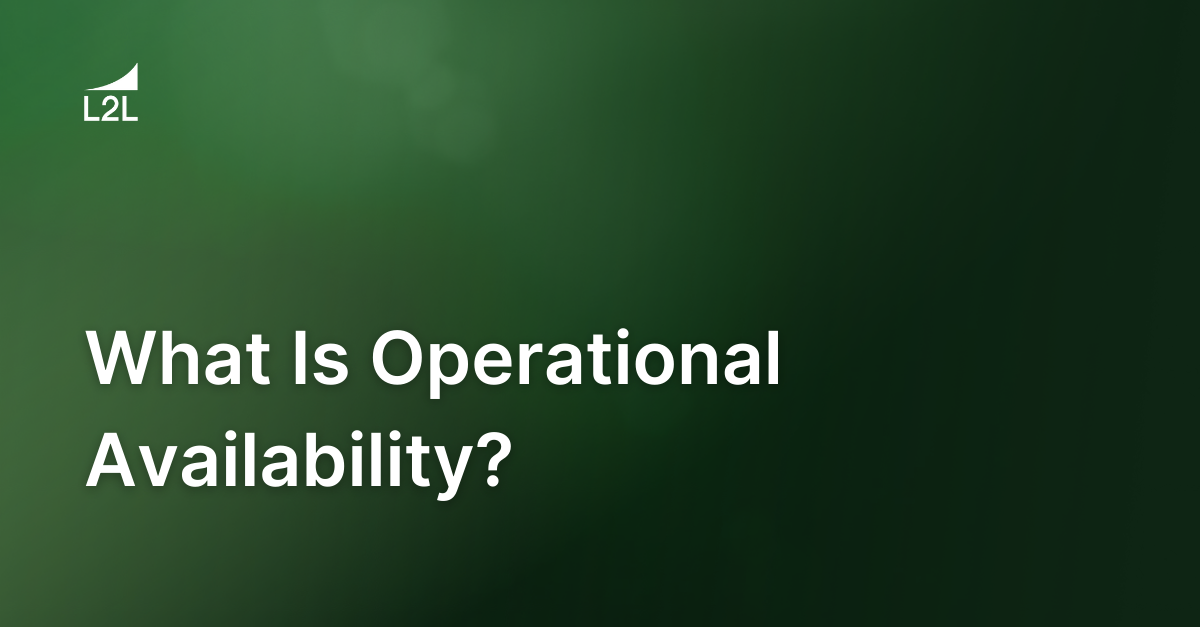
What is operational availability (OA), anyway?
In short, operational availability is an indicator of a piece of equipment’s reliability. It's calculated for all machines, lines, or cells. In short, a machine's operational availability is the percentage of time it can correctly function when it's needed for production. Ideally, each piece of equipment would have 100% OA.
Operational availability is the foundation for all manufacturing. A stable process is easy to predict and equals consistent results.
Do You Really Understand Your Operational Availability?
For years, I would almost brag about my manufacturing lines' and cells' stability. I would monitor operational availability regularly to understand my current capability and situation. My confidence was nearly unshakable.
On paper, the availability of my equipment and manufacturing areas looked great. However, when I drilled deeper within the data and compared operational availability vs throughput, the confidence I once had began to fade. When the pressure is high due to unforeseen conditions like missing customer shipments or quality issues, the environment can change quickly.
The pressure in manufacturing can be fierce. When times get tough and every minute of downtime is scrutinized, you will quickly find that the faith you had in your manufacturing equipment's operational availability wasn't as robust as previously thought.
Over the years, I've experienced many humbling instances regarding the operational availability of my manufacturing lines and equipment. On many occasions during these less-than-ideal times, I found myself working overtime on the production floor.
While these times were high-stress, I worked closely with manufacturing teams to mine some important information. We discovered:
-
The number of downtime instances that are unaccounted for
-
The importance of creating a standardized approach to identifying anomalies
-
How to use actionable data to drive change
-
Nothing builds more trust than positive results
-
Eliminating the waste identified by the production associates strengthens team relationships
Are You Capturing All Causes of Instability in Operational Availability?
Are you capturing all causes of downtime? Working closely with production associates, you can understand many types of incidental tasks and causes of downtime that plague your processes. Over time, these issues become normal and almost acceptable.
These high-occurrence and relatively low-downtime events destroy operational availability and allow for variation and instability to the process. Many of these occurrences aren't documented to reflect the true issues and causes of downtime.
Furthermore many of these events allow for variation within the process or product that results in a Jidoka condition, or no-good products. Time destroys this evidence, and when causes of instability and downtime aren't documented, it becomes difficult if not impossible to understand the conditions or events that led to these outcomes.
Ideally, we capture every event and document all the details for these events. These event details become gold, as this information is needed to make data-driven decisions. These events contain crucial data needed not only for determining operational availability and production measurables, but also for understanding the timing and documentation that details each specific event.
Nothing becomes more frustrating when you're forced to understand all the details for a condition or event that has happened in the past and hasn't been documented.
It's impossible to fully recreate events to understand their root cause. If it's not documented, it never happened!
Causes of instability in operational availability may include:
-
Machine downtime
-
Material downtime
-
Fault reset go
-
Poor changeover
-
Unstable workforce
-
Adjustments
-
Absenteeism
-
Poor execution
-
Poor shift change
-
Quality issues (scrap and rework)
-
No standards or standards not followed
It's likely that you'll identify special causes that drive downtime but are not captured. These events become "normal" and almost start to become justified as part of the standard process. Countless instances of fault/reset go, unjammed, cycle start, and more happen many times throughout the day and may be overlooked or disregarded.
Do You Trust Your Measurement Device/Method for Operational Availability?
Data is crucial when making decisions. For many years, I've seen decision-makers operate on emotions. The squeaky wheel gets the grease. Whoever has the most emotionally-charged request gets the resources. But if you want to identify and eliminate waste, you need to replace emotion-based decisions with actionable, data-based decisions.
When your process to capture events or downtime is difficult and time-consuming, the result is poor decisions and poor behavior. If your method of capturing downtime and events is inflexible and complicated to interact with, your measurement of operational availability is less credible.
Do you have a reliable method for calculating and capturing downtime? Without a consistent, reliable process to measure events and data, you will have no way to measure success.
L2L makes it easy with CloudDISPATCH, the software that names like Energizer and Autoliv trust to help them maintain operational excellence. Want to see how CloudDISPATCH can revolutionize your floor? Schedule a demo!
Revisions
Original version: 15 November 2019
Written by: Jon Richardson
Reviewed by: Daan Assen
Please read our editorial process for more information
Subscribe to Our Blog
We won't spam you, we promise. Only informative stuff about manufacturing, that's all.