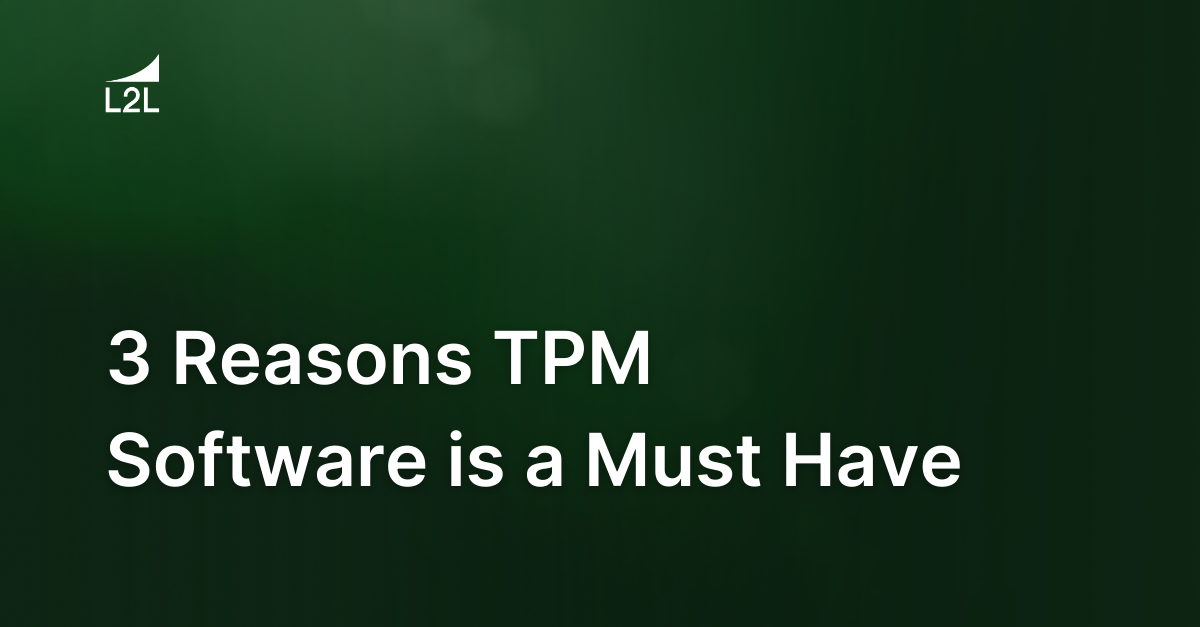
TPM Software
Whether you're looking to expand your current TPM program or just getting it off the ground, TPM Software can make a world of difference.
TPM is most often defined as Total Productive Maintenance, but is also thought of as Total Preventive Maintenance by some. For the purposes of this discussion, I will focus on TPM as Total Productive Maintenance, while not discounting that prevention is an extremely important element nevertheless.
A Brief History of TPM
TPM has been around for many, many years, even before this author was in kindergarten round up. Like many Lean practices and principles we still revere today, the concepts leading to the inception of TPM were first conceived in the United States. You might say TPM was then enticed to attend boarding school and its development was furthered abroad.
Like much of Lean Manufacturing itself, TPM began in the US and was readily adopted by Japan. TPM was born out of necessity in post World War II Japan. The Japanese immediately recognized the value of TPM, quickly embracing it in principle and practice. They continued to build off the basic philosophy of TPM and helped it evolve to become the TPM reality we are familiar with today.
TPM Software
Now that we know where TPM started, let's see what TPM Software is all about and what it means to those of us in the wonderful world of manufacturing.
Although my story is perhaps outside the norm, what I am about to share with you is by no means unique to me. It will help to know that I cut my teeth in manufacturing: High volume, mass production was my wheelhouse. At the risk of sounding immodest, I was pretty dang good at it, too. Who am I kidding? I completely loved it and it showed!
Along with high volume and mass production, our goal was also zero scrap. Yes, zero. Nada. Not easily attained when countless machines, lines, and work cells are steadily cranking out components as well as finished product. This was the perfect environment to drive the need for reducing downtime and defects. You cannot produce consistently at this volume, while simultaneously ensuring zero scrap and defects, without an extremely robust approach.
Earl Whitehouse, TPM Expert Extraordinaire
When I was first introduced to TPM, I got very lucky. I was fortunate enough to have an expert teach me the ropes. Since this expert frequently critiques, I mean, reads my blogs, I dare not use his real name. I'll call him Earl Whitehouse and just refer to him as E.W. for short.
At that time, I was no longer a newbie to manufacturing. I had also spent my fair share of time with our maintenance team. They were all very generous sharing their knowledge and expertise. I knew almost enough to be dangerous, but not quite.
E.W. worked at the same site I did, and he was very familiar with the challenges and obstacles faced by manufacturing, day in and day out. It seemed we were forever ramping up, building more and more product, and trying to do more with less and with fewer people. Especially 'indirect' people, meaning all the folks manufacturing relies on for support.
