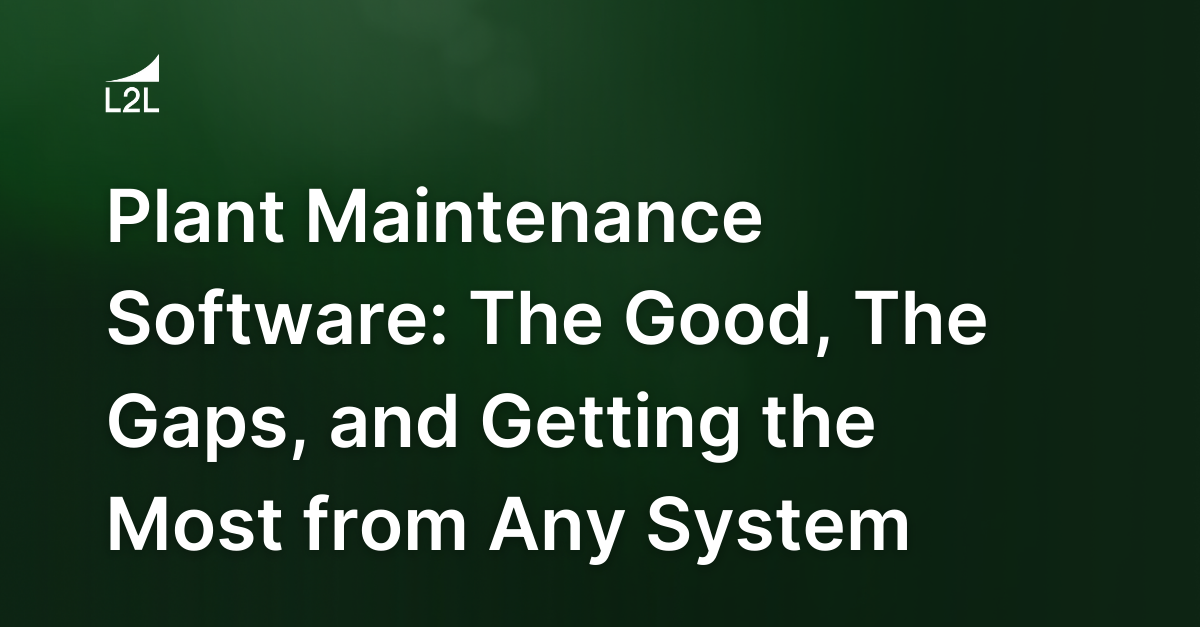
A key principle of modern manufacturing is to operate as efficiently as possible. This is often thought of in terms of specific operations, such as making more products with less raw material consumption or improving quality to minimize scrap and rework. While these are certainly valuable elements of operational efficiency, it's equally important, if not more so, to focus on support organizations. But to fully optimize operations, you need to find plant maintenance software that best suits your facility's needs.
How Maintenance Impacts Your Organization
How these supporting functions perform, with maintenance typically chief among them, is a critical indicator of operations' success. The assignments and responsibilities of these supporting functions often constitute the majority of downtime events affecting operations, whether planned or not.
The resulting need to minimize mechanic time on jobs and optimize execution has driven plant maintenance software to become a standard tool for best-in-class manufacturers.
How Does Plant Maintenance Software Help?
Plant maintenance software is used by an organization with physical assets or property to maintain maintenance operations records. Specifically, plant maintenance software can be used to monitor current asset status and document historical plant asset status via manual entry or integration with external systems or IoT-enabled devices. It can also capture information on activities performed. Some versions also include optional modules that can be applied to major project activities, such as the design and construction of new facilities.
Having real-time visibility into plant equipment status vastly improves a maintenance organization’s ability to respond quickly and minimize downtime. In addition, the ability to effectively manage activities allows for better planning and coordination of work that impacts production. However, the true value of plant maintenance software comes from accruing the data that forms asset histories and the details of each instance of work performed.
Through analysis, this aggregate information exposes waste and opportunities for improvement in current practices:
-
Lack of clarity in the job description and requirements
-
Lack of visibility to jobs available
-
Machine availability to perform work
-
Time spent looking for parts or tools
-
Time spent looking for information (manuals, instructions, and drawings)
-
Travel time to and from the job site
-
Lack of standard work for reactive maintenance
-
Moving resources between jobs and leaving jobs incomplete
Some of these issues may go unrecognized, while others well-known to maintenance veterans remain unaddressed.
