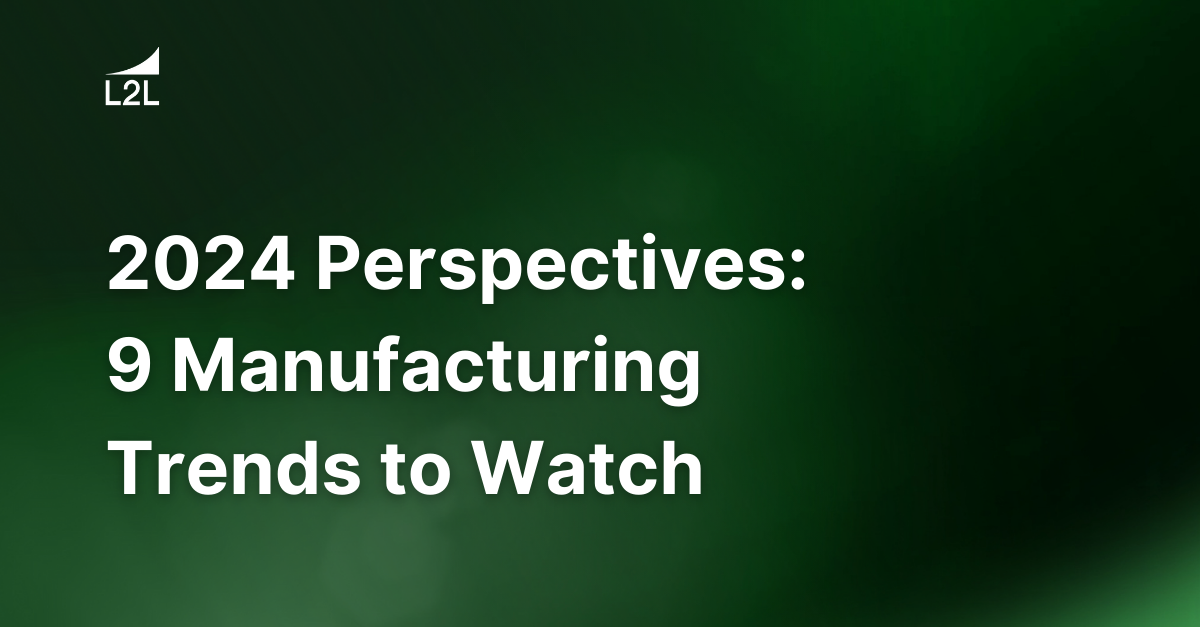
In 2023, the U.S. manufacturing industry experienced significant growth spurred by federal initiatives and private sector investment. Despite the uptick in industrial construction and funding across various sectors, manufacturers still struggle with labor shortages, supply chain volatility, and balancing net-zero benchmarks with cost-effective production methods.
Experts believe that the key to overcoming these challenges lies within the promise of advanced digital manufacturing technologies. While not a fix-all, Industry 4.0 innovations have already proven revolutionary in improving industrial companies’ productivity, efficiency, compliance, and even labor retention.
As manufacturers navigate economic and operational challenges, we can expect to see the following manufacturing trends shape the industry in 2024.
1. Further investments in digitalization and smart manufacturing
Within the past decade, we’ve seen dramatic changes in how manufacturers operate. Digital systems have all but replaced traditional pen-and-paper processes. Emerging technologies like artificial intelligence (AI) and robotic process automation (RPA) are rapidly gaining popularity in industrial settings, and this trend will only accelerate in the coming years.
In 2024, we’ll see more factories embracing smart manufacturing — or digitalization of end-to-end manufacturing processes. Smart factories are designed to increase output and boost cost-effectiveness by integrating AI, machine learning, the Industrial Internet of Things (IIoT), automation, robotics, and other advanced technologies into every stage of production.
Processes driven by automation and intelligent technologies outperform manual processes, thus positioning smart manufacturing as a key driver of industrial transformation. Consequently, we can expect more manufacturers to incorporate advanced digital technologies into their operations in 2024.
2. More work, fewer workers
Although intelligent manufacturing technologies are taking over repetitive tasks traditionally performed by human workers, manufacturers still struggle to fill open jobs. Based on current trends, the ongoing labor crisis won’t abate in 2024.
Deloitte shows U.S. manufacturing labor market fluctuations over the last five years. Source.
The tightening U.S. manufacturing labor market indicates that manufacturing careers aren’t as attractive as they once were, especially regarding shop floor work. With experienced manufacturing workers leaving the workforce — and taking their skills and knowledge with them — companies are left with massive skills gaps that younger generations aren’t filling. Simply put, they don’t stay around long enough to become the skilled workers they’re intended to replace.
While some expect smart technologies to augment this absence of workers, research suggests the growing adoption of innovations like AI may drive the need for more workers. A recent report by the Manufacturing Leadership Council revealed that 32% of manufacturing leaders surveyed believe AI will only increase their need for human workers.
There’s no doubt that labor shortages will continue to top manufacturing leaders’ list of concerns in 2024. However, industrial companies are also expected to boost their investment in attracting and retaining skilled workers.
Learn more about this topic in our eBook: The Manufacturing Leader’s Guide to Attracting and Retaining Skilled Labor.
3. Wider adoption of predictive maintenance
Predictive maintenance isn’t new to industrial companies. In fact, experts estimate that the global predictive maintenance market will reach $64.3 billion (US) by 2030.
As with other AI-powered technologies, predictive maintenance is growing in popularity among manufacturers due to its cost-saving and downtime-preventing capabilities. Its name comes from its ability to predict potential mechanical failures before they occur by applying data analytics, sensor technology, and machine learning to detect and mitigate abnormalities.
