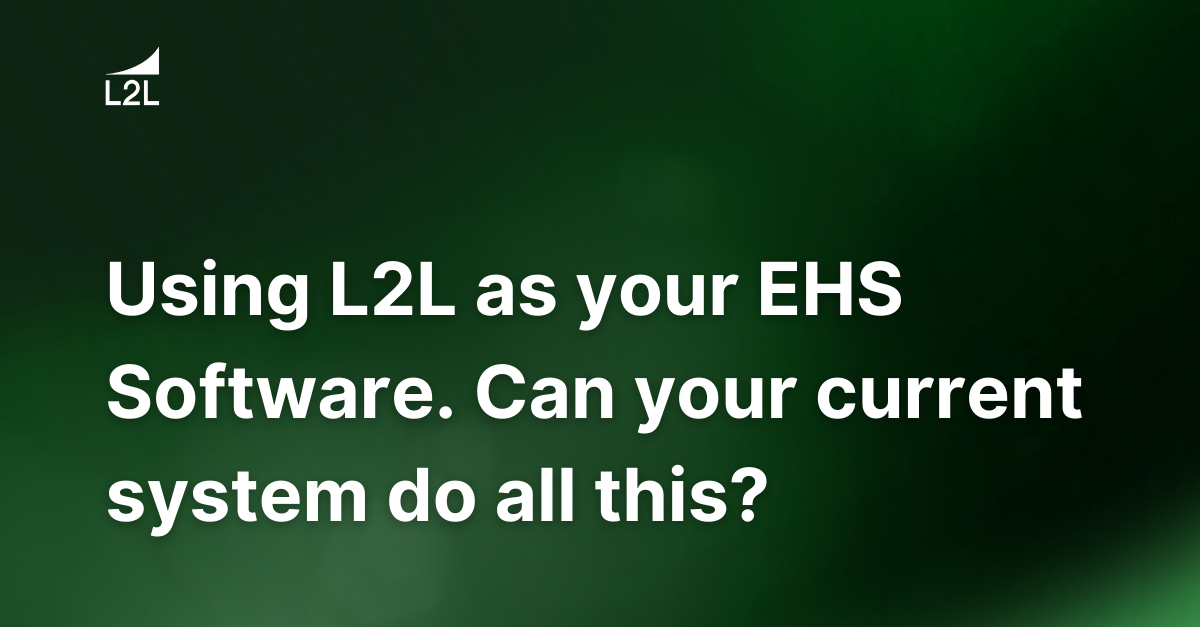
Did you know that June is National Safety Month? The purpose is to bring increased awareness of the importance of safety, and to promote a safe working culture within your facility. So with that in mind, you might be asking yourself, hey, how can I bump up the safety awareness in my plant?
Well, here are some good ways that you can help celebrate National Safety month and build that safety minded culture you need for your plant.
Ideas For Boosting Safety and Using EHS Software
Using L2L as your EHS software system, you can do this easily with a few of these ideas
- Create a push for more employee suggestions (Kaizen) focused on safety as a theme. You can give tickets for chances to win prizes in a raffle. This always generates enthusiasm in the teams and, in turn, will help you find your unsafe conditions.
- This is a good time for annual safety refresher training, like PPE, plant safety guidelines, and lockout tagout training. This can also raise the awareness for focused events.
- Hold a safety slogan contest in your plant and the winner(s) will get a prize and will see their work posted over the next year in signs around the plant. Make sure to include why it's important to be safe as part of the rules for the slogan contest. Who knows, maybe you'll get 12 great slogans and make a safety calendar for next year for the plant.
- Have you ever heard of Christmas in July? Why not Halloween in June! Encourage people to dress like zombies dragging their left foot behind them screaming brains!! Everybody likes zombies. At least when they are doing this, they will feel for trip hazards and put in a Kaizen for it! 😊 I actually read this idea from simplysafe.com about 10 years ago, awesome!
I’m sure your creative team could come up with many more ideas to help promote safety and bring awareness to help create the culture you want.
Now that you have the promotion in place, you need to make sure you can capture and manage the safety behavior you're wanting to build on and encourage. You're probably also looking for good ways to track safety activities in your plant.
To do this, I recommend you break down Safety into two groups, and list the ways you want to manage your Safety system. Start by thinking about proactive versus reactive.
