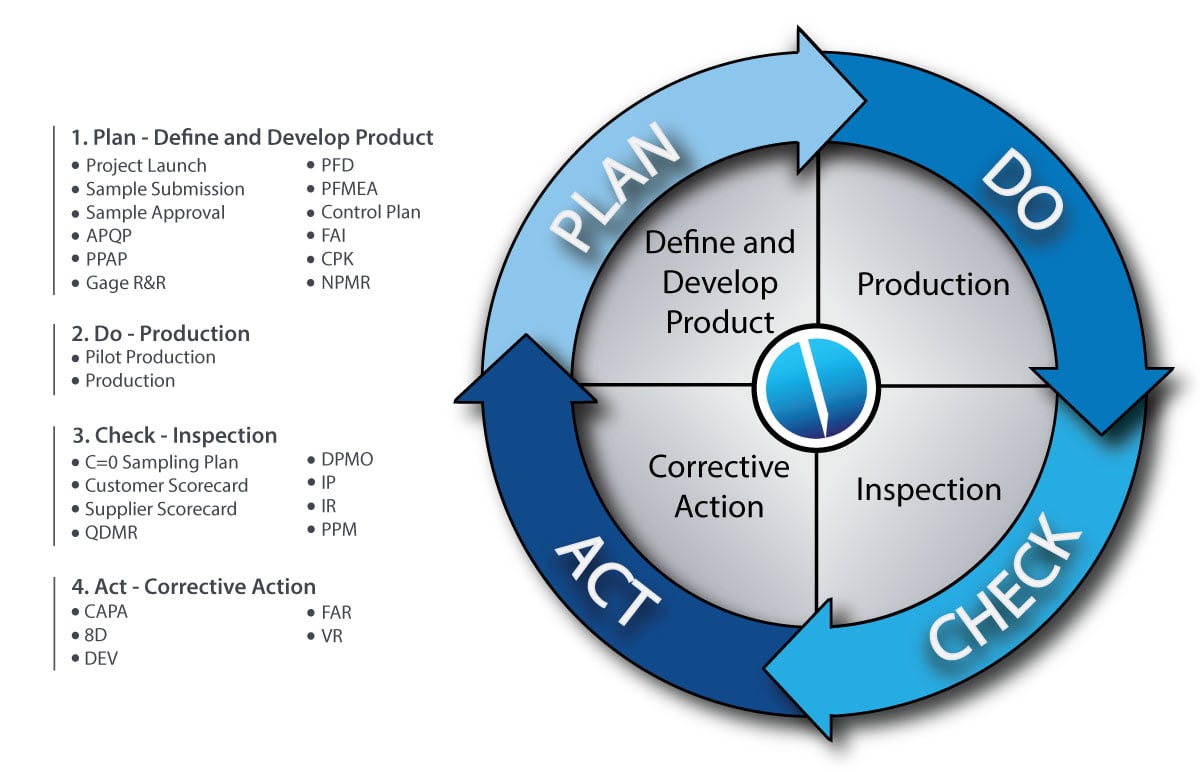
In recent years, the manufacturing sector has been swept up in the wave of Industry 4.0, a revolutionary movement that promises to meld physical production and operations with smart digital technology, machine learning, and big data. The goal of this movement is to create a more holistic and better-connected process for industrial companies.
Industry 4.0 has been hailed as the future of manufacturing, offering the potential for significantly increased productivity, efficiency, and flexibility, there’s a growing concern that its implementation is faltering. However, a closer examination suggests that this may be largely because companies have neglected a fundamental principle that has always been at the heart of manufacturing excellence: continuous improvement.
Understanding Industry 4.0
To fully grasp the challenges, it's important to understand what Industry 4.0 entails. It represents the fourth industrial revolution, characterized by the integration of digital technologies like the Internet of Things (IoT), artificial intelligence (AI), robotics, and cloud computing into manufacturing processes. This movement aims to create smart factories where machinery and equipment can improve processes through automation and self-optimization. The potential benefits are enormous, offering to reduce operational costs, improve product quality, and increase manufacturing flexibility.
