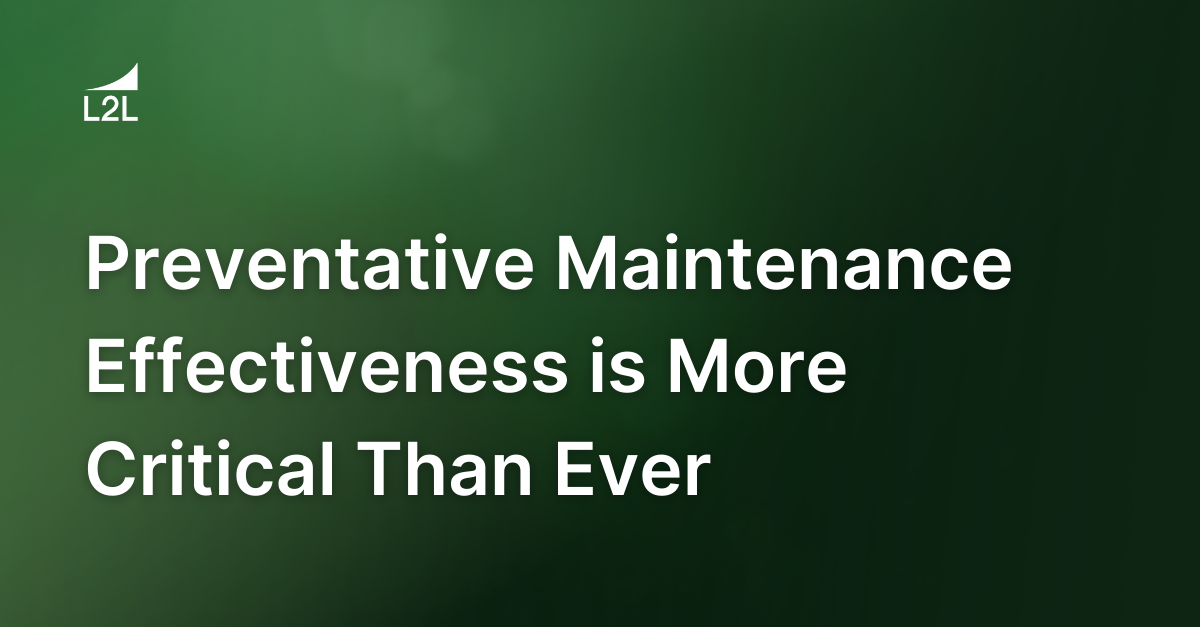
In times of crisis, becoming more efficient is more critical than ever. Some plants are reducing production output or maybe even shutting down. In other cases some plants are ramping up production depending on the product that they produce and the state of their local crisis.
In any case, the need is the same:
Using Preventative Maintenance to Increase Efficiency
The word maintenance means to keep the equipment in good running condition. This can be achieved through sufficient care in the following ways:
- A good TPM operator maintenance program
- Preventative maintenance (PM)
- Predictive maintenance
20 years ago, when I was a maintenance supervisor for an automotive supplier company, our team was fortunate enough to have the opportunity to work with a maintenance supervisor from the Toyota Tsutsumi plant outside of Nagoya.
He would come to the US and teach us the TPS maintenance principles and then we would go to Japan and see in action what we learned from the teachings.
There are three main elements to manufacturing.
- People
- Product
- Equipment
At Toyota, they say strong maintenance means a strong company, and the difference in productivity is the difference of machine availability. They made this point very clear to us. You need to have stability in your production to meet customer demand. Machine availability is one of the foundation blocks to a lean production system.
PMs are just one tooth in the reliability gear for equipment operational availability in a plant, and I want to cover three points that you can use to become more efficient in that area.
- Audit and standardize your PM steps of effectiveness;
- Review your time to complete these steps; and
- Challenge the frequency of those steps.
Now let's take a deeper dive into each of these points.
Audit and Standardize Your Preventative Maintenance Steps
First, review the steps on your current preventative maintenance tasks. Get your team together and read through those steps, and understand if those steps are still relevant. Do they add value?
I've seen some PM checklist steps that said to check all bolts. Really? I mean, there are probably 4,000 bolts on the machine; do you really want to take the time to check every one of those? Or maybe just a few critical ones?
(Psst! Want a preventative maintenance checklist? We've got you covered!)
Another wasted PM step I have seen is checking for loose or missing hardware. I think if you're missing any hardware, your machine wouldn’t be running. These are just a few examples of extraneous steps that don't add value to your process.
Some steps may not be relevant anymore, as modifications and changes have occurred. The component may not even be on the equipment anymore. Or, to the current maintenance staff, they don’t really understand the step and may just have their own interpretation of what is needed.
Clarify the steps and make them more meaningful. After you have gone through the steps, you will want to pull up the machine history in a chronological timeline and review your machine breakdowns, and when you completed your PMs.
Go through those and determine if events (including breakdowns) that occurred between PMs could have been prevented. It could be an opportunity to add or change a step on your checklist.
Challenge the Time To Complete Preventative Maintenance Tasks
The second item that can help with efficiency is to review your updated preventative maintenance steps and see what steps can be broken down and completed while the machine is running. I.e., run time vs. downtime steps.
What can be completed during the downtime of the equipment, ought to be. Break them down to be completed during lunches and breaks when the line has stopped.
And ensure you're handling PM's efficiently by challenging the time it takes to complete each step and looking for ways to decrease that time.
Challenge the Frequency of Your Preventative Maintenance
Finally, challenge the frequency of those PMs. One way may be to be run a component to failure -- if it's not critical to the process.
You may not do that in every instance, but in non-critical steps this could help you set the frequency to a minimum level to ensure PM's aren't being done when they don't need to be. Another point you could review again is the timeline of the breakdown of your PM steps to see if there are any opportunities to extend the frequency out.
For example, say every time you do the PM on the fluid level in a pump, the fluid level is the same. In that case, maybe you can move that from a monthly to a quarterly, or even every six months.
Another thing you can do – especially in crisis times where you might have fluctuating production schedules – is to see which of those can actually be moved from a time-based PM to more of a cycle-based PM. That way you're not doing PMs inefficiently; you're doing them because it’s a weekly and your plant has reduced to one shift.
A Final Word on Preventative Maintenance Steps
Just to wrap up those three points again, we talked about:
- Looking at PM steps effectiveness
- Looking at the time to complete the steps
- Run time vs Downtime Steps
And then also challenge your frequencies, as often as possible, but once you do that, don't forget to measure your pm on time completion percentage and your machine breakdowns per parts produced and chart your progress.
To do this well, you'll need a good LES (lean execution system) or a good CMMS in order to access production records and capture your operation availability. The reason why you're doing all this is to understand the impact that PMs have on your production output. Your goal is to keep the machines running to increase the throughput of the line.
L2L has a great system for doing all of the above; for collecting downtime history, for using the reports to look at the frequency of your breakdowns, for PM scheduling and capture the production output. Go see for yourself at https://www.l2l.com/solutions/drive-availability.
Revisions
Original version: 18 July 2024
Written by: Evelyn DuJack
Reviewed by: Daan Assen
Please read our editorial process for more information
Related Posts
Subscribe to Our Blog
We won't spam you, we promise. Only informative stuff about manufacturing, that's all.