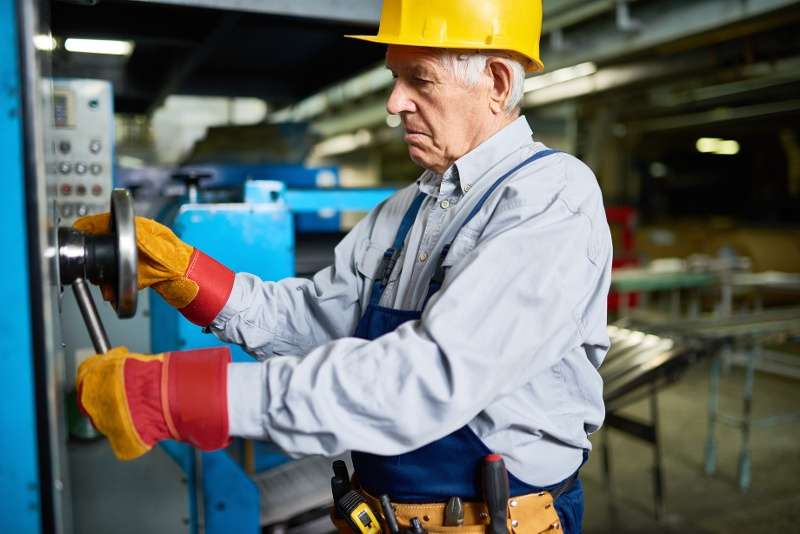
So, you want to add MES to your organization. That's great. You want to use it to drive operational improvements, right? You want to improve all the metrics that are measured and get lots of attention.
Here are just a few of our favorite red-headed stepchildren:
-
- Equipment performance issues. Limping along, down altogether. Putting out bad parts.
- Quality issues. Whether that means scrap, rework, or potential failure in the field. Failures in the field mean costly warranty work and unhappy customers.
- Late delivery. Not meeting delivery commitments leads to incurring unforecasted expedited shipping fees.
- Liquidated damages. Not meeting delivery schedules can also be very costly in terms of liquidated damages when you fail to satisfy contractual obligations. So, not only are your freight costs cutting into your margins, but you have unhappy customers to boot. Customers don't care why your product is late. It's your product, your reputation, and your responsibility. Maybe it's not your fault, but it's your problem.
- Material issues. Wrong materials, late materials, too much material on hand.
Will MES Solve Your Problems?
Will MES solve your problems? Well, that's really the question isn't it? What are your biggest problems? How do you identify which problems you need to solve? How do you know what problem should be addressed first?
The 5 heavy hitters listed above seem so obvious. Or are they? Everyone is quick to blame maintenance when things go wrong, whether the problems are at the beginning or at the end of the manufacturing or fabrication process.
It's easy to blame maintenance, isn't it? Plus, oftentimes the people from that department are not even in the meetings where they're getting all the blame. They have to fix 'their' machines. That's convenient, isn't it?
So, why always point the finger at maintenance and machines? Is it because that's easier than figuring out what your real problems really are? Is it because the squeaky wheel always gets the grease? The squeaky wheel who can make every day a nightmare. You know who I mean.
Complaining about them over and over doesn't make it true. We know. You just want them, the squeakers, to go away.
Think about it...maintenance and machines are not responsible for:
-
- Placing material orders
- Inspecting in-process and finished goods
- Hiring and training new employees
- Negotiating freight
Is it possible that Maintenance and Machines are not solely responsible for every single problem?
A Real World Scenario that MES Couldn't Solve
Here's a classic, real world example. Some of the details may vary, but you'll recognize the theme. (The names have been changed to protect, well, me.)
So, our friendly Purchasing Agent got a fantastic deal on Material 123. Let's refer to it as Exhibit A. It was such an amazing price, said Purchasing Agent got a great big fat bonus!
Unfortunately, there were some defects in Exhibit A that were hard to detect. It jammed some equipment and caused an accident (no one was seriously injured) before the issue was discovered. Certainly the supplier could not have been aware of these defects or would never have shipped the product. (Insert shocked expression on my face here.)
Well, the show must go on, so a generous sized band-aid was applied: A combination of throwing a whole bunch of bodies working a whole bunch of overtime, some WD-40, and applying a little duct tape. Build it, stamp it, mark it with an "A", and ship it!
And then, the band-aided product failed in the field.
And then, the department manager had to send one of her best employees and another associate to the customer location to rework the product.
And then, the department manager got called to the boss's office because now they didn't have enough employees with the training and experience to resolve the issues that still had to be dealt with in the plant.
Note: this wasn't a maintenance and machines issue.
It would be fantastic if all problems in your plant or on your shop floor involved only machines. An MES might be able to solve that. That's a wrap. We're done here. If that were the case, this would be easy. All you'd have to do is optimize all your machines. No more downtime forever. The end. And they all lived happily ever after.
Unfortunately, that's not the reality. And deep in your heart of hearts, or maybe just in your gut, you know that's not reality.
Is MES Right For You?
Many companies who have wrapped their arms around their problems have come to realize that, although they have machine downtime issues, there are often even more costly issues that are hidden: issues related to training, materials, quality, scrap, product deviations. These are all problems that equipment-centric MES leaves unaddressed. An MES system can be a great addition. But it can't do it all. And it can't do it all by itself.
If tracking and logging your problems and controlling your equipment processes are your biggest issues, then, yes, MES should be part of your solution.
Taking care of only machine and down time issues will not address problems with efficiency. Those problems require something more than a standalone MES. An MES (Manufacturing Execution System) will give you some pointers.
No MES by itself can help you with efficiency deficiencies in these areas: people materials, products, planning. For these, you need something more. You need a complementary system. You need Leading2Lean. Integrate L2L with your MES and you will be much happier with the results, and much further ahead than where you started.
Learn more about how L2L can enhance your MES when you download our free guide!
Revisions
Original version: 16 March 2020
Written by: Cara Winther
Reviewed by: Daan Assen
Please read our editorial process for more information
Related Posts
Subscribe to Our Blog
We won't spam you, we promise. Only informative stuff about manufacturing, that's all.