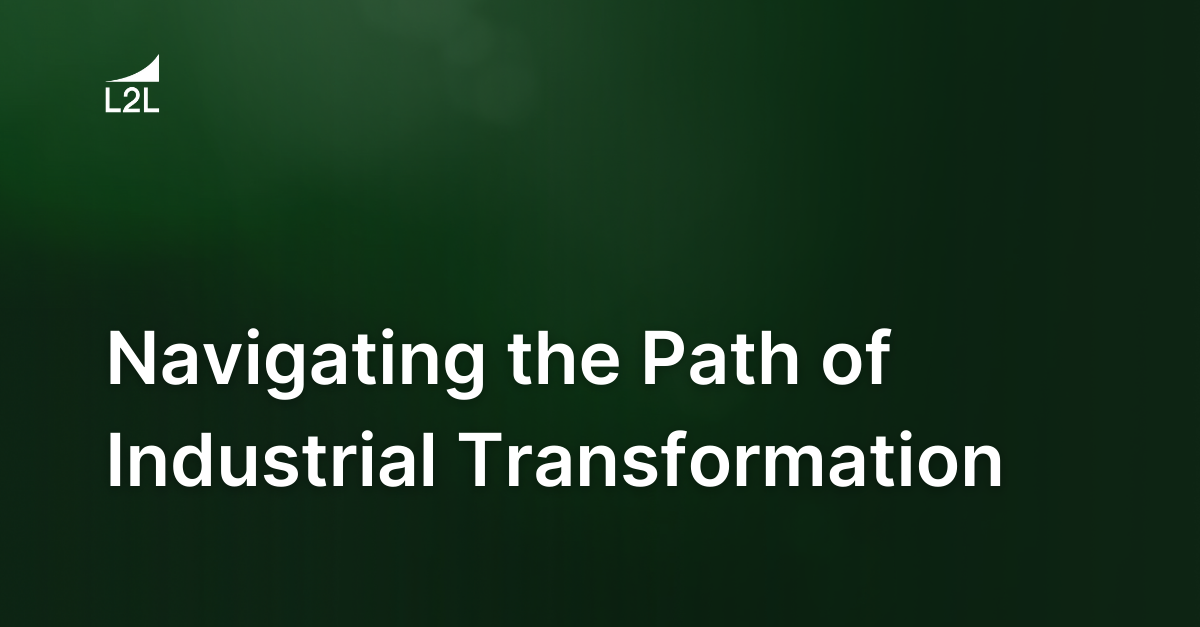
By now, you’ve heard hundreds of stories of companies and entire industries “going digital.” The manufacturing industry is no exception, and massive change is happening — fast.
Industrial transformation (IX), often called Industry 4.0 or the fourth industrial revolution, is an ongoing paradigm shift in the industrial sector that involves the integration of advanced digital technologies into various aspects of the manufacturing process.
Manufacturers invest in IX with the goal of enhancing productivity, efficiency, and competitiveness by using innovations like automation, big data, real-time analytics, the Internet of Things (IoT), and robotics. In fact, experts now consider IX critical for future success due to the value it unlocks across manufacturing processes.
In this article, we’ll cover the drivers of IX, why it’s critical in today’s industrial landscape, and how you can get started on your digitalization journey right now.
Understanding industrial transformation
Industrial transformation fuses traditional manufacturing and industrial practices with the digital world. It uses digital technologies to enable systems capable of self-monitoring and decision-making, fostering a more efficient, agile, and innovative industrial ecosystem.
The journey of industrial transformation actually began with the first industrial revolution in the 18th century, characterized by the advent of mechanization and steam power. Mass production techniques ushered in the second industrial revolution, and electronics integration and automation led to the third. Now, the fourth industrial revolution, or Industry 4.0, is standardizing smart manufacturing, digital supply chains, and connected ecosystems.
Here are some of the key drivers of industrial transformation:
-
Technological Advancements: Rapid advancements in technology are central to IX, paving the way for more innovative solutions and opportunities in the industrial sector.
-
Global Competition: As industries vie globally, there is an increasing need to adapt to changing market dynamics, necessitating transformation to maintain and enhance competitive edge.
-
Consumer Expectations: The modern consumer demands personalization, quality, and convenience. Industries are transforming to meet these evolving expectations, shifting towards a more customer-centric model.
-
Sustainability: There is a growing emphasis on sustainable and responsible manufacturing. IX offers the tools and methodologies to achieve greener, more sustainable industrial practices.
-
Government Initiatives and Regulations: Governments worldwide are initiating policies and regulations to encourage industries to adopt smarter, safer, and more sustainable practices, serving as a catalyst for transformation.
How long does the typical industrial transformation process last?
Remember: Industrial transformation is a long process that requires substantial forethought, commitment, and continuous adjustment and collaboration. It won’t happen in a quarter, or even a year.
