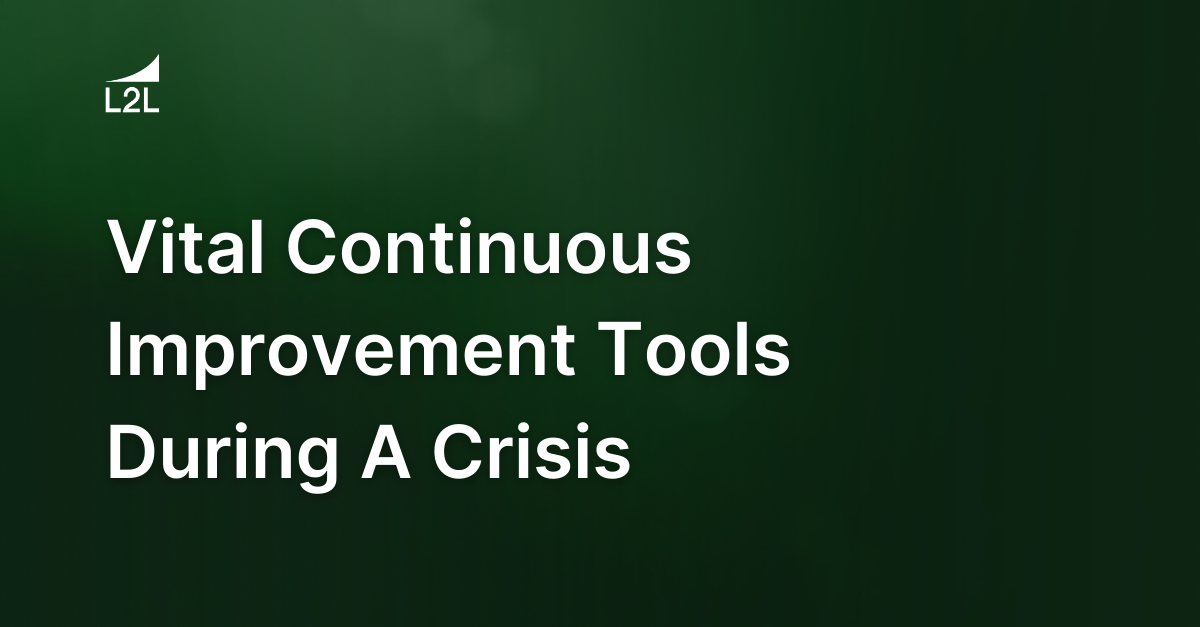
What are Continuous Improvement Tools and what does Continuous Improvement really mean anyway? The idea of continuously improving can seem daunting. There are many facets and approaches to Continuous Improvement. Don't get caught up in the rhetoric. Like so many philosophies, memorizing every term is not the important point. So, take a deep breath and relax while we talk about Continuous Improvement and Continuous Improvement Tools in words we use every day. You'll be amazed how easily these ideas translate to the 'real' world and even to your own life in particular.
Continuous Improvement is True North
One way to conceptualize Continuous Improvement in simple terms is to think of it as always driving towards "True North". Where is 'True North' on the map exactly? How do you know when you're there? Much like True North in our own lives, on a personal level, driving towards True North means always seeking to be and do better. Continuously. Not once a year as a resolution to be discarded by Valentine's Day. Striving to reach the best version: of yourself, your relationships, your dealings with others, both inside and outside your business life.
Continuous Improvement does not mean only perfection is acceptable. As my good friend, Voltaire, liked to say, "Perfect is the enemy of good".
In relation to the use of Continuous Improvement Tools, driving towards True North includes the unrelenting pursuit to identify and eliminate waste. "True North" is a concept in the Lean Continuous Improvement process. It is an idea that emerged from Toyota years ago, symbolically using the needle of a compass as a metaphor for the Lean transformation process. True North works as a compass, providing a guide to take an organization from the current condition to where they want to be, "True North". In many ways, it might be viewed as a mission statement, the purpose of an organization, and the foundation of a plan.
