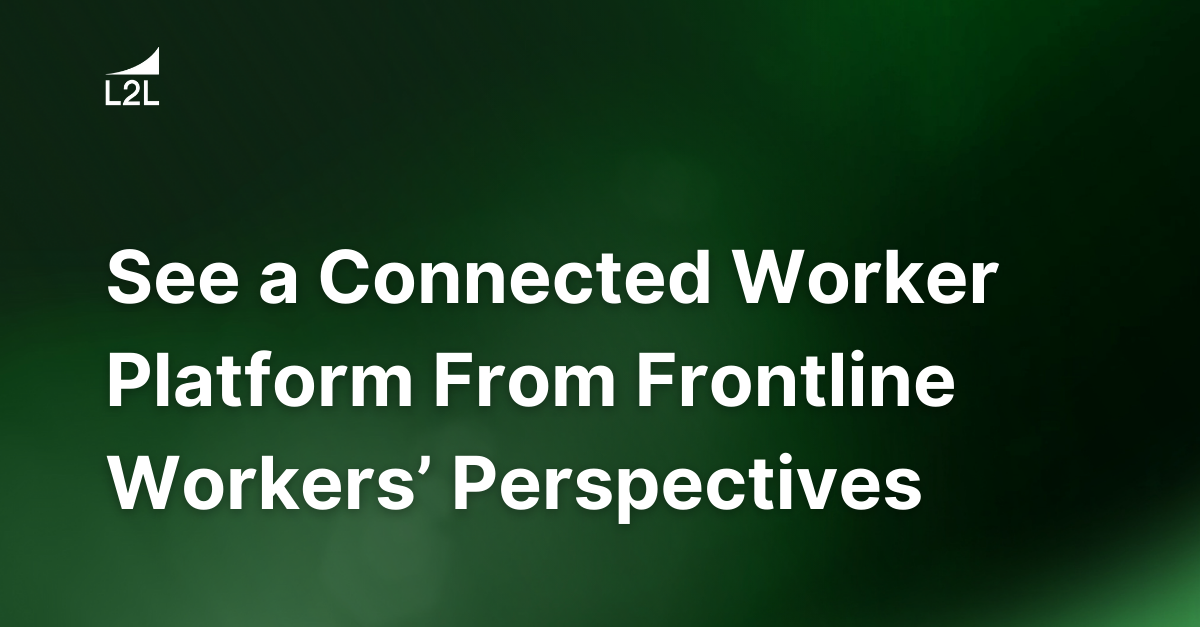
Estimated read time: 8 minutes
Have you ever thought that the world would be a better place if we all got out of our own heads once in a while? Turns out the same is true in the manufacturing industry — especially when it comes to the connected worker approach.
That’s because workers are at the heart of any connected worker solution. (It’s right there in the name, after all.) While no single member of your workforce is calling the shots, they’re the ones who will be most impacted by this change — which means their thoughts are particularly valuable when you’re making decisions about tech solutions like a connected worker platform. That’s especially true when it comes to any employee who works on the assembly line or with machinery.
That’s why we’re taking a walk in workers’ shoes. No matter what role you play in your manufacturing operation, hang up your hat, because you’re now a factory employee. Let’s see what connected worker platforms look like from this perspective!
What is a connected worker platform?
The first thing to understand about connected work from an employee perspective is that some people might not know what it even means right away. You, a factory worker, need a chance to brush up on key terms before you can formulate any opinions on this solution.
Here’s your quick guide:
- Frontline worker: Also called “operators” or even "production associates" a frontline worker is generally an hourly employee who performs tasks on the assembly line. Think of them as being on the front lines of your manufacturing operation.
- Connected worker: A connected worker is any employee in your manufacturing business who is truly “connected.” That means they have instant access to the systems, data and digital processes that are most important to their tasks. Although a connected worker can have any role in your operation, you’re a frontline worker today.
- Connected worker technology: This is an umbrella term referring to the modern digital tools that connect workers to one another and your internal systems. It can include tablets, smartphones, wearable devices, augmented reality and other smart factory solutions.
- Connected worker platform: Speaking of software, a connected worker platform is what brings all these technologies together in one place. It’s the basis for the entire connected worker solution.
How users see a connected worker platform
Now that you know the ropes, it’s time to take a closer look at connected worker platforms from your fresh new perspective. Here are a few things you’d notice about this solution:
There’s only one system to learn
When it comes to productivity, there’s nothing more irritating than having to bounce back and forth between different systems for a single work process. Luckily, as a connected worker, you don’t have that problem. Instead, you have access to a single connected worker platform with a simple, user-friendly interface. With only one system to navigate, you and all the other factory workers are free to focus on tasks that really matter.
You can quickly capture and view data
A connected worker platform gives you all the tools you need to take control of manufacturing data. The system automatically captures and displays the information you need when you need it — and when you enter data manually, you can do so with a smart device like a phone or tablet so you don’t have to interrupt your work.