Continuous improvement: The forgotten core
As companies race to adopt these new technologies, many are making a critical oversight: forgetting the importance of continuous improvement.
Continuous improvement, a concept deeply embedded in methodologies like Lean Manufacturing, The Toyota Production System, Total Productive Maintenance, and Six Sigma, is about constantly seeking ways to reduce waste, enhance efficiency, and increase productivity. It involves not just technological upgrades but a culture of improvement that engages every employee in the quest for better methods, processes, and results.
Why continuous improvement matters in Industry 4.0
Ignoring continuous improvement as you implement Industry 4.0 initiatives is a significant misstep for several reasons:
-
Over-reliance on technology: Simply installing state-of-the-art technology does not automatically translate to improved performance. Knowing how to use the technology to achieve production and business goals is crucial.
-
No continuous improvement mindset: Without a mindset geared towards continuous improvement, companies might not fully utilize these technologies' potential or use them in ways that do not align with their strategic goals.
-
Ignoring human elements: Continuous improvement recognizes the value of human insight and innovation. Industry 4.0’s focus on technology can sometimes lead to undervaluing the role of human creativity and problem-solving, which are crucial for identifying inefficiencies and brainstorming solutions.
-
Lack of adaptability: The absence of a continuous improvement culture can make organizations rigid and slow to adapt. In a rapidly changing market, the ability to quickly identify areas for improvement and implement changes is vital for staying competitive.
Examples of the Industry 4.0 disconnect
There are numerous instances of companies investing heavily in Industry 4.0 technologies without seeing the anticipated benefits. For example, a manufacturing firm might install sensors and AI-driven analytics for predictive maintenance but fail to achieve the expected reduction in downtime because the organization hasn’t cultivated a culture that prioritizes regular process evaluations and adjustments based on data insights. Additionally, a 2020 study by McKinsey found that less than one-third of organizations surveyed were able to move beyond their automation pilot phases.
In contrast, companies that combine technology investments with a strong emphasis on continuous improvement often see more substantial and sustained gains.
Bridging the gap: Modernization vs continuous improvement
To harness the full potential of Industry 4.0, companies must bridge this gap between manufacturing modernization and continuous improvement by:
-
Fostering a culture of continuous improvement: Organizations should promote a culture where every employee is encouraged and empowered to suggest improvements. This includes training staff not only on how to use new technologies but also on the principles of Lean and Six Sigma.
-
Integrating technology with continuous improvement: Technology should be viewed as a tool to facilitate continuous improvement, not as a replacement for it. This means leveraging data and analytics to identify areas for improvement and measure the impact of changes.
-
Emphasizing leadership and vision: Leadership plays a crucial role in merging the goals of Industry 4.0 with continuous improvement. Leaders must articulate a clear vision that encompasses both technological advancement and the ongoing pursuit of operational excellence.
-
Implementing a systematic approach to improvement: Adopting systematic methodologies for continuous improvement, such as PDCA (Plan-Do-Check-Act), can help ensure that efforts to leverage Industry 4.0 technologies are focused, measured, and aligned with the company’s strategic objectives.
Plan-Do-Check-Act frameworks help manufacturers streamline Industry 4.0 initiatives. Source.
Looking ahead
The journey towards Industry 4.0 represents a significant opportunity for the manufacturing sector. However, its promise can only be fully realized if companies remember the importance of continuous improvement. By integrating advanced technologies with a steadfast commitment to optimizing every aspect of the manufacturing process, companies can avoid the pitfalls of a purely tech-centric approach.
The future of manufacturing lies not just in the machines that populate the factory floor but in the ongoing efforts to make those machines—and the processes they are part of—better every day.
How well is your organization balancing technological evolution with continuous improvement? Find out in as little as 5 minutes with L2L’s FREE Smart Manufacturing Scorecard.
Revisions
Original version: 2 April 2024
Written by: Evelyn DuJack
Reviewed by: Daan Assen
Please read our editorial process for more information
Related Posts
Subscribe to Our Blog
We won't spam you, we promise. Only informative stuff about manufacturing, that's all.