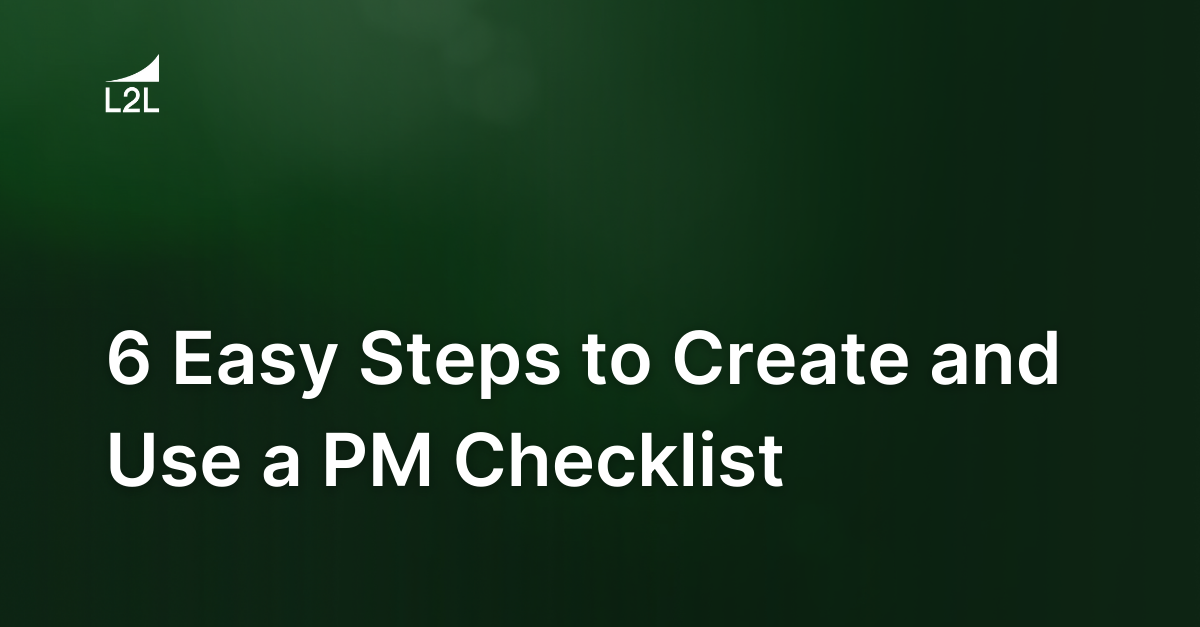
Creating and using a PM Checklist in 6 easy steps:
- Put together a team and come up with a plan.
- Have the Team establish Goals.
- Collect information on existing equipment.
- Decide which asset(s) to start with first.
- Create the PM checklist.
- Create a schedule for your Preventative Maintenance and include the PM Checklist.
The Cloud and Your PM Checklist
First, let’s cover the boring but important stuff! You’re going to want your documents to be available in the cloud. If you’ve been working in manufacturing for 30-40 years, the ‘Cloud’ is likely new and unfamiliar territory to you. Have no fear. ‘Cloud’ is just another word for the internet and it means no more paper copies, and no more waiting for your computer to load because you’ve used up the storage on your hard drive.
The Cloud allows a single document to be attached to multiple events and is accessible by all necessary parties across the world. We offer a single source document revision where the current revision is always present. No more taping up documents for ISO Standards that are all too soon out of compliance because they are outdated. You can’t talk about the Cloud without talking about security and privacy. At L2L, we've taken every step to ensure our customers’ data is completely secure. You know your data is protected and always available.
Some features and functionality to look for: L2L is a Full Intelligent Document Control Center with security settings specific to publishers, approvers, admins, etc. You can assign people to approve documents before they can be published. Setting up categories is an easy and convenient way to keep track of documents that pertain to certain processes. For example, you can set up categories for Safety, Training, Continuous Improvement, Preventive Maintenance, etc. L2L also has the capability of putting a document in front of an Operator working on a production line in the form of Production Standard Work. The Standard Work will launch at specified intervals that you determine.
