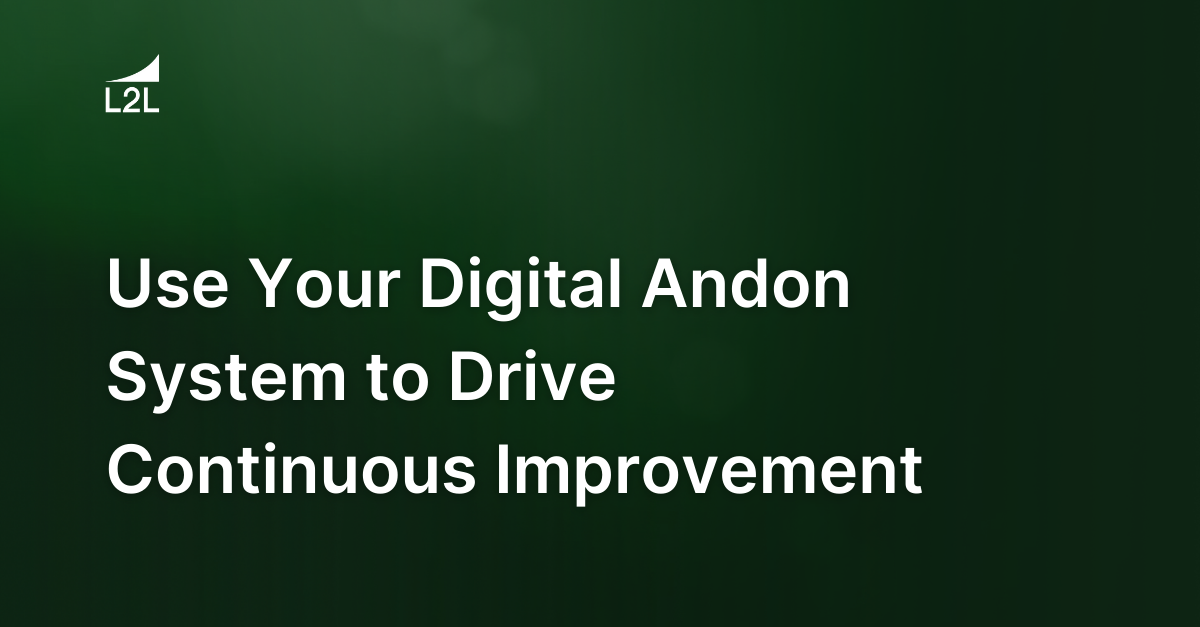
Have you ever looked out across the plant floor and wondered about all the blinking lights on the machines? What if a light is burned out somewhere in that blanket of blinking colors? You'll likely have a step on the PM checklists used by your maintenance team to look for burned-out lights and replace them as needed. But do you know what those lights represent? Do you react to the signals, or do you just use them as a reference because you're not quite sure?
The blinking lights, the horn sounds, and the buzzer noises can drive you mad if you don’t have a process in place to make sense of all those signals. If the folks on the shop floor don't immediately recognize and understand their meaning, they're little more than bells and whistles. That's right — we're talking about your andon system.
What Is an Andon System?
I think most people know that an andon system is used to alert people when a machine, process, or another element of the production flow needs something. It can indicate machine downtime, a material shortage, or that a quality issue.
What most people might not know is that an andon system can be triggered by both people and equipment. Operators can pull a cord or push a button. Machines and even processes can send a signal. But if you have no foundation in place to support the signal, then it's nothing more than noise.
The last thing most of us on the plant floor need is another system that will be quickly disregarded by the people who are supposed to pay attention. So, know what you want to accomplish with your andon system. Understand why it was introduced, where it comes from, and how to use it judiciously. Moreover, make sure all the teams who will be on the triggering and receiving ends of your andon system know and understand the objectives as well. Only create a system you can nurture and support for the long haul.
The word andon comes from a Japanese word meaning lamp or light. The term originated as part of the lean methodology of Jidoka, which means autonomation — or automation with a human touch. Applied to lean manufacturing, the andon system is a way to "stop and fix" issues and compel action.
Here's how it works:
-
The andon system signals problems (machine, material, quality, or safety issue)
-
The team is immediately aware of and can react to problems
-
The problem or potential concern is addressed and resolved
-
The quality of the product and the robustness of the process is ensured before the line resumes operation
If the methodology of "stop and fix" and maintaining a culture of continuous improvement are so important to the success of manufacturing, why, then, are these simple concepts so often ignored? Remember: the last thing people on the shop floor need is another "flavor of the day" dangled in front of them.
