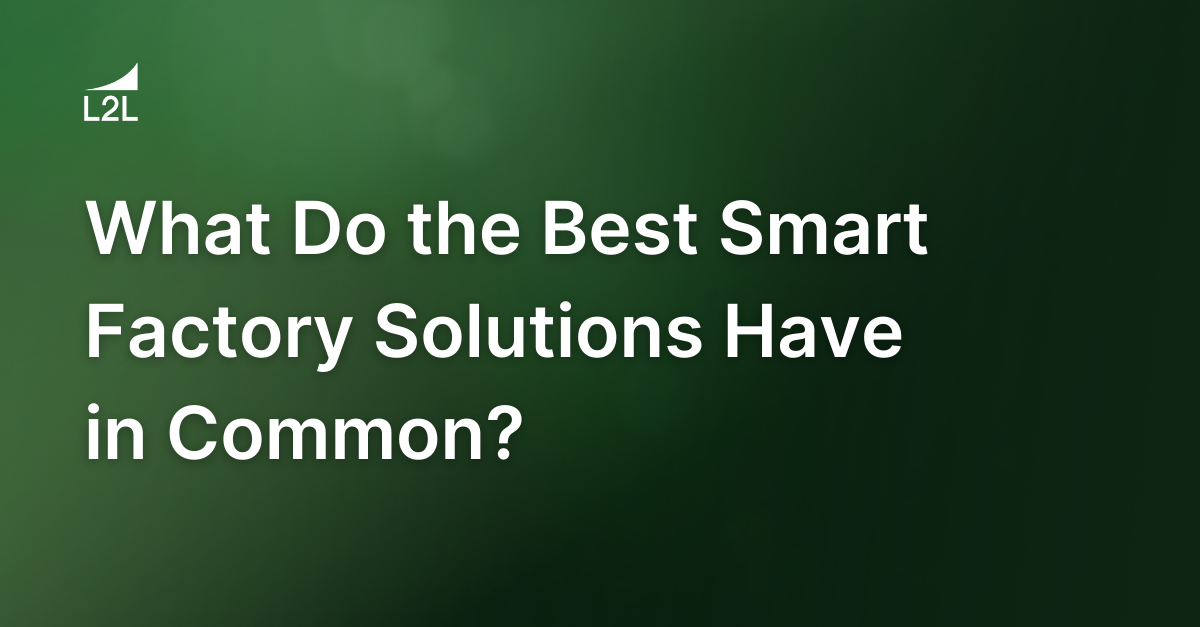
Estimated read time: 8 minutes
Imagine the smartest factory in the world — a shining light in the manufacturing industry, a titan of production efficiency, an expert at data analytics and insight utilization. They handle every manufacturing disruption like it’s no big deal. They’ve even got the know-how to navigate supply chain issues with confidence. What’s the secret? What makes this factory so smart?
If you said technology, you’re right — but there’s more to the story.
The truth is that every smart factory — and every smart factory solution — generally relies on one thing. So what is it they all have in common?
Let’s find out. (Spoiler alert: It all gets back to connected workforce platforms.)
The foundation for smart factory solutions
If you’ve made it this far, you probably know the basics of smart manufacturing and smart factory solutions. In fact, it’s almost impossible to exist in the industry without running into these concepts in one way or another. That being said, it’s important to make sure you understand exactly what’s being discussed when smart manufacturing terms are being thrown around.
Here’s the key thing to remember: A smart factory isn’t smart because it’s chock-full of technology. It’s smart because it’s using that technology in all the right ways.
That’s a pretty big difference. If smart factory solutions were all about getting as much tech as quickly as possible, it would be equivalent to duct-taping random gadgets to the outside of your truck and calling it “the vehicle of the future.” Instead, each solution uses carefully chosen tech tools to address specific problems — and that’s like choosing built-in sensors and systems that help your truck operate, perform and drive better instead of just looking cool.
If you’re thinking that all this sounds familiar, that’s because it is. Smart manufacturing is based on many of the same core principles that shaped other industry innovations, like the concept of lean manufacturing. Waste reduction, efficiency improvements, common sense — these are the building blocks of any good production system, smart factory solutions included. It all fits under the Manufacturing 4.0 umbrella, a strategic approach to the rapid development of technology, automation and interconnectedness across industries. Think of it this way: This is the Fourth Industrial Revolution, and smart factory solutions are your front-row seat.