L2L gives you the ability to attach documents to events specific to areas, lines, machines, and even Dispatch Types. You can share a document across other sister company sites on your server. For a PM Checklist, you’ll want to attach the document directly to a scheduled event.
A PM Checklist in L2L has the capability to launch a Dispatch on reject limits or yes/no questions. The Dispatch can be directed to the trade specific to the task that was out of spec or answered yes/no. You’ll also want to add images or videos, so that your technicians have a visual of how a task is performed or how an asset should look. This creates a closed loop process to ensure that identified abnormalities get resolved immediately.
Let's get started:
Put together a team and come up with a plan
Who should be on the team? Often the PM Coordinator or Maintenance Planner gets the brunt of owning the process. But should they be the only ones involved? Probably not. Depending on which area of the facility are you focused on? Facilities, Molding, Packaging. Now, pick people who actually perform the work, as well as supervisors, team leaders, and other staff who are knowledgeable about the processes and assets in the facility. Thinking through what needs to be done and what machines cause the most trouble is the first step in putting together a PM Checklist. How do the techs address the problem when they first arrive at a machine? Do they all tackle the same tasks first? Those items will be the first tasks on your PM Checklist.
Have the Team establish Goals
The goal of a PM Checklist is to improve the reliability of the plant. Not to just do more PMs. So, now that you know what tasks need to be performed, and you’ll undoubtedly add more over time, but what is your endgame? Continue to use the PM Checklist over a decided upon timeframe and then review the outcomes with your team. Look at the decrease in downtime and interruptions to production. Is your PM Checklist working? Continue to set goals that drive improvement to your processes. That could be as simple as adding pictures or videos to your checklist tasks. Maybe the PM Checklist tasks need to be performed more or less frequently. Use breakdown data and Pareto analysis to fine tune your PM tasks to ensure that the proactive work you are performing is delivering the results you plan to achieve.
Collect information on existing equipment
You’ll want to know where you started to see the changes that occur after implementing your PM Checklist. Get a baseline on KPIs you want to measure. What is the cost of spares for this particular machine annually? How much downtime has accrued? How much time does a technician spend fixing this particular machine? How much does each hour of downtime cost your facility? You’ll also want a method of extracting data after filling out checklists. L2L gives you the ability to pull checklist answers and SPC charts, as well as MTBF (meantime between failure), spares costs, and technician time. Baselining is a key step in knowing if you are actually making progress.
Decide which assets to start with first
Using the baseline KPIs you collected, you’ll have a better understanding of which machines need your focus first. Do you have a machine that is down more than others? Is one machine costing you a lot more in spare parts than others? Focusing on preventive maintenance for those machines will save you time and money. It's challenging to roll out an effective PM program everywhere all at once, so focus your time and energy on the assets or lines that offer the most impact to the business.
Create the PM Checklist
After each item on the PM Checklist is a place to indicate a Yes / No response, enter a value, include a comment, record a measurement, check a box or choose from a dropdown. There's a place for your name, the date, and the time. The PM Checklist gives full visibility and accountability. The L2L digital interactive checklists eliminate the paper process and the ability to "pencil whip" the document. This engages the associates and ensures adherence to standards.
Create a schedule for your Preventative Maintenance and include the PM Checklist
In L2L’s Scheduler Module, you can set up scheduled Preventive Maintenance events to launch daily, weekly, monthly, semi-annually, and even based on number of cycles. You get the picture. Now add your PM Checklist!
As you can see. the actual creation of a PM Checklist is the easy part. Put in the work and take the necessary steps to come up with a Preventive Maintenance process that works and makes sense for your facility. Then reap the benefits of significantly less downtime, reduction in equipment failure, and an increase in ROI!
Learn how to create a PM Checklist or watch this Webinar.
Revisions
Original version: 18 July 2024
Written by: Evelyn DuJack
Reviewed by: Daan Assen
Please read our editorial process for more information
Related Posts
Subscribe to Our Blog
We won't spam you, we promise. Only informative stuff about manufacturing, that's all.