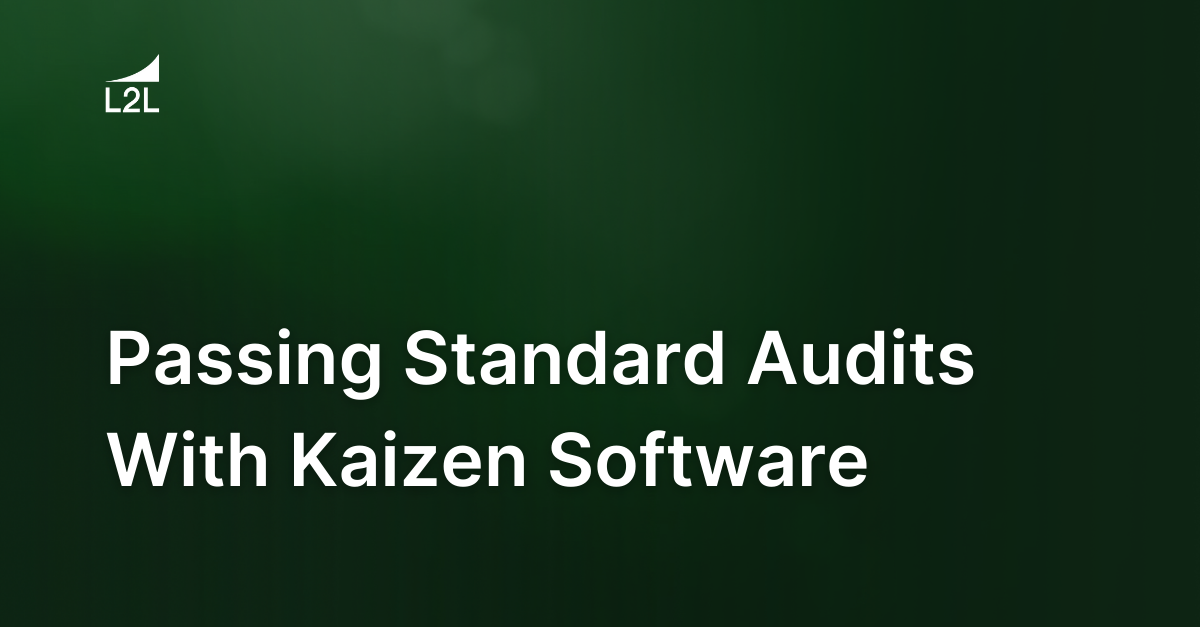
Whether it is ISO 12001 (International Organization of Standards), GFSI (Global Food Safety Initiative), or any of a number of other industry and business standards, one thing that has become common amongst all of these standards is that each requires some level of a Continuous Improvement program. And as any of us who have been through Audits of these standards know, the right, or wrong, Auditor can begin to dig and identify weaknesses in your processes, and those weaknesses are often based in documentation. More specifically, the lack of accurate, comprehensive documentation.
Kaizen Software
For many years, I have taught Kaizen improvement processes in all types of factories and businesses. From food technology to steel industries, and mining to paper producers, each entity having some form of standards for their organization or a required certification to live by. In every instance, I have found the Kaizen processes to be pretty much the same. With the same paper trail left behind when these improvement processes were 'complete'. This is where the trouble begins from an audit standpoint, and this is where a good Kaizen Software can make all of the difference.
Because each Kaizen Event, whether it's a large week long event, or a single individual improvement, generates documentation, creates tasks and follow-up items, it is sometimes difficult to keep all of this information ready and immediately available to produce should an Auditor ask to see it. This documentation is usually the responsibility of the trainer or the local leader to collect, store, catalog, and have prepared, meaning that it usually resides in a common shared drive or even a filing system (a nice word for cabinet), with actual paperwork and printed hard copies. A Kaizen Software feature, like the one found in L2L's Lean Execution System, puts all of these projects into a single location, immediately available thanks to software that can be readily accessed from any computer or mobile device. Additionally, a good Kaizen Software will also feature a standardized document library, where individual documents can be electronically attached and stored digitally, along with the Kaizen project itself. A good Kaizen Software will also allow the Auditor to see the team members involved in the process, pictures and videos for the project, as well as cost savings, all from the entries into the software.
Kaizen Software & Your Safety Program
In my experience, Auditors are not only looking for systems and processes that match the documented procedure, but they are also looking for consistent use of that process as proof the system is in use and not just a dog and pony show for the audit itself. This is accomplished because Kaizen events throughout the plant are all located in the Kaizen Software shared by everyone across the business.
Here's a real life example of an auditing nightmare. An industry leader, who shall remain nameless, had the misfortune of an accident occurring in their facility. In actuality, these folks were doing what they were supposed to be doing to ensure and maintain a safe work environment. Each day, every associate, both on and off the shop floor, would conduct a safety assessment of their immediate work area. These assessments were performed religiously, day in and day out. Plant floor associates, office personnel, guards, the nurse, accounting, purchasing, the safety manager, and custodial staff. You name any department. They did their due diligence. Every single day, including weekends and holidays. They dutifully executed their assignments.
Since no one ever wants to have a safety incident occur and no one wants to see anyone injured, they also used these daily work area assessments to Kaizen their overall safety program. And to their credit, they made great strides!
Then one day, the unthinkable happened. Someone was injured at work. Fortunately, the injury was not serious, but it could have very easily been far worse, potentially life threatening.
You know what happened next. The Auditors arrived (I warned you that this was a nightmare scenario). Since these folks had been doing what they said they would do, they had all the necessary documentation to back up the process they had put in place. Here's where the nightmare part really comes in to play, aside form the Auditors themselves. (shiver)
The Safety Manager now had to produce the documentation. Remember when I said every single person, every single day? For the sake of easy math, let's say they had 400 employees total. And let's say they only performed those audits five days a week over the six month period for which the Auditor wanted them to produce the proof. Each assessment requiring only one little piece of paper per company employee per day. Again, for the sake of easy math, let's say over those past six months, there were an average of twenty working days per month:
400 Employees x 5 pieces of paper x 120 days = 240,000 pieces of paper
Go ahead and catch your breath. I'll wait if you need to get a drink of water. That's right. Two hundred forty thousand pieces of paper. And where might those be? Under the Safety Manager's desk or in some filing cabinets? Sure, that's where some of those reams of paper were stored. However, the duplicate hard copies, you know, in case of a fire or flood, were stored offsite, in not one, but two separate locations. I think you get the gist. Once the paper round up was over, now the fun really began. Verifying data, signatures, etc. The number of man-hours required to prove adherence and compliance was staggering. Don't be those guys, bless their hearts.
Gone are the days of scrambling and hunting for documentation to prove to an auditor that you are actually performing your continuous improvement process tasks. Gone are the days of showing the link of processes and shop-floor usage. And gone are the days of searching through endless documents in a shared drive or box of paper to link all information to a single event. Because really good Kaizen Software like L2L's Lean Execution System provides all of this in one simple, single location.
If you liked this article, then check out: What is Kanaban Software?
Revisions
Original version: 18 July 2024
Written by: Evelyn DuJack
Reviewed by: Daan Assen
Please read our editorial process for more information
Related Posts
Subscribe to Our Blog
We won't spam you, we promise. Only informative stuff about manufacturing, that's all.