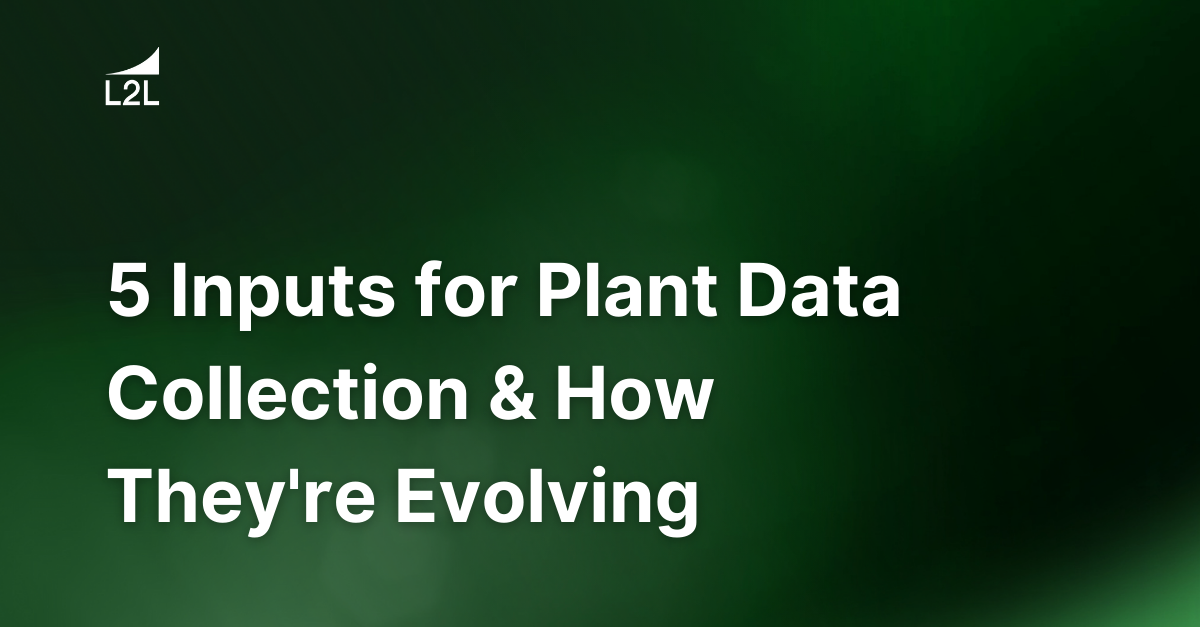
Estimated read time: 7 minutes
The Evolution of Plant Data Collection
Ever since the advent of the CMMS (Computerized Maintenance Management System) in manufacturing plant leaders have been trying to extract data that would point them down the path of improvement. Looking for any semblance of patterns in downtime, spare parts cost or even repair time would give these leaders the advantage they were looking for to create greater flow in the production process. For years this data has been either incomplete or untrustworthy, causing great frustration and loss of faith in software offerings.
Then, as technology progressed, so did the ability of Maintenance and Production software to capture a greater offering of data from the factory floor. In this, what was once known as a CMMS evolved to become an EAM (Enterprise Asset Management) system and what was once an MRP (Material Requirement Planning) system has evolved into the modern MES (Manufacturing Execution System) .
With this new EAM and MES, organizations are able to standardize their approach to capturing equipment data on the maintenance side and production flow data on the operations side. But as every factory leader and those tasked with improving the business will attest, there is still a lot of work in marrying these two data sets to get a good overall look at top line metrics that show plant performance.
For example, when attempting to calculate metrics such as OEE, there are a combination of factors that roll into the equation. These factors include downtime (equipment failure, minor stops, changeovers, etc), planned maintenance time (pm’s, scheduled work, cleaning-in-place), theoretical cycle-time, actual vs demand production numbers, scrap and rework numbers. To calculate OEE, we must get data from the MES, the CMMS and the quality system along with several back end inputs such as total runtime and cycle-time.
Gathering this data inside the factory then takes on a herculean task including whiteboards, log sheets, system query’s, spreadsheets and finally data analysts to compile all of this info into one readable format. I am sure there are a number of additional non-value added processes that I am missing here, but you get the point.
5 Key Inputs of Every Manufacturing Metric
Obviously there needs to be a better way to calculate and display metrics. But before we dive into that, let’s first understand what goes into a plant metric.
