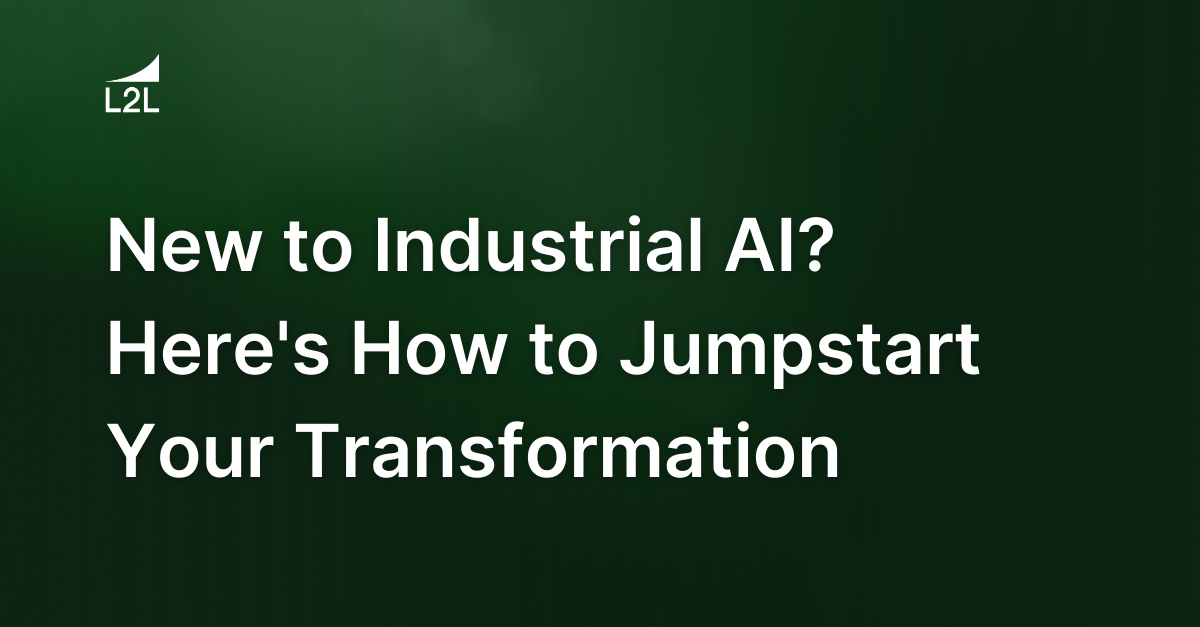
Artificial intelligence (AI) is one of the most disruptive technologies history has witnessed. Its transformative impact is reshaping nearly every major industry, driving unprecedented productivity, efficiency, quality, and even cost savings. Despite this AI revolution, the manufacturing sector has been slow to integrate AI technology into factory operations.
Barriers to AI adoption in manufacturing
Manufacturing’s reluctance to infuse factory processes with intelligent technology isn’t necessarily the product of suspicion. While AI, like any technology, poses risks if used improperly, the main barriers to industrial AI adoption include budgetary constraints, limited internal expertise, and a lack of universal industrial data. In other words, manufacturers don’t have the quantity and quality of data needed to train AI models to scale industrial applications.
However, these challenges shouldn’t stop manufacturers from getting started with AI today. In fact, many industrial companies are already using AI to unlock value on the shop floor. Use cases like AI-driven predictive maintenance, visual inspection systems, and intelligent supply chain optimization are becoming increasingly common among industry leaders — and they’re paying off.
The time to embrace industrial AI is now. Here’s how you can hit the ground running — with minimal risk.
Industrial AI transformation: 5 steps for success
Most manufacturers see AI as crucial for future success. In a recent survey of 300 manufacturing leaders currently using AI, 64 percent said they were only in the research and experimentation phase, and 35 percent reported using AI in production. Although many respondents planned to increase AI spending in the next two years, those who have yet to use AI in production are progressing slowly. This is largely due to challenges with the data, talent, and skills constraints mentioned above.
Industrial AI requires human intelligence, machine learning, and strategic systems. Source.
