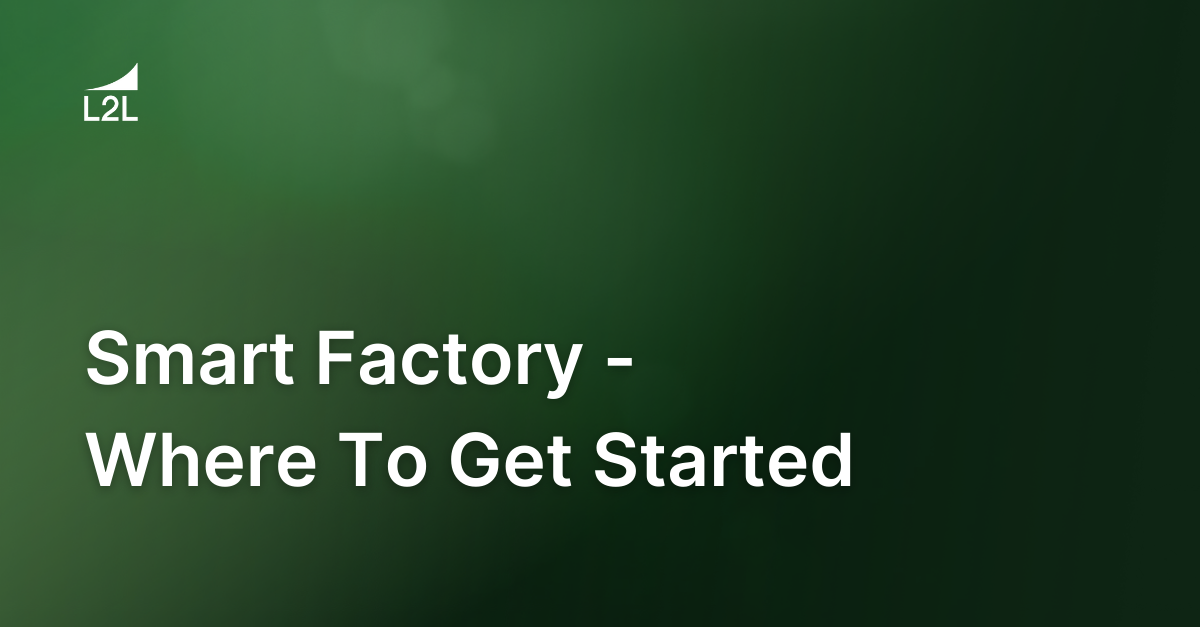
Before we talk about where to start applying Smart Factory technology, it will be helpful to first understand the 5 essential capabilities you’ll want to establish to facilitate the right first steps in your digital transformation journey. These 5 key capabilities are:
- Visibility at each level
- Prioritization insight
- Resolution structure
- Speed to value
- Employee empowerment
We walk you through those in our eGuide A Smarter Approach To The Smart Factory, so if you haven't given that a read, I recommend you check it out. Now that you know what those key elements are, the question becomes, where do you get started and what resources will it take?
The Word "Smart"
Sometime prior to the 12th Century, the word Smart entered the human dialect and according to Webster’s the definition at that time was: having or showing a high degree of mental ability. Subsequently, in the 13th Century, the semantics of Smart morphed to include: to feel or endure distress, remorse, or embarrassment…”That Smarts!”
800 years later the word Smart has taken on a brand new definition. This time to include: operating by automation and/or using a built-in microprocessor for automatic operation, for processing of data, or for achieving greater versatility.
In the context of taking steps toward a Smart Factory, all three definitions actually apply. Smart Factory implementation requires people who have a high degree of skill, we know it doesn’t come easy (there will be some pain), and it requires technology that has only recently been made available to those in manufacturing.
The Smart Factory Project - 5 Keys for a Successful Start
Smart Factory implementation, like other projects, is at its root, a series of tasks that must be accomplished to gain an end result. There are however 5 Key principles you can follow to help ensure a successful implementation of your Smart Factory.
Simplify the Scope
In order to get started, first we have to frame the situation properly to help simplify. Industry 4.0 or digitization can be hard to grasp as a concept, but if you think about what you can do within the four walls of your factory, it starts to become a bit more concrete and manageable. To use an oversaturated euphemism, the key here is to not attempt to “Boil The Ocean”.