What the best smart factory solutions look like
Now that you know where smart manufacturing solutions come from and what they really mean, it’s time to pull back the layers and find out what’s making them tick.
Here are a few examples:
Effective data capture
No factory can be smart without data. Of course, that information isn’t going to just waltz into your systems — which is why smart factory solutions always have a way to effectively capture manufacturing data. That means real-time data can be automatically created by machine and software integrations, sensors, or manually entered by workers with mobile or wearable devices.
A single source of truth
With data comes knowledge. A good smart factory solution helps create a single version of the truth, which unites multiple viewpoints and data sources to help workers see what’s really going on across the entire manufacturing operation. This enables better decision-making, improved resilience to supply chain disruptions, boosted efficiency and more.
Real-time data analysis and insights
By now, you’ve probably noticed that data plays a big role in smart manufacturing. However, data on its own is still just data; you need to be able to turn that information into insights before you can do anything with it. A smart factory relies on analytics to make this possible. Once data is captured, it’s broken down into key elements and translated into actionable ideas — like deciding how to plan your production schedule or how to structure your preventive maintenance approach.
Disruptor visibility
Smart factory solutions also play an important role in identifying and addressing production disruptions. That’s because not all disruptors are machine-related — which means you need a way to capture, analyze and understand issues from other sources across the factory. Smart manufacturing uses tech tools like artificial intelligence to identify patterns of disruption and recommend immediate responses, process improvements and other solutions.
Digitized issue resolution
Once a disruptor or issue has been identified, it’s time to get to work on a resolution — and with smart manufacturing, the entire process can be digitized. Notifications can be sent to the right employees automatically, procedures can be recommended, correct parts can be identified for replacement and downtime can be minimized — all while data about the problem and resolution is being captured and stored for future analysis.
So, it’s clear that these elements are the nervous system of any good smart manufacturing solution. But where do they come from? You can’t just snap your fingers and have things like real-time data analysis or digitized issue resolution, right?
Here’s the big secret: All these elements have one thing in common, and that’s a connected workforce platform.
This tool isn’t just about data capture and analytics — it actively helps improve efficiency, streamline production processes and support workers on the factory floor and beyond. That’s because a platform helps you deploy the right technology in the right places, enabling digital transformation in manufacturing (which is what really makes a factory smart).
How to get started with smart factory solutions
The good news about connected workforce platforms is that you can start using one right now, which means the first step toward a smart factory is well within reach. The only real challenge is deciding to get started.
That’s because the way you’re doing things right now might seem perfectly adequate, even if it’s not exactly “smart.” If your current manufacturing process is working, why rock the boat?
Well, here’s the thing: Digital transformation is no longer optional.
If you want to survive and thrive in an increasingly competitive landscape, you need to speak the language of the future — and that’s real-time data. Without this data (and a platform to capture and analyze it), you’re operating on a fragmented, unreliable view of your factory, and that’s a good way to fall victim to disruptions, downtime, inefficiency and even preventable supply chain issues.
So what does this mean for you? Simple: It’s time to get out of your own way. A connected workforce platform — readily available technology just waiting for you to reach out and grab it — is the foundation for everything we’ve discussed here today. If you want real-time data capture and analysis, digitized issue resolution, a single source of the truth and all the other great things that come with smart manufacturing, you need the foundation that makes it all possible.
Make your factory smarter with L2L
Do you want to evolve your operation into a smart factory? Are you ready to say goodbye to the idea that more tech equals better results and instead embrace the common-sense ideals at the heart of the manufacturing industry? Is it time for your workers to start learning the “language of the future” with access to data capture tools, analytics, insights and more?
If you answered yes to any of these questions, it’s time to see how a connected workforce platform makes all of this possible.
To take the first big step, complete this self-assessment to find out your current level of digital maturity. (Or, if you’re more into baby steps, start by checking out all the manufacturing wisdom on our blog.)
Revisions
Original version: 21 July 2022
Written by: Eric Whitley
Reviewed by: Daan Assen
Please read our editorial process for more information
Related Posts
Subscribe to Our Blog
We won't spam you, we promise. Only informative stuff about manufacturing, that's all.