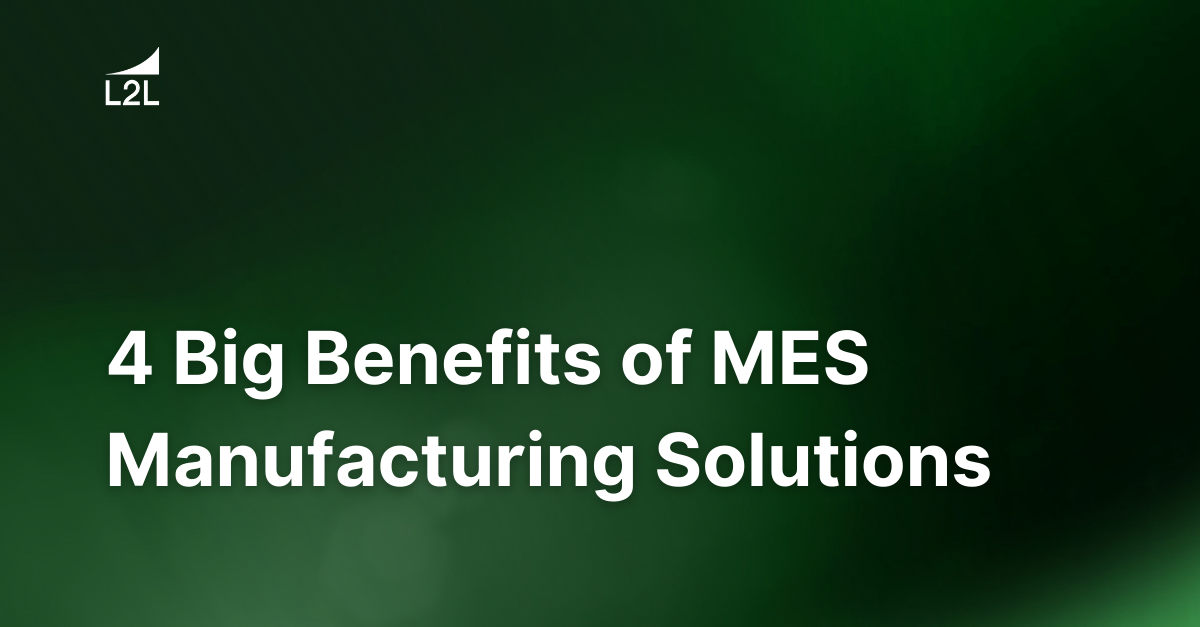
Estimated read time: 8 minutes
Imagine you’re a newcomer to the manufacturing industry. You’ve never stepped foot on a shop floor in your life, and things like EAM, ERP and OEE are just alphabet soup to you. (That’s “enterprise asset management,” “enterprise resource planning” and “overall equipment effectiveness,” respectively, by the way.)
If you were new here, wouldn’t you expect something called a “manufacturing execution system” (MES) to be the best solution on the market? The be-all, end-all solution that stands as a shining example of everything smart manufacturing hopes to accomplish? The best friend of manufacturers everywhere?
Well, in general, MES hasn't been the magic bullet that many wished it to be.
To be fair, a well-designed manufacturing execution system does have a few things to offer to your overall manufacturing process. It just may not keep all the promises it makes.
Today, though, we’re giving MES manufacturing solutions a fair shot. Let’s take a look at why MES hasn’t lost its place on the factory floor (and how you can make those benefits go even further).
How do manufacturing experts define MES?
You may not really be a newcomer to the industry, but it’s still helpful to look at some basic definitions — especially if you want to understand what an MES is and where it drops the ball.
To dive into the history of the manufacturing execution system, we’re starting way back in 1996. Janet Jackson is the highest-paid musician in history, “Fargo” is brand new and the Manufacturing Enterprise Solutions Association (MESA) has just established 11 core functions of an MES.
These functions are organized around Supply Chain Management, Enterprise Resources Management, Sales and Service Management, Product/Process Engineering and Controls. Here they are, in all their glory:
-
Operations/Detailed Scheduling
-
Resource Allocation and Status
-
Dispatching Production Units
-
Product Tracking and Genealogy
-
Maintenance Management
-
Labor Management
-
Quality Management
-
Data Collection
-
Process Management
-
Performance Analysis
-
Document Control
Now, like most things from 1996, this model has since been updated and reconfigured. However, the point remains that MES was originally expected to be a magic bullet.
Spoiler alert: It isn’t.
Although these 11 functions created a helpful framework, they ended up illuminating all the ways in which traditional MES typically falls short. Sure, nothing’s perfect — but MES made promises and failed to keep many of them. That’s the kind of thing manufacturers don’t soon forget.
Of course, we’re not here to exact vengeance on an underwhelming, underperforming traditional manufacturing execution solution. We’re here to take an honest look at what MES can do.
4 benefits of manufacturing execution solutions
A manufacturing execution system may not be everything your shop floor needs, but it does a few things, and it does them really well. Here’s a look at what MES still has to offer:
Visibility
Although a traditional manufacturing execution system (and even some outdated MES software) probably shouldn’t be your only solution for visibility, it certainly has a few things going for it. Take, for example, product traceability — the old “track and trace.” Having an MES at your disposal makes this process more transparent and, thus, better at supporting your overall return on investment (ROI).
