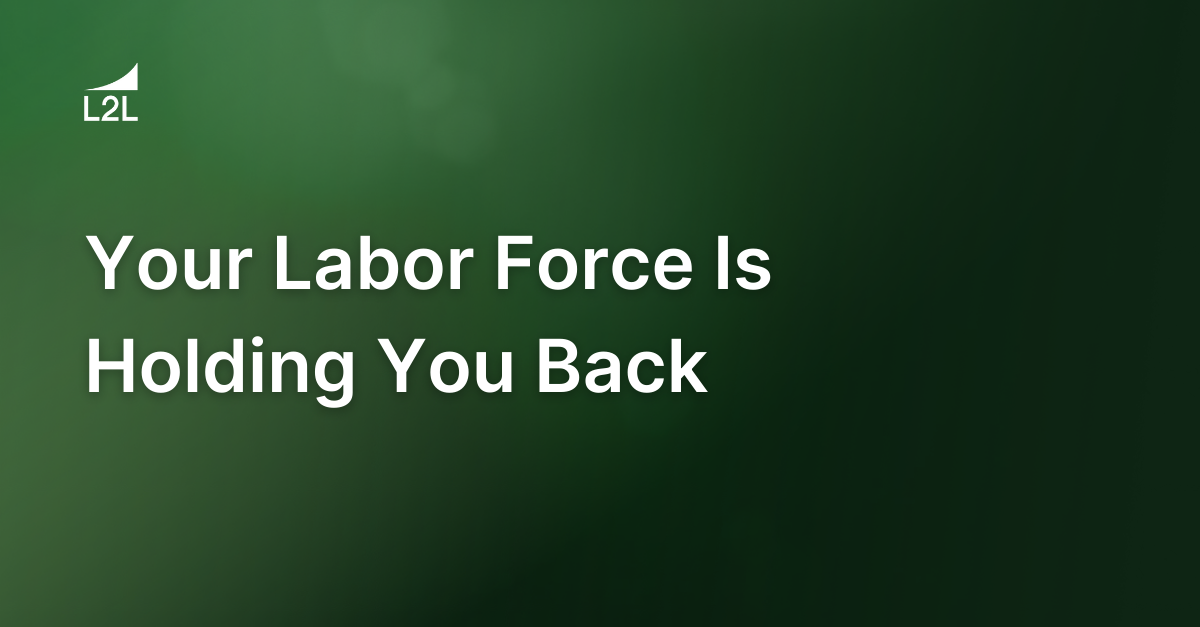
The manufacturing sector is at a critical juncture. Over the past two decades, we've witnessed a troubling trend: a consistent decline in labor availability. This trend is attributed to various factors, notably the "Silver Tsunami" — the wave of aging workers retiring from the industry — coupled with the younger generation's diminishing interest in manufacturing careers. The consequences of these shifts are palpable, manifesting as significant labor shortages and a widening skills gap. This directly threatens the industry’s growth and sustainability.
Understanding the manufacturing labor shortage and skills gap
L2L’s customers frequently express difficulties in two key areas:
-
Finding skilled candidates
-
Retaining workers long-term
As the average tenure of workers has dropped from over two decades to merely three years, the valuable "tribal knowledge" of manufacturing has been vanishing. This loss is profound, with many new employees lacking an understanding of lean manufacturing best practices.
In turn, this leads to a degradation of established processes. This scenario often results in a reversion to basic manufacturing practices on the shop floor — a significant step back for an industry that prides itself on standards and methodologies.
A recent chart from LNS Research and the U.S. Bureau of Labor Statistics underscores this issue, showing a flatline in labor productivity despite the introduction of Industry 4.0 technologies. These technologies, while advancing machine-related visibility, fail to address the fundamental labor issues that impact the backbone of manufacturing efficacy.
Productivity obstacles can involve people, processes, and technology. Source: LNS Research.
People as the change agents
Let’s face it: People are the change agents of manufacturing. Nothing changes unless a human conceives of an idea, rallies support from their team, and implements the idea. This is why labor is the key constraint in manufacturing today.
The exodus of skilled and knowledgeable workers leaves manufacturers with significant challenges when it comes to innovation. Newer workers may not have the key learnings and abilities to innovate, and they often lack the bandwidth to deliver effective change management to keep pace with industry competition. They require costly training and substantial work experience to rise to the standard set by the aging workforce they are replacing. This leaves the organization in a precarious position, where the very employees it relies on are holding back progress.
The call for change and the role of connected workforce platforms
The challenges highlighted at the LNS Industrial Transformation (IX) conference in 2023 illustrate a critical need for organizational restructuring and effective change management. Without addressing these fundamental gaps, manufacturers risk falling behind in an increasingly competitive market. Herein lies an opportunity for transformation through digital technology.
As the CTO here at L2L, I see immense potential in leveraging technology to bridge these gaps. For instance, connected frontline workforce (CFW) platforms like L2L enhance workers’ skills and abilities across maintenance, production, and quality assurance — functions that are crucial yet often overlooked by traditional systems like SCADA, Industrial Internet of Things (IIoT) platforms, and ERP systems. These CFW platforms also help companies maximize the value of their existing manufacturing software by unifying data and turning it into insights workers can take action on faster.
Here are the major ways connected workforce platforms help manufacturers combat the labor crisis:
-
Enhanced training and knowledge-sharing: Digital platforms can provide on-the-job training and critical information directly to the shop floor. This reduces the learning curve for new employees and helps preserve critical operational knowledge through digital means, mitigating the loss of tribal knowledge.
-
Improved retention through engagement: By involving workers in the digital landscape of the factory, employees feel more connected and valued. This engagement can lead to higher job satisfaction and, consequently, better retention rates.
-
Data-driven decision-making: With real-time data at their fingertips, workers can make informed decisions that align with best practices and proven methodologies, thus reducing the tendency to revert to base-level operations or unproven ad-hoc methods.
-
Safety incident prevention: Digitizing work instructions and training modules enables faster and better employee onboarding, which reduces the likelihood of new workers making mistakes and deviating from proper safety protocols.
Navigating future manufacturing labor challenges
Predictions by Gartner and Forrester indicate a rise in unionization and organized employee actions, which could present new challenges for productivity and innovation. However, these movements also push organizations to prioritize their workforce, creating opportunities to address grievances and innovate in labor management and workplace conditions. Using proven technology solutions to boost hiring and retention is a critical action manufacturers can take to create meaningful and impactful workplace improvements.
Solving the labor crisis starts with your workforce
The outlook for labor shortages in manufacturing may seem grim, but it is not insurmountable. As industry leaders, we must champion technologies that not only enhance productivity but also empower our workforce. By investing in digital tools like connected workforce platforms, we can extend the capabilities of our limited labor force, ensuring that our industry not only survives but thrives in the face of these challenges.
The path forward requires a concerted effort from all stakeholders in manufacturing. We must rethink our approach to workforce management, embrace technological aids, and foster a culture that attracts and retains talent. Only then can we overcome the labor challenges that loom large over our industry's future. Let's not just aim to fill the gap — let's bridge it entirely, creating a robust, resilient manufacturing sector for generations to come.
For a more in-depth look at how manufacturers can tackle labor challenges using people-centric technology, download our FREE eBook: The Manufacturing Leader's Guide to Attracting & Retailing Skilled Labor.
Revisions
Original version: 2 May 2024
Written by: Tyler Whitaker
Reviewed by: Daan Assen
Please read our editorial process for more information
Related Posts
Subscribe to Our Blog
We won't spam you, we promise. Only informative stuff about manufacturing, that's all.