Have you ever heard these complaints before?
-
"No time to stop and fix: Just push the FRG (fault reset go) button and keep running."
-
"Here we go again: out of material. I sure hope I don’t have to work overtime because of this."
-
"This giant hunk of junk machine keeps jamming. I’m sick of this thing."
Your shop floor associates send your most important signals — so it's crucial that you design your andon system with them in mind.
An Andon System Case Study
I used to work at a factory where we wanted to institute an andon system in our facility. Our machines already had the Christmas tree lights on top of them, so we decided to use those to signal when equipment was down. The problem with our idea was that there were so many blinking lights all the time that nobody knew if the situation was real or not. Consequently, we decided that we needed to stick with one light tree on each line and use that as the signal that a machine was down on the line.
However, we seemed to forever run into the same issues, false or misleading signals. Someone would forget to shut off the light from an earlier incident, or a person wouldn't realize that they had just switched the light on, signaling a problem when there really wasn't one. It was like a non-stop version of crying wolf, no matter how unintentional.
Sure, this was really a management issue, but as one of the managers was famous for saying, "It's not your fault, it's just your problem." We our team, along with everyone else, to understand what we wanted to get out of the process. We had to build a standard procedure that was repeatable and easy to follow. We had to be transparent and clearly communicate how the process would work, what we wanted to achieve, and what our short and long-term goals were. Without a clear understanding and everyone on board, we were doomed to fail before we even got started.
We had to step back and ask, "What are the benefits of an andon system?"
-
Andon is a tool that helps reinforce the Jidoka philosophy to stop the line and fix the issue
-
Andon is a type of visual management system
-
Makes problems immediately visible in real time
-
The line and machine status is clearly visible to everyone on the floor
-
It creates transparency within the production process
-
Improves communication across disciplines and departments
-
Increases accountability of both the operators and the support teams responsible to address issues on the line
-
Highlights opportunities to kaizen for improvements
After thinking about the benefits of implementing a true andon system, we visualized a process for using out andon system to help production operators get the help they needed. We quickly realized that what we really wanted was a way to create an emergency response system in the plant — one that mirrored calling 911.
Using our andon system, all Production would have to do was put in a "call" (dispatch, work order, etc.) and provide necessary information. That call would immediately be directed to the correct support department responsible for responding to the issue. Whether that meant quality engineering, maintenance, or material runners, we had to cultivate a culture of responsiveness to problems. We desperately needed an easy way to break down silos between departments and work together to solve the problems.
We also needed an easier way to capture relevant data. With a more user-friendly vehicle to input information, we could quickly retrieve and analyze the data. Ideally, our andon system would give us a much clearer picture of our plant's recurring problems. Armed with accurate information, emotion is soon eradicated from the equation. If your teams have good data readily available to them, they will make good decisions.
The Power of an Andon System
Make waste visible, teach what waste looks like, and react to the uncovered waste to solve problems one by one. By solving problems and involving everyone — including operators, maintenance, and other support groups — you:
-
Raise the skill level of your people; no need for them to feel like they have to check their brains at the door
-
Improve the quality of your Kaizen events
-
Make your goal of a continuous improvement culture a reality
-
Embody "Safety First" — it is still first and foremost
It wasn’t easy, but a good lean execution system (LES) aided in our vision for andon and helped us solve our biggest problems — knocking them down one by one. And, just like in the old magazine articles from Outdoor Life: "This Happened to Me!"
Why You Need a Digital Andon System Now More Than Ever
Helping people recognize and respond to problems quickly has never been more critical. As leaders in manufacturing, we have a responsibility to safeguard our workers' safety and well-being. Remember when "phoning it in" was considered somehow lesser than? Not anymore.
With a robust yet simple-to-use andon system like L2L in your plant, people can truly see, react, and respond to any problem quickly and in real time. Not everyone needs to be physically present to grasp a shop floor situation. Between remote monitoring, timely updates, and the ability to assess events from anywhere, you and your teams have the tools they need to remedy the problem.
Learn how L2L's CloudDISPATCH Andon module can help you solve some of your biggest problems on the plant floor and avoid coming face to face with problems you've never seen before.
Revisions
Original version: 18 July 2024
Written by: Evelyn DuJack
Reviewed by: Daan Assen
Please read our editorial process for more information
Related Posts
Subscribe to Our Blog
We won't spam you, we promise. Only informative stuff about manufacturing, that's all.