MES is also a good option for supply chain visibility. It helps you more confidently navigate disruptions, raw material shortages and other key supply chain issues by tracking the goods you need the most.
Finally, if you’re looking for better ways to handle logistics scheduling and planning, you could do a whole lot worse than MES. With the right MES software, you might even be able to overcome workflow inefficiencies and keep all your assets and shop floor workers pushing in the same direction.
Machine management
Look, if you want predictive or preventive maintenance, then EAM or CMMS are your best bet (make sure you’re looking at a next-gen maintenance solution though if you go down that path).
If, however, you’re interested in machine process control, an MES solution might be able to help you out. The system gives you the ability to monitor a machine’s production process, allowing you to make changes and see the results in real-time. It doesn’t have the robust value of a modern enterprise asset management solution, but it does provide key data that can help improve your manufacturing operation.
Data management
Speaking of key data, an MES can help you juggle some of that, too. Recipe management is a particularly relevant example, as managing recipe data is one of the things a manufacturing execution system does best — and, of course, it’s a highly important part of your production process.
There’s also regulatory compliance to consider. Although there are elements of compliance that fall outside the MES umbrella, well-designed MES software can help you manage data in ways that are both efficient and secure. It can also help you keep track of how local, state and federal laws may impact your data capture process.
Labor management
MES probably isn’t your best bet when it comes to complete labor management. However, it can help lay the groundwork for other solutions in a few crucial ways, giving you some of the tools you need to help support workers on the shop floor (and beyond). Plus, it’s a great tool for more effectively managing the policies and procedures that make you stand out from the competition on the hiring front.
Getting more out of your manufacturing execution software
Be honest: Did you read that last section and find yourself asking, “Is this really it?”
The truth is that MES isn’t perfect. As manufacturers, we know that — and the entire industry is working to decide what happens next. Do we bite the bullet and spend the time, money and resources necessary to implement a complex MES setup that might get close to providing key benefits? Do we give up on manufacturing entirely and choose an easier career?
Both of these questions have one answer: No.
We’ve come this far with MES, and it has a few things it does really well. That means it’s best to identify gaps in your average MES solution and find a tool that bridges those gaps. (More on that in a minute.) Let’s take a look at some of the most important shortcomings of a manufacturing execution system:
Lack of a standardized approach
Imagine MES like a kid following you around and judging everything you do. It’s good at pointing out issues, but it’s not so good at telling you which solutions are ideal. That becomes really irritating really quickly. It also results in a break/fix process that only treats symptoms of production issues and fails to address the underlying causes.
Quality control
Although a good MES solution is certainly capable of managing and monitoring certain elements of the production process, it drops the ball on quality assurance. MES is worried about how and when production happens; the outcome is someone else’s problem. Unfortunately, that “someone” is you.
Transparency
Yeah, yeah — “visibility” was already on our list of MES benefits, so it seems like a cheap shot to include “transparency” on this list of weaknesses. The truth is that, while a manufacturing execution system can help you control some kinds of data, it leaves you high and dry in other cases.
Take, for example, the dreaded audit. If you’re leaning on a traditional MES solution to help you manage an audit, you’ll quickly realize the system has not been keeping track of data like records — which means you’re probably in some trouble.
MES also isn’t great at tracking certain material data. Inventory management? Order scheduling? Material shortages on the shop floor? For these things, you’re on your own.
Skills and training
Remember when we said MES probably isn’t your best bet for labor management? That’s because traditional MES software only tells you one part of the story. It’s totally blind to other details like tracking employee progress in skills training and certifications. This doesn’t just sell your workers short; it also puts factory floor teams in a position where they often have to cross their fingers and hope other employees know what they’re doing (because there’s no single, unified platform to help leaders keep track of this information).
So, how do you begin to improve on MES with all of these gaps?
Fear not: There’s good news on the horizon. With solutions like L2L CloudDISPATCH and our L2L Production module, you don’t have to give up on your traditional MES. Instead, you can bridge the gaps in its performance and end up with one approach that actually keeps its promises. Better yet, you won’t have to worry about starting from scratch; our smart factory approach and process control system can integrate with your existing MES solution, which means you won’t lose any progress you’ve already made. (Learn more about our by-manufacturers, for-manufacturers software on our blog.)
MES can be a powerful tool. You just need to give it a helping hand.
Don't give up on MES
If you clicked this article hoping to find some validation or redemption for your manufacturing execution system, we hope you can breathe a sigh of relief. Sure, traditional MES software disappointed all of us when it failed to live up to MESA’s expectations back in 1996 — but MES, like everything else, has come a long way since then.
Some of that progress is based on our better, more accurate understanding of what an MES system should do. Most of it, though, is thanks to bigger, better solutions that have stepped in to pick up the slack from MES.
Those solutions can be yours. Don’t give up on MES — just book a demo of our Smart Manufacturing Platform to see what’s possible.
Revisions
Original version: 18 July 2024
Written by: Evelyn DuJack
Reviewed by: Daan Assen
Please read our editorial process for more information
Subscribe to Our Blog
We won't spam you, we promise. Only informative stuff about manufacturing, that's all.