Using EHS Software To Be Proactive
- How do you manage your behavior-based safety (BBS) Audits in your existing EHS software? Do you have a way to track the audit checklists and to trend those findings?
- Do you have an automatic scheduling system that launches reminders to those assigned to do these audit checklists, or whatever other safety audits you may have? Do you know if they are late, on-time, or completed at all?
- How are your safety training protocol and document control being managed? Questions like who was trained, by whom, when, and did the person acknowledge that they were trained, are important to track. When is the retrain date? Are you training to the latest revision of the safety standards for your plant?
- What about near misses? Do you have an easy way to document these learning events and to review these in your daily toolbox or your stand-up meetings? It’s especially important to recognize, share, and correct these potential safety hazards. Near miss lessons can save you a lot of money if acted upon and corrected.
- Add RMI (Risk Management Information) prevention to scheduled standardized work for your teams so that they can perform their daily stretches to help reduce and prevent repetitive motion injuries from happening.
- And of course, an employee suggestion program is a must have for an effective EHS software system. A simple way that’s visual for employees, so they can capture and submit their ideas. Make sure these ideas get routed to the correct approvers so people can track the progress from these ideas. Capture the cost savings and reward your teams for putting in ideas to make your plants safe. I'm sure there are some ergonomic opportunities to correct and I'm sure you get those requests a lot.
Using EHS Software To Be Reactive
- How do you track your accidents, your environmental spills, and your non-conformance issues today? You need to capture those in an event management system that gives the dates, the times, what happened, the location. It’s been said that time destroys evidence, so make it easy for the teams to capture this information quickly and document what happened. That's where a software solution like L2L is invaluable. All details entered quickly, easily, and paperless. If they have to look around for the paperwork, a zombie might get them and then there goes the clues.
- Where do you track the progress on the root cause analysis (RCA) performed by the team to correct the incident? It’s got to be easy to access and to immediately know the status of the actions being taken. Teams have to know what happened to eliminate the issue from happening again. That’s the goal. Don’t let it happen again.
- After the RCA is performed and the actions are in place, you will need to share those lessons (Yokoten). Once those incidents happen, you need to ask yourself where else this could happen in the facility? Make sure that those findings are tracked as well, and make sure that all those actions get implemented in all of the other areas or machines where the issue could happen. Your EHS software needs to provide a way for you to share the information with your sister sites, if you have multiple plants, so they can make these changes and benefit from the incident learning. I guess this could be a proactive point as well, but it's very important to follow up.
People who build the product need to have their EHS software system work together seamlessly with the vehicles that track the other issues they deal with every day. Hopefully they don’t need the reactive safety tools very often. But when they do, they need to know right where to go: the same place they enter a quality issue or log a downtime event. Don’t mess around and have 15 different systems managing all the processes on the floor.
Tying EHS Software To Your Lean Execution System
In my 35 plus years in the workforce, I've had my share of accidents, including stitches and broken bones. Hey now, before you pass judgment thinking I'm unsafe, I like to consider myself a hard working individual who has had some bad luck. Or not paying attention. But I have worked in farming, in a weld shop, and have been in a manufacturing plant for a very long time. I'm guessing you already know those are three of the top 10 most dangerous jobs in the world. However, those all happened before the place I was working had a Lean Execution System (LES) to manage the all the event abnormalities, including EHS incidents like I've just described in this article.
Is your EHS software tied into your plant's Lean Execution System? If not, you may want to look at a LES system like L2L to help bring all the information together in one spot and be simple to use.
And so, don't just focus on safety for the month of June. You must drive the safety culture you want all year long and take safety seriously. Get in the game! Make sure your plant has the system they need and like to use.
You have seen the ads on TV, "To stay safe! We are all in this together." And I guess those messages help. But I do know what works is JFDI (just focus and do it!).
For more information on how L2L can bring together your EHS software and other software systems at your site, visit our page, Integration Made Easy.
Learn more about National Safety Month
Revisions
Original version: 18 July 2024
Written by: Evelyn DuJack
Reviewed by: Daan Assen
Please read our editorial process for more information
Related Posts
Subscribe to Our Blog
We won't spam you, we promise. Only informative stuff about manufacturing, that's all.