The comprehensive information captured within plant maintenance software adds further value. Aside from highlighting process gaps impacting efficiency, the data also provides objective context around these gaps.
Correlating cost, man hours, and machine downtime metrics to each potential improvement enables prioritization and drives organizations to action.
Plant Maintenance Software vs CMMS
When discussing technology solutions for maintenance organizations, plant maintenance software may not be the most popular name in users’ lexicon. Most people are more familiar with “CMMS,” or computerized maintenance management systems (or software). Although seemingly interchangeable, there are some distinctions between them.
Traditionally, CMMS is a suite of functionalities that support end-user objectives of optimizing maintenance and asset management. These solutions include activities such as:
-
Administering preventive maintenance plans
-
Scheduling labor resources
-
Conducting maintenance and asset reporting
-
Managing contacts
-
Managing building estimates (depending on the CMMS)
Popular options for CMMS include Maximo, eMaint, Fiix, and L2L.
As CMMS constitutes a generalized set of uses, it's often broken down into subsets by application. Some of the more common solutions are:
-
Enterprise Asset Management (EAM), which is focused on physical assets like equipment or vehicles and is primarily used to extend asset life, manage asset status, and evaluate asset performance.
-
Computer-aided facility management centers on the maintenance of one or more facilities. This solution typically features maintenance management, property maintenance, personnel and equipment resource scheduling, and document storage for maps and blueprints.
-
Plant maintenance software may be referred to by the blanket term CMMS or as a subset of it. Since plant maintenance software is often used in production environment applications, which may have particular safety and maintenance requirements, an industry-specific plant maintenance software solution or module of a CMMS may be appropriate.
As plant maintenance software can be enveloped within a CMMS, these two products have several similarities:
Asset Management |
The ability to maintain an asset of any type through both preventive maintenance and status monitoring |
Work Order Management |
The ability to digitally administer work orders to automate the process of creating, planning, approving, and executing work requests on time |
Data Collection & Analysis |
The ability to collect, either via manual entry or IoT connectivity, data on asset status and performance to provide insight into maintenance metrics to identify common failure modes and develop corrective and preventive measures |
Proactive Approach |
The ability to transition from reactive work to planned preventive work through the collection and analysis of asset data |
Differences - Plant Maintenance Software vs CMMS
Reporting Functionality |
CMMS reporting functionality enables users to monitor relevant metrics and predict future performance based on historical and present data. |
Task Prioritization |
CMMS ensures the necessary inventory and labor resources are available to complete tasks or to order and stock components and schedule activities to ensure the required resources are available at the time of work. |
Design and Construction |
Some industry-specific plant maintenance software can support the design and construction of industrial facilities to maximize efficiency and ensure both safety and compliance requirements are satisfied, preventing future problems. |
Estimations Capability |
Some plant software includes an estimation module that predicts labor and material costs using real-time data so companies can plan accordingly to maintain budget adherence. |
What Doesn’t Plant Maintenance Software Do (And Why Does That Matter)?
From the above review of plant maintenance software and how it fits into the overall scheme of CMMS, it should be evident that deploying one or both systems can capture immense value for not only the maintenance support organizations but production overall. The ability to respond faster and more accurately to downtime events, better predict and avert machine failures, and more efficiently allocate resources to planned work leads to better asset availability and manufacturing throughput.
However, maintenance is only one piece of the puzzle of business success. Production remains the key to any manufacturing organization, bolstered by a slew of other support groups, such as training, engineering, and quality. Despite these teams’ common goal of assisting production, their disparate workflows, particularly manual ones, means there are as many systems and data repositories in use as there are departments. These systems become silos, making data and progress sharing difficult.
The Production-Focused Solution to Plant Maintenance Software
Fortunately, there's a solution to this challenge. The L2L Lean Execution System provides a single platform within which all departments’ workflows are represented: from plant maintenance and CMMS to production management, training, project management, and even lean tools. Each support group’s workflows are digitized, their data compiled into metrics, and reporting and analysis are executed within one easily accessible application.
By centralizing information across the plant, L2L enables cross-team communication and drives collaboration for significant operational improvement. To see how you can improve your plant maintenance and overall organizational performance, check out the L2L LES platform today!
Revisions
Original version: 18 July 2024
Written by: Evelyn DuJack
Reviewed by: Daan Assen
Please read our editorial process for more information
Related Posts
Subscribe to Our Blog
We won't spam you, we promise. Only informative stuff about manufacturing, that's all.