In the context of Lean, True North is a precise, concise, and universal set of ideals. These ideals, when considered and implemented together, provide a compass that transcends any one organization, strategy, geography, or culture.
Continuous Improvement Tools
Continuous Improvement Tools come in various shapes and sizes. Many products have been developed that are intended to help the user gain knowledge and understanding of how and when to utilize these Continuous Improvement Tools.
There are many terms and tools that have become remarkably familiar "buzz" words over the years. Terms and tools such as Kaizen, Yokoten, Jidoka, Takt Time, Level Loading, Standardized Work, and Problem Solving for example. If you've been walking the Lean path for some time, all of these words evoke certain thoughts and ideas about your Lean journey. When you took your first steps down that path, who could have imagined that these words would become part of our everyday vernacular? Perhaps equally amazing is the reality that in addition to talking the talk, we've embraced walking the walk. These are not just buzz words representing the current flavor of the month. We grasp the philosophies these embody as well.
Maybe that's really the key that unlocks the box of Continuous Improvement Tools: embracing change and being open to new methods and philosophies.
All of these elements play strategic roles in the overall Continuous Improvement process, both individually as well as collectively. They are not only essential, they are immensely powerful as well. Incorporate them and essential tools to be used to ensure a robust lean continuous improvement process is utilized.
It takes more than just one or two of these tools to propel the drive towards "True North". Utilizing these Continuous Improvement Tools is the foundation to create and foster the culture of Continuous Improvement within your organization.
Lean Continuous Improvement Tools are no different than skills employed in other arenas. The tools must be developed and honed, just as carpenters, athletes, and musicians must learn and master their "tools of the trade" if they are to remain competitive and viable. Each tool must be ingrained through implementation, practical lean activities, and mastering the tools over time and continued use. Learning to master these tools long term will lay the groundwork for further lean system and site development and transformation.
The Continuous Improvement Process in a Crisis
Times of crisis tend to affect how people think and act. The challenges of such situations breed powerful emotions which can shift our outlook and reasoning. Most often, these negative feelings of fear, helplessness, and even denial drive us toward a fatalistic mentality because it seems that trying to adapt to the situation is asking too much of ourselves and would be a wasted effort. By accepting circumstances and allowing them to dictate our actions, we can achieve some sense of security amidst uncertainty – and master our continuous improvement process.
A Continuous Improvement Process is Key
For all the comfort provided by a fixed mindset, it also prevents us from achieving anything greater than a “safe” outcome. There is another path, though. While crises typically create negative emotions, they also incite other compelling feelings – empathy for others, decency to do right, and even the love of a challenge.
These can be leveraged to push ourselves instead to a growth mindset (a.k.a. a kaizen mindset, a continuous improvement process), where setbacks become opportunities for learning and better outcomes. And when a business commits to this approach, the results can be significant: because it’s a return to the proven power of the continuous improvement process.
A Snippet of Continuous Improvement History
Although the continuous improvement process and crisis do not seem natural partners, Kaizen, continuous improvement’s most popular approach, was born of catastrophic circumstances.
Kaizen arose in post-WWII Japan from the import of Edwards Deming’s Plan-Do-Check-Act approach to quality improvement, the economic necessity to achieve more with less, and the local tact to engage all levels of the organization.
The outcome was the ability for a business to become more adaptable and innovative through identification and implementation of efficiency gains based on insight from a company culture with an instilled growth mindset.
For Japan, this process resulted in year-over-year GDP growth and product quality such that by the 1980s, it was a leading global economic force. Businesses that therefore pivot from a protectionist approach during turbulent times, and instead lean on their continuous improvement fundamentals will not only come out ahead, but potentially transformed.
Continuous Improvement Process Fundamentals
There are central tenets across the multitude of continuous improvement methodologies. Examining each is a reminder of their value under normal conditions and reveals their importance during periods of upheaval.