The time was right and E.W. was tapped to spearhead this plant wide effort toward more operator centric equipment maintenance. Particularly those activities that did not require a Journeyman Electrician or a PhD in Automation.
Please don't read anything into that statement. Something that does not necessitate an advanced degree does not mean it is not still very important. It means that people who have never performed those particular functions can be taught what needs to happen. Those very same shop floor folks can often do some teaching of their own. After all, they spend more time with each piece of equipment than anyone else.
So, teams were formed, tasks were identified and assigned to individuals, and we began to tackle many of the routine jobs that need to be performed on a daily or weekly basis. Most of the operators were very excited that they would not have to radio for maintenance or take down their machine while maintenance performed every PM. This also freed up the maintenance folks to tackle bigger issues. There was peace in the world and everyone lived happily ever after. The End.
Well, not quite. Performing the work was not a deal breaker. It was a good change of pace for everyone. But sometimes manually documenting everything in a log book became very tiresome. There were also times that a TPM task had already been performed, but someone had forgotten to write it down.
Fast forward to the 21st Century and Leading2Lean
E.W. was still hard at it, perfecting his mastery of all things TPM. By now, E.W. had taught hundreds, maybe thousands of people, the hows and whys of TPM. People from all over the world understood the importance of regularly performing TPM activities. They enjoyed and embraced the work, but their love for manual documentation had not blossomed alongside their dedication to the upkeep of their equipment.
Although E.W. did not invent Leading2Lean (L2L), (that was Bob Argyle, the CCO of L2L and his team), he is the person who first introduced me to the marvel that is Leading2Lean. His summary of L2L was so impressive, I had to know more! When Bob first showed me what L2L was capable of, I was blown away! My first thought was, "Where was L2L when I was still out on the shop floor?"
L2L = TPM Software
Many of you reading this blog right now have L2L in your shops and love how it has helped your organization already. It seems like Leading2Lean's Pillar Principles were customized just for TPM.
1) Transparency:
Not just in sharing information. In making sure everything is available to everyone. When it comes to TPM Software and performing TPMs, everyone needs to know and clearly understand all the tasks necessary to extend equipment lifespan and optimize performance. You have to know, or be able to quickly find, the recommended procedures: what needs to be greased? What needs to be aligned? What needs to be cleaned before it can be properly inspected. You're only one little mouse click away from all the information you need.
2) Visibility:
In my humble opinion, this is perhaps the single most important aspect of TPM, TPM Software, L2L, and Lean Manufacturing itself. As a wise TPM advocate once told me, "You can't catch the fish you can't see." In TPM Software speak, "It's hard to address what's hidden." (Address as in maintain, clean, fix, improve, replace, resolve).
We have all been there. People can start to be territorial about their area or responsibility. This does not just pertain to manufacturing. For whatever reasons, people get uncomfortable when they feel too much is on display out there for everyone to see. Often this is based out of fear: "What if everyone can see what I'm doing and I'm not doing it right?" or "If I'm the only person who really knows how to do this. My job will be safe forever." or "I don't want anyone to see that we have an extra widget. They'll want it and I don't know if we can get more."
While there were almost certainly real events that led to these feelings, that's no way to lead people or manage resources. And it's definitely not the way to run a factory. Fortunately for all of us, most people have learned how counterproductive this mentality is. When people understand the rules and the boundaries are clearly marked, they want to be in the game. They want to play their best and they want to win. Visibility is the great equalizer: it levels the playing field.
3) Accountability:
For many of us, this is where the rubber meets the road. Accountability should never be mistaken for finger pointing or a means by which to punish. Accountability means having ownership. In the context of TPM and TPM Software, accountability is the vehicle by which every person is given opportunities: to take ownership, to demonstrate initiative, to rise to the occasion. To make a difference. Accountability means every individual at every level knows and understands their contribution. Every result is not the fault of the workers and the responsibility of management.
So, Why TPM Software?
So, why practice TPM and why the need for TPM Software? Ultimately, the goals of both TPM and TPM Software are increased productivity, cost reduction, elimination of waste, increased employee engagement through ownership, and increased quality. TPM is vital to the successful realization of all of these. TPM Software makes these all more readily attainable.
The Big 3: Transparency, Visibility, Accountability. Sound familiar? It does if you are using a Digital Production System like Leading2Lean. With L2L as your system, TPM comes to life. Photos, videos, quick data entry and collection, rapid response. All in one place. All easy to track, see, and share. If you have not yet incorporated L2L into your TPM world, call us to schedule a demo and learn more and see how easy this transformation is!
Revisions
Original version: 18 July 2024
Written by: Evelyn DuJack
Reviewed by: Daan Assen
Please read our editorial process for more information
Related Posts
Subscribe to Our Blog
We won't spam you, we promise. Only informative stuff about manufacturing, that's all.