Pick one aspect of your factory you want to improve. What is your greatest heartache right now? Is it downtime? If so, then you will want to find your number one culprit in the entire plant. Somewhere on your factory floor there is a single piece of equipment that is giving the largest amount of problems. Start there! Implement the right devices that are going to give you the data you need to solve that single problem, then repeat this process. This approach has minimal cost and maximum impact.
Neutralize the Pressure By Knowing The True Goal
During the onset of a Smart Factory project, plant leadership becomes subject to a tremendous amount of pressure from internal and external influences. Internal corporate leadership can place this pressure by looking for speed and efficiency in the implementation and seeking the
desired results in the shortest possible time frame at the lowest possible cost. More internal pressure comes from support departments such as IT and data analysis groups who claim results will not be realized until large amounts of infrastructure, such as middleware applications, server hardware and integration support are in place throughout the entire enterprise.
At the same time, external vendors add pressure by claiming data must be captured at every point in the process, often suggesting that this be accomplished through the purchase of their products. All of this pressure combines to an ineffective implementation filled with high stress, scope creep and blown budgets.
There is a simpler way!
Start Where It Hurts (Appropriate Integration)
Quick results in a Smart Factory implementation are not achieved by quickly implementing a large and blanketed integration system. Quick and efficient results are products of deploying what is known as ‘appropriate integration’. Appropriate Integration begins through the deployment of simple to use Cloud-based technology like L2L that quickly gives a team visibility to processes that are causing the greatest amount of disruption to production. Only when this single disruption or constraint is identified should smart technology such as IoT (Internet of Things) and IoP (Internet of People) devices be deployed, and only in that area, and only when a clear ROI can be projected.
The key here is not to deploy technology in hopes of discovering issues, the key is to deploy a simple inexpensive software like L2L that will identify where the company should be spending its Smart Factory dollars. Speed and efficiency in the deployment comes from the fact that while a team is installing the technology exactly where it is needed, L2L is busy collecting the data to help identify the next focus area. Efficiency and cost savings come from the team’s ability to repeat this process in areas that will yield the greatest results.
Use Your Smartest Device
Key to any Smart Factory implementation is the involvement of the smartest device already deployed on the shop-floor. Of course I am talking about the human mind. Each employee processes the ability to give instant feedback on the status of your production process in real-time. The question becomes: Are you using that advantage or is it still locked up because there is not a process or system that easily allows for that information to be tracked?
As suggested in the previous paragraph, companies are understanding that at the foundation of a Smart Factory implementation is the need to simplify and easily get this data from the employee. New software design technology, along with increased availability and reduced cost of mobile devices coupled with rapidly improved access to cloud services has finally delivered the ability to have your employees participate in the real-time data collection process.
As society has become increasingly more comfortable in the use of Apps and websites for social applications, that knowledge of how to design software so that anyone of any age can use it has bled over into software design being used on the factory floor. Social intelligent design is a must have and an integral part of L2L’s ability to be used by all ages and facets of your organizations. We often make the statement, “if you can post pictures of your Grandkids online, then you can use L2L”. We all know that creating a positive User Experience through a simple to use User Interface on today’s software is the only way to ensure that factory workers will be the front-line to capture the data that drives your Smart Factory implementation.
Conclusion
A Smart Factory implementation can quickly over burden local leadership with pressure to perform on all levels including Cost, Efficiency and Buy-in. Simplifying the Smart Factory project approach by deploying cloud-based software to identify the troubled areas of the production process is the right first step towards the Smart Factory. Once this step is complete, the process of deploying the appropriate IoT and IoP devices can take place.
This focused approach reduces overall implementation costs and yields instant results for all to see. Finally, if ensuring the right devices are deployed to the right problem area is key to success, then using the brains of your employees to help collect data in real-time is the ultimate deployment of Smart Factory technology. Giving them a simple to use User experience will create buy-in and ownership from those dealing with these issues on a daily basis.
If you haven’t read our new eBook, A Smarter Approach to the Smart Factory, it covers 5 essential capabilities for smart manufacturing success. you can find it here.
Revisions
Original version: 18 July 2024
Written by: Evelyn DuJack
Reviewed by: Daan Assen
Please read our editorial process for more information
Related Posts
Subscribe to Our Blog
We won't spam you, we promise. Only informative stuff about manufacturing, that's all.