Define What’s Important
All good problem-solving first starts with a thorough understanding of the issue: distilling down the current situation, the consequences of this state, and the justification for addressing this condition. Rigor in problem definition ensures the right questions are asked to avoid wasting resources on subjects that do not align with business objectives or conversely, leave outstanding issues on the table.
When business circumstances change, as during an emergency, the focus becomes reassessing and potentially narrowing the scope of the strategic plan. These campaigns, typically formed at the outset of the fiscal year, must be pared down to their essential pieces by asking what are the critical business priorities at that time – such as operational continuity or personnel safety – to assure proper resourcing and commitment from leadership.
Customer Focus
For many businesses, attention is rededicated to understanding who is the customer: which individuals does the company need to care for in these times, and what is valuable to those customers? Employing empathy to identify the customers’ needs reveals which processes to concentrate effort and resources on and how to define criteria for success.
What Success Looks Like
With the critical customers and processes during the crisis identified, the metrics by which these goals will be managed must be defined. Goals, as always, should be specific, measurable, attainable, relevant, and time-bound to drive individuals and the organization on the correct trajectories to achieving necessary changes. Any preexisting metrics that do not support core activities should be set aside for a time to keep focus on those essential tasks.
When considering what to measure to recognize improvement, though, leading indicators for the subject processes should be used whenever possible: the further upstream an operation can be monitored, the earlier aberrant conditions can be identified and amended. Additionally, focusing metrics on the means of a process, versus the process output, engages front line personnel in managing and improving those vital operations.
Ownership & Communication
To properly execute a plan, whether during normal operations or in a crisis, two elements are needed: ownership and communication. Each component of a strategy should have an autonomous owner responsible for implementation, and the entire plan and the status of each component should be available to all. Providing visibility in this manner reinforces the accountability of owners while also promoting collaboration: an outside perspective may help another owner overcome a hurdle to completing a task, or fresh eyes may spot an additional opportunity otherwise not in .
The Obeya room is a powerful continuous improvement tool that satisfies the need for accountability and visibility, while also promoting: speed. An Obeya room is like a “war room”; it contains the strategy, the delegation of responsibilities, and other essential decision-making tools such as escalation policies and up-to-data. Centralizing and sharing these management elements facilitates rapid issue resolution by assuring the information needed is consistent and readily available to all involved.
Engage the Workforce
Continuous improvement, like many business initiatives, are made stronger by leveraging workers’ collective intelligence: the people most familiar with the work and processes of focus will know best the issues and shortcomings, and are most likely to have considered what innovations and modifications would be of greatest value. Many techniques to engage the front lines relate to the other building blocks of continuous improvement and, as demonstrated, can easily be retooled to focus on the critical crisis-response activities:
- Burning Platform: share initiatives with personnel, both in terms of the specific goals that each department can impact as well as the broader effect they will have on the company and customer
- Communicate: provide continuous access to information and status of enterprises so people can see their influence
- Enable: provide tools and a forum for employees to interact and collaborate with strategic program leadership
- Acknowledge: recognize contributions with both thanks and with action to implement ideas
Try– Try – Try
The continuous improvement process is based making change part of daily life. The approaches mentioned above; defining a strategy and metrics, communicating goals, and engaging personnel; all help to bake ownership of improvement into an organization’s culture. To maintain the momentum of change and innovation brought by such engagement, implementing improvement must be broken away from a project life-cycle structure for the iterative plan-to-check-act cycle.
Organizations taking this approach drive consistent action developing and testing multiple solutions to an issue through cyclical trial and error. Particularly in times of crisis, process change cannot be allowed to stagnate by seeking progress over perfection. While a lack of thorough planning and design may be unsettling, a bias toward action ensures that improvement is always achieved, either radically or incrementally. Furthermore, it serves to also perpetuate the culture in which all employees are responsible for identifying and resolving problems.
Revisions
Original version: 18 July 2024
Written by: Evelyn DuJack
Reviewed by: Daan Assen
Please read our editorial process for more information
Related Posts
Subscribe to Our Blog
We won't spam you, we promise. Only informative stuff about manufacturing, that's all.