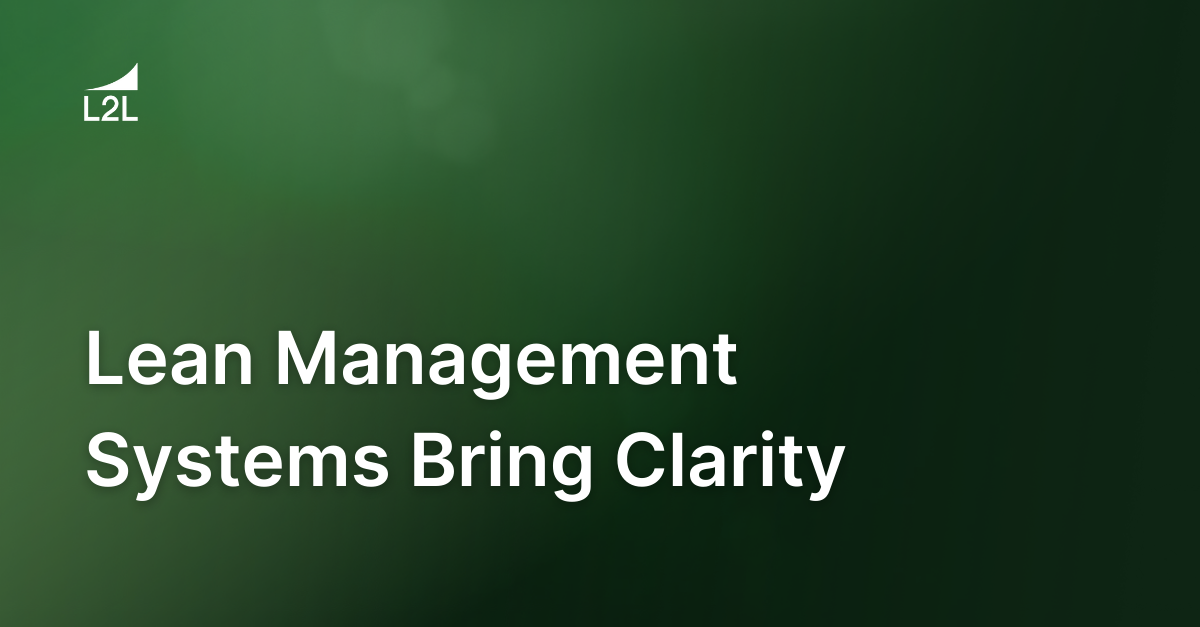
In the digital world we live in today we would never ask or expect our Law Enforcement Groups to perform their duties without using or taking full advantage of all the modern tools available today (i.e., cameras, radios, phones, computers, databases, etc). Without these modern tools I would suspect they would almost feel handcuffed, not capable of efficiently performing their jobs and duties to their full potential.
These digital tools used daily around the world in all Law Enforcement settings are powerful and can bring objectivity and transparency to difficult situations. They can remove much of the guesswork and emotion out of determining what happened and what action to take next, allowing for quicker resolution.
The True Value of a Lean Management System
An effective Lean Management System is as valuable for manufacturing as these digital tools are for an effective and efficient law enforcement agency.
My comparison of how relevant these modern tools such as video footage can be to law enforcement, and the importance of a Digital Lean Manufacturing System in our manufacturing sites rings true to me because I have lived it.
As a Process Engineer for many years in the automotive industry I found it can be critical if not catastrophic if/when issues arise. It's an environment of enormous pressure to solve costly problems. In this environment it's imperative you determine the correct causes of problems in order to eliminate future recurrences, and time is of the essence during these critical moments. You can't wait to collect and compile tons of information or data. Or continue to make further emotion-based decisions.
Decisions and subsequent actions need to be quick and accurate when resources are lean.
Using a Lean Management System allows the user to confidently and objectively define and prioritize these events and problems. Of equal or greater importance is using a Lean Management System to continue to monitor and verify the effectiveness of the implemented changes or ensuring the root causes of problems are solved.
A Lean Management System Case Study
I have been a part of many situations in the past where I have learned firsthand the importance of good data. Good data and traceability turns a very subjective quality event into a solvable situation.
One event I recall took place in our shipping area where we sent flawed products to a customer unknowingly (This didn't happen often, but on occasion it does). When the customer attempted to use the product, they identified a poor quality condition.
In this specific instance, ultimately the flawed Products were traced back to specific sequences of when defects had been identified and rejected at the machine during the normal scheduled shift.
All Known Customer Returns had been identified to be manufactured around each instance of a First Time Quality Reject. All Customer Returns had been identified and associated with a previously cycled scrap record. The team found when the known reject part was cycled, a new additional failure mode was created and introduced the very next cycle, resulting in shipping no-good product.
By reviewing our Lean Management System's Pitch Board Data and understanding when the Scrap Reject was identified, the team was able to review these specific lots and time frames to quickly identify suspect products.
The game changer with all of these events I have been a part of is using the real-time data available in your Lean Management System. As minimal or irrelevant some data points may seem, they all collectively tell you a story. The data does not lie, even if you don't understand its story at the time.
Ultimately in this instance the past Pitch Board Data/Scrap results narrowed the scope of work and were able to direct the team to all associated NO Good Products. Additionally the Pitch Board Data directed the team to the originating instance of when the defects first started based upon the scrap records documented within the Lean Management System. By reviewing the Pitch Board data including scrap inputs over the previous shifts this allowed the Team to have an objective method in identifying all potential defects manufactured and potentially shipped.
Revisions
Original version: 18 July 2024
Written by: Evelyn DuJack
Reviewed by: Daan Assen
Please read our editorial process for more information
Related Posts
Subscribe to Our Blog
We won't spam you, we promise. Only informative stuff about manufacturing, that's all.