IX journeys vastly differ from company to company, and the same is true of their timelines. How long your IX process will take depends on many factors — particularly your digital maturity.
According to LNS Research, most industrial enterprises will take three to five years to finish a transformation of this scale. However, the speed at which you go from vision to value depends on your organization’s preparedness for IX.
The main stages of the industrial transformation journey
Since IX is a complex and time-consuming process that affects every area of a business, the journey must happen in multiple stages. For most organizations, the main stages of IX look something like the following:
Stage 1: Assessment and planning
The assessment and planning stage of IX involves evaluating current manufacturing processes, workforce capabilities, and technology infrastructure. You can begin by conducting a gap analysis to identify disparities between your organization’s current state and ideal state in terms of technology adoption and efficiency.
Define key performance indicators (KPIs), perform a cost-benefit analysis, and build a roadmap for digital technology implementation. Then, sit down with stakeholders and map out your vision and strategy for your IX journey.
Stage 2: Implementation
The implementation stage is where you put your plans into action. This involves technology adoption, redesigning processes to align with new digital systems, and workforce training and development to get everyone up to speed with new tools.
During this phase, you’ll help your entire company transition to the transformed state, optimizing operations, and improving efficiency while keeping your workforce updated and engaged during a period of massive change.
Stage 3: Optimization
Optimization focuses on continuous improvement — finding out what works and what doesn’t. This stage requires you to refine systems and processes, establish feedback loops to gather data, analyze performance, and make necessary adjustments to enhance efficiency and productivity.
During this phase, you must ensure that new systems and technologies support organizational goals and allow for ongoing refinement, scalability, and flexibility.
Stage 4: Maturation
Once you’ve reached the maturation stage of IX, you’ve already integrated new technologies into your existing systems, redesigned processes, and made countless adjustments along the way. Now, it’s time to take what works and scale it across your organization. This often means expanding your transformed factory’s capabilities with new integrations.
However, you’ll also need to conduct continuous performance monitoring to ensure that you stay on target with your goals.
Common pitfalls: Why industrial transformations fail
As with any major technological (and cultural) transitions, industrial transformation journeys come with a wide range of challenges. Some of these challenges can derail your transformation altogether without a clear vision and careful planning. In fact, some experts report that up to 70% of transformations end up failing.
However, your organization doesn’t have to be part of that statistic. Here are the most common — and avoidable — pitfalls manufacturing leaders must navigate during IX:
-
Weak commitment from top management: Unless your organizational leadership fully supports your IX initiatives, you’ll have a hard time finding the time, resources, and support for a successful technological overhaul. If top management doesn’t support IX, neither will your employees.
-
Lack of clear vision and strategy: IX is an undertaking far too significant — and expensive — to execute without a crystal-clear vision and strategy. Aligning stakeholders around your vision and producing a detailed, multi-phase plan for implementation, optimization, and continuous improvement is crucial for success.
-
Inadequate technological infrastructure: Part of being prepared for IX is ensuring that you have the right technological infrastructure for the transformation you want to achieve. While upgrading your existing tech stack may seem like a hassle, it’s far easier and cheaper than discovering your system’s inadequacies midway through IX.
-
Resistance to change: Change equals disruption, and not everyone will be on board with learning new tools and systems. This is why it’s critical that you clearly communicate the value of IX to everyone who will be affected by the transformation.
-
Workforce unpreparedness: IX initiatives often fail because workforces lack the skills and training to maximize the value of new technologies. Make sure you put sufficient time and resources into training and upskilling, and use solutions like a connected worker platform to make the learning curve more manageable.
-
Poor project management and leadership: Poor project management and leadership can lead to misalignment of goals, ineffective resource allocation, and lack of direction, undermining the successful execution of IX initiatives.
Overcoming these challenges requires not only meticulous planning and research but also buy-in from your organization's leadership. Make sure you have both before committing to your IX journey.
Is your plant ready for industrial transformation?
Now that we’ve covered the basics of industrial transformation, its stages, and the challenges to navigate during your IX journey, it’s time to assess your organization’s readiness for an endeavor of this scale.
When handled the right way, IX brings indispensable benefits to manufacturing facilities, including increased productivity and efficiency, a reduction in downtime, and greater workforce longevity. But every IX success story begins with an organization that’s fully prepared.
Where does your company sit on the digital maturity scale? If you’re not sure, now is the time to figure that out. And you can do this for FREE with L2L’s Digital Maturity Assessment, which takes only five minutes to complete.
Revisions
Original version: 3 October 2023
Written by: Evelyn DuJack
Reviewed by: Daan Assen
Please read our editorial process for more information
Related Posts
Subscribe to Our Blog
We won't spam you, we promise. Only informative stuff about manufacturing, that's all.