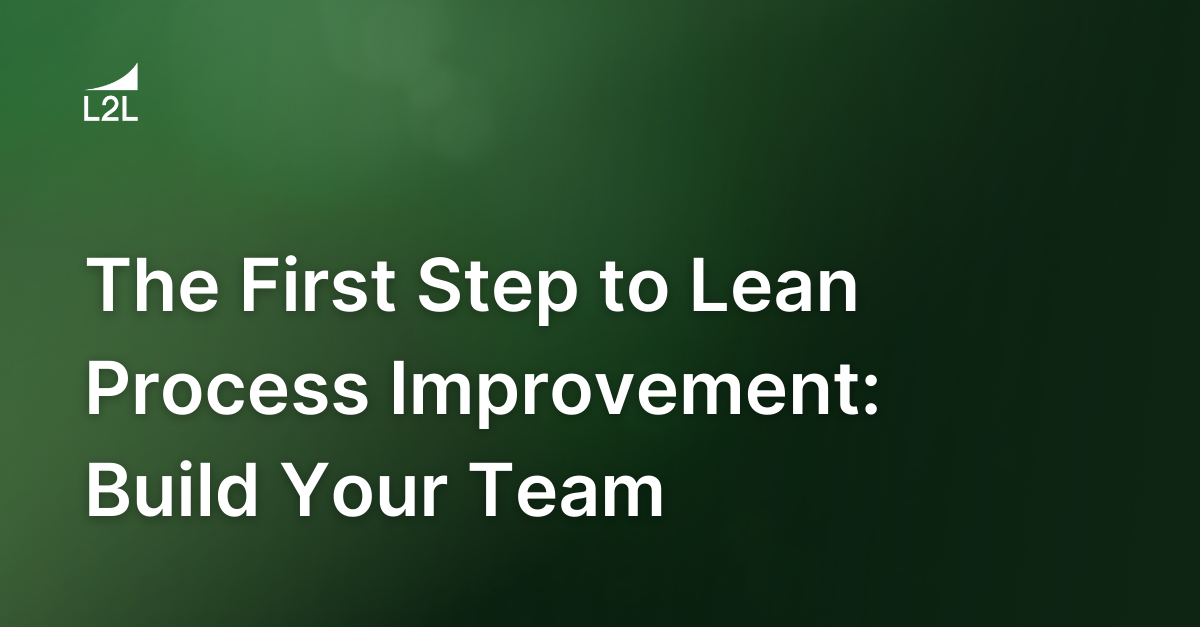
I asked if lean process improvement is a journey, a treasure hunt, or the ultimate X-Games for manufacturing and production. Or is it something else entirely?
If you think this is a trick question, pat yourself on the back. If you answered, "All the above," Bravo! Way to avoid this common pitfall.
There's no single correct answer. How you and your teams embrace this quest in your facility is entirely up to you. Well, almost. There are a few aspects of lean process improvement that are essential elements and will be included universally, no matter your industry or end goals (goals, plural — because you should always have more than one).
What Is Lean Process Improvement?
Lean process improvement means continually reviewing your operations to identify opportunities to do better. Lean process improvement opportunities come in varying shapes and sizes. Some of them can seem rather small or insignificant at first glance. That doesn't mean they aren't worth exploring. Nothing inspires your teams like getting some victories under their belts.
Where to start this lean process improvement? Just as this is not a one-and-done deal, neither is it a one-man or one-woman show. There is no "lean" without "team."
Assemble Your Lean Process Improvement Team
Put together a lean process improvement team made up of people from different physical locations as well as different areas of responsibility from within your plant. Having folks from Maintenance, Quality, Manufacturing, Safety, and even Accounting and Purchasing makes for a great interdisciplinary group. Each department brings a different point of view to the table.
Make sure you include varying ages, backgrounds, and years of experience. You don't want every person to be a manager, nor do you want every person to be a new hire. We all have filters that influence our views and our approach.
In a diverse group, everyone will have a concept of where their piece of the puzzle fits into the overall strategy. With these different puzzle pieces, you get more clues as you put the pieces in and start to glimpse the big picture.
Here's another tip when putting together your team. Every member cannot be the head chef, nor can every person chop the vegetables or wash dishes. It's great to have some people who have an idea of what they're doing already. It's also great to have people who bring enthusiasm to the mix. You don't want an entire team of people who say either "yes" or "no" every time. Most importantly, you want to have people who will work together and be respectful of other team members' ideas.