In the near future, we’ll likely see digitally mature facilities basing predictive maintenance strategies on digital twins, or virtual replicas of machines or processes. This practice lets manufacturers test and implement predictive maintenance systems with less risk and better cost-effectiveness.
Avoiding unplanned downtime is crucial for lowering costs and meeting production targets. With predictive maintenance becoming more advanced and effective, manufacturers increasingly consider this technology a must-have for future-proofing operations.
4. Strong focus on data management
As manufacturing operations have become more data-driven, the need for robust data management systems has skyrocketed. Each day, plants collect innumerable data from processes, machines, people, and other sources that need to be organized, analyzed, and evaluated. But their data is only as valuable as their ability to put it to use.
Overwhelmed by big data, manufacturing companies are increasing their investment in data management solutions. We can expect this trend to accelerate in 2024 as companies expand their data collection and governance processes.
LNS Research illustrates the importance of implementing a data management and governance framework with manufacturing organizations. Source.
By properly capturing, storing, and democratizing data across their organizations, manufacturers can easily glean insights and improve decision-making processes.
5. Using AI and related technologies
The concept of AI has been around for decades, but the manufacturing industry has been slow to incorporate AI into its production processes. However, research indicates that most manufacturing leaders will invest heavily in AI and related technologies within the next few years.
AI applications in manufacturing will extend across nearly every function, including procurement, quality control, maintenance, research and development (R&D), production, and more. For example, machine learning algorithms will continue to enhance quality control, helping manufacturers spot defects faster and fine-tune processes to prevent further quality issues.
According to a new report by Deloitte, incorporating generative AI into workforce training will become increasingly common. By analyzing data on specific workplace scenarios, including safety hazards, AI can better tailor content to a facility’s specific needs. Additionally, we’ll see AI paired with augmented and virtual reality (AR/VR) technologies to create simulated training environments.
6. Welcoming cobots to the production floor
Factory automation and robotics help manufacturers speed production, improve quality and efficiency, and enable workers to focus on more complex tasks. In 2024, we can expect to see even wider adoption of RPA and related technologies — including collaborative robots (cobots) to augment human work.
Cobots are a subset of robotics designed to work alongside people in industrial settings. Often equipped with computer vision, they’re typically used to perform dangerous or repetitive tasks, such as heavy lifting or packaging, making factories safer and more efficient. With their growing popularity among manufacturers, the global cobot market is expected to reach almost $2 billion (USD) in 2026.
7. A slow shift to product-as-a-service model
Manufacturers are beginning to embrace the product-as-a-service (PaaS) model — selling products on a subscription basis — to adapt to evolving consumer preferences, operate more sustainably, and avoid overproduction. This shift offers customers access to products without committing to ownership, promoting a circular economy. For example, an auto parts manufacturer can “rent” welding robots for a certain number of months or welds and send them back when they’re no longer needed.
Manufacturers benefit from recurring revenue streams, increased customer loyalty, and the ability to continuously upgrade and monitor products. Additionally, the PaaS model helps companies meet the rising demand for flexible, cost-effective solutions, fostering innovation while promoting resource efficiency and waste reduction. It reflects a strategic response to market dynamics, emphasizing collaborative, long-term relationships between manufacturers and consumers, and we’ll likely see more industrial companies shift to PaaS in 2024.
8. Continued focus on sustainability
Sustainability has been a major focal point for industrial organizations in recent years. To reduce their environmental impact and meet increasingly strict EHS requirements, manufacturers are boosting their investments in resource-efficient production processes in 2024 and beyond. Reducing carbon emissions, promoting circular economy principles, partnering with clean energy suppliers, and improving process efficiency will be central to manufacturers’ sustainability focus moving forward.
With the industrial sector accounting for nearly 30% of U.S. greenhouse gas emissions, manufacturing companies feel growing pressure from customers to adopt more sustainable practices. We predict that 2024 will showcase more plants incorporating robotics, AI, sustainable packaging, and recycling initiatives into production processes.
9. Getting in front of cybersecurity concerns
Cyber threats have become an unfortunate byproduct of digitalization. As factories become more reliant on software to run their production processes and store their data, the risk of cyberattacks, particularly in the form of ransomware, increases significantly.
In 2022 alone, the U.S. manufacturing sector faced approximately 250 data violation incidents, which impacted around 23.9 million users. Moreover, the global cost for each security breach was approximately $4.47 million (USD).
To protect their organizations from costly cyber threats, manufacturers are prioritizing cybersecurity in their digital transformation projects now more than ever. Moreover, experts urge manufacturers to carefully vet suppliers and other supply chain players for proper cybersecurity measures before partnering with them.
Stay on top of manufacturing trends
In 2024 and beyond, manufacturers must focus on future-proofing their businesses. Increasing operational efficiency through smart technologies while establishing comprehensive data security protocols is critical for hitting production targets and minimizing disruptions. Creating a workforce environment that attracts skilled workers and encourages them to stay long-term will continue to be foundational for success in the coming years.
Manufacturers that focus on digital maturity and take proactive steps to retail skilled labor will be better positioned for innovation and sustained growth. Don’t get left behind in 2024 — equip yourself with the knowledge and tools you need to become an industry leader.
To fast-track your industrial transformation journey, download LNS Research’s FREE eBook: The Future of Industrial Work: Developing a Sustainable Workforce Strategy.
Revisions
Original version: 22 December 2023
Written by: Evelyn DuJack
Reviewed by: Daan Assen
Please read our editorial process for more information
Related Posts
Subscribe to Our Blog
We won't spam you, we promise. Only informative stuff about manufacturing, that's all.