How can manufacturers ensure a smooth, timely AI implementation on the production floor that solves both short and long-term problems? Here are five steps industrial leaders can take to make the most of their AI investments.
1. Identify the problems you want to solve with AI
Start by identifying the production problems you want to solve. Is your proactive maintenance strategy less effective than you hoped? Is your quality assurance team short-staffed and therefore slower at addressing component defects? Are you struggling to maintain optimal inventory levels? It’s crucial that you gather data on what is and isn’t working across all of your manufacturing processes. Once you set clear objectives, it’s time to determine where AI technologies can help.
2. Put together the right team
Implementing AI requires a mix of skills. From data scientists and AI specialists to domain experts who understand your manufacturing processes in-depth, you need to assemble a team that can help bridge the AI knowledge gaps in your organization.
If your current team lacks AI expertise, consider hiring new talent or seeking the expertise of external partners like AI consultants or technology vendors. An interdisciplinary team will be crucial for developing and deploying effective AI solutions.
3. Prepare your data
The backbone of any successful AI initiative in manufacturing is good data. In fact, nearly 57 percent of manufacturers say poor data quality is a barrier to AI implementation. Here's what you need to focus on:
-
Data collection: Ensure that you are collecting the right data. This includes data from machines, production lines, quality control, and even environmental data from the factory floor.
-
Data quality: Your data must be accurate, complete, and consistent. Invest time in cleaning your data, dealing with missing values, and removing inaccuracies in your data sets.
-
Data integration: AI systems require integrated data that provides a comprehensive view of your operations. This might involve integrating data from various sources such as ERP systems, Manufacturing Execution Systems (MES), Computerized Manufacturing Maintenance Systems (CMMS), and IoT devices.
You can’t accelerate, let alone scale, AI initiatives without a solid data foundation. Manufacturing technologies like connected workforce platforms are especially useful in helping you prepare for AI by quickly gathering and processing data from machines and systems. This makes it much easier to build data sets that help AI “learn” your manufacturing processes.
4. Choose the right tools and technologies
Once you’ve identified potential AI use cases and ensured your data infrastructure is suitable for AI, it’s time to select the tools and technologies that best support your AI projects. Options range from machine learning models that can predict equipment failures to computer vision systems that inspect product quality. Depending on your objectives, the complexity of AI solutions can vary significantly.
Start with pilot projects that can scale. Connected workforce platforms like L2L offer out-of-the-box intelligent capabilities that learn and adapt to dynamic shop floor processes and require weeks, not months, to set up.
5. Test, train, and optimize
Before committing to new AI projects, it’s crucial to understand how they do — and don’t — work on a small scale and without disrupting production. The length of AI pilot phases varies based on the individual solution, but testing periods should give you a thorough understanding of the solution’s strengths and limitations.
Training your workforce to understand and work alongside AI is essential before a large-scale roll-out. Focus on change management strategies to address any apprehension or resistance. Educate your employees about AI’s benefits and involve them in the development process to make the transition smoother. In fact, they may suggest ways to optimize AI for real-world manufacturing scenarios.
Accelerate your AI transformation with connected workforce technology
If your competitors aren’t already using AI in production processes, they’re most likely piloting AI use cases. Early adopters gain a competitive edge through improved efficiency, productivity, and adaptability. By starting your AI journey today, you’re taking a step towards future-proofing your business, ensuring it’s ready to meet future challenges and opportunities head-on.
Remember that your readiness for AI depends on the quality of your data. L2L’s Connected Workforce Platform makes it easy for manufacturers to collect and visualize valuable, actionable data from their operations. But our platform also features built-in AI capabilities like predictive analytics and intelligent guidance, ensuring that employees always have the insights they need to do their best work.
For more information about how L2L can help you kickstart your AI journey, reach out to sales@l2l.com, or see our platform in action for yourself with our Interactive Product Tour.
Revisions
Original version: 1 May 2024
Written by: Evelyn DuJack
Reviewed by: Daan Assen
Please read our editorial process for more information
Related Posts
Subscribe to Our Blog
We won't spam you, we promise. Only informative stuff about manufacturing, that's all.