Teams are more cooperative
Connected work helps you cooperate more effectively with other parts of the workforce, like the maintenance team. For example, when you enter data, the system can automatically flag a problem and send a notification to maintenance. They can quickly respond and let you know what to expect so you can plan your own tasks around any repairs or downtime.
Downtime and other disruptions are reduced
In many ways, connected worker platforms keep people on the same page. Maybe you’re a new employee and you’ve got a question about a task. Lucky for you, it’s easy to access digital work instructions informed by long-time members of the workforce — which means you don’t have to create downtime by asking questions.
But that’s not the only kind of disruption that can be reduced by connected worker technology. As a frontline worker, you’ll have vital manufacturing data at your fingertips at all times, allowing you to anticipate and navigate interruptions of all kinds. Even issues you can’t avoid, like supply chain disruptions, are easier to handle when you can see them coming.
Processes are improved
Better processes are good news for the entire plant, but they’re possibly even better for the frontline workforce. That’s because employees like you can use tech tools to support productivity in simple ways, like automating tasks or working together to solve problems. Most importantly, smarter processes lead to improved worker safety, higher morale and more.
You can try new tech
As a frontline employee, you’re probably excited to get your hands on technology that can make your job easier. With a connected worker platform, you’ll always be able to integrate new tech into your existing approach — all because your technology is connected to you and you’re connected to the manufacturing system.
You’re free to share improvements
Thanks to a little concept called yokoten, a Japanese word that roughly translates to “sharing sideways,” connected worker platforms allow the entire workforce to share productivity and operation improvements. If you find a better way to collect a certain piece of data, perform a task or work with a machine, you can share it across the entire organization to help everyone improve.
Your workplace is more efficient and accessible
Sure, a connected worker platform improves intricate things like safety, productivity and operational efficiency — but it does all that by simply making work easier. When connected technology makes it easy to access and utilize tools, processes and even work instructions, you can perform better, make fewer mistakes, expand your skill set and become a valuable contributor to the supply chain. Plus, an accessible, connected workplace means workers with different abilities and backgrounds can cooperate to achieve more than they could individually.
Other benefits of a connected worker platform
As a connected worker on the front lines, you have a critical role to play in the utilization of a connected worker platform. However, you’re not the only piece of the puzzle. Take off those frontline worker shoes and put on your CEO hat, because we’re zooming out to see how connected work benefits the whole manufacturing operation:
Reduced costs
Without a connected worker platform, you’d be left trying to put disjointed, dissimilar and often incompatible technologies together. That can quickly get expensive — not to mention all the cost savings you’d be missing out on.
Luckily, connected worker platforms address these problems. That’s because all your tech tools and smart factory solutions can be integrated into one streamlined touchpoint, reducing the need for expensive, piecemeal approaches. Plus, when your workforce can share data and insights in real-time, it’s easier to avoid potentially pricey mistakes.
Less human error
Speaking of mistakes, let’s take a look at human error. It’s understandable and inevitable — but with a connected worker platform, everyday missteps don’t have to eat away at productivity. Instead, connected workers can quickly and easily identify where they went wrong and what the appropriate solution is, all by glancing at a mobile device or checking process data.
Improved organizational agility
When your workforce is connected, your entire manufacturing operation can move with more agility. That’s because everyone is on the same page about improvements, changes, supply chain considerations and more, allowing you to rapidly course-correct if an obstacle shows up on your radar. You also have the freedom to more quickly adapt to industry updates like new technology or approaches — just integrate it into your connected worker platform and keep going.
Stronger competitive edge
At the end of the day, connected worker platforms help you and your workforce achieve continuous improvement and operational excellence. Every frontline employee has the data they need right when they need it, every maintenance worker knows exactly what’s causing an issue and how to fix it, every IT team member can quickly respond to system issues — all because a connected worker platform took natural skill sets and enhanced them with smart technology. Can your competitors even dream of keeping up?
Put a connected worker platform to work for you
Now that you’ve seen connected worker platforms from different angles, it’s time to look at this solution from one last perspective: your own.
Connected work is a big deal, and it’s only becoming more important as supply chain disruptions and growing customer demands put more pressure on manufacturers. No matter what role you play in your operation, you can’t afford to let this opportunity slip away; after all, it’s difficult to catch up on digital solutions once you’ve missed your window.
Luckily, you probably already have some of the most important ingredients — like dedicated frontline workers and mobile technology. Now all you need is a connected worker platform to bring it all together.
If you’re ready to see what a connected worker solution looks like from your perspective, now’s your chance. Request a demo of L2L’s Smart Manufacturing and Connected Worker Platform today!
Revisions
Original version: 22 July 2022
Written by: L2L
Reviewed by: Daan Assen
Please read our editorial process for more information
Related Posts
Subscribe to Our Blog
We won't spam you, we promise. Only informative stuff about manufacturing, that's all.