Work with your team and brainstorm some ideas. What are some of your site's problem areas, historically — even if they're not huge? What are some annoyances people from each department deal with regularly? Problems that seem negligible on the surface cold have a bigger effect on your plant's performance than you realize.
My very wise mother had an expression that I have used countless times: "A man can sit on a mountain, but he can't sit on a tack." Think about that for a minute and you'll get the point (pun intended).
None of us stuff an entire apple in our mouth all at once. We take one reasonably sized bite after another, and we get to the core of that apple every single time.
Using a Problem Statement to Inform Your Lean Process Improvement
Now that you have your team together, what do you want to tackle?
You need a problem statement: A description of an issue or concern to be addressed and improved. Identify the current state, the problem, and the desired state: where you are and where you want to be. Taking the time to define what you're trying to accomplish will return better results in the long run — and your team is in it for the long run.
It's easier to get where you're going when you know where that is. Waze and MapQuest are great substitutes for throwing darts at a globe. Make sure everyone has a clear understanding, and the same understanding, of what the problem is, where you're starting out, and where you want to be at the finish line.
There are some great tools available to help you craft your problem statement.
Here are some things to keep in mind:
Establish a baseline measurement for each problem. Your lean process improvement team will realize each problem is an opportunity. Lay out the workflow and scrutinize the path your product takes from raw material to finished goods.
Incorporating cause and effect may help wrap your head around the problem. Quantify the problem. Not every problem has the potential for huge windfalls in terms of either cost savings or creating revenue, but many of them will. This is one time when you will be forgiven for discussing finances with strangers.
Implementing Lean Process Improvement
You have your team in place. Check. You have your first problem statement. Check. What aspects of the problem statement should you go after?
-
Unnecessary tasks: Are you polishing that apple for a good reason or because you've always polished it?
-
Redundant steps: Do you inspect that gadget twice because of a customer mandate or was that a stop-gap measure put in place in the early days?
-
Do associates like pushing wheelbarrows out to the back forty, uphill in the snow? Or could your vendors' drivers place their components closer to where you need them in your operation?
-
What if you didn't pay for those components until you actually consumed them?
-
What if you didn't have two of everything? Could you liberate some real estate, not have so much money tied up in inventory, not build twice as much as you need, or not have to sort through two years' worth of finished goods if you find a problem?
-
Do associates in any part of your organization have to wait for approval? More than one layer of approval? Is this an opportunity for streamlining and efficiency by training and empowering the people who do the work to make these decisions?
-
Do you have people who spend their time running copies, collating, and copying? Stapling and shuffling? Please note the date and the century. Don't even get me started on the price of paper and printer ink. Plus those boxes of paper are really, really heavy.
-
Is manual data entry still part of business as usual? If so, you also have data correction people. Any data that doesn't have to be entered manually doesn't have to be corrected manually, either.
-
Do you deal with quality concerns on a regular basis? Do you have designated rework experts?
-
Do you have exorbitant warranty costs?
-
Are customers screaming about late deliveries?
-
Are you turning inventory before or after it starts drawing a pension?
-
Are you constantly paying expedited freight charges?
-
Do you have the local airport on speed dial?
These are very real issues and they can be very painful. Sometimes, we're so busy running around cutting bandages to stop the bleeding that we forget we shouldn't be running with scissors in the first place.
A Final Word on Lean Process Improvement
As you pursue opportunities to get better, your lean process improvement culture will flourish. You're not in this alone. Highlight the victories of your team and share those wins across your plant. As your team grows in confidence, encourage those members who are ready to form teams in their own areas.
Remember, lean process improvement is not a one-time event. It's a mindset and a better way to begin each day. The satisfaction of knowing you have made lean process improvement strides is also a great way to look back on your day.
And if you really want to make lean process improvement easy, check out L2L's revolutionary software — everything you need to build a powerful lean process improvement system is built into the system.
Revisions
Original version: 18 July 2024
Written by: Evelyn DuJack
Reviewed by: Daan Assen
Please read our editorial process for more information
Related Posts
Subscribe to Our Blog
We won't spam you, we promise. Only informative stuff about manufacturing, that's all.