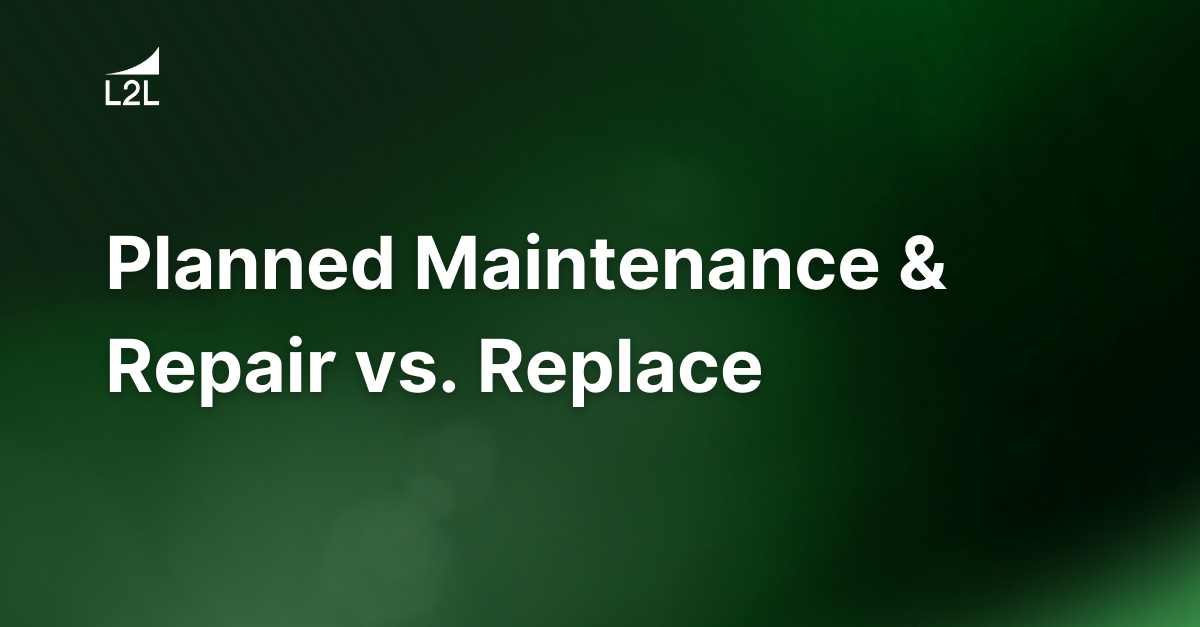
A familiar expression in maintenance management is, “Why not just replace rather than repair?" Replacement means you'll have new, long-lasting equipment. After all, isn’t that a good practice?
It may be a sound approach if the cost equation supports it. Often, however, it doesn't. Equipment and components may be easily repaired without replacement. If it’s cheaper to replace than repair, then replace. If it’s less expensive to repair, then that approach makes more sense. It’s a cost-based decision.
A $100 sensor might reasonably be a “replace.” A leak detector that costs $30K is going to be a “repair.”
The key is understanding the real cost, not just the cost of the part alone.
Do Your Preventive and Planned Maintenance Plans Address The Repair vs Replace Question?
The real problem companies have in the repair vs replace dilemma is that sometimes, replacing components becomes the easy way to troubleshoot issues. Because technology is increasingly complex, it’s sometimes hard to tell why something is not performing well. If a component is replaced, and the problem goes away, then component replacement makes sense — but only if a faulty component is actually the culprit.
But if replacing a component doesn't resolve the issue, it can complicate things further. If the problem does not go away, the part was consumed unnecessarily. Sometimes the part gets pulled off and put into spares, but then people are hesitant to use it because it looks like it was used.
Or, if the part that was used to troubleshoot is then put back in spares, it may have been used for a short period of time before being pulled off and put into spares. Now you have an issue where the life of the part going forward is unknown, which throws off the time-based approach. More often than not, the part just gets thrown away to eliminate confusion and doubt.
In the case where the part you swapped out wasn’t the issue, perhaps not much was lost in terms of consumables. But much is lost if time is factored into the total equation. If a $100 sensor takes 30 minutes to change out, that 30 minutes in lost production could come at a cost of $2,000. In that case, it's not justified to take that 30 minutes to pull the part off and put the old one back on when production is stopped and waiting for you to get their equipment back up and running.
With the right software and technology, you can implement standard processes for troubleshooting based on the maintenance history of the machine. For example, if nine times out of 10, the above problem is solved by resetting the sensor, replacing the sensor could be a costly mistake as the previous sensor may not be defective.
This scenario could lead to a problem-solving project to understand why the sensor is losing its settings. It could be the wrong sensor for the job or a faulty design that needs to be addressed with the vendor. Technicians are now armed with much more information to solve problems correctly and more efficiently while finding the root cause of recurring issues.
Simply replacing parts without historical data just adds further risk to the maintenance process. But with a machine's historical data at your fingertips, you can confidently decide whether to repair or replace it, keeping wasted time, money, and materials to a minimum.
You can adopt a smarter approach to repair vs replacement with technology and software that preserves historical data and maintenance records.
Revisions
Original version: 18 July 2024
Written by: Evelyn DuJack
Reviewed by: Daan Assen
Please read our editorial process for more information
Subscribe to Our Blog
We won't spam you, we promise. Only informative stuff about manufacturing, that's all.