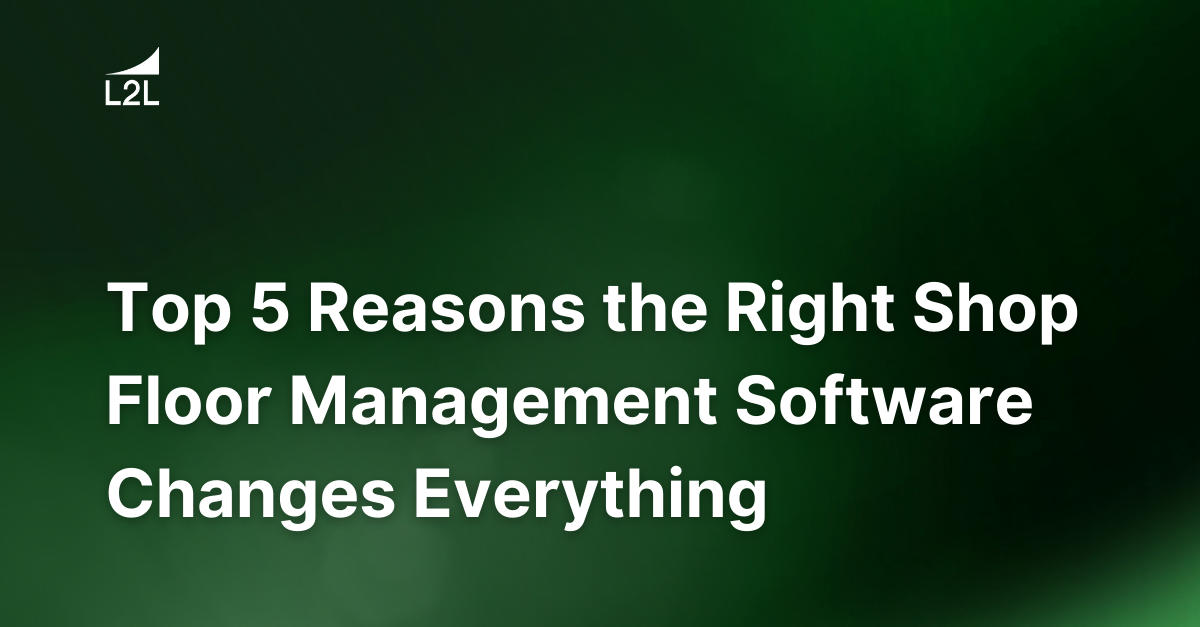
If your industry is manufacturing or production related, you and your team have even more reasons to stand a little taller after the past few years. You've all had to do more, often with less. From supply chain disruptions to labor shortages, you and your resources have been pushed to your max — and you've certainly felt the consequences of it on your shop floor.
Shop Floor Management Software Is More Than a Nice-to-Have
What does this have to do with shop floor management software? After navigating the pandemic and post-pandemic challenges, you've learned a few lessons and even some cool things about your teams and about yourself as a leader. And most likely, you've come to realize that daily interaction with shop floor management software is essential to the success of your business.
Shop floor management software (also called shop floor software and shop production software) is an essential element of a successful manufacturing business. Here's the truth: you can't be everywhere at the same time. You can't work remotely and be physically present on the shop floor at the same time. You have to be able to immediately assess performance at a glance, and so must your team. Moreover, you must be able to gauge how your teams are doing even when you can't see them in person.
5 Essentials of Shop Floor Management Software
You need shop floor software that tells you where hold-ups may occur. Does your team have the materials and tools to perform their jobs? Will your finished goods be ready to ship on time? Do you have the right people where they need to be and fully trained so everything keeps running? Do you have the right number of people today, tomorrow, next week, and next month?
This is where the rubber meets the road, so make sure your shop floor management software addresses these five essential questions:
1. Does your team have the necessary raw materials, sub-assemblies, and tools to perform their jobs?
Your shop floor management software should help you:
-
Track spare parts consumption, costs, and trends
-
Satisfy calibration dates and requirements for calibration performed both inside and outside your facility
-
Connect all people and processes digitally (without paper)
-
Capture and record material shortages and trends (If we've learned anything from 2020, it's how vital our supply chains are)
2. Will your finished goods be ready to ship on time?
Shipping delays are costly. Here's how shop floor management software helps prevent them:-
Satisfy customer delivery requirements
-
Notification and escalation of all concerns and victories
-
Avoid expedited freight charges
-
Turn goods at your targeted rate
3. Do you have the right people in the right places?
Shop floor management software can help you effectively allocate personnel:-
Fully train your workers in the skills for specific areas, lines, and machines to keep everything running
-
Have enough skilled people to train others
-
Provide evidence of satisfactorily completing training
-
Generate a complete history of documentation, including dates
4. Are your workforces still in flux?
Labor shortages and high turnover still plague manufacturers. Shop floor software can help you make sure you:-
Have enough people for both the present and the long term
-
Can perform and monitor work and checks remotely
-
You provide your team with immediate access to checklists and necessary documents
-
People can be moved when shortages arise
5. Can you plan and monitor production events in real time?
Know at a glance if you're on schedule, ahead, or behind:-
Are you trending in the right direction?
-
Are you hitting your targets?
-
Are you building good products? This includes actual throughput, scrap, rework, and reject, and defect quantities.
With the right shop floor management software, you can:
-
Easily monitor and display all production metrics (OA, OEE, PPM, downtime)
-
Ensure correct product and product orders are being run
-
Schedule and deliver reports directly to your inbox on a regular basis. Include all the people who need to be kept apprised: your shop floor leaders, your boss, accounting, your internal customers, and internal suppliers.
How Shop Floor Management Software Drives Success
How does having the right shop floor management software change everything, when it seems like everything has already changed? There was a time when a clipboard and some mimeographed pages were enough for you to keep it all together. Throw in a whiteboard or two, and you were set.
Sure, you could still do that. Or, you can embrace the technology that allows for much easier input of information. Your shop production software should make it easy for everyone to input data related to the work they're performing. It's hard to hold up your clipboard and share a spreadsheet with workers in a different building, or a different city entirely.
What we're all after is to make operations management easier, even with the need to work remotely. It's not just easier; it's safer, too. People in separate locations, different departments, and across various shifts have been able to share and analyze data without having to meet face to face.
L2L provides remote shop floor management capabilities that make it easy and convenient to share progress and results, including user-friendly visual charts that readily convey the state of your shop floor. Yes, we have experienced unprecedented changes in the manufacturing space, and your shop floor production management software needs to be up to the task.
No one can predict how manufacturing practices will evolve in the next decade, but a lesson that continues to hit home is that the only constant in this life is change. Make sure your shop floor management software is flexible and adapts to your needs. With L2L on your side and in your shop, shop floor management is one less thing to stress about.
Interested in more great content? Check out the L2L YouTube Channel!
Revisions
Original version: 4 December 2020
Written by: Cara Winther
Reviewed by: Daan Assen
Please read our editorial process for more information
Related Posts
Subscribe to Our Blog
We won't spam you, we promise. Only informative stuff about manufacturing, that's all.