Currently, on our Smart Manufacturing Platform here at L2L, we have 18 metrics that our customers can choose to display on the L2L dashboards. They simply pick the ones they want and L2L does the calculation in the background. But as we learned in the previous section of this blog, collecting these metrics can be difficult... well, unless you know exactly what to collect and do it all in the same system.
What is critical is knowing what inputs go into nearly all manufacturing metrics and then collecting that data at the base level. What I am saying is that there are basically 5 inputs that go into nearly every manufacturing metric out there today. If these 5 inputs are collected into the same system at the same time, then software coding will be able to calculate and display those metrics in real-time.
So what are these 5 inputs?
-
Demand - The second key input is knowing how many of a particular product, production run or product order your customer requires. This is a simple knowledge of how many pieces, units or pounds are scheduled to be produced during a given duration of time.
-
Actual - Key to any performance metric is the input of Actual especially compared to the previous input of Demand. As a matter of fact, it could be said that really the most important production monitor as to performance of a process is the comparison of Demand v. Actual.
-
Scrap/Rework - Once a factory knows how many of a product needs to be produced, then understands how many of that product was actually produced, the next logical question for any production metric (like OEE) will be how many did we have to rework or throw away? This is usually a very difficult input to capture in current MES systems.
-
Labor - Knowing what labor minutes were used during activities on the shop-floor gives an input rarely available to data analysts. At a minimum, data crunchers can usually request or query the amount of labor used in a factory or on a particular line in broad strokes. But knowing how many labor hours were used to produce a single product or product order or exactly how many hours were used to repair a piece of equipment is usually data only captured in a manual process and only by the most disciplined of organizations.
-
Time - This is kind of a catch all category, but basically, all manufacturing metrics are framed around elements of time on a factory floor, such as cycle-time, resource time, planned production minutes, shift schedules, and of course downtime. All critical factors to almost all manufacturing metrics.
Currently in L2L’s Smart Manufacturing Platform, there are 19 separate metrics that can be calculated using these 5 key inputs. These are:
- Earned Hours
- Labor Minutes Per Unit (LMPU)
- Labor Hours Per Unit (LHPU)
- Man Hours
- Operational Availability (OA)
- Overall Equipment Effectiveness (OEE)
- Part Produced Per Man Hour (PPMH)
- Part Produced Per Hour (PPH)
- Performance Efficiency (PEFF)
- Production Pace
- Pitch Pace
- Scrap/Defect/Rework Percentage
- Theoretical Efficiency
- Reject Rate
- Performance Per Part
- Time Per Unit
- Non Productive Minutes
- Labor Efficiency
- Production Quality / Yield Percentage
All In The Same System
The key element to combining the 5 inputs for all of these metrics is having a system that captures all of them in the same piece of software code. Let Me Explain!
New Smart Manufacturing Platforms, like L2L, can capture all of this data simultaneously across the plant floor. Daily production Demand and Actuals are captured on the operations portion of the software while at the same time production disruption data and time, like downtime, material shortages, or operator fixes, are captured in the same system. That time is immediately factored into the calculation along with all of the other factors mentioned. The software can then do all of the metric calculations in the background and simply display the end item number in the visual format the plants desire.
Calculating, seeing and displaying the metrics that are important to your organization is all done in real-time, because the 5 key inputs are being captured in real-time on the shopfloor.
Here, take a look at what I am talking about. In this image you will see the L2L Operator Portal and note all of the metric inputs the system is capturing on this single screen and the metrics that are being displayed in real-time because of the capture of these inputs.
So the real question we need to answer is not what metrics to use, but rather, how to capture all of the data needed to see any metric we choose.
By focusing your efforts to capture all 5 of the key inputs, you’ll be on the right path. And even better, having a Smart Manufacturing Platform that will capture all 5 in real time, you’ll quickly move your operations much further ahead on this path to production performance.
To ensure you have all 5 inputs being correctly captured, and to realize the operational benefits, book a demo today, we’d love to show you how easy it can be.
Revisions
Original version: 18 July 2024
Written by: Evelyn DuJack
Reviewed by: Daan Assen
Please read our editorial process for more information
Related Posts
Subscribe to Our Blog
We won't spam you, we promise. Only informative stuff about manufacturing, that's all.