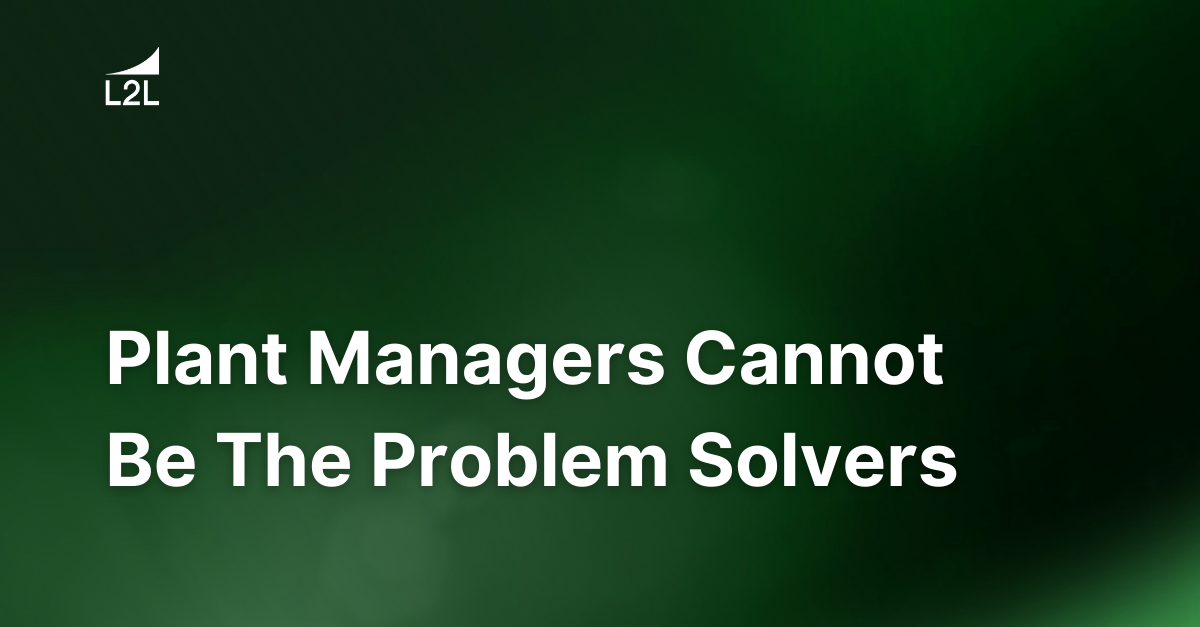
The human brain, especially for those in leadership positions such as a Plant Manager, is a problem solving machine.
The brain loves to solve problems, even those problems that have already been solved by someone else. Because being a problem solver has served these leaders so well in the past and may even be the catalyst for their rise to prominent positions, plant leaders spend valuable time and energy trying to solve the issues keeping their plant from achieving improved performance. But should they really be spending precious time on being the problem solver?
The question is really one of culture inside the manufacturing facility. If a culture of team problem solving is nurtured, then oftentimes there is a much deeper and richer culture of teamwork, lean problem solving methods, and continuous improvement. But, if these cultures do not exist, then the Problem Solving mindset is left up to the individual. Coming in like a knight on a white horse, the individual problem solver will look for an opportunity to stand out in the crowd with a brilliant idea that will save the day. But did this brilliant idea actually improve the process or did it merely stop the bleeding on one incident only to have the entire organization move on to the next disaster?
To stop this, a Plant Manager must transition from the Problem Solver persona to one of a teacher and coach to their organization on how to solve problems. There are three main approaches leaders should take to move in this direction.
1. Stop Relying On The Problem Solver
It is inherent in any process, and in entire plants for that matter, that similar processes and problems will arise across different departments and production lines. Much like quality defects found on different models of cars, if you see a defect or a problem on one particular car, you can rest assured that this same problem will rear its ugly head on all of the other vehicles of the same make, year and model. Because production lines and processes are usually designed and implemented within a certain timeframe, producing the same product and using the same raw materials, problems and issues will appear on numerous lines at the same time.
Real strife occurs when individual employees are the problem-solvers for that individual line or machine. You know the person I am talking about. The one we all look at and say, “Wow, they sure do know how to run that machine better than anyone else”. The fact of the matter is they are the best individual problem solver for that machine or process and that’s good for nobody.
This was made evident to me during a training session years ago in a chicken processing facility when a new employee confessed that “I really thought I was somebody because I was the only one in the plant who could run the Oxy-fuel and hybrid combustion rotary aluminum furnace. But that all changed when the plant shut down, I discovered that there weren’t another one of those furnaces within 1000 miles of my house and I didn’t know how to do anything else”.
Plant leaders must find a way to share this knowledge across lines, teams, departments and even plants if they want to do right by their plants and employees.
2. Gosh Darn It! Find The Root Cause.
Really, this step is about integrity to follow the previous piece of advice. To stop relying on the Problem Solver and put real lean problem-solving processes, procedures and culture in place to solve the problem at the root cause. The Plant Manager is the one person that can have the temperament and control to put these things in place. This will not be a section on how to do problem-solving, but better yet how to implement technology, processes and people that can help focus on the real root cause of the problems you face.
Recent advancements in Smart Factory platforms like L2L allow for a Plant Manager to have all of the data available for their team to expose the real problems. For example, in a recent visit to a plant, we found they had implemented Smart Factory technology that allowed the operator to digitally indicate every single time the machine stopped and the reason for the stoppage. We call these Operator Fixes in L2L. What the data exposed was the largest amount of downtime for that piece of equipment came from the operator having to enter the stacking robot cage to straighten the pallet in the case stacker. This data was not just downtime numbers, but actual defined data that could then be handed to a team to solve that particular problem at the root cause.
Root cause problem solving, like all continuous improvement and lean manufacturing techniques, has evolved into the technology age. It is a Plant Manager’s obligation to provide their employees with the best technology and thus the best opportunity to succeed, even in root cause problem-solving.
3. Stop Solving Solved Problems
Please bear with me here for a quick personal story. My wife owns a small tea shop and recently she met with her employees to figure out a way to standardize the amount of cream they put into drinks to go. Various ideas were talked about and they finally landed on using a small cup to measure the amount. The next morning, as we sat at breakfast and she related this story to me, a quick Amazon search revealed that someone had designed and produced a creamer pump specifically designed to fit the bottle of store-bought brand of creamer they use.
My point here is that improvement and problem solving can be simple if we take just a few minutes and approach the problem much like my automobile scenario. If I am having this problem, then surely someone else must be as well and therefore a solution may already be available that’s quicker, cheaper and simpler. Teaching a team of individuals this technique can be as fruitful as any lean problem-solving method you may deploy across the factory. This is especially true when it comes to sharing ideas and having a platform like L2L that allows for these ideas to be shared sideways (yokoten) from department to department and plant to plant. Imagine the power of a single repository of improvements that could be shared between processes in America, Europe and Asia all at the click of a button.
So when a problem in the plant arises, a plant leader can quickly go through these three steps in their head and start the team and organization along the path of building that culture.
- Stop relying on the Problem Solver
- Have the right data to find the root cause
- Stop solving a solved problem
Using these three techniques, a Plant Manager can quickly change the culture in their factory and improve the business at the same time.
Interested in learning more, check out our OnDemand webinar below:
Revisions
Original version: 18 July 2024
Written by: Evelyn DuJack
Reviewed by: Daan Assen
Please read our editorial process for more information
Related Posts
Subscribe to Our Blog
We won't spam you, we promise. Only informative stuff about manufacturing, that's all.