeal to younger generations, respondents across every age group were in near-unanimous agreement — 85.5% — that there is a shortage of skilled manufacturing workers in the U.S.
85.5% of respondents agreed that the U.S. has a shortage of skilled manufacturing workers.
While the manufacturing labor shortage can be attributed to a wide array of factors, poor day-to-day experiences, from communication barriers to low pay, are a leading cause of worker retention problems.
Here are the most common reasons manufacturing workers quit their jobs according to our survey results:
-
Salary too low (40%)
-
Poor communication (31.4%)
-
Bad physical work environment (16.4%)
-
Unclear or unrealistic expectations (15.9%)
When asked what attracted them to their current employer, though, the respondents cited slightly different factors as their most important considerations:
-
Salary (58.6%)
-
Good communication (32.7%)
-
The company makes interesting products (21.36%)
-
Better supporting technology (20.5%)
Unsurprisingly, pay is the top consideration for most manufacturing workers. However, the quality of workplace communication can also make or break the manufacturing work experience.
Another factor worth noting is employers’ commitment to environmental safety and sustainability: 86.8% of respondents consider this factor at least somewhat important when selecting an employer.
In the next section, we’ll explore how technology impacts plant communication and other important aspects of work satisfaction.
Part 2: The impact of technology on frontline manufacturing work
In general, survey participants agreed that mobile technology makes their jobs easier and improves productivity and safety, with 57.7% responding “Yes.”
Moreover, 76.8% of respondents said that they would consider changing jobs if the new company used technology that helped them do their jobs better or more easily.
When asked how important digital technology was to their manufacturing work, 69.1% stated that it was very important or somewhat important.
69.1% of respondents indicated that being able to use digital technology was important for their manufacturing work.
Not only did we find that manufacturing professionals tended to value the use of digital technology in their roles, but we also found that manufacturing software was particularly valuable to these workers.
In fact, 93.1% of frontline respondents said that the software they use on the factory floor helped them perform their jobs better.
93.1% of frontline workers believe the software they use in their jobs is useful and improves their performance.
Although shop floor software yielded significant benefits for frontline workers, most solutions still have areas for improvement.
According to this survey’s frontline respondents, the top improvements suggested for software at their manufacturing jobs fell into the following categories:
-
Improved user experience/user interface (UX/UI)
-
Clearer, more detailed work instructions
-
Inclusion of video content for training
-
Better software user training
-
Enhanced communication capabilities
-
More real-time data accessibility
Overall, our survey revealed that digital technology plays a pivotal role in helping workers do their jobs well, safely, and with less frustration.
Part 3: Key survey takeaways
Based on our survey data, we can conclude that the incorporation of digital technology into everyday manufacturing processes significantly improves the worker experience.
As shop floor software becomes more common, workers expect that technology to evolve with their needs; i.e., more access to real-time information, better UX/UI, mobile-friendliness, incorporation of video, etc. But advancements in manufacturing technology are only part of the equation in solving the industrial labor shortage.
Based on our survey, here are some key takeaways for manufacturers focused on improving employee retention:
-
Offer competitive pay and adequate opportunities for long-term career growth.
-
Ensure that communication among peers and supervisors remains clear, open, and efficient — connected workforce technology can help.
-
Be clear about your organization’s stance on environmental health and other ethical issues, and act accordingly.
-
Give employees at all levels a voice in organizational decisions when possible, and take time to show them that they’re valued.
To learn more about current manufacturing challenges and solutions, check out L2L's digital transformation survey and LNS Research’s new report on the future of industrial work.
Revisions
Original version: 6 December 2023
Written by: Evelyn DuJack
Reviewed by: Daan Assen
Please read our editorial process for more information
Related Posts
Subscribe to Our Blog
We won't spam you, we promise. Only informative stuff about manufacturing, that's all.